В Самарской области открыли производство свечей зажигания. Где производятся свечи зажигания поставляемые в россию
Свечной завод Bosch: один в поле – воин!
Россия активно стремится к повышению уровня локализации, особенно в автопроизводстве, а между тем в стране функционирует всего лишь один завод по производству свечей зажигания. Хотя свечи – не нам объяснять – чрезвычайно важный компонент, без которого двигатель автомобиля попросту не запустится. Этот завод – расположенное в городе Энгельсе предприятие «Роберт Бош Саратов».
Исторический воин
Действительно факт остается фактом, но все попытки запустить другие проекты по производству свечей зажигания в нашей стране, так или иначе, претерпели неудачу. Единственный, продолжающий успешно работать – это бывший «Завод Автотракторных Запальных Свечей (ЗАЗС)» ведущий свою историю с 1942 года.
Начинался он как «Завод керамических изделий». После войны здесь наладили выпуск сначала только изоляторов для свечей зажигания, а чуть позже все производство свечей зажигания было перенесено сюда. В советский период здесь изготавливались свечи зажигания для автомобилей ГАЗ, ВАЗ, УАЗ, двигателей ЗМЗ, грузовиков ЗИЛ, КамАЗ, «Урал», автобусов ПАЗ и РАФ, мотоциклов ИЖ, мотопил «Тайга». Свечи зажигания, выпущенные на заводе в г. Энгельс, использовались для розжига дизельного топлива в подогревателе автомобилей КамАЗ, а также в стационарных бензиновых двигателях УД-15, -25 и их модификациях.
Но советская эпоха закончилась… И началась круговерть постперестроечной и первокапиталистической неразберихи. В этой бесноватой пляске сгинули многие предприятия отечественного автопрома, продукция которых прежде пользовалась неизменной популярностью населения. Такая же участь могла постигнуть и фабрику в Энгельсе. Сохранить предприятие работоспособным и эффективным позволили тесные отношения с Bosch. Дело в том, что к середине 90-х годов прошлого века объемы продаж и популярность свечей Bosch в России достигли того уровня, при котором было целесообразно начать локальное производство.
Поэтому в 1997 году Robert Bosch GmbH приобрела контрольный пакет акций открытого акционерного общества «Завод автотракторных запальных свечей». В 2001 г. была выпущена первая свеча с логотипом Bosch. А в 2004 году произошло объединение «БОШ-Саратов», выпускающего компоненты впрыска топлива, и «ЗАЗС» в одно предприятие, которое в сентябре 2004 было переименовано в «Роберт Бош Саратов». 2008 г. ознаменовался тем, что Bosch стал 100% владельцем завода, располагающегося сегодня на территории 236 тыс. м2 с площадью строений – 70 тыс. м2.
Флагманское предприятие советской эпохи и сегодня остается одним из передовых в российской автокомпонентной отрасли. В настоящее время оно, как уже было сказано, является единственным в России производителем широкого ассортимента свечей зажигания, предназначенных для двигателей российских и зарубежных легковых и грузовых автомобилей, автобусов, мотоциклов, мопедов, мотороллеров, мотолодок, мотопил и прочих устройств, использующих двигатели с воспламенением от искры.
Ежегодно здесь изготавливается более 50 млн свечей зажигания, около 60% из которых идет на экспорт. Руководство предприятия отлично понимает задачи стоящие сейчас перед российскими автокомпонентщиками, главный приоритет которых в импортозамещении. И предприятие могло бы выпускать больше единиц продукции, Bosch мог бы усилить свое присутствие здесь, но пока в России выпускается лишь около 0,8 млн двигателей дальнейшее увеличение энгельсовского производства лишено смысла – оно и так с лихвой перекрывает потребности рынка.
На заводе выпускаются свечи с одним и несколькими боковыми электродами; свечи, содержащие редкоземельный металл иттрий; свечи, специально разработанные для двигателей, работающих на газе и многие другие. Бренды: Bosch, ЭЗ, APS Приоритет. Среди клиентов завода АвтоВАЗ, «Группа ГАЗ», КАМАЗ, УАЗ, ЯМЗ, Daimler, GM, BMW, Renault, VW и Ford – на российские конвейеры всех этих автомобиле- и двигателестроителей поступает продукция «Роберт Бош Саратов». Естественно предприятие обладает всеми необходимыми сертификатами: ISO 14001 и ISO/TS 16949.
За последние 10 лет производство свечей на заводе в г. Энгельс изменилось практически полностью. Установлено и используется высокотехнологичное оборудование, осуществляется постоянный многоуровневый контроль качества. Одним из способов обеспечения высокого уровня качества продукции является заключение договоров на поставку сырья и материалов c международными поставщиками компании Bosch. О высоком уровне качества готовой продукции говори и такой факт: за последние 5 лет уровень отказов свечей зажигания из Энгельса у производителей автотехники снизился в разы – с 67 ppm в 2009 г. до 0,35 ppm в 2013 г. То есть возвращается лишь 0,35 ед. готовой продукции из 1 млн ед. выпущенной.
Все это позволяет предприятию показывать высокие результаты при проведении аудита его партнерами. Не так давно – в феврале 2014 г. – в системе менеджмента качества Renault предприятие было переведено на более высокий уровень с поставщика «С» на «В».
На поточной линии
Производство свечи зажигания можно условно разделить на два крупных производственных блока. Первый – керамический, где изготавливаются изоляторы. Второй – металлообрабатывающий, отвечающий за выпуск корпусов и металлических компонентов. Третий – сборочный участок, включающий собственно сборку и упаковку готовой продукции. Пройдемся по каждому из этих этапов внимательнее.
Основной продукт керамического производства – изолятор: компонент довольно ответственный и чрезвычайно значимый. На сегодняшний день завод освоил изготовление трех видов керамики. Это керамика, которая выдерживает 35 кВ, 50 кВ и 60 кВ на мм3. Последняя была введена в производственную программу где-то полтора года назад по запросу Ford, нуждающегося в свечах с изоляторами очень высокой электропрочности.
Изготовление изолятора начинается с помола исходного сырья – глинозема (Al2O3), из которого делается керамика – полный диэлектрик. Кстати, из этого же материала делается и алюминий – полный проводник. Но разные технологические процессы дают разные материалы.
Сырье загружается в мельницу, в мельницах находятся керамические шары, измельчающие массу. Размер зерна – 2-3 мкм. Это очень очень тонкий помол. Используются итальянские мельницы, функционирующие практически в автоматическом режиме. Глинозем, которого в смеси более 95%, закупается за границей, поскольку в данный момент в России, к сожалению, необходимый глинозем не производится. Другие компоненты, которых в смеси несравненно меньшее количество, как например, мел – приобретаются в России и странах Содружества.
Прежде глинозем закупали в Бокситогорск – глинозем при свечном производстве используется специальный, не тот из которого делают алюминий. Теперь это производство закрыто из-за нерентабельности – ну не интересно делать в России керамику, проще гнать тонны глинозема в гигантских объемах для изготовления алюминия, нежели небольшие партии для керамических производств. Ну да мы отвлеклись на частный случай извечных российских парадоксов – с одной стороны изо всех сил рвемся к локализации, а с другой... Возвращаемся, в общем, к технологическому процессу.
Получившийся шликер (шликер (нем. Schlicker) – используемая в производстве керамики кашеообразная, мягкая масса, смешанная с водой) перекачивается в большие емкости. Поскольку речь идет о керамике, на всех этапах процессах производится фильтрация самыми различными и наиболее эффективными способами: виброфильтрация, магнитная сепарация и проч. – вылавливаются все возможные загрязнения, которые потенциально могут присутствовать. В противном случае заданной электропрочности не достичь.
