Где производят лада гранта
Где собирают Лада Гранта: особенности производства
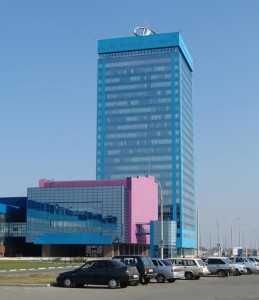
АвтоВАЗ в городе Тольятти
Если вы задались вопросом о том, где собирают Лада Гранта, ответ можно найти на официальном сайте компании:
- в стенах АвтоВАЗа, что находится в городе Тольятти;
- в ИжАвто — городе Ижевск, оба предприятия расположены на территории России.
Первоначально проекту присвоили рабочее название Low Cost, тогда как внутри завода автомобиль имел обозначение ВАЗ-2190. Первое название переводится с английского как низкая цена. Название для машины выбиралось из множества тысяч вариантов, присланных в рамках конкурса, который объявил производитель. Компания преследовала такую цель, что у народного автомобиля должно быть народное название. Победителем конкурса оказался житель Красноярска, который получил награду — машину Lada Kalina.
В процессе мероприятия ММАС-2010 президент АвтоВАЗ рассказал, что предполагаемая стоимость новинки будет равна 220 000 руб. на момент старта производства.
Повышение стоимости классических представителей Lada 2105 и 2107 было обусловлено тем, что Granta имеет статус более комфортного и безопасного авто. В то же время была озвучена информация о том, что Granta выйдет на российский рынок к концу 2011 г.
Позже было объявлено о том, что стоимость авто в базовой комплектации будет равна 229 000 руб. Повышение связано с ценой на подушку безопасности, которая, вопреки планам, присутствует на всех авто, в том числе и на базовой комплектации. Начальную цену скорректировало наличие фиксатора детских сидений ISOFIX и соответствие токсичности выхлопа правилам стандарта Eвро-4.
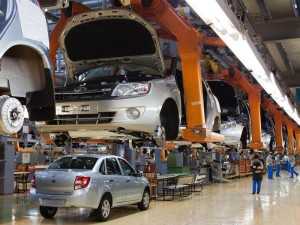
После сборки первого самого дешевого авто модельного ряда цена модификаций только увеличивалась
Производитель провел презентацию авто как раз в городе Тольятти. После 16 мая этого же года на конвейере АвтоВАЗ стартовала сборка новинки в тестовом режиме. Тогда как серийный выпуск производитель решил начать в октябре. За этот период на Волжском заводе была отработана методика выпуска. Старт реализации был намечен на 1 декабря. За 2 месяца, пока шел прием заявок, более 20 000 жителей России изъявили желание купить данный автомобиль.
После этого наиболее дешевая комплектация Granta несколько раз дорожала. С 1 апреля 2012 года машина подорожала на 10 000 руб. А со 2 июля этого же года произошло повторное повышение: самая бюджетная комплектация стала обладать ценой, равной 259 000 руб. В 2013 году стоимость наиболее дешевой комплектации стала равна 279 000 руб.
На конец прошлого года низшая цена автомобиля в стандартной комплектации составляла 293 600 руб. Не всегда выпуск авто шел гладко, например, производитель АвтоВАЗ был вынужден отозвать несколько десятков тысяч реализованных авто модели Гранта, что было обусловлено обнаруженными неисправностями тормозной системы.
Особенности производства
Собирают автомобиль по особой технологии. Весь процесс, начиная со сварки и заканчивая сборкой, производится с помощью высокотехнологичного оборудования, поставляется которое зарубежными и российскими предприятиями.
Процесс сварки Granta
Машины Лада Гранта лифтбек имеют кузова, которые свариваются на роботизированных комплексах. Производитель совместно с немецкой фирмой Kuka разработал и изготовил роботов, которые работают на сварочных линиях. Корректируется функционирование линий сварки согласно математическим моделям, создаваемым в процессе проектирования описываемого авто. Применение этих технологий позволяет компании получать отличные показатели по геометрии кузова и соединению деталей.
Особенности окрашивания Лада Гранта
Процесс окрашивания кузова гарантируют надежную защиту от коррозии
Методика, которая используется для окрашивания Лады, применяется в стенах популярных автомобильных заводов европейского происхождения. На этом этапе компания применяет оборудование немецкого производителя Eisenmann. Основная особенность проведения работ по окрашиванию выражается в применении методики, которая способна гарантировать высокое качество антикоррозийной обработки и нанесения покрытия.
Перед тем как подвергать кузов нанесению краски, его поверхность проходит заблаговременную подготовку. При этом его транспортировка осуществляется на программируемом «челноке». Кузов машины вращается силой робота в нескольких плоскостях. Это позволяет обеспечить попадание грунтов и обрабатывающих смесей во все полости кузова.
Как только кузов прошел все технологические емкости с растворами грунтов и обрабатывающих растворов, челнок приводит его в такое положение, чтобы оказались удалены излишки смесей. Это предотвращает попадание составов в следующую ванну. Процесс окрашивания кузова и последующее нанесение лака осуществляют 32 робота марки Eisenmann. Из них 6 предназначены для линии грунта, а остальные работают на двух лаковых линиях.
При окрашивании поддерживаются определенные условия, что касается, например, постоянного температурного режима в 20°С, движение транспорта ограничено, рабочие трудятся только в одноразовых комбинезонах. Маляры перед посещением окрасочной камеры проходят шлюз, в котором со специалиста воздухом удаляются маленькие частицы пыли, которые могли бы оказать губительное влияние на качество окраски.
