Ремонт головки клапанов
Ремонт головки цилиндров
Ремонт головки начинается с тщательной отмывки керосином или растворителем. Удаляем металлической щёткой, зажатой в патроне электродрели нагар из камеры сгорания и с тарелок клапанов.При разборке клапанного механизма потребуется рассухариватель клапанов, например такой, как показан на фото внизу, но наиболее эффективный несложно изготовить своими руками, по чертежам опубликованным вот в этой статье.
Перед разборкой и после, внимательно осматриваем головку цилиндров. Трещины, сколы в любых местах головки не допускаются. При подозрении на попадание охлаждающей жидкости в масло проверяем головку на герметичность, для этого необходимо заглушить отверстия рубашки охлаждения и опустив головку в теплую воду, нагнетаем в неё сжатый воздух под давлением 1,5 — 2,0 кг. В течении 1,5 минут не должно наблюдаться выхода пузырьков воздуха. Более подробно о такой проверке, а так же о ремонте треснувшей головки, я написал вот тут.
Сёдла клапанов . Форма фасок сёдел клапанов показана на фото. На рабочих фасках сёдел в зоне контакта с клапанами не должно быть коррозии, точечных раковин, прогаров и повреждений. Небольшие повреждения устраняем снятием ( как можно меньше металла) специальным набором фрез с направляющими ( например, качественный набор американской фирмы НЬЮВЭЙ). Подробно об этом я написал в этой статье.
После этого, тщательно промываем головку, седла и маслянные каналы и потом продуваем их сжатым воздухом.
Направляющие втулки клапанов.Проверяем зазор между направляющими втулками и стержнями клапанов, соответственно, измерив микрометром стержень клапана и нутромером отверстие направляющей втулки. Зазор для новых втулок : 0,022 — 0,055 мм для впускных клапанов и 0,029 — 0,062 мм для выпускных. При износе максимально допустимый зазор 0,3 (при отсутствии повышенного шума). Если повышенный зазор между направляющей и клапаном не может быть устранён заменой более толстым клапаном, то меняем направляющую втулку (выпрессовываем) — об этом читаем тут.
Можно нарастить диаметр стержня клапана хромированием, при условии что нет ступеньки (неравномерного износа диаметра) на стержне. Если запрессовали новые втулки (лучше заказать токарю бронзовые), то после запрессовки их необходимо развернуть специальной развёрткой с длинной направляющей. Затем притираем клапана к сёдлам притирочной пастой ( лучше на водной основе) — как это правильно сделать читаем здесь.
Также, клапана проверяем индикатором часового типа на отсутствие кривизны стержня, прокручивая клапан в двух маленьких призмах и следя за отклонениями стрелки индикатора. Отклонение даже в несколько сотых мм. недопустимо. Маслосъёмные колпачки, естественно, заменяем на новые.
Пружины клапанов осматриваем на наличие трещин, проверяем упругость.
Толкатели клапанов: проверяем их рабочую (трущуюся ) поверхность, на ней не должно быть задиров и царапин.
Распределительный вал , рабочие поверхности кулачков, поверхности под сальник, а так же эксцентрик (не на всех) отбеливаются или цементируются для повышения износостойкости, эти поверхности должны быть отполироваными и не иметь рисок, царапин и износа в виде потертостей, ступенек.
Если есть глубокие риски и выше перечисленные дефекты, то вал необходимо заменить. Устанавливаем распредвал на две призмы и проверяем радиальное биение с помощью индикаторной стойки. Биение шеек подшипников и тыльной части кулачков не должно превышать 0,02 мм. Ну а как повысить ресурс штатного распредвала советую почитать вот тут.
Корпусы подшипников распредвала не должны иметь трещин и повреждений, а на опорных поверхностях под шейки распредвала не должно быть задиров и царапин. Зазор между шейками распредвала и отверстиями опор определяется промером этих деталей и вычетом от большего меньшее( микрометр и нутромер).
Так же, зазор можно определить с помощью пластмассовой калиброваной проволоки (описано на примере коленвала) Расчётный зазор для новых деталей: 0,069 — 0,11 мм, а максимально допустимый износ : не более 0,2 мм. После замены деталей, которые не вписываются в максимально допустимые зазоры, остаётся всё собрать. После фрезеровки сёдел и притирки клапанов на клапане в месте соприкосновения с седлом, должна быть тоненькая (1 — 1,2 мм) матовая полоска, без разрывов по кругу.
После сборки клапанного механизма ( засухаривания), клапаны проверяем на герметичность, для этого камеры згорания заливаем керосином, в течении не менее двух минут, а лучше пяти, не должно быть просачивания керосина между сёдлами и клапанами. Далее устанавливаем головку на блок, естественно, установив между ними новую прокладку.
Порядок затяжки болтов головки и гаек корпусов подшипников смотрим на фото ниже. При затяжке используем динамометрический ключ, а требуемый момент затяжки болтов находим в мануале своего двигателя. Остаётся одеть и затянуть приводной шкив и отрегулировать тепловые зазоры.
приспособление для рассухаривания клапанов
Регулировка тепловых зазоров.
Тепловые зазоры клапанов на каждой модели двигателя имеют разное значение, на дизелях больше, на бензиновых моторах меньше, и каждый производитель в мануале или на наклейке клапанной крышки пишет своё значение (для выпускных всегда больше, так как нагрев больше).
Я опишу регулировку зазоров и, если будут какие то цифры, то это всего лишь примерное значение. А вообще, существуют два основных способа регулировки: с помощью замены регулировочных шайб (на более свежих моторах), и на более старых( классика) моторах, с помощью регулировочных болтов с контргайками.
Способ с регулировочной шайбой: для начала выставляем распредвал по меткам( обычно на шкиве и разъёме головки с блоком), но крутим за болт коленвала только по часовой стрелке и затем доворачиваем ещё на 40 -50°. Это 2 — 3 зуба на шкиве распредвала, при этом в первом цилиндре будет фаза сгорания.
Замеряем зазоры клапанов первого цилиндра с помощью щупа и если зазоры больше нормы, то запоминаем, насколько больше, далее отжимаем толкатель и извлекаем регулировочную шайбу. Микрометром измеряем её толщину. Определяем толщину новой шайбы по формуле: Т = В + (А — Б), где Т — толщина новой шайбы, А — замеренный зазор, В толщина снятой шайбы, Б- номинальный зазор мм.
Например : А= 0,28 мм; В = 3,80 мм; Б = 0,25 мм, то получаем Т = 3,80 + ( 0,28 — 0,25 ) = 3,83 мм — толщина новой шайбы. Оттянув толкатель (спец оправкой) устанавливаем более толстую новую шайбу, далее проверяем, щуп должен входить между толкателем и кулачком с лёгким защемлением. Остаётся последовательно прокручивать коленвал на пол оборота ( а метка на шкиве распредвала при этом проварачивается на 90°) и отрегулировать зазоры на клапанах остальных цилиндров.
Способ с регулировочными болтами ещё проще. Сначала, так же, выставляем по меткам распредвал, что соответствует концу такта сжатия поршня первого цилиндра, проверяем щупом величину зазоров у обоих клапанов и если щуп проходит свободно или совсем не проходит, производим регулировку.
Для этого на регулировочный болт надеваем накидной ключ, а на контргайку рожковый и ослабляем эту контргайку. Затем вставляем между регулировочным болтом и стержнем клапана щуп и проворачиваем болт, добиваясь чтобы щуп скользил с лёгким усилием, когда добились, вынимаем щуп и затягиваем контргайку, следя за тем, чтобы регулировочный болт оставался наместе ( не прокручивался).
Аналогично, регулируем зазоры в 3, затем 4 и 2 цилиндрах, поворачивая после каждого цилиндра коленвал на 180° (распредвал повернётся соответственно на 90°). Вот и всё, закрываем клапанную крышку.
Более подробно о регулировке клапанных тепловых зазоров можно почитать и вот здесь.
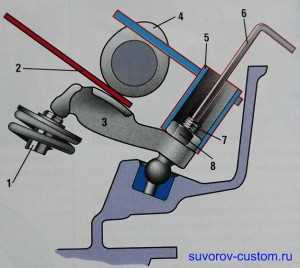
Регулировка зазора клапана.1 — стержень клапана, 2 — щуп, 3 — коромысло, 4 — кулачок распредвала, 5 — накидной ключ, 6 — шестигранный ключ, 7 — регулировочный винт, 8 — контргайка.
Часто на двигателях, которые эксплуатировали с неправильными тепловыми зазорами, тарелки клапанов в месте соприкосновения их с сёдлами, пригорают и теряют герметичность. От этого естественно падает компрессия в цилиндрах, и соответственно падает мощность двигателя.
Вернуть мотору былую силу можно притерев клапаны. Как и с помощью чего это правильно сделать, можно почитать вот в этой полезной статье. Ну а об устройстве, обслуживании и ремонте головки двигателя я написал отдельную подробную статью вот тут.