Затем согласно фирменному рецепту добавляются связующие компоненты, после чего начинается процесс получения пресс-порошка: шликер под высоким давлением порядка 40-50 атм. через отверстие диаметром 0,5 мм распыляется внутри особой колбы. Сверху колбы через горелку подается горячий воздух. Под воздействием создаваемым завихрениями горячего воздуха, буквально, «в ритме вальса» частички собираются в гранулы.
Их размер уже 30-50 мкм. В зависимости от вида керамики по электропрочности реализуются в целом идентичные но в нюансах немного отличные техпроцессы: это и тонкость помола, и давление на пресс-формовочных машинах и проч. И, конечно же различаются глиноземы: для более высокой по электропрочности керамики – более «чистый» с точки зрения химического состава.
Далее следует формование изолятора. Пресс-порошок поступает в резиновую матрицу, где сжимается под давлением 400-500 бар. Получается заготовка, которая потом придается нужная форма в зависимости от вида изолятора. Сошлифованный при обработке материал используется повторно. Потери на всем технологическом цикле ничтожны – около 1.5%.
Очень важно понимать то что в России как и на всех заводах Bosch по всему миру используется одно и тоже производственное оборудование. А именно печь для обжига и сушки керамического сырья, холодновысадочные автоматы, токарные станки, сварочное и резьбонакатное оборудование, станки для подгибки бокового электрода и перфорирования корпуса, линии сборки изолятора и линии конечной сборки, линия упаковки и производственная оснастка одинаковы на всех заводах Bosch.
Следующий этап – ключевой. Заготовки собираются в специальные контейнеры и отправляются на обжиг. Именно в печи происходят те процессы, которые собственно и создают изолятор как таковой. На предприятии еще сохранилась советская печь, которой более 30 лет. Рядом стоит новая печь, привезенная из Бамберга с головного предприятия Bosch. Она позволила увеличить потенциальные мощности завода до 100 млн ед. продукции в год. С ее появлением сразу решились многие важнейшие вопросы. В том числе вопрос качества – колебания температуры в печи всего 5 градусов, что самым благоприятным образом сказывается на стабильности процесса. А так же вопросы экологии и экономии – с точки зрения потребления энергии эта печь гораздо более экономична.
Температура – 1600 градусов, весь цикл – порядка 33 часов: тележки (в печи помещается около 30 вагонеток, на каждой вагонетке порядка 10 тыс. заготовок) с заготовками равномерно движутся по зонам нагрева/остывания как по линии конвейера. Тут изделие из хрупкого спрессованного порошка превращается в твердый, керамический изолятор. Усадка – порядка 20%. По выходу из печи изолятор получает свои механические прочностные характеристики, достигается плотность 3,7 г/см3 и заданная электропрочность.
Параллельно изготавливается корпус и другие компоненты свечи. Корпус производится из прутка: за 6 ударов (каждый порядка 250 т) пресса формируется заготовка корпуса в зависимости от типа свечи. Примечательно то что, несмотря на работу сразу нескольких прессов, отбивающих мощнейшими ударами в сотни тонн замысловатых технологический ритм, в цехе не ощущается никакой вибрации. Добиться этого удалось благодаря потрясающей сбалансированности оборудования.
После получения заготовки она обрабатывается. К ней приваривается боковой электрод в зависимости опять же от типа свечи (может быть и несколько боковых электродов), накатывается резьба, производится клеймение, в цехе гальваники наносится покрытие никеля.
По соседству на нескольких линиях ведется сборка сердечника: центральный электрод, контактная голова и проч. Процесс автоматизирован. Линии получены опять же с головного предприятия из Бамберга. Впрочем не стоит думать что завод укомплектован лишь импортными станками. Особая гордость коллектива предприятия – линии сборки свечи, где выполняется окончательная сборка свечи зажигания, спроектированные и созданные на самом заводе собственным конструкторским бюро. Эти машины ни в чем не уступают привезенным из Германии. Их производительность примерно аналогичная – 30-40 тыс. в сутки.
На каждом этапе непременно контроль качества – и визуальный и технологический (в зависимости от этапа), весь брак или подозрительные изделия сразу удаляются из общего потока и потом уже более внимательно проверяются. Причем, что принципиально важно, система контроля качества изделий на всех предприятиях Bosch одинаковая. Например, везде ведется статистический контроль, проводится выборочный контроль партий, автоматическое измерение, визуальный контроль при 10-кратном увеличении, тестирование на диэлектрическую прочность, тестирование в камере солевого ткмана и прочее. Так же осуществляется надзор за производственной средой.
В финале – упаковка. Упаковка различается: одноместная, четырехместная, в коробках и блистерах и т. д., упаковочные машины автоматические и полуавтоматические.
Вот такой производственный путь проходит свеча, прежде чем оказаться в двигателе автомобиля или на прилавке магазина автозапчастей. В заключение остается только сказать, что предприятие продолжает и дальше совершенствовать продукцию расширяя модельный ряд свечей зажигания. Традиционный российский бренд ЭЗ в сентябре презентовал обновленный каталог применяемости свечей на 2014-2015г., который включил в себя большое количество новых моделей автомобилей.
В начале 2015 года ассортиментный ряд будет расширен тремя новыми модификациями свечей ЭЗ Yttrium: FR7LDC+, FR7HC+ и FR7LCX+. Модель FR7LDC+ предназначена для таких автомобилей как Chevrolet Lacetti, Renault Logan, Sandero, Clio II и Kangoo, Skoda Fabia и Octavia, Volkswagen Polo, Golf IV, Caddy и других. FR7HC+ подходит для Volkswagen Polo, Jetta, Skoda Fabia, Roomster, Rapid, Praktik, SEAT Ibiza и т.д. Третья новинка FR7LCX+ предназначена для Chevrolet Aveo, Cruze, Honda Accord, Civic и CR-V, Mazda 323 и многих других. Кроме того, в ближайшее время для всех свечей линейки ЭЗ Yttrium планируется смена дизайна картонной блистерной упаковки для соответствия единому фирменному стилю бренда ЭЗ. Порадует новинками и продукция титульного бренда – Bosch. Но об этом уже в следующих номерах журнала.
dvizhok.su
Производство свечей зажигания в Германии и России: есть ли разница?
А вам известно, что современная свеча зажигания образует искру 30 раз в секунду? Неудивительно, что расчетное количество циклов срабатываний составляет 150 миллионов раз! Для сравнения: энергосберегающая лампа рассчитана на 50 тысяч циклов. Процесс производства свечи зажигания мы увидели своими глазами. Сначала в немецком Бамберге, а затем в российском Саратове на заводах Bosch.
Как и любой компонент современного автомобиля, свеча зажигания — продукт сложный и высокотехнологичный. Более того, тенденция последнего времени такова, что по требованию производителей свеча разрабатывается под конкретный двигатель. Отсюда и многообразие типов (например, у Bosch 1250 наименований свечей), и жесткие требования к параметрам и качеству, в том числе практически полное отсутствие допусков при производстве.
Конечная сборка свечи занимает всего 0,9 секунды, но весь процесс «рождения» растянут на 6 дней! При этом большая часть времени приходится на производство керамического изолятора. Толщина его стенок может составлять всего 1 мм, но при этом он должен выдерживать напряжение 30.000 вольт, а его сопротивление должно оставаться стабильным при температурах около 1000°С.
Как утверждают представители Bosch, кроме маркировки и упаковки, разницы между продуктами для ОЕМ и АМ нет.