После того как автомобиль оказывается собран, его поверхность имеет высокое качество окрашивания, что обусловлено еще и тем, что в процессе этого применяются современные материалы. Например, трехкатионные фосфатирующие смеси повышают коррозионную устойчивость кузова за счет плотной микрокристаллической структуры пленки.
Особенности сборки
Двери собираются на отдельном конвейере
Когда собирают автомобиль модели Granta, на начальном этапе манипуляторы демонтируют двери. Их сборка осуществляется на другом конвейере. Анализ качества двери завершается ее монтажом на тот же автомобиль, с которого они были демонтированы. Отдельно монтируется и приборная панель.
Заполнение соответствующих емкостей машины эксплуатационными составами производится контрольно-наполнительным оборудованием. Оно должно еще и протестировать системы охлаждения мотора посредством вакуума, проверяются и тормозная и топливная системы. На этом же этапе происходит анализ работоспособности системы улавливания паров бензина. Заправка жидкостями производится только тогда, когда анализ на герметичность был завершен и прошел успешно.
Когда собирают автомобиль, процесс может быть и остановлен, это происходит, если возникают какого-то рода отклонения. Труд специалистов линии сборки облегчен, это обусловлено еще и тем, что собирают двери на отдельной линии. Специалисты трудятся, стоя на платформе, устремленной вперед, а не следуют за перемещающимся кузовом.
Когда осуществляется работа в особо важных участках линии, после завершения операции работники оставляют именной штамп в контрольной карте. Это позволяет анализировать ситуацию о том, кто ответственен за ту или иную операцию в процессе сборки. В конце каждой из 8 сборочных линий и на компьютерных роликовых стендах машины должны пройти проверку.
Их результаты собираются по каждому авто. После этого они поступают в информационную сеть производителя. Помимо того, что автомобиль проходит тщательную проверку в рамках конвейера, каждая машина модели Granta после завершения сборки и предпоследней стендовой проверки проходит тестирование на испытательном треке.
Таким образом выпускают автомобили в стенах заводов компании АвтоВАЗ, что позволяет получить качественные машины.
1ladagranta.ru
Ответы на вопросы по Лада Гранта Лифтбек
Новинка отечественного производителя вызывает неподдельный интерес у многих слоев населения, особенно, у потенциальных покупателей. Наш сайт старается предоставить вам самую новую и свежую информацию. Не забывайте посещать новостной раздел, где собрана вся самая свежая информация о Лада Гранта Лифтбек.
Почему лифтбек LADA Granta дороже седана LADA Granta?
В настоящее время цена LADA Granta в кузове седан начинается от 289 тысяч рублей (комплектация «стандарт»). Вместе с тем заявленная АВТОВАЗом цена LADA Granta лифтбек в самой дешевой комплектации стартует с отметки в 214 тысяч рублей. Начальник управления по маркетингу АВТОВАЗа Александр Бредихин рассказал, что изначально LADA Granta лифтбек ориентирован на более требовательных покупателей. Из-за этого уже в базовой версии лифтбек оснащается лучше, чем седан. Так на всех LADA Granta в кузове лифтбек бамперы окрашены в цвет кузова, а диаметр колесных дисков составляет 14 дюймов. У седанов Лада Гранта в комплектации «стандарт» бампер неокрашенный. Причем покрасить его нельзя даже за доплату. Помимо этого седан комплектуется 13-дюймовыми колесными дисками.
В числе прочего лифтбек в самой дешевой комплектации оснащается 8-клапанным мотором с облегченной шатунно-поршневой группой и модернизированной механической КПП с тросовым приводом. Седан LADA Granta в аналогичной версии оснащается старой КПП с тягами и бензиновым 84-сильным двигателем в «тяжелой» ШПГ. Вместе с тем, известно, что АВТОВАЗ эту версию седана в скором времени планирует снять с производства.
Получит ли лифтбек LADA Granta спортивную версию?
Седан LADA Granta Sport весьма успешно стартовал на российском рынке. Ежемесячно продается около 200 таких автомобилей. Объемы продаж при этом ограничены возможностями производства. Поэтому, по словам Александра Бредихина, на АВТОВАЗе активно обсуждают возможность выпуска спортивной версии лифтбека LADA Granta. Если эта идея получит одобрение, то купить лифтбек с приставкой Sport можно будет не ранее 2016 года. Такой версии в планах на текущий и следующий год нет.
Опускаются ли до конца в LADA Granta лифтбек задние боковые стекла. Пропало ли дребезжание при неполном закрывании задних стекол?
На лифтбеке LADA Granta задние стекла до конца не опускаются. При этом остается чуть меньше половины. Дребезжания при хлопании дверьми с опущенными стеклами не наблюдается. Сами по себе задние двери в LADA Granta лифтбек стали закрываться легче. Этого вазовцам удалось достичь за счет использования модернизированных уплотнителей и дверных ручек.
Насколько легко в лифтбеке Лада Гранта открывается и закрывается багажник?
Пятую дверь в лифтбеке LADA Granta можно открыть только с ключа. Также это можно сделать с помощью кнопки в салоне (это опция). Подниматься вверх открытая дверь сама не торопится. Сначала приходится ее немного подталкивать. Закрывается дверь вполне легко. Отдельное неудобство могут создать скользкие внутренние ручки, за которые просто так ухватиться сложно. С текстильной петлей, которую журналисты прикрепили в качестве эксперимента к ручкам нескольких машин, процесс закрывания двери стал удобнее. Как отметили представители АВТОВАЗа, это решение может быть внедрено, если будет положительная реакция покупателей.