Надеюсь эта статья о ремонте головки цилиндров будет полезна начинающим мастерам, успехов всем.
suvorov-castom.ru
Ремонт клапанов - авто
ВОССТАНОВЛЕНИЕ КЛАПАНА
ОБЩАЯ ЧАСТЬВнешне конструкция клапана довольно проста. Основные части:стебель, перемещающийся в направляющей втулке, и головка, которая 'садится' на седло, герметизируя камеру сгорания. Формой головка напоминает перевернутую вверх дном тарелку, поэтому головку называют еще "тарелкой клапана". Она имеет рабочую фаску с углом 30° или 45° относительно плоскости тарелки и цилиндрический поясок. Он необходим для увеличения жесткости тарелки и защиты ее кромок от обгорания и коробления. Кроме того, поясок позволяет сохранить основные геометрические размеры тарелки клапана в случае перешлифовки его рабочей фаски. Ширина пояска в различных конструкциях двигателях бывает до 2 мм.
На форсированных двигателях клапаны делают составными. Если обычный клапан изготавливается из однородного материала, то составной - из двух частей: стебля из износостойкого металла и тарелки из жаропрочного. Соединение производится сваркой трением.Нередко полый выпускной клапан заполняется легкосплавным металом (натрием), что снижает теплонапряженность клапана.Стремясь повысить износостойкость, некоторые фирмы, например MERCEDES, хромируют поверхность стебля клапана. BMW применяет 'ремонтные' клапаны с увеличенным диаметром стебля: 8.0; 8.1; 8.2 мм. Для чего - понятно: чтобы не перепрессовывать направляющую втулку клапана, у которой со временем увеличивается внутренний диаметр по причине естественного износа. Торец стебля, испытывающий, как и тарелка, большие нагрузки, в разных типах двигателей упрочняют различными методами на глубину до 1 мм.На стебле клапана есть специальные проточки для 'сухарей', фиксирующих клапанные пружины. Если дело дошло до ремонта или проверки клапана, не мешает на всякий случай проверить состояние этих проточек - не нарушена ли геометрия их поверхностей вследствие выработки. Это может привести, как говорят механики, к 'рассухариванию' клапана.Впускные и выпускные клапаны - составляющие одного целого. Выполняют они общую задачу, но в разных условиях.Большой диаметр тарелки впускного клапана обеспечивает лучшее наполнение цилиндра топливной смесью. Той же цели служит тюльпанообразная форма тарелки, встречающаяся в некоторых конструкциях.При работе двигателя клапаны одновременно совершают возвратно-поступательное и хаотичное вращательное движения, что обеспечивает более равномерный износ седел, направляющих втулок и самих клапанов. Эксплуатация двигателя с увеличенными тепловыми зазорами из-за возрастания ударных нагрузок приводит к повышенному износу торца стебля и росту боковых нагрузок на втулку.Обычно уже предварительный осмотр торца стебля клапана позволяет сделать вывод: если глубина выработки торцевой части не более 0,2 - 0,3 мм, то ее, выработку, еще можно вывести на шлифовальном станке. Не забывайте, что глубина упрочняющего слоя торца стебля клапана 0,5-0,7мм. Обязательно промерьте износ стебля клапана с помощью микрометра. Наличие 'осязаемой ступеньки' в районе маслосъемного колпачка и без измерений говорит о необходимости замены клапана.Незначительные износы фаски клапана, типа точечной эррозии, можно устранить притиркой. Допустимая зернистость притирочного порошка - 10-14 мкм. Притирая клапаны более грубым порошком, Вы наверняка повредите рабочие кромки пары 'клапан-седло'. При этом образуются глубокие риски, от которых уже никак не избавишься. Они ускоряют образование нагара на рабочей фаске, что приводит к увеличению теплового сопротивления в месте контакта клапана и седла. Это ухудшает теплоотвод от тарелки клапана, увеличивая опасность ее перегрева, коробления и разрушения. Если же на рабочей фаске Вы обнаружили значительную выработку, раковины, небольшие участки прогара и т. п., нарушающие плотность посадки клапана в седло, то здесь без механической обработки не обойтись. При восстановлении фаски клапана не забывайте, что в случае применения механизма с гидрокомпенсаторами зазора, расстояние от торца клапана до верхней плоскости головки цилиндра строго регламентировано. Незначительное изменение этого расстояния на 0,1 - 0,15 мм в некоторых случаях улучшает работу гидрокомпенсатора, так как его рабочая зона смещается.
Основанием для отбраковки клапана являются:
Явные повреждения клапана: гнутость, прогары, трещины, забоины.
Изменение диаметра стебля по его длине более 0,02 мм.
Ступенчатый или боковой износ стебля клапана.
Поврежденные проточки под сухари.
Уменьшение высоты цилиндрического пояска ниже допустимой производителем.
Расклеп торцевой части стебля и глубина выработки торцевой части более 0,2 - 0,3 мм.
Если ваш клапан прошел эти тесты, то есть шанс его восстановить.Восстановление протекает следующим образом:
Вначале клапан очищают от нагара и масляных отложений.
Проводят измерения диаметра стебля клапана, а результаты записывают маркером на тарелке клапана. Эти значения потребуются при восстановлении направляющей втулки.
Замеряют выступание торца клапана над опорной поверхностью тела головки блока под пружину. Это значение для каждого клапана рекомендуется записать и сравнить со значением, полученным после обработки фаски клапана и седла.
После этого клапан зажимают в цанговый зажим станка и далее резцом или камнем формируют фаску.
После обработки такой фрезой на поверхности фаски образуется особый микрорельеф, благодаря которому приработка клапана происходит быстро и эффективно, а притирка носит контрольную функцию.К резанию фаски клапана следует относиться осторожно. Снять необходимо ровно столько, чтобы поверхность стала чистой. Иногда встречаются клапаны с некачественно нанесенным упрочняющим слоем. В этом случае после обработки наблюдается пятнистая структура. Самое главное в этот момент остановиться и не продолжать резание. Дальнейшую доработку поверхности лучше провести пришлифовкой с седлом.С новыми клапанами, как правило, проблем нет, однако к новым отечественным клапанам и различным подделкам следует относиться как к б/у и тщательно контролировать все параметры. К этому призывает весь опыт восстановления головок блока. Основная характеристика подделки - низкая цена. Она очень привлекательна при покупке, но убытки впоследствии будут во много раз больше.
sites.google.com
Ремонт головки блока: как избавиться от притирки, притирка клапанов и сёдел клапанов
Как известно, при ремонте головок блока цилиндров нередко обнаруживается износ клапанов. Клапаны при этом могут быть изношены по фаске (она приобретает характерную вогнутую форму), стержню и его торцу, по которому клапан контактирует с толкателем. Естественно, изношенные детали не могут нормально работать в отремонтированном двигателе
Как обычно решают такую проблему? Разумеется, самое простое решение — заменить клапаны на новые и забыть о проблеме. Но, как обычно, простое оказывается далеко не лучшим. Например, новые детали могут быть весьма недешевы, особенно, если цену 1 клапана надо умножить на их потребное количество (16, 24, 32, а то и все 48). Кроме того, клапаны на некоторые моторы могут оказаться в «длинном» заказе, и их удастся получить не раньше чем через 2-3 недели, а то и месяц, что уже никак не назовешь не только простым, но и рациональным способом решения проблемы.
Вот тогда и встает вопрос о ремонте. Такое возможно, когда стержень клапана практически не изношен, в то время как фаска тарелки и торцевая поверхность стержня потеряли первоначальную геометрию в результате длительной работы в паре с сопряженными деталями (с седлом и толкателем соответственно). А здесь есть определенное количество вариантов.
Дело мастера боится?
Некоторые «мастера», например, вообще не придают значения фаске и торцу. Поправили седла ручными фрезами типа NEWAY — и «в путь», берут и притирают изношенную фаску к седлу в надежде, что притирка все исправит. Даже проверяют потом посадку клапанов с помощью керосина — видимо, прочитали когда-то об этом в древних писаниях эдак полувековой давности. Только, к сожалению, чудес не бывает — такую «работу» хорошей никак не назовешь, тем более что на торец стержня в подобных случаях обычно внимания совсем не обращают. В результате и клапаны не ходят, прогорают из-за неправильного сопряжения с седлом, и мотор стучит по причине «косого» контакта торца с толкателем.
