Замена коленчатого вала
ремонт и замена коленчатого вала своими руками

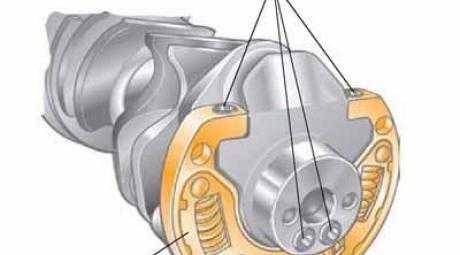
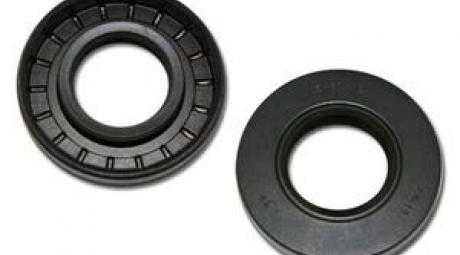
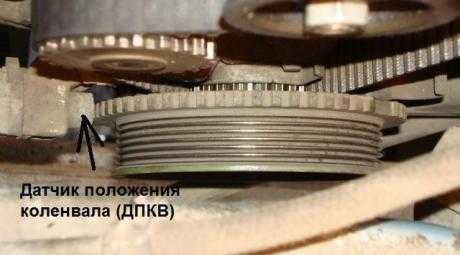
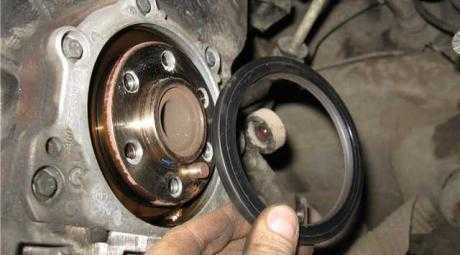
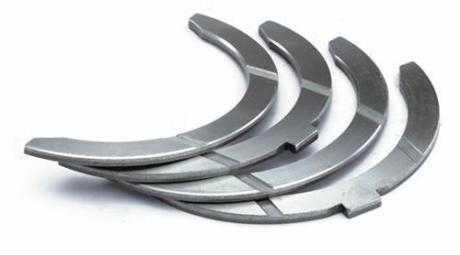
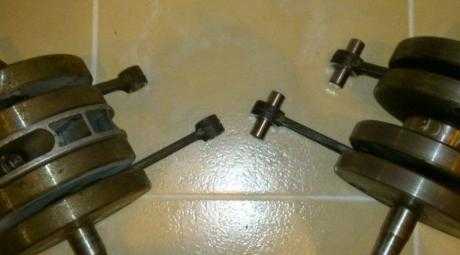
Коленчатый вал является одним из главных элементов двигателя. Он принимает возвратно-поступательную энергию от шатунов поршневой группы и преобразует ее во вращающее движение. Эта энергия, в дальнейшем, передается на коробку передач и колеса автомобиля.
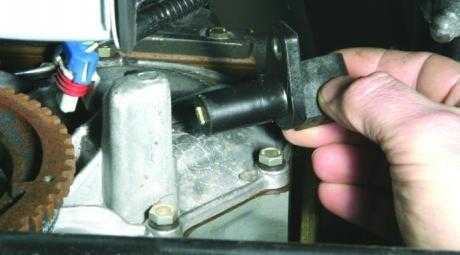
Практически во всех современных источниках технической информации выход из строя датчика положения коленчатого вала (далее по тексту ДПКВ), или датчика синхронизации, причинно связывается с остановкой силового агрег
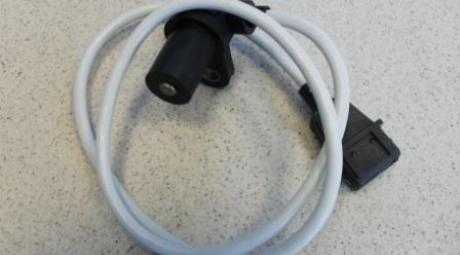
Датчик положения коленчатого вала – элемент, без преувеличения, важный, поскольку нарушение его работоспособности делает невозможным эксплуатацию силовой установки, а, следовательно, и транспортного средства. Если быть предельно точным, то неисправности датчика коленвала влекут за собой...