Будет ли в LADA Granta лифтбек регулироваться по высоте водительское сидение и по вылету руль?
Подобные решения АВТОВАЗ первыми применит на седане LADA Vesta, который начнут выпускать в 2015 году. Лада Гранта подобные регулировки сможет получить не ранее начала 2016 года. Именно на это время АВТОВАЗ запланировал провести рестайлинг семейства Лада Гранта.
Получит ли лифтбек LADA Granta парктроник и пакет дополнительной шумоизоляции?
Как рассказали представители АВТОВАЗа, усиленная шумоизоляция и задние датчики парковки будут устанавливаться на версии лифтбека «люкс». Также парктроник и пакет дополнительной шумоизоляции ставится и на люксовые версии седана Лада Гранта.
Когда лифтбек LADA Granta начнут поставлять в страны СНГ?
Александр Бредихин рассказал, что в СНГ вазовские новинки появляются примерно через три месяца, после старта российских продаж. Это связано с процедурами по адаптации машин под местные рынки. В случае с лифтбеком LADA Granta этот срок планируется сократить.
new-granta.ru
Как собирают Гранту-лифтбек | Русский Автомобиль
На Иж-Авто вопросами безопасности занимаются немножечко параноики. И я им честно об этом сказал. Охранники меня не менее честно предупредили: если направишь объектив в сторону Ниссана, то паранойя, не паранойя – никто разбираться не будет, просто отберут флешку.
Это какое-то дежа-вю, прости господи. Ровно десять лет тому назад на Иж-Авто, который тогда находился под протекторатом ГК СОК, меня вообще арестовали и посадили во внутризаводскую кутузку (настоящую, с решётками и нарами), откуда вызволял лично главный инженер завода. А всё потому, что сфотографировал «не ту» машину.
Жёсткие времена СОКа прошли, но наследие оказалось сильным. Бывший до недавнего времени директором Иж-Авто Алексей Алексеев тоже на дух не переносил журналистов, а когда один таки приехал и в его репортаж нечаянно попала часть крыши (sic!) Nissan Sentra, то разразился жуткий скандал с увольнением «кого следует».
Сейчас на Иж-Авто директор новый – ВАЗовец Михаил Рябов, он тут с февраля. И он тоже не хочет портить отношений с японцами, которые избыточно щепетильно относятся к секретности в своей работе в Ижевске. Нервничают даже, когда Nissan в этом контексте просто упоминают, а уж если называют модель – просто обижаются. Поэтому ко мне приставили человека из службы безопасности, который сурово следил за ориентацией фотокамеры. Следил, скажу я вам, да не уследил… Ну да ижевцам я тоже не враг и не буду пока публиковать снимки «секретного» Ниссана. Сейчас не о нём речь, а о заводе: что тут происходит, как и зачем. Тем более, что только что в Ижевске стартовало производство Гранты-хэтчбека, которая заменит на конвейере Иж-Авто Гранту-седан. Самое время прогуляться по заводу и посмотреть, как делают Гранту.
Логично было бы начать с цеха штамповки, ведь все оригинальные для хэтчбека детали локализовали в Ижевске. Но – увы – штамповка оказалась недоступной. Причём не по соображениям информационной безопасности, а по более прозаической причине: «там грязно и мы не хотим, чтобы там снимали». Поэтому начнём с цеха сварки. Благо, тут тоже хватает нового оборудования и оригинальных операций по хэтчбеку.
Сварочный цех
В сварочном цехе до начала производства хэтча работало 350 человек. Сейчас кадровый состав расширяют до 668 человек. Имеется в виду только сварка Гранты, кузова Ниссанов будут «вариться» в другом корпусе, там как раз сейчас монтируется новое оборудование.
База автомобиля – его пол. На лифтбеке (будем называть Гранту-хэтч именно так, это её официальное обозначение) он состоит из трёх частей, передней, средней и задней. Собственно, процесс сварки кузова начинается с состыковки этих элементов.
На этом участке можно «варить» полы как седана, так и хэтча, достаточно заменить один стенд, где приваривается «панель задка» (по заводской терминологии).
Сварка происходит вручную, обычными клещами.
Получается, в итоге, вот такая деталь.
Потом её стыкуют с передней частью:
Получается вот что.
Это и есть основание пола будущего автомобиля. К нему последовательно пристыковывают пять деталей – арки задних колёс, усилители порогов и моторный отсек, подсобранный ранее.
Теперь нужно сделать надстройку. Для этого весь упомянутый комплект поступает в автоматическую линию сварки основания кузова.
Чуть правее от этого процесса находится участок сварки боковины, правой, конечно же. А левую делают слева.
Конфигурация цеха получается предельно рациональной: пока варится основание, параллельно изготавливают боковины. А потом они просто подносятся каждая со своей стороны.
Теперь основные делали кузова состыкованы:
И в дело вступают роботы.
Поставщик робототехники – Волжский машиностроительный завод, который раньше входил в структуру ВАЗа, но при Комарове обрёл самостоятельность. Но всё равно основным заказчиком ВМЗ остаются ВАЗовские подразделения. Ещё на Иж-Авто есть промышленные роботы фирмы Kuka, правда, немного.