Более грамотные покупают специальный инструмент для обработки седел клапанов. Такой, к примеру, тоже выпускает известная фирма NEWAY. Спору нет, вещь красивая, да и недорогая. Но, к сожалению, имеет целый ряд недостатков. Так, с помощью этого приспособления практически не удается исправить биение фаски относительно стержня, если таковое имеет место. Кроме того, биение уже обработанной фаски в среднем получается довольно большим, и редко выходит меньше 0,02-0,03мм (фаска нового клапана «бьет» не больше 0,01мм). В довершении всего, резцы, используемые в приспособлении, формируют микропрофиль поверхности, весьма далекий от идеала, что требует обязательной притирки для сглаживания микронеровностей. В общем, сил затрачивается порядком, а хорошего выходит мало. И, заметьте, везде требуется эта притирка. Видимо, неспроста…
О «доброй» притирке замолвите слово…
Притиркой, как известно, называют процесс «пристукивания» и «пришлепывания» клапана к седлу с абразивной пастой. Проводится такая операция вручную, с помощью соответствующего приспособления, позволяющего вращать и «пристукивать» клапан. В результате этого отдельные неровности и погрешности предварительной обработки седла и фаски клапана удается сгладить, что делает посадку клапана более плотной.
А когда ее, притирку, применяют? Очевидно, тогда, когда детали обработаны из рук вон плохо и криво. Тогда три сильнее и дольше, и получишь то, что хотел — герметичность. Только никакого профиля сопрягаемых поверхностей, углов там всяких на фасках, уже не будет — паста все сотрет и сгладит.
А так уж она нужна, эта притирка? Ведь очевидно и другое — чем точнее обработаны фаска и седло, тем меньше в ней, притирке, потребность. Например, в серийном производстве моторов такой процесс не применяется — не только по причине больших затрат времени, но и вследствие высокой точности обработки сопряженных деталей. При этом притирка не только не улучшает, а наоборот, ухудшает прилегание клапана к седлу и герметичность сопряжения.
С другой стороны, притирка во многих случаях наносит значительный ущерб долговечности клапанного механизма. Например, на двигателях нередко применяются седла из специального чугуна и спеченных материалов. А они обладают пористостью, и во время притирки поры заполняются абразивом. В дальнейшем при работе двигателя абразив поступает в зону контакта клапана с седлом, что приводит к интенсивному изнашиванию сопряженных поверхностей (поскольку поверхность седла насыщена абразивными частицами, клапан изнашивается сильнее). Особенно сильно страдают от притирки клапаны некоторых современных двигателей, у которых для улучшения теплоотдачи и снижения трения в материале седла содержится бронза.
Лет 50 назад чем обрабатывались, к примеру, седла клапанов? Правильно (как это вы догадались?), с помощью ручных фрез, в лучшем случае. Потому что хорошего оборудования для ремонта седел наша промышленность как-то не освоила. Как работает ручная фреза, тоже понятно — криво и косо. Тогда, чтобы исправить ее «работу», и надо было притирать — долго и тщательно.
А какие двигатели ремонтировались в те далекие времена? Как правило, это были тихоходные нижнеклапанные монстры, которые нынче увидишь не во всяком музее. Их удельная мощность (на 1 литр объема) едва дотягивала до 25л. с., обороты — до 3500, а степень сжатия 7,0 казалась пределом фантазии.
С какими же клапанами и седлами имели дело наши дедушки? В принципе, с такими же, как и сейчас, если не считать что самый тонкий стержень клапана был 9мм, а самая узкая фаска — около 3мм.
А что мы имеем сегодня? Удельная мощность современных двигателей выросла почти в четыре раза, обороты — вдвое, степень сжатия перевалила за 11. При этом диаметр стержня клапанов уменьшился до 5,5-6,0мм, а ширина фасок — в три (!) раза.
Несмотря на такие достижения мировой автопромышленности, у нас в России автосервисы по-прежнему, как и полвека назад, дружно трут. Притирают, понимаешь, седла к клапанам, а клапаны к седлам, невзирая на год выпуска, марку и модель двигателя. И нисколько не задумываются о том, что на дворе уже 21-й век, и ему соответствует не только техника, но и давно применяемые во всем мире ремонтные технологии, включая оборудование для ремонта. Но нет, отдельные «ученые», видимо, настолько досконально, от корки до корки, изучили древние фолианты, что даже умудряются герметичность седел «на керосин» проверять! Хотя о чем это мы — такие умельцы обычно ничего не читают, а любят народный фольклор, устные предания «старины глубокой».
Завидная консервативность, не правда ли? Помните Райкина: их бы энергию, да в мирных целях! И электрический ток вырабатывать. Потому как, если ко всем «притирщикам» динамо-машину подключить, то энергии на целую ГЭС получить можно. На радость Чубайсу.
К сожалению, а может, к счастью, автосервисы пока в РАО ЕС не входят. Поэтому делать все надо грамотно, ориентируясь не на дедушек в ватниках, а на современные технологии и знания процессов, происходящих в двигателе. Именно по этой причине все ремонтные технологии для клапанов и седел следует рассматривать, в 1-ю очередь, с точки зрения потребности в притирке после обработки — если притирка не требуется, то технология по точности обработки не уступает серийной, ее следует признать удовлетворительной и рекомендовать для ремонтного производства. Напротив, если притирка необходима, то технология неудовлетворительна, и применять ее нельзя (или, к примеру, применять допустимо, но только в исключительных случаях).
Так что же нужно, чтобы исключить притирку? Для этого необходимо сразу несколько условий. Очевидно, должна быть соосность седла и отверстия в направляющей втулке с одной стороны, и фаски и стержня клапана — с другой. Первое дает оборудование для ремонта седел клапанов, второе — новый качественный клапан либо оборудование для ремонта самих клапанов. Общие требования к этим ремонтным процессам, исключающие какие-либо финишные операции, в том числе, притирку, довольно жесткие — оборудование должно обеспечивать несоосность (несовпадение и/или перекос осей на базовой длине детали) соответствующих поверхностей не более четверти рабочего зазора. В данном случае это зазор между стержнем клапана и втулкой. Почему же четверть, а не половина или треть? Для ответа рассмотрим этот вопрос более подробно.
Сколько-сколько?
Допустим, седло и отверстие направляющей втулки абсолютно соосны. Тогда, очевидно, фаска клапана будет полностью прилегать к седлу только в том случае, если несоосность фаски и стержня не превысит половины рабочего зазора стержня во втулке (перекос осей фаски и стержня в 1-м приближении не учитываем).
Но несоосность возможна и между втулкой и седлом. Тогда, разделив допуски поровну, получим очевидный результат — для того, чтобы исключить какие-либо финишные операции при ремонте седел и клапанов, необходимо выбранной технологией обеспечить несоосность втулки с седлом и стержня с фаской не более четверти рабочего зазора. Учитывая, что смещение оси одной из поверхностей относительно другой вызывает взаимное биение этих поверхностей, максимально допустимая величина этого биения будет вдвое больше смещения осей, то есть половиной от зазора во втулке.
Переведем дух и оценим результат. Если принять среднюю величину зазора между стержнем и втулкой 0,03мм, то притирка не будет нужна в случае, если все взаимные биения поверхностей уложатся в 0,015мм. Однако с учетом того, что, помимо смещения осей возможен и их перекос, допуск на биение должен быть жестче — около 0,01мм.
Результат был вполне предсказуем — как и в любом другом соединении двигателя, все огрехи производства и ремонта должны быть меньше половины рабочего зазора. Но оценим этот результат еще и с точки зрения ремонтной практики. А здесь так — никакая ручная фреза для седел или ручное приспособление для ремонта фасок клапанов даже не приблизятся к этой цифре! По причине отсутствия жесткости инструмента относительно базы, от которой ведется обработка, или вовсе из-за отсутствия этой самой базы. Это значит, что применение «гаражного» инструмента просто обрекает «гаражников» на долгую и мучительную притирку.
Ну что ж, флаг им в руки, пусть трут. Нас же интересует не гаражный, а профессиональный ремонт — для него-то что выбрать?
Скоро сказка сказывается…
Первое, что пытались в недалеком прошлом внедрить на некоторых ремонтных предприятиях — это универсальные станки. Так, для шлифовки фасок клапанов иногда приспосабливали доставшиеся в наследство от прошлых времен круглошлифовальные станки. Спору нет, хороший станок — и полдела сделано. Только вот незадача — у такого оборудования не предусмотрен зажим клапанов. Тоже не беда, проблему решали с помощью различных приспособлений, включая специальные патроны, цанговые зажимы и т. д. Тем не менее, ремонт клапанов современных двигателей на таком оборудовании остается проблематичным независимо от усилий, потраченных на доработку станка.
Еще одно подобное «решение» — обработка фаски на токарном станке. Трудности те же, но следует прибавить отвратительное качество поверхности фаски, которое практически невозможно улучшить. Естественно, в дальнейшем весьма вероятны прогары таких клапанов.
Неудачей, как правило, оканчиваются и попытки использовать отечественные специализированные станки для шлифовки фасок клапанов. Это вообще отдельная тема. В целом такое оборудование, разработанное много десятилетий назад на основе неких иностранных аналогов, могло бы в какой-то степени удовлетворить потребности отечественного ремонтного рынка. Если бы не одно «но» — его недостаточная приспособленность для ремонта тонких клапанов современных двигателей.