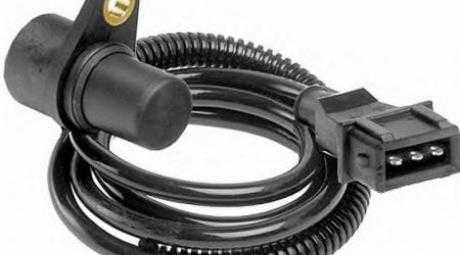
Современный автомобиль – это технически сложный комплекс, включающий в себя различные системы, узлы и агрегаты. Контроль их работоспособности осуществляется при помощи большого количества датчиков.
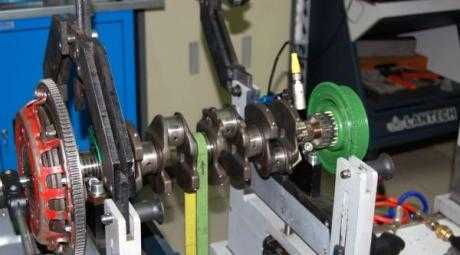
Коленчатый вал, являясь одним из важнейших конструктивных элементов силового агрегата любого автомобиля, производится с применением достаточно сложных технологий.
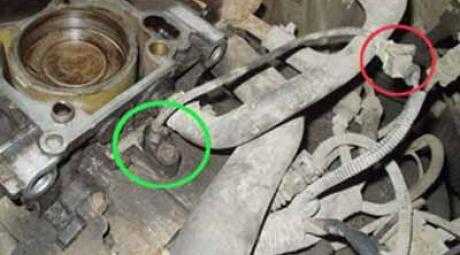
Определить, где находится датчик положения коленвала, не имея представления о том, что это такое и как он выглядит, довольно непросто. Именно поэтому вводная часть нашей статьи будет посвящена информации о назначении и конструктивных особенностях устройства, называемого в зависимости от источника,...
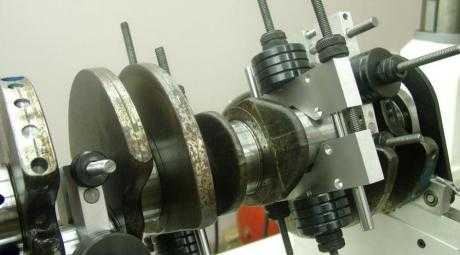
Коленчатый вал представляет собой одну из самых важных и дорогостоящих деталей силового агрегата внутреннего сгорания. Конструктивно он представляет собой деталь, состоящую из коренных и шатунных шеек, которые соединяются щеками. Выполнить ремонт коленвала своими руками практически невозможно.
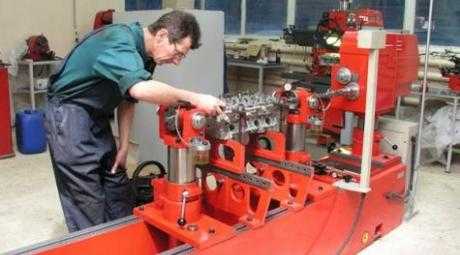
Коленчатый вал — это специальная деталь, выполненная из высокопрочной стали и чугуна. С его помощью создаётся крутящий момент методом передачи усилий от поршней через шатуны. Конструкция данного механизма предусматривает несколько штучных и коренных шеек.
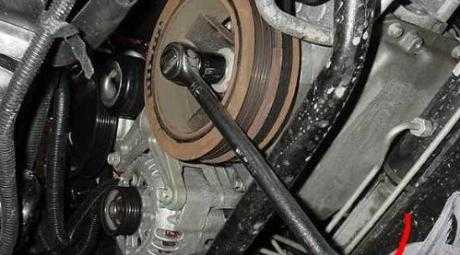
Каждый автолюбитель прекрасно знает, что большинство поломок и технических операций можно выполнить самостоятельно, сэкономив при этом хорошие деньги. В данной статье мы поговорим о том, как снять шкив коленвала без обращения в сервисный центр.