Сначала изготавливается пресс-порошок. Для его получения все компоненты (а это глинозем, мел, магнезия и некоторые другие) смешиваются и мелко перемалываются в специальной мельнице, после чего сушатся и остужаются — этот процесс занимает около трех дней. Получившиеся гранулы размером всего около двух микрон отправляют в пресс-форму. Из нее выходит готовая болванка, которую затем отправляют на шлифовку.
Получившаяся заготовка уже без пяти минут изолятор свечи, но она пока не обладает необходимой прочностью — ее легко сломать руками. Поэтому получившиеся детали примерно в течение суток обжигают в газовой печи. Кстати, печь работает без остановки годами, ведь на ее разогрев до рабочей температуры (1600°С) уходит около двух месяцев! Еще один любопытный момент: в процессе обжига болванка «усаживается» на 20%, но технологический процесс отработан настолько, что получают предельно точные размеры с погрешностью в пределах 0,05 мм! После термической обработки изолятор становится прочнее стали, разрушить его крайне тяжело.
Затем детали поступают на участок предварительной сборки. Там выполняется маркировка, наносится глазурь, внутрь изолятора помещается центральный электрод, заливается проводящий стеклогерметик с резистивными присадками, устанавливается контактный стержень, после чего готовый сердечник вновь подвергается короткой термообработке (35 минут при 850°С).
В соседнем цехе из легированной стали изготавливают корпус свечи. В пять этапов металлический стержень под давлением пресса превращается в заготовку. Процесс штамповки выдавливанием используется отнюдь не случайно: так достигается высокая точность, к тому же обеспечивается экономия материала. При данном методе выходит всего 15% потерь, тогда как при токарной обработке — до 60%. Но без фрезеровки не обойтись — и это уже следующий этап, после которого деталь очищается от масла и пригаров и отправляется на участок сварки, где к корпусу приваривают боковой электрод. Далее следуют нарезка резьбы, нанесение маркировки и конечный этап изготовления корпуса — покрытие никелем. Звучит просто, но каждый этап — сложный технологический процесс со своими секретами — практически везде фотосъемка запрещена.
Достать фотоаппараты нам разрешили лишь на участке предварительной и окончательной сборки. На автоматизированной линии происходит установка внутреннего уплотнительного кольца и изолятора в металлический корпус, производится обжим, обрезается и изгибается боковой электрод, устанавливается контактная гайка и наружное уплотнительное кольцо. После этого наступает очередь упаковки.
Вся разница — в Ленине?
На территории завода в Саратове он есть — памятник вождю пролетариата сохранили. На головном предприятии в Бамберге, понятное дело, Ильича мы не увидели. А есть ли другие отличия между двумя заводами и производственными процессами?
Завод в Бамберге рассчитан на большие объемы, а в Саратове более гибкая система производства, чему способствует собственная разработка — так называемые круглые столы, которые можно быстро переналадить под разные виды свечей. Между тем в России налажено производство лишь части ассортимента. Например, платиновые свечи выпускают только в Бамбурге.
Если не касаться масштабов, то следующим отличием является разная степень автоматизации. В Саратове она ниже, чем в Бамберге, так как затраты на зарплату в России меньше, и то, что в Германии делают роботы, здесь выполняется вручную. Впрочем, речь идет лишь о перемещении деталей (например, установка сырых изоляторов в капсели для обжига осуществляется вручную), а все остальные операции все равно выполняются автоматикой.
На свечном производстве в Саратове работает 431 сотрудник (в том числе иностранцы на руководящих должностях), производственная площадь составляет 9600 кв. м, освоено 385 типов свечей, в день выпускается 180.000 штук (в Бамберге — 500.000 штук ежедневно), в 2013 году ежегодный объем производства должен достигнуть 60 млн штук.
Свечи, предназначенные для поставки на конвейер, помещаются в специальные контейнеры, а те, что идут на вторичный рынок, — в картонные коробки. Как утверждают представители Bosch, кроме маркировки и упаковки, разницы между продуктами для ОЕМ и АМ нет: используются одни и те же материалы и оборудование, на каждом этапе производства — проверка качества.
А отличаются ли свечи немецкого и российского производства? Отвечая на этот вопрос, представители компании энергично убеждают в том, что независимо от места производства (а у Bosch пять свечных заводов, разбросанных по всему миру) качество продукции неизменно находится на одинаковом уровне. И для пущей убедительности рассказывают о единой системе менеджмента, контрольной, технической и координационной функции головного предприятия в Бамберге, из которого в тот же Саратов было поставлено оборудование, а сейчас поступают инструменты, сырье и отдельные компоненты для производства свечей.
Но куда показательнее то, что доля экспорта в продукции российского завода за последнее время выросла до 47%, в 2011 году получено разрешение на производство свечей на конвейеры Ford и Opel, а на вторичный рынок российские свечи поступают через единый логиcтический центр в Карлсруэ. То есть для Bosch принципиальной разницы, где произведены свечи, нет. И надпись made in Russia на фирменной упаковке самими немцами воспринимается как само собой разумеющееся.
Иван КРИШКЕВИЧ, фото автора и Bosch
Газета «АВТОБИЗНЕС»
Поделиться:autooboz.info
Анализ рынка свечей зажигания для автомобилей
Интересный факт – свечи зажигания, обязательный элемент конструкции любого двигателя внутреннего сгорания, появились раньше, чем сам автомобиль. Первый патент на свечу зажигания был выдан еще в 1860 году, правда, предназначены эти свечи были для газового двигателя. Современные свечи зажигания работают в условиях колоссальных нагрузок, поэтому производители постоянно совершенствуют свой ассортимент, предлагая все новые, более надежные и долговечные модели, что неизбежно сказывается на состоянии рынка свечей зажигания.
Несмотря на то, что сегодня рынок свечей зажигания насыщен множеством современных высокотехнологичных решений, базовая конструкция самой свечи не претерпела практически никаких изменений с прошлого века. Катушка зажигания генерирует высоковольтное напряжение, которое через входной терминал свечи подается на ее центральный электрод. Он заключен в изолятор из огнеупорного диэлектрика, отделяющий электрод от «массы». Главная задача изолятора – доставить разряд высокого напряжения к искровому промежутку без утечек. Изолятор вставлен в корпус свечи, сделанный из металла и ввернутый в резьбовое отверстие головки блока. Разряд с центрального электрода бьет в боковой электрод, который приварен к корпусу свечи. Именно с электродами связаны все значимые изменения, которые претерпели свечи зажигания за последние годы, и касаются они материалов, используемых для производства электродов, а также их количества.
Конструктивные находки
Давайте коротко вспомним основные этапы эволюции свечей зажигания. Традиционные свечи имеют один центральный и один боковой электрод. Для производства боковых электродов используется высокотемпературная сталь, причем к корпусу электрод приваривается при помощи контактной сварки. Во время работы свечи боковой электрод сильно нагревается, что может привести к возникновению калильного зажигания. Чтобы этого избежать, многие производители стали вводить в конструкцию современных свечей зажигания дополнительные боковые электроды. Одни работают не одновременно – в создании электрической дуги участвуют центральный электрод и только один из боковых. Никакой особой очередности при этом не существует, потому что предсказать, в какой из боковых электродов искра ударит в следующий раз, невозможно. Несмотря на это, конструкция успешно решает проблему с перегревом – электроды задействуются по одному и их средняя температура намного ниже, чем в обычных свечах с одним электродом. Это значительно увеличивает срок службы свечи.