Теперь кузов с напольного конвейера переезжает на подвесной. И проходит стадию доварки вручную. Это потому, что роботы не могут добраться до всех нужных мест. Плюс экономия на роботах; плюс некоторые операции человек делает быстрее. Используются и контактная, и дуговая сварки.
Дальше к передней части болтами крепятся некоторые детали.
Потом начинается линия комплектования кузова.
Привариваются двери и крышка капота….
Тут надо сделать небольшую паузу и пройти на участок сборки дверей.
Здесь подсобирают дверные половинки, наклеивают каучуковые демпферы.
Есть жалобы потребителей на то, что под демпфирующими накладками развивается коррозия. В принципе, если в цехе сухо, а материал хорошо прикатать, то коррозии там сто лет не будет. Но фольгированный каучук кладут просто так, без разогрева и прикатки – так положено. Сейчас ВАЗовцы собираются перейти на более прогрессивный метод демпфирования, с введением в материал намагниченной металлической стружки, которая будет удерживать его на поверхности и при горячей сушке не даст «сползти». Такие нашлёки можно накладывать уже после катафорезного грунтования.
Потом скрепляют каркас и лицевую панель:
И отправляют дверь на завальцовку. Этим станком фирмы Kuka на заводе гордятся. Выглядит всё эффектно: автомат сам забирает дверь из ложемента, переносит на рабочий стол – и два манипулятора с роликами начинают «объезжать» дверь по периметру, уплотняя завальцовку. Давление в точке контакта – 130 кг!
Теперь возвращаемся на участок комплектования кузова. Петли, с одной стороны прикрученные к дверям, с другой стороны привариваются к нужному месту дверного проёма.
Я спрашивал, не проще ли сначала петлю приварить, а потом дверь к ней прикрутить? Нет, говорят, не проще, замучаешься «выставлять» дверь в проёме, с оптимальными зазорами.
Дверь на специальных приспособлениях…
…подводят к кузову…
…и прикручивают. Сначала задние боковые, потом передние. Теперь можно заняться их точной подгонкой…
…с использованием нехитрого инструментария…
…и ещё кое-что доработать молотком.
Можно ехать дальше.
Дальше – это на установку пятой двери, единственной оцинкованной детали кузова лифтбека.
Никаких тебе манипуляторов, всё вручную.
Кстати, к задней двери в скором времени добавятся и задние оцинкованные крылья. А вот в Гранта-седане ни одной оцинкованной детали нет.
Можно ставить последнюю деталь – крышку капота.
Порадовало, что заводчане не упрощают название этой детали и говорят именно «крышка капота». Ибо капот – это совсем другое.
Теперь кузов нужно протереть сухой ситцевой тряпочкой
– и отправить на рихтовку.
Потом его ещё раз протирают и пылесосят – нельзя, чтобы продукты абразивной рихтовки попали под лакокрасочный слой.
Кузов готов. Отправляемся вслед за ним в окрасочный цех.
Окрасочный цех
Это – масштаб. Идёшь и думаешь: он когда-нибудь кончится, а? И бросается в глаза безлюдность: многие операции выполняются автоматически и даже человеческого контроля не требуют. Плюс большинство работников скрыто в камерах, их можно разглядеть только сквозь мутноватые стёкла.
Как бы мы сейчас не относились к СОКу и лично Юрию Качмазову, но всё это великолепие выстроено ими, на их деньги. Они даже не успели толком попользоваться: три года сборки трёх моделей KIA для такого оборудования – только обкатка.
Самое начало – приход «чёрного» кузова из цеха сварки и его стыковка с окуночным (смешное слово, да?) транспортёром (на профессиональном сленге – скитом).
На скиту кузов пройдёт все операции подготовки поверхности к собственно покраске.
Итак, кузов отправляется в обработку, которая состоит из промывки и обезжиривания специальными ПАВами (поверхностно-активными веществами), поставляемыми немецкой фирмой Chemetall.
Вот за этими непрозрачными стенами агрегата подготовки начинается таинство обработки кузова.
Потом следует ещё одна промывка водой, она удаляет остатки ПАВов. И промывка активирующими составами, воздействующими на поверхность металла, как бы «разрыхляя» его на молекулярном уровне. Это позволяет более активно взаимодействовать с реагентами следующей стадии обработки – промывке в фосфатной ванне (соединения на основе ортофосфорной кислоты). Заканчивается это всё трёхстадийной промывкой специально подготовленной (деминерализованной) водой. Эта вода циркулирует по замкнутому контуру, до выработки моющих свойств. Состава хватает примерно на одну смену, ночью её сбрасывают в очистку.
Внутризаводская станция переработки сточных вод имеет каскад из пресс-фильтров, в которых остаётся сухой осадок. Его утилизируют, а вода идёт дальше, на нейтрализацию. Часть её потом возвращается в процесс промывки.
После фосфатирования, которое де-факто является первой стадией грунтования (так как мелкие очаги коррозии превращаются в стабильные некорродирующие соединения) кузов поступает на линию катофореза. То есть электростатического осаждения грунта. На раствор подаётся высокое напряжение – пальчики лучше туда не совать. Все двери оснащены датчиками: при открывании автоматика снимает напряжение с ванны и останавливает конвейер.
Тут уже можно увидеть процесс, хотя бы через стекло. Вот кузов погружается в ванну…
…и выплывает обратно.
Вообще катафорезных ванн шесть. В первой происходит основной процесс, потом несколько стадий промывки ультрафильтрационным раствором, который получается из расщепления самого грунта на жидкостную и вязкую фракции. Далее – промывка деминерализованной водой.