Так, в те далекие времена, как мы уже отмечали выше, стержень клапана был жестким и прочным, поскольку имел диаметр в среднем 9-11мм. Тогда все просто — зажимаем стержень в какой-нибудь патрон и шлифуем фаску без особых проблем. А теперь попробуйте то же самое сделать в таком патроне, если стержень 5,5мм диаметром. Что, не получается? То-то…
Проблема в том, что патрон-то не зажимает такой маленький стержень точно, да и тарелка консольно висит — шлифовальный круг ее легко отжимает. В результате биение фаски относительно стержня легко выходит за все допустимые пределы независимо от того, какой старый станок используется — универсальный или специализированный.
Не лучше обстоит дело и с оборудованием для обработки седел. Ручные фрезы мы уже рассмотрели — ничего хорошего с ними не выходит. Как правило, ничего путного не удается сделать и с помощью специальных шлифовальных машин для седел — по причине недостаточной жесткости ручных образцов или громоздкости стационарных монстров, что делает их использование для ремонта головок двигателей легковых автомобилей, особенно, современных, весьма затруднительным.
В последние годы получили распространение более совершенные ручные машины — с резцовыми головками. Такие машины сегодня выпускают не только зарубежные, но и некоторые отечественные фирмы. В этих приспособлениях удается добиться существенно большей жесткости режущей системы и точности обработки, нежели у ручных фрез. Во многом этому способствует система самоцентрирования режущего инструмента относительно базы — отверстия в направляющей втулке.
К сожалению, далеко не все такие образцы отвечают необходимым требованиям — не всегда их конструкция действительно жесткая, что негативно отражается на точности обработки седел. Поэтому неудивительно, что все попытки добиться с их помощью взаимного биения седла и втулки менее 0,02-0,03мм тоже обречены на провал. Точнее, на последующую долгую и тщательную притирку клапана к седлу. Что, в принципе, одно и тоже. Так что же, получается, выхода нет?
…Да не скоро дело делается
Поиск выхода из тупика, по нашему мнению, надо начинать с анализа рынка оборудования. Действительно, существует довольно много производителей профессионального оборудования для ремонта клапанного механизма. Но даже первый взгляд на их продукцию показывает интересную картину — многие фирмы специализируются на полной гамме станков для ремонта двигателей. Здесь и шлифовальные, и расточные, и хонинговальные для различных деталей и поверхностей — просто глаза разбегаются!
Ну что же, когда все, да еще в одном месте — это удобно. Но широкая универсальность и узкая специализация — вещи немного разные. Тем более что оборудование для ремонта головок и клапанов у этих фирм даже немного теряется среди мощных станин, шпинделей и суппортов.
В такой ситуации привлекают внимание, в 1-ю очередь, специализированные фирмы, которые, вполне вероятно, «собаку съели» на ремонте клапанных механизмов. И такая фирма есть — одна из немногих. Это французская фирма SERDI, основу производственной программы которой составляют именно «головочные» станки, а не какие-либо другие.
Возможно, кому-то нужны самые мощные, высокопроизводительные и дорогие образцы. Такие среди широкого спектра станков SERDI имеются, включая прецизионные станки с уникальной тройной воздушной системой SERDI для сверхточного базирования режущего инструмента относительно направляющей втулки. Но это сравнительно дорогостоящая техника, применение которой оправдано для довольно крупных предприятий с большими объемами выпускаемой или ремонтируемой продукции. И действительно, станки SERDI успешно работают во всем мире, включая заводы многих автомобильных фирм. Более того, оборудование данной марки давно прописано у моторостроителей и команд «Формулы-1» — там, где точность важнее всего.
Но для нас, учитывая реалии отечественного рынка ремонтных услуг, наибольший интерес представляют именно недорогие позиции, доступные многим автосервисам. Поэтому мы выбрали только два станка, отвечающие, на наш взгляд, потребностям отечественных сервисов и моторных мастерских по главному критерию «качество-цена». Это портативный станок для седел SERDI MICRO и шлифовальный станок для фасок клапанов SERDI HVR90.
Начнем с HVR90. Небольшой настольный станок позволяет с одинаковым успехом шлифовать фаски любых клапанов длиной 70-290мм со стержнями диаметром 4-14мм и тарелками 12-90мм. Что неудивительно — в конструкции станка применены специальные роликовые призмы, прижатие стержня клапана к которым осуществляется автоматически пневмоцилиндрами при включении вращения клапана. Прижатие, что характерно, точное, жесткое и однозначное.
Но это не все — одновременно еще одним пневмоцилиндром происходит нажатие на торец стержня клапана и прижатие его тарелки к вращающемуся полиуретановому наконечнику шпинделя (он и вращает клапан). Последнее действие особенно важно — висящий на призмах клапан дополнительно опирается еще и по краям, что заметно повышает жесткость всей схемы и уменьшает отжим тарелки клапана от круга при шлифовании фаски. И никаких шариковых, цанговых, кулачковых и прочих патронов и зажимов!
Очень удобно и приспособление для шлифовки торца стержня — в течение считанных секунд обрабатывается не только торец, но и его фаска, если это необходимо. Ну а собственно шлифовка фаски тарелки занимает не более 5-10 секунд.
И что получается? Ставим готовый клапан на прибор, измеряющий биение фаски относительно стержня — так и есть, биение фаски не превысило 3 деления микронного индикатора, то есть 6 микрон, вдвое меньше, чем мы рассчитывали! Завидный результат, тем более что он дает возможность увеличить допуск на биение седла — с 0,010 до 0,015-0,020мм. А это неплохо, ведь процесс шлифовки обычно точнее, чем резания, поэтому на последний хотелось бы иметь допуск побольше.
Ну что ж, посмотрим теперь, что даст станок для обработки седел. SERDI MICRO снабжен специальной станиной UNICLAMP, она ставится на верстак, а уже на нее устанавливается головка блока. Станина имеет кронштейн, который одновременно позволяет прижать головку к станине и установить рабочий узел станка. Такая конструкция позволяет легко ориентировать станок на любых ГБЦ независимо от параллельности их плоскостей и угловых наклонов клапанов.
Рабочий узел включает в себя шпиндель с резцедержателем и лимбом с ценой деления в 0,02 мм и ходом в 15 мм для определения глубины обработки, а также систему ориентирования, которая позволяет наклонять шпиндель до 30 градусов в продольном направлении и дополнительно центрировать его в пределах 8 градусов в любых направлениях. Этого достаточно для всех известных головок блока.
Система центрирования полностью механическая и позволяет практически «намертво» зафиксировать положение шпинделя простым поворотом соответствующего колеса на рабочем узле. А это важно, поскольку отсутствуют различные нежесткие или недостаточно жесткие элементы в креплении шпинделя. Например, не используются разного рода магниты, нередко применяемые в аналогичных станках других производителей: магнит в системе центрирования требует идеально плоской подложки, в противном случае возникает люфт, резко снижающий точность обработки.
Еще одна интересная особенность и преимущество — в станке используется такие же твердосплавные резцы, резцедержатели и пилоты, что и в полноразмерных станках SERDI. Кстати, на станке могут применяться резцы любого профиля, но наиболее удобны так называемые мультиугловые, которые сразу формируют полный профиль седла — и рабочую, и примыкающие фаски. Такие резцы имеют всевозможные углы и ширину фасок — что называется, на любой вкус. По каталогу фирмы всегда можно заказать и получить не только любой резец, но и пилот для направляющей втулки любого диаметра из огромной номенклатуры этих изделий.
Еще одно преимущество — станок комплектуется вакуумтестером для проверки герметичности клапанов после обработки. Это имеет принципиальное значение, поскольку без нормальной проверки невозможно оценить качество ремонта (керосин не в счет — эту проверку оставим «истинным ценителям»). Вакуумтестер работает от воздушной сети, за счет эжекции создается разрежение в рабочей части прибора, которое измеряется вакуумметром. Для проверки достаточно поставить клапан в головку блока (не собирая пружину), установить на прибор специальную насадку, близкую по форме к отверстию канала, прижать ее к отверстию и нажать кнопку — прибор покажет разрежение в канале, которое не должно быть меньше 0,6 кг/см2.
Теперь осталось попробовать станок SERDI MICRO в деле. Ставим головку блока, настраиваем вылет резца (это делается быстро с помощью специального приспособления, в которое вставляется клапан) и обрабатываем последовательно несколько однотипных седел «как чисто». Теперь ставим специальное измерительное приспособление для определения взаимного биения седла и клапана и проверяем...
...Что получилось?