Еще одна интересная находка последних лет – раздвоенный боковой электрод. Его острые концы улучшают условия ионизации горючей смеси, обрабатывая гораздо больший ее объем, и ускоряют начало ее горения. В некоторых моделях роль бокового электрода выполняет резьбовая часть свечи: на изолятор наносятся две кольцевые токопроводящие дорожки, и в результате в момент подачи напряжения на свечу возникают сразу три искры – между центральным электродом и нижней токопроводящей дорожкой, между корпусом и верхней дорожкой и между самими дорожками. В результате одна свеча поджигает горючую смесь сразу в трех местах, повышая мощность двигателя и снижая расход топлива.
Наиболее заметные изменения, как известно, произошли с центральным электродом. В традиционной конструкции для его изготовления используется никель, а современные высокотехнологичные свечи производятся с использованием сплавов с примесями платины, иридия, иттрия и других редких металлов. Они являются великолепными проводниками и используются для изготовления наконечников электродов очень малых диаметров без снижения срока службы свечи. Тонкий диаметр концентрирует заряд, ускоряя зажигание топливной смеси. Важными достоинствами таких свечей являются их относительно небольшие размеры, позволяющие использовать их в небольших, но мощных двигателях, и длительный срок их службы. Кроме того, «драгоценные» свечи достаточно толерантны к качеству топлива.
Описание исследования
Главной задачей аналитического отдела в этот раз был сбор информации о представленности брендов, предлагающих классические свечи зажигания с медно-никелевым центральным электродом. Данные были получены с помощью телефонного опроса розничных торговых точек, а также сбора информации из открытых источников – розничных магазинов и прайс-листов оптовых компаний, выложенных в интернете. Мы выделили наиболее хорошо представленные на российском рынке торговые марки свечей зажигания, а также рассчитали их среднюю стоимость. В качестве основы были взяты наиболее популярные в России модели автомобилей – Lada Priora, седан Ford Focus II и корейский Hyundai Solaris IV, произведенные в 2010 году. В результате была получена следующая картина.
Lada Priora
Система зажигания Lada Priora проста и достаточно эффективна – индивидуальные катушки зажигания и отсутствие каких-либо подвижных деталей позволяют свести к минимуму обслуживание системы и исключают необходимость различных регулировок. Представленность брендов, предлагающих свечи зажигания для отечественной «Приоры», оказалась достаточно большой. В общей сложности на рынке представлено около полутора десятков различных торговых марок свечей накаливания. Впрочем, в наш отчет вошли только 11 из них – доля остальных брендов на рынке оказалась ничтожно мала. Выделить явных лидеров по представленности в розничной торговой сети не удалось – показатели большинства брендов практически одинаковы. Верхнюю строчку в этом своеобразном рейтинге торговых марок заняли сразу два бренда – Champion и Denso, представленные в 15% всех опрошенных нами торговых точек. С отрывом всего в 1% идет немецкий бренд Bosh, сразу следом за ним – японская NGK с 13%. Свечи зажигания, произведенные под «материнским» брендом Lada, представлены только в 4% всех торговых точек.Разброс цен на свечи зажигания для Lada Priora также нельзя назвать очень большим. Свечи Lada оказались самыми недорогими – в среднем всего около 85 рублей. Свечи почти всех остальных представленных в нашем исследовании производителей оказались в среднем ценовом сегменте. Ценовое лидерство принадлежит бренду Ween – свечи зажигания этого производителя стоят в среднем около 275 рублей. Вторым номером идут свечи, выпущенные под маркой Champion, – чуть менее 210 рублей. Все остальные представленные в диаграмме производители предлагают свою продукцию по цене от 145 до 200 рублей. Средняя стоимость свечей зажигания для «Приоры» составила 167 рублей.
Ford Focus II
Ford Focus второго поколения так же оснащается простыми и надежными системами зажигания, состоящими из высоковольтной катушки, проводов и свечей. Катушка управляется электроникой, а сама система не требует регулировки и обслуживания.
Представленность различных торговых марок свечей зажигания для второго «Фокуса» так же оказалась достаточно обширной, причем и здесь выделить одного безусловного лидера не получилось – рынок поделен между производителями почти равномерно. Сразу пять торговых марок в нашем исследовании – Ford, Beru, Bosch, Champion и NGK – оказались представлены в 12% торговых точек. Всего на один процент их опередили свечи зажигания под брендом Denso, которые обнаружились в 13% всех опрошенных нами магазинов. Ненамного отстает от «золотой» пятерки швейцарская торговая марка Finwhale, представленная в 11% магазинов.
А вот разброс цен на свечи зажигания для Ford Focus второго поколения оказался совсем не таким равномерным – цены колеблются от вполне демократичных 118 рублей за никелевые свечи Bosch до почти 290 рублей за свечи торговой марки Valeo. Через отметку в 200 рублей «перевалили» также свечи Febi bilstein. Все остальные представленные в исследовании производители предлагают свою продукцию в сегменте от 130 до 170 рублей. Средняя стоимость никелевых свечей зажигания для Ford Focus II составила 168 рублей – почти столько же, сколько и для «Приоры».
Hyundai Solaris IV
Система зажигания Hyundai Solaris, как и ранее рассмотренные нами, также не имеет каких-либо отличительных особенностей – все те же катушки и свечи зажигания, управляемые микропроцессором. Свечи для этого популярного «корейца» представлены на рынке 7 брендами, причем и здесь результаты разделились между ними достаточно равномерно – разница в большинстве случаев составляет всего один процент. Условно лидирующие позиции занимает торговая марка Bosh, продукция которой представлена почти в каждом шестом магазине. С минимальным отрывом идет бренд Champion, разделивший свою позицию со свечами, произведенными под маркой Hyundai. Еще одной ступенькой ниже оказался японский бренд NGK с 15%, следом – свечи торговой марки Denso. Впервые в нашем сегодняшнем исследовании «засветился» финский бренд Grand Prix, на долю которого пришлось 10%.
Разброс цен на свечи зажигания для Hyndai Solaris тоже нельзя назвать сильно большим – почти все бренды предлагают свою продукцию в сегменте от 135 до 210 рублей. Из этой категории выпадают свечи Grand Prix, оказавшиеся самыми недорогими – средняя цена на них в большинстве торговых точек составила всего 84 рубля. Верхнюю строчку ценового рейтинга заняли свечи Bosch – они стоят в среднем 240 рублей. Свечи, произведенные на собственных заводах Hyundai, обойдутся владельцу Solaris в 205 рублей. Средняя же стоимость свечей зажигания для автомобилей этой марки составила приблизительно 165 рублей.
В заключение хочется сказать, что результаты немного удивили даже нас самих – средние цены на свечи зажигания для всех трех автомобилей оказались примерно одинаковыми. Впрочем, в нашем исследовании рассматривались только классические никелевые свечи, доля которых на рынке, по мнению специалистов, в ближайшие годы будет постепенно снижаться, и скоро они окажутся вытеснены более дорогими, но при этом более долговечными и эффективными моделями.
Комментарии специалиста:
Илья Мигушин, технический эксперт NGK Spark Plug (Eurasia):
- Основная тенденция последних двух лет – снижение доли недорогих свечей на вторичном рынке и перераспределение спроса в пользу дорогостоящих высокотехнологичных свечей и свечей, содержащих драгоценные металлы, с увеличенным интервалом замены.
В числе технологических новинок NGK – свечи с игольчатыми напайками на тонких направленных боковых электродах, выполненных из иридия и платины для предотвращения износа. Такие свечи позволяют увеличить мощность мотора благодаря генерации более мощной искры и обеспечивают надежное воспламенение при любых режимах эксплуатации двигателя. Технология применяется, в частности, в свечах ILZKFR8A7S, специально разработанных для новых двигателей M270 концерна Mercedes-Benz.