Прошедший все стадии катафореза кузов стоит на качающемся столе, который наклоняет его вперёд и назад градусов на двадцать, чтобы стекли остатки всех жидкостей из полостей. Теперь кузов можно отправлять в сушильную печь.
Всем этим хозяйством управляет автоматика в виде огромного шкафа вдоль стены.
Длина печи и скорость конвейера ровно такие, чтобы обеспечить нормальную сушку при 200 градусах Цельсия – это наиболее горячий участок всей окрасочной линии. По понятной причине внутрь меня не пустили… Сама сушка занимает 1 час 15 минут. А все стадии от первой промывки до выхода из печи длятся 2 часа 13 минут.
Именно катафорезное грунтование – основа защитного антикоррозийного слоя автомобиля, от его качества зависит долговечность кузова. Заданная технологическим циклом толщина покрытия – 20-24 микрона. На Иж-Авто, как уверяют, грунт не экономят и немного превышают толщину, до 28 микрон. Это лучше защищает металл. Грунтовочные материалы поставляет фирма PPG. Они же идут и в Тольятти, на окраску автомобилей В0 (Алмера, Ларгус и Логан/Сандеро).
Настало время кузову пройти через ласковые женские руки (почему-то тут работают только женщины), которые произведут с ним несколько дополнительных защитных манипуляций – герметизация стыков полиуретановым герметиком, закрывание технологических отверстий заглушками.
Герметик наносится на зафланцовки всех дверей и крышки капота и на все внутренние стыки металлических деталей.
Следующий участок – нанесение противошумных материалов, целлюлозно-битумных. Их просто раскладывают по нужным местам, дабы потом, в следующей печи, они сами «обтекли» рельеф и прилипли к грунту.
Теперь кузов перемещается на участок нанесения герметика на днище.
Тут так же обрабатываются все стыки.
Плёнкой и малярным скотчем защищаются нижние части дверей, ведь дальше на днище будут наносить противошумную мастику.
Сама мастика наносится в закрытой камере, вручную, обычным распылителем.
Теперь нужно пройти ещё одну печь, в которой герметик и мастика полимеризуются и приобретают твёрдость, а звукоизоляционные материалы подплавляются и прилипают к нужным местам. Кузова из печи выходят румяными и посвежевшими.
Теперь настало время того процесса, который и называется окраской.
Перед этим кузов нужно протереть специальными салфетками для снятия статического напряжения.
Потом вручную прокрашивается внутренняя часть кузова, в два слоя.
На окраске лицевой поверхности стоят две группы роботов, последовательно работающих в электростатическом поле и распылением.
А третья группа роботов наносит прозрачный лак
На Иж-Авто применяется двухслойная технология – база + лак. Но база может быть разной, в том числе и с металлизированным оттенком (наполненная алюминиевой пудрой, частицы которой под воздействием электростатического поля приобретают определённую направленность). Бывает база с наполнением в виде мелкодисперсных частиц слюды и кварца, она выглядит ещё эффектнее, чем привычный «металлик».
Сейчас в работе шесть цветов. Гамма формируется по заявкам из дилерских центров и она полностью повторяет ВАЗовскую. Эмали используются фирмы PPG. Для каждого цвета имеется отдельная подсистема (система коммуникаций), так что переход осуществляется достаточно быстро.
Вот и всё, кузов приобрёл почти законченный вид. Совокупная толщина лакокрасочного покрытия составляет 93 микрона для обычного цвета и 150 для металлика (там база толще).
Теперь – финишная проверка и подчистка.
В конце каждой смены произвольно выбранные кузова проверяются на толщину покрытия, его твёрдость и соответствие эталонному цвету. В цехе даже стоит кузов- эталон.
Последняя операция – наклейка декоративной чёрной плёнки 3M на стойки кузова и дверей.
Теперь кузов можно отправлять в сборочный цех.
Сборочный цех
Процесс сборки Грант начинается с того, что кузова поступают из окрасочного цеха в накопитель.
И оттуда уже попадают на первый пост главного конвейера.
Это место называется TRIM, что означает просто конвейер, а участки его обозначаются, соответственно, как TRIM 1, TRIM 2 и т.д. Тут 240 человек собирают салон. Конвейер напольный, движется металлическая лента по центру. Ни одного выступа у движущегося полотна нет, так что тут абсолютно безопасно. Да и скорость невысока.
Вот кузов будущей Гранты заходит на TRIM 1.
Тут снимают двери, которые уходят на отдельную подсборку. Типичное решение для современного автозавода, но новое для Иж-Авто, как ни странно. Когда тут производилась Kia Spectra, её собирали вместе с дверями.
Двери навешиваются на подвесной транспортёр и уезжают в другое место.
А оголившийся кузов готовится принять первые детали салона.
В первую очередь лепят дополнительные вибродемпфирующие накладки, теперь уже битумные.
Их предварительно разогревают в специальной печи до 60 градусов.
Потом устанавливается электропроводка.
Лифтбек требует большей сноровки от сборщиков, чем седан, тут приходится подсобирать заднюю дверь – вести проводку к фонарям и стеклоочистителю. К тому же нужно всегда учитывать комплектацию конкретной машины – проводка там различается. Для удобства монтажа дверь удерживается на распорке.
Бог мой, какие красивые девочки тут работают! Вот эту зовут Ира. Я с ней познакомился и с трудом переборол желание остаться в Ижевске навсегда.