А получилось следующее — из 4-х обработанных седел одно имеет биение примерно 0,03мм, два — в пределах 0,04-0,05мм и одно — около 0,06мм. Проверяем на вакуум — везде одинаковая герметичность, разрежение примерно 0,7 кг/см2. Непонятно почему, но биения седел вышли за те допустимые пределы, о которых мы говорили выше…
Обрабатываем еще ряд, более медленно и аккуратно — уже лучше, биения лежат в пределах 0,03-0,05мм. Что это значит, становится понятно — вручную не удается абсолютно точно установить рабочий узел станка, да и усилия при вращении шпинделя рукояткой, вполне возможно, вносят свой вклад в погрешность обработки. Нельзя исключить и погрешность самого измерения. Но интересно, что еще одна повторная обработка седел с максимальной тщательностью все-таки привела к уменьшению биения некоторых седел почти до приемлемого уровня — 0,02-0,03мм.
Итак, в конечном счете, получается суммарное биение седла и фаски клапана несколько больше, чем мы рассчитывали. Причем, основной вклад в это биение вносит погрешность обработки седла, а не фаски клапана. Интересно, а как обстоит дело с новыми заводскими деталями — головкой блока и клапанами? Берем новую ГБЦ марки ВА3 и такие же клапаны, измеряем, и…. Получаем биение седел около 0,03-0,04мм, а фасок клапанов в пределах 0,01мм — практически то же самое, что мы получили при ремонте.
Что это значит, понятно — применяя хорошее оборудование для ремонта клапанов и седел, притирку, в самом деле, можно упразднить, подтверждения чего мы и добивались нашим экспериментом. И подтвердили — оборудование SERDI действительно дает вполне надежную технологию ремонта, по результатам близкую к технологии массового производства. Но можно ли теперь совсем исключить эту пресловутую притирку из технологии ремонта? В принципе, да, но делать такое исключение надо осторожно, что называется, с умом, а именно, с обязательной проверкой и перепроверкой результатов. А как же иначе?
Опубликовано в журнале "Автомобиль и сервис" №9/2005.
www.spb-motor.ru
Ремонт головки блока - как избавиться от притирки
Как известно, при ремонте головок блока цилиндров нередко обнаруживается износ клапанов. Клапаны при этом могут быть изношены по фаске (она приобретает характерную вогнутую форму), стержню и его торцу, по которому клапан контактирует с толкателем. Естественно, изношенные детали не могут нормально работать в отремонтированном двигателе.
Как обычно решают такую проблему? Разумеется, самое простое решение — заменить клапаны на новые и забыть о проблеме. Но, как обычно, простое оказывается далеко не лучшим. Например, новые детали могут быть весьма недешевы, особенно, если цену 1 клапана надо умножить на их потребное количество (16, 24, 32, а то и все 48). Кроме того, клапаны на некоторые моторы могут оказаться в «длинном» заказе, и их удастся получить не раньше чем через 2-3 недели, а то и месяц, что уже никак не назовешь не только простым, но и рациональным способом решения проблемы.
Вот тогда и встает вопрос о ремонте. Такое возможно, когда стержень клапана практически не изношен, в то время как фаска тарелки и торцевая поверхность стержня потеряли первоначальную геометрию в результате длительной работы в паре с сопряженными деталями (с седлом и толкателем соответственно). А здесь есть определенное количество вариантов.
Дело мастера боится?
Некоторые «мастера», например, вообще не придают значения фаске и торцу. Поправили седла ручными фрезами типа NEWAY — и «в путь», берут и притирают изношенную фаску к седлу в надежде, что притирка все исправит. Даже проверяют потом посадку клапанов с помощью керосина — видимо, прочитали когда-то об этом в древних писаниях эдак полувековой давности. Только, к сожалению, чудес не бывает — такую «работу» хорошей никак не назовешь, тем более что на торец стержня в подобных случаях обычно внимания совсем не обращают. В результате и клапаны не ходят, прогорают из-за неправильного сопряжения с седлом, и мотор стучит по причине «косого» контакта торца с толкателем.
Более грамотные покупают специальный инструмент для ремонта фаски клапанов. Такой, к примеру, тоже выпускает известная фирма NEWAY. Спору нет, вещь красивая, да и недорогая. Но, к сожалению, имеет целый ряд недостатков. Так, с помощью этого приспособления практически не удается исправить биение фаски относительно стержня, если таковое имеет место. Кроме того, биение уже обработанной фаски в среднем получается довольно большим, и редко выходит меньше 0,02-0,03мм (фаска нового клапана «бьет» не больше 0,01мм). В довершении всего, резцы, используемые в приспособлении, формируют микропрофиль поверхности, весьма далекий от идеала, что требует обязательной притирки для сглаживания микронеровностей. В общем, сил затрачивается порядком, а хорошего выходит мало. И, заметьте, везде требуется эта притирка. Видимо, неспроста…
О «доброй» притирке замолвите слово…
"Притирка клапанов" - Притиркой, как известно, называют процесс «пристукивания» и «пришлепывания» клапана к седлу с абразивной пастой. Проводится такая операция вручную, с помощью соответствующего приспособления, позволяющего вращать и «пристукивать» клапан. В результате этого отдельные неровности и погрешности предварительной обработки седла и фаски клапана удается сгладить, что делает посадку клапана более плотной.
А когда ее, притирку, применяют? Очевидно, тогда, когда детали обработаны из рук вон плохо и криво. Тогда три сильнее и дольше, и получишь то, что хотел — герметичность. Только никакого профиля сопрягаемых поверхностей, углов там всяких на фасках, уже не будет — паста все сотрет и сгладит.
А так уж она нужна, эта притирка? Ведь очевидно и другое — чем точнее обработаны фаска и седло, тем меньше в ней, притирке, потребность. Например, в серийном производстве моторов такой процесс не применяется — не только по причине больших затрат времени, но и вследствие высокой точности обработки сопряженных деталей. При этом притирка не только не улучшает, а наоборот, ухудшает прилегание клапана к седлу и герметичность сопряжения.
С другой стороны, притирка во многих случаях наносит значительный ущерб долговечности клапанного механизма. Например, на двигателях нередко применяются седла из специального чугуна и спеченных материалов. А они обладают пористостью, и во время притирки поры заполняются абразивом. В дальнейшем при работе двигателя абразив поступает в зону контакта клапана с седлом, что приводит к интенсивному изнашиванию сопряженных поверхностей (поскольку поверхность седла насыщена абразивными частицами, клапан изнашивается сильнее). Особенно сильно страдают от притирки клапаны некоторых современных двигателей, у которых для улучшения теплоотдачи и снижения трения в материале седла содержится бронза.
Лет 50 назад чем обрабатывались, к примеру, седла клапанов? Правильно (как это вы догадались?), с помощью ручных фрез, в лучшем случае. Потому что хорошего оборудования для ремонта седел наша промышленность как-то не освоила. Как работает ручная фреза, тоже понятно — криво и косо. Тогда, чтобы исправить ее «работу», и надо было притирать — долго и тщательно.
А какие двигатели ремонтировались в те далекие времена? Как правило, это были тихоходные нижнеклапанные монстры, которые нынче увидишь не во всяком музее. Их удельная мощность (на 1 литр объема) едва дотягивала до 25л. с., обороты — до 3500, а степень сжатия 7,0 казалась пределом фантазии.
С какими же клапанами и седлами имели дело наши дедушки? В принципе, с такими же, как и сейчас, если не считать что самый тонкий стержень клапана был 9мм, а самая узкая фаска — около 3 мм.
А что мы имеем сегодня? Удельная мощность современных двигателей выросла почти в четыре раза, обороты — вдвое, степень сжатия перевалила за 11. При этом диаметр стержня клапанов уменьшился до 5,5-6,0 мм, а ширина фасок — в три (!) раза.
Несмотря на такие достижения мировой автопромышленности, у нас в России автосервисы по-прежнему, как и полвека назад, дружно трут. Притирают, понимаешь, седла к клапанам, а клапаны к седлам, невзирая на год выпуска, марку и модель двигателя. И нисколько не задумываются о том, что на дворе уже 21-й век, и ему соответствует не только техника, но и давно применяемые во всем мире ремонтные технологии, включая оборудование для ремонта. Но нет, отдельные «ученые», видимо, настолько досконально, от корки до корки, изучили древние фолианты, что даже умудряются герметичность седел «на керосин» проверять! Хотя о чем это мы — такие умельцы обычно ничего не читают, а любят народный фольклор, устные предания «старины глубокой».
Завидная консервативность, не правда ли? Помните Райкина: их бы энергию, да в мирных целях! И электрический ток вырабатывать. Потому как, если ко всем «притирщикам» динамо-машину подключить, то энергии на целую ГЭС получить можно. На радость Чубайсу.
К сожалению, а может, к счастью, автосервисы пока в РАО ЕС не входят. Поэтому делать все надо грамотно, ориентируясь не на дедушек в ватниках, а на современные технологии и знания процессов, происходящих в двигателе. Именно по этой причине все ремонтные технологии для клапанов и седел следует рассматривать, в 1-ю очередь, с точки зрения потребности в притирке после обработки — если притирка не требуется, то технология по точности обработки не уступает серийной, ее следует признать удовлетворительной и рекомендовать для ремонтного производства. Напротив, если притирка необходима, то технология неудовлетворительна, и применять ее нельзя (или, к примеру, применять допустимо, но только в исключительных случаях).