Для современных бензиновых двигателей с непосредственным впрыском предназначены свечи зажигания с ориентированным боковым электродом. Электрод приварен к металлическому корпусу, будучи ориентированным по направлению резьбы. Подобная конструкция свечей применяется в частности, для всех двигателей Mercedes, в 1,2- и 1,4-литровых моторах семейства TSI от Volkswagen.
Кроме того, в ассортименте NGK есть свечи для автомобилей, оснащённых газовым оборудованием. Иридиевый центральный электрод свечи LPG диаметром всего 0,6 мм и уменьшенный межэлектродный зазор позволяют снизить нагрузку на катушку зажигания, а использование специально сконструированного керамического изолятора с широким калильным числом, а также наличие дополнительного медного сердечника в боковом электроде позволяют поддерживать оптимальный теплоотвод при работе как на бензине, так и на газе.
Виталий Гисич, старший специалист товарной категории российского подразделения Denso:
- За последние годы всё больше автопроизводителей стали устанавливать на своих конвейерах высокоэффективные свечи зажигания с увеличенным сроком службы. И для этого есть немало объективных причин.
Первая из них - это ужесточение экологических норм. Только высокоэффективные иридиевые и платиновые свечи могут обеспечить оптимальные параметры сгорания топливной смеси при одновременном снижении энергопотребления за счет уменьшения эффективной площади разряда.
Лучшее сгорание ведет к снижению содержания вредных выбросов и экономии топлива, которое является второй причиной перехода автопроизводителей на новые типы свечей зажигания.
Третья причина в том, что процесс замены свечей стал более трудоемким, так как производители стремятся сделать двигатели более компактными и функционально более сложными. Все это ведет к усложнению операций и повышенным требованиям к исполнителю, который будет производить замену, а следовательно, и к росту стоимости замены свечей. Логично предположить, что автовладелец предпочтет свечи зажигания, интервал замены которых больше.
Обратите внимание на диаграмму, наглядно показывающую, какую долю в поставках на конвейер занимают иридиевые, платиновые и свечи суперзажигания (SIP). Доля обычных никелевых свечей на рынке постепенно будет сокращаться по мере старения автопарка либо заменяться линейками универсальных свечей типа DENSO TT(Twin Tip).
automediapro.ru
Информация о производителе NGK
АВТОЗАПЧАСТИ ДЛЯ ИНОМАРОК NGK
КиберМаркет по продаже ЗАПЧАСТЕЙ ДЛЯ ИНОМАРОК VIN-CODE.ORG предлагает СВЕЧИ ЗАЖИГАНИЯ, ВЫСОКОВОЛЬТНЫЕ ПРОВОДА компании NGK
NGK Spark Plug Co., Ltd.- ведущий в мире производитель свечей зажигания, свечей накаливания, лямбда зондов (под торговым знаком NTK) и прочих компонентов для двигателей внутреннего сгорания. Компания также производит компоненты из промышленной керамики для полупроводников, аппаратуры связи и пр. Штаб квартира компании NGK Spark Plug Co., Ltd. находится в Нагоя (Nagoya), Япония.
История создания компании:
1919 г. - основание NGK INSULATORS., LTD. (предшественник NGK SPARK PLUG CO., LTD.)
1936 г. - основание NGK SPARK PLUG CO., LTD.
1949 г. - разработка «новой керамики» под торговой маркой NTK
1975 г. - открытие первого европейского филиала в Лондоне
1979 г. - открытие первого офиса в Европе (Дюссельдорф, Германия)
1980 г. - открытие офиса и склада в г. Ратинген (Германия)
1990 г. - открытие Европейского технического центра NGK в г.Ратинген (Германия)
1996 г. - выход на российский рынок
2006 г. - открытие Представительства NGK Spark Plug Europe GmbH в Москве
Компания NGK Spark Plug Co. Ltd была основана в октябре 1936 года в Японии. Название компании NGK (NIPPON GAISHI KAISYA) переводится как японская изоляторная фабрика. После реструктуризации в 1997 году компания объединяет три группы:
- · авто компоненты свечи зажигания, свечи накаливания, комплекты проводов, лямбда зонды)
- · компоненты средств связи (компоненты электрических полупроводников)
- · техническая керамика ( керамика для резки, тонкая керамика)
Деятельность компании NGK в мире
В настоящее время компания NGK представлена на всех континентах и насчитывает 8 сбытовых подразделений, 11 заводов и 14 сбытовых представительств. Годовой оборот компании составляет порядка 2,0 млрд. Евро. Общее число сотрудников по всему миру - около 10 тысяч. Компания NGK постоянно работает над созданием новых технологий, затрачивая ежегодно около 11% своего оборота на научные исследования и разработки. Европейский технический центр NGK в Ратингене (Германия), открытый в 1990 году, общей площадью 2200 кв. м, обеспечивает европейских производителей автомобилей любой поддержкой, которая требуется для проверки двигателей и шасси, имитации холодного климата и специализированных работ по анализу выхлопных газов.
Компания NGK поставляет компоненты на сборочные конвейеры, являясь техническим партнером 52 автопроизводителей. Кроме того, на вторичном рынке осуществляет поставки для 526 клиентов. Среди клиентов компании - Audi, Alfa Romeo, Bentley, BMW, DaimlerChrylser, Ferrari, Fiat, Ford, Honda, Jaguar, Lancia, Mazda, Mitsubishi, Opel, Renault, Skoda, Toyota, Volkswagen и Volvo и др. По данным компании NGK более 87% всех мировых производителей легковых автомобилей выбирают свечи зажигания NGK для первой комплектации. Что касается европейских производителей, то на более 50% всех сходящих с конвейеров производителей BMW Group, Fiat Group и VW Group машинах стоят свечи зажигания NGK.
Деятельность компании в Европе
Компания NGK Spark Plug Europe GmbH в 2009 году отметила 30 лет успешной работы на европейском рынке. За прошедшие три десятилетия компания прошла в Европе путь от новичка рынка до одного из крупнейших поставщиков свечей зажигания, свечей накаливания и кислородных датчиков на европейском континенте.
В 1979 году был основан NGK Spark Plug Deutschland – „предшественник“ сегодняшней компании. На тот момент компания насчитывала 10 сотрудников. Постоянные успехи в первичной комплектации в последующие годы делали марку все более востребованной среди автопроизводителей – и особенно на вторичном рынке.
В 1989 году NGK Spark Plug Deutschland превратилась в знакомую теперь уже многим компанию NGK Spark Plug Europe GmbH. За эти десять лет портфолио компании пополнили свечи накаливания и кислородные датчики. Все большее число автопроизводителей использовали продукцию NGK, наметился очередной подъем. Компания NGK переехала на ул. Harkortstraße в г.Ратинген, где организовала Технический Центр и два склада – один для поставок на конвейеры автопроизводителей, а второй для вторичного рынка. В 2009 в Европе компания насчитывала уже 340 сотрудиков.
На сегодняший день торговая марка NGK известна в 38 европейских странах. Компания является ведущим поставщиком на первичную комплектацию свечей зажигания и кислородных датчиков и, кроме того, все более успешно продвигает свечи накаливания среди автопроизводителей. На вторичном рынке среди покупателей неизменно возрастает популярность двух ассортиментов компании: V-Line, введен в 1991г., и D-Power, введен в 2005 г. Эти две линейки продукции доказывают: ключ к успеху кроется в сочетании передовых технологий и ассортимента, отвечающего требованиям рынка.
Деятельность компании в России
В России компания NGK начала бизнес в 1996 году, предлагая поставки авто компонентов для вторичного рынка. В 2006 году открыто Представительство NGK Spark Plug Europe GmbH в Москве. В настоящее время компания NGK поставляет на российский рынок широкую гамму продуктов: свечи зажигания, свечи накаливания, кислородные датчики и провода зажигания. В России компания NGK занимает лидирующие позиции на вторичном рынке свечей зажигания.