Для защиты порогов используются специальные мягкие накладки, на которые можно безбоязненно садиться.
Раньше использовались накладки и для крыльев, но от них, по словам заводчан, больше проблем, чем пользы: магнитики, которыми они крепились к кузову, царапали лакокрасочное покрытие больше, чем сами работники.
Слева от ТРИМа тем временем идёт формирование кит-боксов (ящичков с детальками и метизами, если по-простому).
Кит-боксы имеют удачную конфигурацию и отлично встают над центральным тоннелем.
Пока идёт сборка салона, отдельные люди подсобирают рулевую рейку – крепят к ней рулевые тяги с наконечниками.
Другой человек монтирует рейку в моторном отсеке. Вот тут раньше было крепление хомутом на двух шпильках.
Но в прошлом году ВАЗ внедрил более жёсткое болтовое крепление. К сожалению, справа остались шпильки и хомут.
Конвейер, тем временем, продолжает движение.
Монтируется ЭБУ и пенопластовая подставка для ног переднего пассажира.
Доделывается проводка.
Теперь настало время волокнистых звукопоглотителей. Их несколько типов.
Те, которым предназначено просто лежать на полу, фиксируют отвратительной на вид смолой.
Но под матами её, разумеется не видно.
Тут же монтируют и главный звукоизолирующий элемент – войлочный мат на моторный щит.
И тут красавицы! Куда деваться?
В «Люксе» передний звукопоглотитель другой, составной.
Устанавливая уплотнитель в дверной проём, одна девочка делает примерно 150 ударов молотком!
Ну что ж, теперь можно класть формованный напольный ковёр.
Подсобранная заранее панель приборов…
…ставится вручную, двумя крепкими работниками.
В перспективе на Иж-Авто планируют делать это специальными манипуляторами, как на том же ВАЗе. Манипуляторы уже куплены и смонтированы в нужных местах конвейера, но работники пока их не освоили.
Зато освоили установку амортизаторов – по похожей технологии. Сначала, рядом с конвейером, стойки подвески подсобираются.
Складываются в удобном месте.
Потом стойки надеваются на манипуляторы и заносятся к точкам крепления на кузове. Вот передняя подвеска:
А вот задняя:
Пока крепят элементы подвески, отойдём в сторонку, на участок сборки приборных панелей. Они приходят с ВАЗа полностью разобранными, в виде набора компонентов. А пластмассовый корпус для некоторых комплектаций вообще льют в Ижевске.
Металлический каркас крепится на специальной стойке.
И на него последовательно навешиваются воздуховоды, отопитель, электроника, корпус.
С этой задачей в производственном масштабе справляются 16 человек.
Неподалёку собирают силовые агрегаты. Двигатель приходит из МСП ВАЗа «голым», без навесного оборудования. Но с катаколлектором.
Не менее отдельно поставляется и коробка передач.
На небольшой настольной линии двигатель соединяют с коробкой и недостающими электроагрегатами.
Это объект приложения сил для 21 работника. Которым в обеденный перерыв и отдохнуть не зазорно.
В конце линии силовой агрегат приобретает завершённый вид, обзоводясь даже колёсными приводами.
Раз уж мы отклонились от главного конвейера, давайте пройдём эту часть цеха до конца. Тем более, что тут начинается самое интересное.
Участок шасси подразумевает, что работа с автомобилем ведётся снизу, следовательно, кузова переезжают на подвесной конвейер.
Самая первая операция на сборке шасси – установка тормозных трубок с регуляторами тормозных сил. Та часть тормозной системы, что находится в моторном отсеке (усилитель тормозов, ABS и пр.) уже установлено на ТРИМе.
А дальше…
Дальше начинается маленький кольцевой конвейер. Это новое оборудование, его закупили только в этом году. На этом кольцевом участке ставятся силовой агрегат и задняя балка в сборе. Производительность – 30 автомобилей в час.
Силовые агрегаты устанавливаются вот на такие палеты:
Получается так:
Позади, на такой же палете ставится собранная задняя балка.
И конвейерная тележка подводит это дело прямо под кузов.
Всё, «женитьба» прошла успешно.
Потом подвесной конвейер продолжает свой прямолинейный путь, а соприкасающийся с ним напольный кольцевой продолжает круговое движение.
После того, как кузов прошёл кольцевой конвейер, на него устанавливают детали выпускной системы и защитные элементы днища – термоэкраны, локеры, пластиковые накладки.
Промежуточный финал – установка колёс. Для этого подвесной конвейер приспускается максимально близко к полу.
Колёса прикручиваются специальным многошпиндельным гайковёртом.
Теперь Гранта похожа на настоящий автомобиль!
И ей самый путь на финальный участок. Конечно, перекатываться машина будет не самостоятельно, на этом участке конвейера смонтированы две движущиеся ленты, аккурат под ширину колеи.
В этом месте дособирают моторный отсек – подключают электрику и тормоза, все патрубки.
Хороший повод оценить качество некоторых пластмассовых деталей. Кромка вот этой накладки обработана из-рук вон плохо, как будто её сапожным ножом отрезал пьяный сапожник. Да, деталь скрыта под крышкой капота… Но это всё равно показатель внимания к качеству конкретного поставщика.
Идём дальше, на установку стёкол. Тут царит хай-тек.
На маленькие треугольники боковых стёкол вручную наносится «праймер» (грунт), по периметру чёрного ободка с внутренней стороны.
А герметик наносит робот – строго по обозначенному контуру и в нужной дозировке. Человек так не сможет.