Так что же нужно, чтобы исключить притирку? Для этого необходимо сразу несколько условий. Очевидно, должна быть соосность седла и отверстия в направляющей втулке с одной стороны, и фаски и стержня клапана — с другой. Первое дает оборудование для ремонта седел клапанов, второе — новый качественный клапан либо оборудование для ремонта самих клапанов. Общие требования к этим ремонтным процессам, исключающие какие-либо финишные операции, в том числе, притирку, довольно жесткие — оборудование должно обеспечивать несоосность (несовпадение и/или перекос осей на базовой длине детали) соответствующих поверхностей не более четверти рабочего зазора. В данном случае это зазор между стержнем клапана и втулкой. Почему же четверть, а не половина или треть? Для ответа рассмотрим этот вопрос более подробно.
Сколько-сколько?
Допустим, седло и отверстие направляющей втулки абсолютно соосны. Тогда, очевидно, фаска клапана будет полностью прилегать к седлу только в том случае, если несоосность фаски и стержня не превысит половины рабочего зазора стержня во втулке (перекос осей фаски и стержня в 1-м приближении не учитываем).
Но несоосность возможна и между втулкой и седлом. Тогда, разделив допуски поровну, получим очевидный результат — для того, чтобы исключить какие-либо финишные операции при ремонте седел и клапанов, необходимо выбранной технологией обеспечить несоосность втулки с седлом и стержня с фаской не более четверти рабочего зазора. Учитывая, что смещение оси одной из поверхностей относительно другой вызывает взаимное биение этих поверхностей, максимально допустимая величина этого биения будет вдвое больше смещения осей, то есть половиной от зазора во втулке.
Переведем дух и оценим результат. Если принять среднюю величину зазора между стержнем и втулкой 0,03мм, то притирка не будет нужна в случае, если все взаимные биения поверхностей уложатся в 0,015мм. Однако с учетом того, что, помимо смещения осей возможен и их перекос, допуск на биение должен быть жестче — около 0,01 мм.
Результат был вполне предсказуем — как и в любом другом соединении двигателя, все огрехи производства и ремонта должны быть меньше половины рабочего зазора. Но оценим этот результат еще и с точки зрения ремонтной практики. А здесь так — никакая ручная фреза для седел или ручное приспособление для ремонта фасок клапанов даже не приблизятся к этой цифре! По причине отсутствия жесткости инструмента относительно базы, от которой ведется обработка, или вовсе из-за отсутствия этой самой базы. Это значит, что применение «гаражного» инструмента просто обрекает «гаражников» на долгую и мучительную притирку.
Ну что ж, флаг им в руки, пусть трут. Нас же интересует не гаражный, а профессиональный ремонт — для него-то что выбрать?
Скоро сказка сказывается…
Первое, что пытались в недалеком прошлом внедрить на некоторых ремонтных предприятиях — это универсальные станки. Так, для шлифовки фасок клапанов иногда приспосабливали доставшиеся в наследство от прошлых времен круглошлифовальные станки. Спору нет, хороший станок — и полдела сделано. Только вот незадача — у такого оборудования не предусмотрен зажим клапанов. Тоже не беда, проблему решали с помощью различных приспособлений, включая специальные патроны, цанговые зажимы и т. д. Тем не менее, ремонт клапанов современных двигателей на таком оборудовании остается проблематичным независимо от усилий, потраченных на доработку станка.
Еще одно подобное «решение» — обработка фаски на токарном станке. Трудности те же, но следует прибавить отвратительное качество поверхности фаски, которое практически невозможно улучшить. Естественно, в дальнейшем весьма вероятны прогары таких клапанов.
Неудачей, как правило, оканчиваются и попытки использовать отечественные специализированные станки для шлифовки фасок клапанов. Это вообще отдельная тема. В целом такое оборудование, разработанное много десятилетий назад на основе неких иностранных аналогов, могло бы в какой-то степени удовлетворить потребности отечественного ремонтного рынка. Если бы не одно «но» — его недостаточная приспособленность для ремонта тонких клапанов современных двигателей.
Так, в те далекие времена, как мы уже отмечали выше, стержень клапана был жестким и прочным, поскольку имел диаметр в среднем 9-11мм. Тогда все просто — зажимаем стержень в какой-нибудь патрон и шлифуем фаску без особых проблем. А теперь попробуйте то же самое сделать в таком патроне, если стержень 5,5мм диаметром. Что, не получается? То-то…
Проблема в том, что патрон-то не зажимает такой маленький стержень точно, да и тарелка консольно висит — шлифовальный круг ее легко отжимает. В результате биение фаски относительно стержня легко выходит за все допустимые пределы независимо от того, какой старый станок используется — универсальный или специализированный.
Не лучше обстоит дело и с оборудованием для обработки седел. Ручные фрезы мы уже рассмотрели — ничего хорошего с ними не выходит. Как правило, ничего путного не удается сделать и с помощью специальных шлифовальных машин для седел — по причине недостаточной жесткости ручных образцов или громоздкости стационарных монстров, что делает их использование для ремонта головок двигателей легковых автомобилей, особенно, современных, весьма затруднительным.
В последние годы получили распространение более совершенные ручные машины — с резцовыми головками. Такие машины сегодня выпускают не только зарубежные, но и некоторые отечественные фирмы. В этих приспособлениях удается добиться существенно большей жесткости режущей системы и точности обработки, нежели у ручных фрез. Во многом этому способствует система самоцентрирования режущего инструмента относительно базы — отверстия в направляющей втулке.
К сожалению, далеко не все такие образцы отвечают необходимым требованиям — не всегда их конструкция действительно жесткая, что негативно отражается на точности обработки седел. Поэтому неудивительно, что все попытки добиться с их помощью взаимного биения седла и втулки менее 0,02-0,03мм тоже обречены на провал. Точнее, на последующую долгую и тщательную притирку клапана к седлу. Что, в принципе, одно и тоже. Так что же, получается, выхода нет?
…Да не скоро дело делается.
Поиск выхода из тупика, по нашему мнению, надо начинать с анализа рынка оборудования. Действительно, существует довольно много производителей профессионального оборудования для ремонта клапанного механизма. Но даже первый взгляд на их продукцию показывает интересную картину — многие фирмы специализируются на полной гамме станков для ремонта двигателей. Здесь и шлифовальные, и расточные, и хонинговальные для различных деталей и поверхностей — просто глаза разбегаются!
Ну что же, когда все, да еще в одном месте — это удобно. Но широкая универсальность и узкая специализация — вещи немного разные. Тем более что оборудование для ремонта головок и клапанов у этих фирм даже немного теряется среди мощных станин, шпинделей и суппортов.
В такой ситуации привлекают внимание, в 1-ю очередь, специализированные фирмы, которые, вполне вероятно, «собаку съели» на ремонте клапанных механизмов. И такая фирма есть — одна из немногих. Это французская фирма SERDI, основу производственной программы которой составляют именно «головочные» станки, а не какие-либо другие.
Возможно, кому-то нужны самые мощные, высокопроизводительные и дорогие образцы. Такие среди широкого спектра станков SERDI имеются, включая прецизионные станки с уникальной тройной воздушной системой SERDI для сверхточного базирования режущего инструмента относительно направляющей втулки. Но это сравнительно дорогостоящая техника, применение которой оправдано для довольно крупных предприятий с большими объемами выпускаемой или ремонтируемой продукции. И действительно, станки SERDI успешно работают во всем мире, включая заводы многих автомобильных фирм. Более того, оборудование данной марки давно прописано у моторостроителей и команд «Формулы-1» — там, где точность важнее всего.
Но для нас, учитывая реалии отечественного рынка ремонтных услуг, наибольший интерес представляют именно недорогие позиции, доступные многим автосервисам. Поэтому мы выбрали только два станка, отвечающие, на наш взгляд, потребностям отечественных сервисов и моторных мастерских по главному критерию «качество-цена». Это портативный станок для седел SERDI MICRO и шлифовальный станок для фасок клапанов SERDI HVR90.
Начнем с HVR90. Небольшой настольный станок позволяет с одинаковым успехом шлифовать фаски любых клапанов длиной 70-290мм со стержнями диаметром 4-14мм и тарелками 12-90мм. Что неудивительно — в конструкции станка применены специальные роликовые призмы, прижатие стержня клапана к которым осуществляется автоматически пневмоцилиндрами при включении вращения клапана. Прижатие, что характерно, точное, жесткое и однозначное.
Но это не все — одновременно еще одним пневмоцилиндром происходит нажатие на торец стержня клапана и прижатие его тарелки к вращающемуся полиуретановому наконечнику шпинделя (он и вращает клапан). Последнее действие особенно важно — висящий на призмах клапан дополнительно опирается еще и по краям, что заметно повышает жесткость всей схемы и уменьшает отжим тарелки клапана от круга при шлифовании фаски. И никаких шариковых, цанговых, кулачковых и прочих патронов и зажимов!