Награды компании NGK (выборочно):
"За Выдающееся Качество" (Audi)
"За Отличную Оценку Партнера" (VW)
"Золотая Автомобильная Премия за Качество" (Fiat)
"Лучший Поставщик во всех Категориях" (Honda UK)
"Поставщик Года" (GM)
"За Последовательный Успех в Отличном Качестве Продукции" (Mazda)
“Мировая награда за качество” (Nissan)
“Золотая награда за инновации» (EQUIP AUTO 2009)
NGK: прогресс и инновации
NGK Spark Plug Europe GmbH предлагает ассортимент свечей зажигания - более 2000 наименований - на практически любой двигатель внутреннего сгорания, от стандартных одноэлектродных свечей до эксклюзивных гоночных моделей, которые используются в болидах «Формулы 1».
«Компания NGK Spark Plug Europe GmbH достигла больших успехов с того момента, когда более 30 лет назад её бренд впервые появился в Европе. Сегодня практически все автопроизводители в мире в качестве исходного оборудования используют свечи зажигания и кислородные датчики, выпущенные компанией NGK Spark Plug Europe GmbH, в частности, это относится ко всем европейским автопроизводителям. Кроме того, в течение последних нескольких лет компания NGK стала одним из ведущих поставщиков свечей накаливания для автомобильной промышленности», - рассказывает Генеральный директор компании NGK Spark Plug Europe GmbH Хисаши Наканиши.
В ассортименте также присутствует большое количество многоэлектродных свечей зажигания с 2, 3, 4 боковыми электродами, которые служат дольше стандартных моделей. Применение на таких свечах технологии «скользящего искрообразования» или «полуповерхностного разряда» позволяют также значительно увеличить надежность работы при холодном пуске и противостоять образованию нагара.
У компании есть отдельная программа свечей зажигания, центральный электрод которых выполнен из сплава драгоценных металлов, таких как платина и иридий. Особенность свечей данного типа заключается в том, что центральный электрод имеет очень тонкое сечение и чип из драгоценных металлов. Технология, используемая в свечах данного типа, обеспечивает максимально эффективное воспламенение топливно-воздушной смеси, повышает надежность зажигания, препятствует искровой эрозии, значительно увеличивает срок службы.
Одна из последних разработок компании – «гибридные» свечи зажигания, которые сделаны для двигателей с непосредственным впрыском топлива, например для моторов D-4 (Toyota) и FSI (Audi). Центральный электрод этих моделей, сделанный из иридия или платины, обеспечивает наилучшие рабочие характеристики воспламенения смеси, а технология «полуповерхностного разряда» - 100% надежность зажигания даже в экстремальных условиях эксплуатации. «Гибридные свечи зажигания PFR7W-TG. установлены в двигателях V8 (420 л.с.) и V10 (525 л.с.), обеспечивая им оптимальные рабочие характеристики.
Другим примером применения «драгоценных» свечей PFR7S8EG, разработанных совместно с инженерами концерна Volkswagen/Audi. Они устанавливаются на турбированные двигатели TFSI с прямым впрыском, а также на традиционные безнаддувные двигатели, используемые в автомобилях Audi, VW, Seat и Skoda.
Широкий ассортимент NGK позволяет удовлетворить потребности даже самых «капризных» в техническом плане автомобилей. Например, у мощного Mercedes SLS AMG с мотором мощностью 571 л.с. конструктивно очень мало места для установки свечей, однако серийная модель NGK ILZKAR8A10 имеет особенно тонкую удлиненную резьбу диаметром всего 12 мм. Благодаря центральному электроду из иридия и выступающему на 5 мм изолятору эта свеча зажигания гарантирует оптимальное воспламенение даже при самых сильных перемещениях топливно-воздушной смеси. А в лучшей модели серии BMW X1 - автомобиле BMW X1 xDrive 28i с рядным шестицилиндровым двигателем мощностью 190 кВт (258 л.с.) - производитель делает ставку на свечи зажигания NGK LZFR6AP11GS, чтобы и в экономном режиме послойного смесеобразования и при полной нагрузке гарантировать одинаково надежное и эффективное зажигание.
NGK Spark Plug Europe GmbH большое внимание уделяет растущему рынку дизельных автомобилей. Совсем недавно, благодаря созданию новых высокотемпературных керамических свечей накаливания, компания стала ведущим поставщиком на заводы Mercedes-Benz. Новая технология обеспечивает оптимальный холодный пуск даже при самых низких температурах окружающей среды, так как свечи достигают рабочей температуры 1000°C менее чем за 2 сек., сохраняя высокую температуру продолжительное время.
Новые модели Mercedes, оснащённые такими свечами, показывают убедительные результаты по экономии топлива. Новые высокотемпературные свечи накаливания можно найти также под капотом E220 CDI Blue Efficiency, E250 CDI Blue Efficiency, а также E280 CDI.
Данные свечи накаливания доступны и на вторичном рынке в линейке D-Power. Они полностью идентичны тем, которые используются в оригинальной комплектации, также как и все другие свечи накаливания из этой серии. В оригинале их устанавливают на более чем 57 моделей концерна Volkswagen/Audi, таких как Audi A4 TDI, Skoda Superb и Passat TDI, на уже упомянутые автомобили Mercedes Benz, некоторые модели Citroen, Pegeuot, а также на Mitsubishi Pajero III, 3.2.
Для двигателей, работающих на газе, предназначена серия LPG LaserLine, которая позволяет покрыть потребности 95% этого сегмента авторынка. Используемая при производстве данных свечей зажигания технология устанавливает новые стандарты в сфере двигателей, работающих на газе. Их центральный электрод имеет иридиевый чип, а боковой – платиновую напайку. Эти благородные металлы крайне устойчивы к эрозии и коррозии, а также противостоят жестким рабочим условиям работы на газе значительно лучше, чем традиционные материалы. Зазор между центральным и боковым электродом свечей зажигания LPG LaserLine выставляется на заводе и составляет 0,8 мм, что в большинстве случаев исключает последующую регулировку. Медный сердечник бокового электрода улучшает отвод тепла и помогает оптимально регулировать высокие температуры, возникающие при сгорании газа. Компания NGK Spark Plug Europe GmbH, являясь ведущим мировым производителем кислородных датчиков марки NTK, поставляет лямбда-датчики на многие мировые марки автомобилей. Например, для 1,2-литрового двигателя TSI мощностью 77 кВт от Volkswagen/Audi. Здесь в качестве регулирующего датчика используется широкополосный датчик ZFAS-U2. Он в состоянии подавать в широком рабочем диапазоне сигнал, пропорциональный остаточному кислороду в выхлопном газе. Таким образом возможно поддержание оптимального соотношения воздух-топливо в рабочих состояниях от обедненной смеси до насыщенной. В датчике ZFAS-U2 впервые нагревательный и сенсорный компоненты интегрированы в единый керамический элемент, что позволяет снизить потери тепла и обеспечивает готовность датчика к работе уже через 5 секунд после запуска двигателя. В качестве диагностического датчика NGK Spark Plug Europe GmbH предлагает OZAS-S2, отличающийся высокой точностью измерений.