У монтажника есть пара минут, чтобы вставить стекло в проём.
Аналогичная технология применяется и для других вклеиваемых стёкол – сначала праймер, потом автоматическое нанесение мастики. Только роботы тут уже существенно больше.
И стекло приходится брать минимум двоим, за присоски: тяжёлое.
То же самое – с задним стеклом.
Окончательная полимеризация герметизирующей мастики происходит в течении суток. В этот период нежелательно прикладывать к стёклам какие-то усилия. Для некоторой страховки от смещения стёкла фиксируют скотчем.
Конвейер меж тем продолжает своё монументальное течение.
Я не могу! Опять эти ижевские девушки!
Эти феи оформляют убранство багажников, кладут запаски.
Более сильный пол ставит сткеклоочистители и газовые упоры задних дверей на лифтбеках.
А в салон через свободные пока проёмы заносятся сиденья.
Ну вот мы и подошли к месту с символическим названием «финал 2». Сюда приходят двери с участка их автономной сборки. Двери снимают с транспортёра.
И тем же манипулятором пристыковывают к кузову.
Пришла пора заливать всё жидкое. В первую очередь моторы заправляют охлаждающей жидкостью. Это происходит через специальный коннектор.
Интересно смонтирован компрессор: он берёт жидкость у стационарных магистралей, а сам ездит вдоль конвейера по потолочному рельсу.
Тут же в печке подогреваются накладки на кузов (молдинги). Их монтируют на двусторонний скотч, адгезия у которого выше в горячем состоянии.
Можно посмотреть внутризаводскую расшифровку комплектаций Гранты.
На самом последнем этапе осуществляется контроль сборки и работоспособности избранных узлов. Например, проверяют «дворники» и «писалки».
Машину осматривают так называемые чек-мэны (контролёры, если по-нашему).
Потом заправка бензином, протряска подвески на специальном участке…
…и вуаля, очередная Гранта едет в накопитель.
Отсюда её заберут на регулировку света фар и углов установки колёс, но это рутинные операции, мы их смотреть не будем.
Гранту-лифтбек на Иж-Авто, на самом деле, собирают с февраля. Это были пилотные партии, всего к концу марта сделали около сотни машин. Реально производство стартовало в апреле, когда произвели уже 846 штук. 800 из них сразу поехали к дилерам ВАЗа.
Сейчас завод работает в две смены – на этот график перешли в прошлом году, когда начали делать Гранту-седан. Но седан «уходит» из Ижевска, с июня тут будут производить только лифтбек. Это будет «фирменная» модель завода, в Тольятти её сборка не планируется.
В августе стартует сборка Nissan Sentra, коих ходят собрать до конца года 6800 шт. Японцы уже вовсю тестируют производственные процессы и собрали приличное количество пробных экземпляров.
Общий объём таким образом составит 72 000 автомобилей. Это немного для такого большого и современного завода, только-только чтобы показать безубыточность. О прибыли можно будет думать только в 2015 году, когда к седану Sentra добавится одноимённый хэтчбек (в январе) и Renault Logan нового поколения (в июне- июле). Под Renault сейчас обустраивают отдельный конвейер, на месте разрушенного совсем старого, ещё советского. Вот за этой плёнкой скоро «вырастет» фактически второй завод.
Ижевск получил вторую… нет, третью жизнь. И стал нормальным сборочным заводом, без собственных закидонов и намерения делать что-то своё, посконное. Жаль? Не знаю. Завод и в советское время не был в авангарде автомобилестроительного прогресса. В новых условиях, при тотальном диктате рынка с собственными разработками шанса выжить у него не было никакого. Наверное, лучше в Альянсе, чем в гробу. Как АЗЛК.
PS: изначально этот материал готовился для Drom.ru, там он и опубликован в первую очередь. Но весь собранный материал в дромовскую версию не поместился, так что тут получилась «расширенная комплектация».
Нравится(18)Не нравится(2)
При использовании материала, пожалуйста, сделайте ссылку на Русский автомобиль.
rusautomobile.ru
Лада Гранта характеристики, с пробегом
Очередная модель от «АвтоВАЗа», да еще пришедшая на смену «Классике», — событие историческое. В ближайшее время на ней будет ездить значительная часть нашей страны. Или не будет. Для того что бы это выяснить, а заодно ответить на вопросы читателей «Зарулем.РФ», мы отправились в Тольятти — на родину Lada Granta.
«Разница? Разница есть!» Под такими девизом состоялась первая официальная презентация серийной модели Lada Granta на «АвтоВАЗе». Принимать работу у вазовцев приехал премьер-министр Владимир Путин. После короткого тест-драйва на заводском полигоне, он остался доволен новым российским бюджетником. Собирать Lada Granta будут на одном конвейере вместе с Kalina, для сварки кузовов в настоящее время остановлена одна из двух сварочных линий, где идет настройка оборудования под новую модель.
Аксессуары Лада Гранта
Lada Granta будет выпускаться в трех типах кузова: седан универсал и хетчбэк. Причем грантовский седан «убьет» аналогичный кузов у Kalina, так как за меньшие деньги клиент получает больше машины. В настоящее время идет тестовая сборка, но расчетная мощность — 150 тысяч экземпляров в год.Помимо цены у двух бюджетников довольно значительные расхождения в своих деталях. Несмотря на то, что Granta построена на основе Kalina, примерно 400 комплектующих были разработаны специально под новинку. У Granta собственный багажник, капот, передние и задние крылья, бампера и оптика, а двери и крыша — калиновские. Несмотря на увеличившиеся свесы геометрическая проходимость не пострадала.