Очень удобно и приспособление для шлифовки торца стержня — в течение считанных секунд обрабатывается не только торец, но и его фаска, если это необходимо. Ну а собственно шлифовка фаски тарелки занимает не более 5-10 секунд.
И что получается? Ставим готовый клапан на прибор, измеряющий биение фаски относительно стержня — так и есть, биение фаски не превысило 3 деления микронного индикатора, то есть 6 микрон, вдвое меньше, чем мы рассчитывали! Завидный результат, тем более что он дает возможность увеличить допуск на биение седла — с 0,010 до 0,015-0,020мм. А это неплохо, ведь процесс шлифовки обычно точнее, чем резания, поэтому на последний хотелось бы иметь допуск побольше.
Ну что ж, посмотрим теперь, что даст станок для обработки седел. SERDI MICRO снабжен специальной станиной UNICLAMP, она ставится на верстак, а уже на нее устанавливается головка блока. Станина имеет кронштейн, который одновременно позволяет прижать головку к станине и установить рабочий узел станка. Такая конструкция позволяет легко ориентировать станок на любых ГБЦ независимо от параллельности их плоскостей и угловых наклонов клапанов.
Рабочий узел включает в себя шпиндель с резцедержателем и лимбом с ценой деления в 0,02 мм и ходом в 15 мм для определения глубины обработки, а также систему ориентирования, которая позволяет наклонять шпиндель до 30 градусов в продольном направлении и дополнительно центрировать его в пределах 8 градусов в любых направлениях. Этого достаточно для всех известных головок блока.
Система центрирования полностью механическая и позволяет практически «намертво» зафиксировать положение шпинделя простым поворотом соответствующего колеса на рабочем узле. А это важно, поскольку отсутствуют различные нежесткие или недостаточно жесткие элементы в креплении шпинделя. Например, не используются разного рода магниты, нередко применяемые в аналогичных станках других производителей: магнит в системе центрирования требует идеально плоской подложки, в противном случае возникает люфт, резко снижающий точность обработки.
Еще одна интересная особенность и преимущество — в станке используется такие же твердосплавные резцы, резцедержатели и пилоты, что и в полноразмерных станках SERDI. Кстати, на станке могут применяться резцы любого профиля, но наиболее удобны так называемые мультиугловые, которые сразу формируют полный профиль седла — и рабочую, и примыкающие фаски. Такие резцы имеют всевозможные углы и ширину фасок — что называется, на любой вкус. По каталогу фирмы всегда можно заказать и получить не только любой резец, но и пилот для направляющей втулки любого диаметра из огромной номенклатуры этих изделий.
Еще одно преимущество — станок комплектуется вакуумтестером для проверки герметичности клапанов после обработки. Это имеет принципиальное значение, поскольку без нормальной проверки невозможно оценить качество ремонта (керосин не в счет — эту проверку оставим «истинным ценителям»). Вакуумтестер работает от воздушной сети, за счет эжекции создается разрежение в рабочей части прибора, которое измеряется вакуумметром. Для проверки достаточно поставить клапан в головку блока (не собирая пружину), установить на прибор специальную насадку, близкую по форме к отверстию канала, прижать ее к отверстию и нажать кнопку — прибор покажет разрежение в канале, которое не должно быть меньше 0,6 кг/см2.
Теперь осталось попробовать станок SERDI MICRO в деле. Ставим головку блока, настраиваем вылет резца (это делается быстро с помощью специального приспособления, в которое вставляется клапан) и обрабатываем последовательно несколько однотипных седел «как чисто». Теперь ставим специальное измерительное приспособление для определения взаимного биения седла и клапана и проверяем, что получилось.
А получилось следующее — из 4-х обработанных седел одно имеет биение примерно 0,03мм, два — в пределах 0,04-0,05мм и одно — около 0,06мм. Проверяем на вакуум — везде одинаковая герметичность, разрежение примерно 0,7 кг/см2. Непонятно почему, но биения седел вышли за те допустимые пределы, о которых мы говорили выше…
Обрабатываем еще ряд, более медленно и аккуратно — уже лучше, биения лежат в пределах 0,03-0,05мм. Что это значит, становится понятно — вручную не удается абсолютно точно установить рабочий узел станка, да и усилия при вращении шпинделя рукояткой, вполне возможно, вносят свой вклад в погрешность обработки. Нельзя исключить и погрешность самого измерения. Но интересно, что еще одна повторная обработка седел с максимальной тщательностью все-таки привела к уменьшению биения некоторых седел почти до приемлемого уровня — 0,02-0,03 мм.
Итак, в конечном счете, получается суммарное биение седла и фаски клапана несколько больше, чем мы рассчитывали. Причем, основной вклад в это биение вносит погрешность обработки седла, а не фаски клапана. Интересно, а как обстоит дело с новыми заводскими деталями — головкой блока и клапанами? Берем новую ГБЦ марки ВАЗ и такие же клапаны, измеряем, и…. Получаем биение седел около 0,03-0,04мм, а фасок клапанов в пределах 0,01мм — практически то же самое, что мы получили при ремонте.
Что это значит, понятно — применяя хорошее оборудование для ремонта клапанов и седел, притирку, в самом деле, можно упразднить, подтверждения чего мы и добивались нашим экспериментом. И подтвердили — оборудование SERDI действительно дает вполне надежную технологию ремонта, по результатам близкую к технологии массового производства. Но можно ли теперь совсем исключить эту пресловутую притирку из технологии ремонта? В принципе, да, но делать такое исключение надо осторожно, что называется, с умом, а именно, с обязательной проверкой и перепроверкой результатов. А как же иначе? ?
www.motornn.ru
Персональный сайт - ремонт ГБЦ своими руками
Как менять седла и направляющие клапановИсходим из того, что трещин в теле головки нет (при нормальной эксплуатации они большая редкость), а вот клапанные седла почти всегда имеют износ, да еще и подгорают. Тем не менее начинать с них нельзя. Технологической базой для обработки седел служат направляющие втулки клапанов, поэтому их восстанавливают первыми.Втулки из сравнительно мягких материалов (бронзы, например) можно ремонтировать, для этого существует специальный инструмент. Он выпускается фирмами Sunnen и Neway. Принцип действия такого инструмента заключается в прокатывании роликом рабочей поверхности отверстия. В результате там образуется спиральная канавка, у краев которой пластичный металл поднимается вверх. После калибровки отверстия разверткой нужного диаметра удается восстановить номинальный зазор между стержнем клапана и втулкой.
Очевидные достоинства способа — доступность и невысокая цена инструмента. Но недостатков больше. Удается отремонтировать только втулки с относительно небольшим износом (не более 0,1 мм). Спиральная канавка несколько улучшает смазку стержня клапана, но одновременно уменьшает рабочую поверхность втулки. Это значит, что давление стержня на единицу опорной площади возрастает и отремонтированная втулка изнашивается примерно в два раза быстрее по сравнению с новой. Поэтому основным способом ремонта узла все-таки остается замена втулок.
Технология выпрессовки старых втулок может быть разной, но чаще всего применяют ударный способ. Со стороны седла на втулку устанавливают латунную или бронзовую оправку, по которой наносят удары молотком. Чтобы не повредить посадочное гнездо в головке, оправка должна быть ступенчатой: по меньшему диаметру она с небольшим зазором входит во втулку на глубину 30—40 мм, а по большему — свободно проходит через гнездо в головке цилиндров.
Втулки из бронзы не создают больших проблем при выпрессовке, обычно они устанавливаются в головку с небольшим натягом. При выпрессовке "твердых” втулок головку желательно нагреть до 150 градусов, чтобы несколько уменьшить натяг (у материала втулки коэффициент линейного расширения меньше, чем у алюминиевого сплава головки блока). Нагревать головку лучше в электропечи, но в условиях гаража подойдет и бытовая электроплитка.
Иногда для выпрессовки втулок применяют винтовые приспособления. Они не получили широкого распространения из-за ограниченного усилия, хотя шансов повредить гнездо здесь меньше.
Если ни один из способов не позволяет выпрессовать втулку из-за слишком плотной посадки в гнезде, ее приходится высверливать. Эту работу следует выполнять на станке, обеспечивающем соосность сверла и отверстия втулки. Обычный сверлильный станок тут вполне подойдет, а вот при пользовании ручной электродрели неизбежны перекосы и повреждение посадочного гнезда. Кстати, деталь лучше высверливать не полностью. При толщине стенки около 1 мм оставшуюся часть обычно удается выбить без особого труда.