Наконец, компания NGK предлагает на вторичном рынке широкий ассортимент комплектов высоковольтных проводов зажигания. Все они соответствуют спецификациям оригинальной комплектации автопроизводителей и изготавливаются в соответствии с ISO 3808 и ISO 6856. Кроме того, провода зажигания имеют крайне износостойкую внешнюю оболочку из силикона и могут применяться даже при постоянной температуре в подкапотном пространстве до 220°С (класс температуростойкости F). Строение штекера, длина проводов и помехоподавление оптимально подходят для различных автомобилей, так что гарантирован как беспроблемный монтаж, так и их надежная работа.
xn----ctbholqj.xn--p1ai
Свечи зажигания Bosch: вековое немецкое качество
Компания Bosch является признанным мировым лидером в производстве свечей зажигания, и вне зависимости от локации завода качество продукции всегда остается на высоте.
Первая в мире свеча зажигания, разработанная компанией Bosch и работавшая от магнето высокого напряжения, была создана более века назад, в 1902 году. Это стало настоящей революцией в области автомобилестроения, а технологии массового производства свечей сделали возможным стремительный рост объемов выпуска транспортных средств. С того момента компания Bosch выпустила свыше 10 миллиардов свечей и разработала более 20 тысяч модификаций, постоянно их совершенствуя.
Сегодня к свечам зажигания предъявляют особые требования. Основа для их выполнения – применение более устойчивых к коррозии и искровой эрозии материалов (интервал замены, превышающий 100 тысяч км), уменьшение диаметра свечи, увеличение длины резьбы, ужесточение требований к электрическим характеристикам свечи (керамике, изолятору), направленный боковой электрод и т.п. Свечи зажигания все больше и больше разрабатываются под конкретный двигатель.
В ассортименте Bosch есть свечи зажигания для любого двигателя с учетом требований автопроизводителей и новейших разработок компании – с центральным электродом, легированным иттрием, с электродами, покрытыми платиной, со сплавом платины с иридием, с серебряным покрытием. Количество боковых электродов в свечах зажигания Bosch варьируется от 1 до 4, а диаметр центрального электрода достигает 0.6 мм.
Свечи зажигания Bosch, широко востребованы как в автомобильном сегменте, так и в специальных сферах применения (мотоциклы, снегоходы, катера, газонокосилки, бензопилы, стационарные двигатели и т.д.), и выпускаются на заводах Bosch в Германии, России, Бразилии, Китае и Индии. Размещение производства свечей в разных странах - логичный этап развития компании и бренда. Для того чтобы это произошло, необходимо выполнение некоторых условий: объемы продаж и популярность марки должны достигнуть определенного уровня. При этом нет разницы, где производится свеча: будь то, к примеру, Германия (город Бамберг) или Россия (город Энгельс), качество свечи остается неизменным. Это позволяет компании обеспечивать непрерывный процесс поставки и наличие актуального ассортимента на складах, тем самым удовлетворяя повышенный спрос на свечи зажигания Bosch во всем мире.
Завод Bosch в городе Бамберге - первый и основной завод компании по выпуску свечей зажигания - был открыт в 1939 году. Производственные мощности завода занимают площадь в 100 000 кв.м. и позволяют выпускать до 500 000 свечей зажигания в день, насчитывая при этом 1250 различных видов.
Завод в России в городе Энгельсе производит свечи зажигания уже более половины столетия. В течение 2009 - 2013 годов компанией Bosch запланировано инвестировать в развитие завода более 16 млн. евро. Ежедневно на заводе выпускается более 180 тысяч свечей 385 различных типов. География поставок свечей зажигания Bosch, производимых в России на заводе в г. Энгельсе, очень широка – это страны СНГ, США, Европы (Великобритания, Германия, Португалия, Испания и т.д.), Латинской Америки, Южной Африки, Индонезии, Тайвань, Австралия и многие другие. С 01.07.2011 российский завод Bosch получил разрешение на поставку свечей зажигания для GM-Opel Europe и Ford Europe. И завод не собирается останавливаться на достигнутых результатах!
Задача Bosch как ведущего производителя - следовать заданному высокому стандарту качества, вне зависимости от того, на каком заводе производится его продукция.
Все заводы Bosch по производству свечей зажигания функционируют одинаково, ход технических процессов идентичен и в Бамберге, и в Энгельсе. К примеру, на заводе в России используется современное высокотехнологичное оборудование тех же поставщиков, что на заводе в Германии: прессы для штамповки выдавливанием Hatebur, токарные автоматы Schütte, сварочные автоматы Bihler и др.
Немаловажным фактором в обеспечении одинакового уровня качества продукции является централизованное заключение договоров на поставку сырья и материалов. Все комплектующие для производства конкретной свечи зажигания совпадают на каждом из заводов, исключений из этого правила почти не бывает. Так, например, сырье для производства свечей на заводе в г. Энгельсе, такое как гранулят, герметик, глазурь и др., поставляют из Бамберга, Германия. Инструменты, калибры и важные системы подачи также не являются исключением. Центральный электрод производится на заводе в Бамберге, Германия, и поставляется в Россию. Немаловажно, что контроль качества выпускаемого продукта также осуществляется по единой системе стандартов, например, статистические графики контроля процесса, графики качества, автоматическое измерение данных процесса и размерных элементов абсолютно одинаковы.
Кроме того, большое количество специалистов из Германии, работающие на заводах Bosch в разных странах, осуществляют постоянную проверку качества и контролируют технологический процесс производства. Например, на данный момент на российском заводе Bosch трудится 9 немецких коллег, и это не считая тех, которые регулярно приезжают для проведения тренингов и семинаров. Так, например, за 2011 год более 900 чел./дней было затрачено на обучение сотрудников, половину из которых российские сотрудники провели на заводе в Германии, а половину – работники немецкого завода на производстве в России.
Поэтому на сегодняшний день национальные акценты уже не актуальны, и самым значимым является тот уровень качества, который компания гарантирует для своих товаров. Бренд Bosch – это бесспорно высокое качество продукции, в т.ч. свечей зажигания.
Подтверждением этого являются многочисленные успехи компании и признание Bosch ведущим производителем свечей зажигания в различных областях. Так, например, по результатам опроса читателей немецкого авторитетного журнала «Auto, motor und Sport» на протяжении 20072012 годов Bosch был признан лучшим брендом в категории «Свечи зажигания».
Крупнейшие мировые производители используют свечи зажигания Bosch для серийной комплектации автомобилей. Так, например, автомобили Ford Focus III («Duratec» Ti-VCT 1.6л), новый Volkswagen Passat (TSI 1.8; TSI 2.0), Volkswagen UP (44 кВт/60л.с. и 55кВт/75.с.) сходят с конвейера, укомплектованные свечами зажигания Bosch.
Компания Bosch производит свечи не только для массового авторынка, но и для гоночных автомобилей. Свечи Bosch не раз приносили победу в таких соревнованиях, как 24-часовая серия Le Mans, лига Indy Racing, серия V8 Supercar, Шведский чемпионат кузовных автомобилей и Deutsche Tourenwagen Masters (DTM). Кроме того, инновационные разработки для автоспорта Bosch использует в серийном производстве свечей.
Всё это в очередной раз свидетельствует о высоком качестве, надежности и широком ассортименте свечей зажигания Bosch для любого автомобиля.
Установив свечи зажигания Bosch, автовладелец сможет без проблем эксплуатировать свой автомобиль в самых разных условиях.
Информация с сайта www.bosch.ru
bishka.ru
В Самарской области открыли производство свечей зажигания
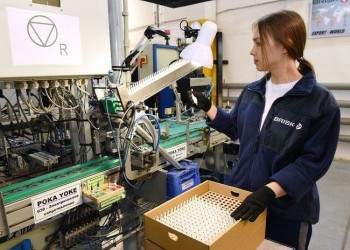
В Тольятти состоялось открытие производства свечей зажигания чешской фирмы «Brisk». Сегодня продукция компании экспортируется в 70 стран мира. Объемы продаж свечей зажигания этой марки в России составляют 25 млн штук в год, что составляет 20% отечественного рынка.