Торпеда на Лада Гранта своя оригинальная, но с использованием некоторых деталей от Kalina — к примеру, таких как «крутилки» регулировок отопительной системы. Для уменьшения «сверчков» и удешевления стоимости разработчики пошли по пути сокращения деталей (с 59 до 39 штук) «торпеды», сделав ее более монолитной. Сидения, рулевое колесо, рычаг коробки передач и панели дверей тоже оригинальные. В шасси машины основное изменение касается задней подвески, которая позже появится и на Kalina. Впервые конвейерные вазовские машины получили не параллельный, а «отрицательный развал» задних колес.В конструкции передней подвески увеличен кастор и оптимизирован стабилизатор поперечной устойчивости. На версии с электроусилителем устанавливается «короткая» рулевая рейка — три оборота от упора до упора, против четырех на машине без рулевого усилителя. Все эти изменения позволили сделать Granta устойчивее "Калины". Со слов вазовцев, там где Kalina по максимуму поворот проходит на скорости 80 км/ч, Granta спокойно проезжает на 95 км/ч.
Для Granta будут предложены три варианта бензинового мотора 1,6-литра: 80 л.с., 90 л.с. и 98 л.с. Модификация среднего 8-клапанного 90-сильного двигателя была специально разработана для Granta и также появится затем на Kalina. Каждый агрегат закреплен за одной из трех комплектаций: «Стандарт», «Норма», «Люкс».В 90-сильном моторе была установлена облегченная шатунно-поршневая группа, за счет чего удалось снизить шумность и вибронагруженность и увеличить ресурс движка. Показатели по экономичности остались примерно в тех же границах: примерно 7,0-7,5 литра на «сотню» в зависимости от типа кузова.
Тольяттинцы окончательно определились с поставщиком автоматической трансмиссии — им будет японская компания Jatco, далекий партнер по альянсу «Renault-Nissan-АвтоВАЗ». Но двухпедальные Granta увидят свет не раньше середины 2012 года, потому что процесс доводки 4-скоростного японского «автомата» под нашу модель еще не завершен. Механические коробки с тросовым приводом пока рассматриваются лишь в качестве перспективных комплектующих.
Первые краш-тесты Granta прошла в техническом центре автозавода. И, по заверениям автопроизводителя, модель соответствует всем требованиям по безопасности ЕК ООН, а также российским нормам по безопасности. Однако экспортировать за рубеж Granta пока не собираются.
Планируется, что стартовая цена составит 220 тысяч рублей, а максимальная около 300 тысяч рублей. Конечно, такие ценники не были бы возможны без жесткой экономии на оснащении: более простенькая обивка дверей, меньше деталей в бамперной группе и т.д. Самая дешевая Granta близка по оснащению к классическим «Жигулям», но, разумеется, не по технической начинке.К концу года машины в комплектации «Стандарт» должны поступить в продажу. За ними последуют модели в оснащении «Норма» и «Люкс». Но пока на заводе не берутся точно прогнозировать время появления той или иной модификации. Все зависит от организованности поставщиков.
Лада Гранта: КОНСТРУКТИВНЫЕ ОСОБЕННОСТИ:для LADA Granta разработано и освоено около 400 оригинальных автокомпонентов (примерно 260 из них АВТОВАЗ приобретает у поставщиков).
передние и задние крылья
капот
крышка багажника
светотехника
передний и задний бамперы
панель приборов
сиденья
обивки дверей
рулевое колесо
переднее и заднее стекла
боковые вклеиваемые стекла
У LADA Granta модернизированы передняя и задняя подвески и силовой агрегат.Для LADA Granta разработан модернизированный 8-клапанный мотор объёмом 1,6 литра, его основные особенности
- облегченная шатунно-поршневая группа
- мощность в 90 л.с.
- низкий расход топлива
- низкий уровень шумов и вибраций
- АВТОВАЗ модернизирует технологию при освоении LADA Granta: внедряется порядка 50 новых единиц оборудования и еще около 40 – подвергаются принципиальному изменению.
- Сварка LADA Granta будет осуществляться на автоматических линиях, где до нее производилась сварка кузовов седана LADA Kalina
- Окраска и сборка LADA Granta будет осуществляться на действующем производстве LADA Kalina.
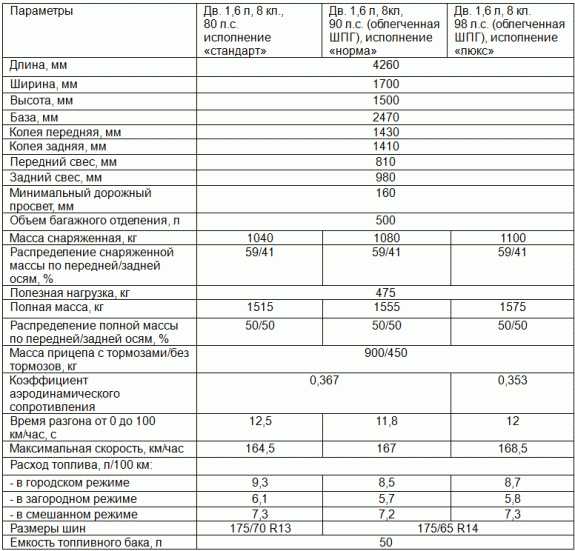
www.info-myauto.ru