Общее правило замены втулок на любых двигателях гласит: ни в коем случае нельзя запрессовывать новые детали без измерений фактического натяга. Особенно это касается отечественных двигателей, запчасти для которых нередко бывают просто бракованными. Но даже те, что успешно прошли технический контроль, тоже не отличаются стабильностью размеров. А еще случается приобрести втулки ремонтного размера под видом стандартных. Что произойдет, если пытаться их поставить, догадаться нетрудно. Поэтому надо точно измерить диаметр гнезда и новой втулки, чтобы определить натяг. Он должен быть в пределах 0,03—0,05 мм (то есть диаметр втулки больше диаметра гнезда на эту величину).
Если натяг недостаточен из-за "слабого” гнезда, придется увеличивать его диаметр, чтобы установить втулку ремонтного размера. Эту работу также следует выполнять только на станке во избежание перекоса (увода) отверстия. Натяг для ремонтной втулки желательно сделать несколько большим, поскольку в старом гнезде материал на поверхности уже деформирован, а в новом нет, да и шероховатость поверхности здесь больше.
Перед запрессовкой надо обеспечить разность температуры деталей: головку нагреть до 150 градусов, а втулки охладить (например, в морозильной камере или с использованием сухого льда). Запрессовку выполняют быстро, двумя-тремя ударами молотка по оправке. Если втулка имеет тонкий поясок для посадки маслосъемного колпачка (как у двигателей ВАЗ), то оправка не должна опираться на этот поясок ни с одной стороны, иначе втулка сломается.
Некоторые мотористы запрессовывают втулки "вхолодную”, без нагрева и охлаждения деталей. Это плохо. Алюминиевый сплав при большом натяге деформируется, и реальный натяг уменьшается. Когда при работе двигателя посадка естественным образом ослабляется (не следует забывать, что алюминиевая головка при нагревании расширяется больше, чем чугунная втулка), клапан в такой втулке начинает перегреваться. Это связано с нарушением отвода тепла от стержня клапана к головке. В дальнейшем втулка начнет "ездить” в гнезде. Иными словами — потребуется повторный ремонт, причем сложнее предыдущего. После запрессовки втулок и остывания головки их отверстия калибруют развертками. Здесь тоже есть свои хитрости. Желательно применять специальные алмазные развертки — они дают стабильный размер отверстия при довольно долгой работе. Простые ручные развертки из инструментальной стали быстро изнашиваются, обычно их хватает на одну-две головки.
Обработав отверстия, надо обязательно проверить зазоры клапанов во втулках. Для впускных клапанов они должны быть в пределах 0,02—0,04 мм, для выпускных — 0,03—0,04 мм. Стремиться к минимальным зазорам не следует, особенно у выпускных клапанов, поскольку это чревато их заклиниванием при работе.
Основные задачи, решаемые при ремонте седел, — обеспечение соосности рабочей фаски и отверстия втулки и создание определенного профиля седла, рекомендуемого заводом-изготовителем для данной модели двигателя.
Для обработки седел применяют различный инструмент, разные приспособления и станки. В гараже чаще всего используют ручные угловые фрезы с жестким креплением на направляющем стержне (пилоте). Фрезы обычно имеют углы при вершине 30, 45 и 60 град., хотя встречаются и другие (например, 15 и 75 град.). Такие фрезы могут быть изготовлены из инструментальной стали или с твердосплавными пластинами.
Основной недостаток данного инструмента — люфт пилота в направляющей втулке, особенно когда у нее есть какой-либо износ. Из-за люфта очень трудно обеспечить соосность седла и втулки.
Несколько лучше качество обработки у инструмента с неподвижным закреплением пилота во втулке и свободной посадкой фрезы на пилоте. Таковы изделия некоторых американских фирм, включая Neway, продукция которой есть на нашем рынке. Ее характерная особенность — твердосплавные пластины, закрепляемые на резцовой головке, и очень малый зазор в соединении резцовой головки с пилотом. Интересна и особая конструкция пилота, позволяющая зафиксировать его без перекосов даже в тех случаях, когда втулка имеет явный износ. Комплект доступен по цене, хотя и заметно дороже отечественных угловых фрез.
Общим недостатком всех инструментов данного типа является большая сложность обеспечения соосности седла и втулки, если изначально этой соосности не было. Это как раз и случается после замены втулки. Вся загвоздка в деформации пилота: чем сильнее прижимаешь инструмент к седлу, тем больше изгибается пилот и тем хуже будет результат. Кстати, некоторые иностранные фирмы, например Sunnen, делают специальные измерительные приборы для контроля соосности седла и втулки. Недостатки простых инструментов делают применение более дорогих приспособлений вполне оправданным. Среди них более доступны портативные приспособления фирм Sunnen и Mira, проверенные практикой. При профессиональном ремонте используют шлифовальные приспособления различных типов, а также специализированные расточные станки для комплексного ремонта головок блоков. Достоинства такого оборудования очевидны, но цена высока, поэтому у нас оно пока не получило широкого распространения. При обработке формируют определенный профиль седла: уплотнительную фаску и две фаски, примыкающие к ней. Здесь надо руководствоваться данными производителей автомобиля, но есть и некоторые общие рекомендации. У подавляющего большинства моторов уплотнительная фаска имеет угол 45 град. и ширину примерно 1,5 мм. Примыкающие фаски чаще сделаны под углами 30 и 60 град., хотя изредка встречаются седла с более сложным профилем.
Если для ремонта используют ручные фрезы и резцовые головки, то предварительную обработку уплотнительной фаски ведут до тех пор, пока не получится ровная поверхность без каких-либо дефектов.
С новыми клапанами, как правило, проблем нет. Проблемы появляются, если в дело идут уже работавшие клапаны (такая ситуация характерна для иномарок). У старых клапанов фаски обычно в той или иной степени изношены, без их дополнительной обработки хорошего уплотнения тарелки с седлом не получить.
Ремонт клапана — дело не очень простое и тоже требует соответствующего оборудования. Начинать надо с проверки деформации стержня, для чего существуют различные способы. Наиболее просто (но не слишком точно) проверить клапан, положив его на призмы и измерив индикатором биение тарелки. Гораздо лучше воспользоваться специальным измерительным приспособлением. Подобные приборы зарубежного производства можно найти и у нас, причем по вполне доступной цене.
У хорошего клапана биение рабочей фаски относительно стержня не превышает половину рабочего зазора стержня в направляющей втулке, то есть не более 0,02 мм. Если же оно более 0,05 мм, деформированный клапан лучше заменить. Кстати, у новых отечественных клапанов биение фаски зачастую не укладывается в допустимые пределы, поэтому использовать эти детали без проверки не рекомендуется.
Обрабатывать фаску желательно на хорошем оборудовании, иначе трудно обеспечить точность обработки. Для этого вполне подходят универсальные круглошлифовальные станки, которые есть на многих промышленных предприятиях. За рубежом выпускают портативные станки для ремонта клапанов (на них также шлифуют изношенные торцы), но для большинства мастерских они слишком дороги. Существуют и простые приспособления для ручной обработки фаски клапана. Подобное приспособление с твердосплавными резцами выпускает уже упомянутая выше фирма Neway. Стоит оно относительно недорого, но, к сожалению, не вполне заменяет хороший станок.
Окончательная обработка стыка клапана и седла — это известная многим притирка клапанов. Сегодня на Западе при профессиональном ремонте такая операция уже практически не применяется. Если седло и фаска клапана обработаны точно (а это обеспечивается только специализированными станками или приспособлениями), то притирка не только не нужна, но скорее вредна. Другое дело при ручной обработке деталей фрезами и резцовыми головками. Поверхности после ремонта здесь могут иметь далеко не идеальную форму и шероховатость.
Притирать клапаны лучше всего корундовой абразивной пастой или порошком зернистостью 20—50 мкм, смешанным с маслом. Использовать алмазные пасты не стоит, поскольку алмаз имеет свойство внедряться в материал притираемых деталей (в частности, в седло). В дальнейшем это может значительно ускорить износ деталей.
Пасту наносят на фаску, клапан вручную притирают круговыми движениями в обе стороны, периодически отрывая от седла. Для привода клапана удобно использовать специальную рукоятку с цанговым зажимом. В некоторых мастерских применяют электропривод, но от него лучше отказаться — можно повредить притираемые детали или получить неоптимальные фаски из-за больших и плохо контролируемых усилий и скорости обработки.
Притирка не должна быть долгой, на каждый клапан обычно хватает 1—2 минут. Притертые поверхности приобретают серый матовый оттенок, по которому легко определить качество работы. Если обнаружено значительное неприлегание, то притирать клапан дальше не следует, лучше повторить обработку седла или клапана описанными выше методами. Иначе после "глубокой” притирки фаски на деталях приобретут закругленную форму, как после длительной работы в двигателе.
И еще: надо иметь в виду, что притирка нужна не столько для обработки, сколько для контроля качества сопряжения. Если притертые поверхности вытереть насухо и несколько раз провернуть клапан в обе стороны, прижимая его к седлу, то на фасках деталей появится блестящая линия. Получится она замкнутой, проходящей по всей окружности — значит, все сделано правильно и прилегание деталей хорошее.
melkay.ucoz.ru