Основным партнером ООО «Бриск Рус» станет АВТОВАЗ. Российское и чешское предприятия связывают давние и прочные отношения.
Реализация данного проекта с объемом инвестиций в 5 млн евро, и созданием в Тольятти 50 новых рабочих мест, стала возможным благодаря поддержке АВТОВАЗа.
«Brisk» является поставщиком свечей для моторов, выпускаемых на тольяттинском автозаводе. Кроме того, эти свечи рекомендованы АВТОВАЗом к применению на всех современных моторах LADA. С локализацией производства уровень интеграции только повысится. Объем выпуска составит 4,5-5 млн. свечей зажигания в год. Новое производство способно полностью обеспечить АВТОВАЗ по этому направлению.
Выбор площадки в Тольятти — это вопрос экономической целесообразности, важнейший фактор, повышающий конкурентоспособность поставщика. Для АВТОВАЗа критически важно соответствие партнера ключевым характеристикам: жесткие сроки поставки, требуемое качество и оптимальная цена. И организация современного производства автокомпонентов по соседству с автосборочной площадкой значительно упрощает для поставщика эти задачи.
АВТОВАЗ, находясь в Альянсе Renault-Nissan дает серьезные возможности для роста местных и локализованных международных поставщиков. Если партнер соответствует стандартам LADA, то он соответствует и международным стандартам Альянса, что потенциально дает ему возможность выхода на глобальный рынок.
АВТОВАЗ работает не только над стимулированием процесса локализации зарубежных поставщиков, но с местными партнерами, для того, чтобы предложить покупателю автомобиль, соответствующий мировым стандартам качества, безопасности, экологичности и экономичности по приемлемой цене.
rus.vrw.ru
История компании NGK, производящей свечи зажигания и накаливания
NGK Spark Plug Co., Ltd.- ведущий в мире производитель свечей зажигания, свечей накаливания, лямбда зондов (под торговым знаком NTK) и прочих компонентов для двигателей внутреннего сгорания. Особо нужно отметить свечи зажигания NGK, их качество и надежность в работе. Компания также производит компоненты из промышленной керамики для полупроводников, аппаратуры связи и пр. Штаб квартира компании NGK Spark Plug Co., Ltd. находится в Нагоя (Nagoya), Япония.
История создания компании:1919 г. - основание NGK INSULATORS., LTD. (предшественник NGK SPARK PLUG CO., LTD.) 1936 г. - основание NGK SPARK PLUG CO., LTD. 1949 г. - разработка "новой керамики" под торговой маркой NTK 1975 г. - открытие первого европейского филиала в Лондоне 1979 г. - открытие первого офиса в Европе ( Дюссельдорф, Германия) 1980 г. - открытие офиса и склада в г. Ратинген (Германия) 1990 г. - открытие Европейского технического центра NGK в г.Ратинген (Германия) 1996 г. - выход на российский рынок 2006 г. - открытие Представительства NGK Spark Plug Europe GmbH в Москве
Компания NGK Spark Plug Co. Ltd была основана в октябре 1936 года в Японии. Название компании NGK (NIPPON GAISHI KAISYA) переводится как японская изоляторная фабрика. После реструктуризации в 1997 году компания объединяет три группы:" авто компоненты свечи зажигания, свечи накаливания, комплекты проводов, лямбда зонды) " компоненты средств связи (компоненты электрических полупроводников) " техническая керамика ( керамика для резки, тонкая керамика)
Деятельность компании NGK в миреВ настоящее время компания NGK представлена на всех континентах и насчитывает 8 сбытовых подразделений, 11 заводов и 14 сбытовых представительств. Годовой оборот компании составляет порядка 2,0 млрд. Евро. Общее число сотрудников по всему миру - около 10 тысяч. Компания NGK постоянно работает над созданием новых технологий, затрачивая ежегодно около 11% своего оборота на научные исследования и разработки. Европейский технический центр NGK в Ратингене (Германия), открытый в 1990 году, общей площадью 2200 кв. м, обеспечивает европейских производителей автомобилей любой поддержкой, которая требуется для проверки двигателей и шасси, имитации холодного климата и специализированных работ по анализу выхлопных газов.
Компания NGK поставляет компоненты на сборочные конвейеры, являясь техническим партнером 52 автопроизводителей. Кроме того, на вторичном рынке осуществляет поставки для 526 клиентов. Среди клиентов компании - Audi, Alfa Romeo, Bentley, BMW, DaimlerChrylser, Ferrari, Fiat, Ford, Honda, Jaguar, Lancia, Mazda, Mitsubishi, Opel, Renault, Skoda, Toyota, Volkswagen и Volvo и др. По данным компании NGK более 87% всех мировых производителей легковых автомобилей выбирают свечи зажигания NGK для первой комплектации. Что касается европейских производителей, то на более 50% всех сходящих с конвейеров производителей BMW Group, Fiat Group и VW Group машинах стоят свечи зажигания NGK.
Деятельность компании в ЕвропеКомпания NGK Spark Plug Europe GmbH в 2009 году отметила 30 лет успешной работы на европейском рынке. За прошедшие три десятилетия компания прошла в Европе путь от новичка рынка до одного из крупнейших поставщиков свечей зажигания, свечей накаливания и кислородных датчиков на европейском континенте.
В 1979 году был основан NGK Spark Plug Deutschland - "предшественник" сегодняшней компании. На тот момент компания насчитывала 10 сотрудников. Постоянные успехи в первичной комплектации в последующие годы делали марку все более востребованной среди автопроизводителей - и особенно на вторичном рынке.
В 1989 году NGK Spark Plug Deutschland превратилась в знакомую теперь уже многим компанию NGK Spark Plug Europe GmbH. За эти десять лет портфолио компании пополнили свечи накаливания и кислородные датчики. Все большее число автопроизводителей использовали продукцию NGK, наметился очередной подъем. Компания NGK переехала на ул. Harkortstra?e в г.Ратинген, где организовала Технический Центр и два склада - один для поставок на конвейеры автопроизводителей, а второй для вторичного рынка. В 2009 в Европе компания насчитывала уже 340 сотрудиков.
На сегодняший день торговая марка NGK известна в 38 европейских странах. Компания является ведущим поставщиком на первичную комплектацию свечей зажигания и кислородных датчиков и, кроме того, все более успешно продвигает свечи накаливания среди автопроизводителей. На вторичном рынке среди покупателей неизменно возрастает популярность двух ассортиментов компании: V-Line, введен в 1991г., и D-Power, введен в 2005 г. Эти две линейки продукции доказывают: ключ к успеху кроется в сочетании передовых технологий и ассортимента, отвечающего требованиям рынка.
Деятельность компании в РоссииВ России компания NGK начала бизнес в 1996 году, предлагая поставки авто компонентов для вторичного рынка. В 2006 году открыто Представительство NGK Spark Plug Europe GmbH в Москве. В настоящее время компания NGK поставляет на российский рынок широкую гамму продуктов: свечи зажигания, свечи накаливания, кислородные датчики и провода зажигания. В России компания NGK занимает лидирующие позиции на вторичном рынке свечей зажигания.
Награды компании NGK (выборочно):"За Выдающееся Качество" (Audi) "За Отличную Оценку Партнера" (VW) "Золотая Автомобильная Премия за Качество" (Fiat) "Лучший Поставщик во всех Категориях" (Honda UK) "Поставщик Года" (GM) "За Последовательный Успех в Отличном Качестве Продукции" (Mazda) "Мировая награда за качество" (Nissan)"Золотая награда за инновации" (EQUIP AUTO 2009)
mdmotors.ru