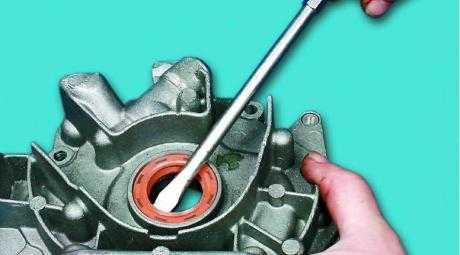
В автомобиле есть масса узлов, в конструкции соединения которых, используются сальники. Самую важную роль данный уплотнитель играет в коленчатом вале мотора. В процессе эксплуатации сальники теряют свою эластичность.
Замена - коленчатый вал - Большая Энциклопедия Нефти и Газа, статья, страница 1
Замена - коленчатый вал
Cтраница 1
Замена коленчатых валов или их ремонт, как правило, вызывается появлением на них рисок, задиров и изгибов шеек, что влечет прово-рот вкладышей, на которых уложен вал, или расплавление их баббитовой заливки. [1]
При замене коленчатого вала двигатель снимают с автомобиля и устанавливают на стенд. Разборка двигателя при этом ведется в следующей последовательности. Снимаются шкив коленчатого вала, масляный картер, маслоприемник, крышка распределительных шестерен, крышка и щиток картера сцепления, крышки шатунов и их вкладыши, шестерня коленчатого вала, крышки коренных подшипников и коленчатый вал в сборе с маховиком и сцеплением, который затем подается на пост разборки коленчатого вала. [2]
Сборка двигателя после замены коленчатого вала ведется в последовательности, обратной разборке. [4]
На пробеге 220 тыс. км необходимо планировать замену коленчатого вала с вкладышами. [5]
Нижнюю крышку звездочек привода газораспределения снимают при ремонте или замене коленчатого вала, ремонте или замене цепи газораспределения и замене самоподжимного сальника уплотнения переднего конца коленчатого вала. [6]
Крышку заднего сальника коленчатого вала снимают при ремонте или замене коленчатого вала и замене самоподжимного сальника вследствие течи. [8]
Капитальный ремонт кроме работ среднего ремонта включает замену гильз цилиндров, расточку гильз или цилиндров под ремонтные размеры, ремонт или замену коленчатого вала. [9]
Так, пониженная износостойкость коренных подшипников коленчатых валов двигателей ЗМЗ-53 и ЗМЗ-24 проявляется, как правило, в необходимости трехкратной замены вкладышей и одной замены коленчатого вала для достижения предельного технического состояния цилиндров. [10]
На рис. 2.11 показаны результаты формирования оптимальной структуры и периодичности ремонтов двигателя ЯМЗ-238, из которых следует, что для данного двигателя за период до КР целесообразно выполнение ПР на пробеге 120 тыс. км, при котором заменяются вкладыши подшипников коленчатого вала и поршневые кольца, а на пробеге 200 тыс. км необходимо проведение СР. При среднем ремонте целесообразна замена коленчатого вала с вкладышами, головки цилиндров в сборе с клапанным механизмом и поршней с поршневыми кольцами. Выполнение ПР и СР обеспечит пробег двигателя до КР, равный 300 тыс. км, и наиболее полное и эффективное использование ресурса его основных деталей. [11]
Он работал у Боултона и Уатта и в 1782 году изобрел планетарную передачу для замены коленчатого вала. Мэрдок руководил установкой и эксплуатацией паровых насосов на шахтах Корнуэлла и построил модель паровоза с балансирным паровым двигателем. Было известно, что треть добываемых в Ньюкасле углей летуча и что при нагревании выделяется горючий газ. Мэрдок нагрел уголь в чайнике и поджег газ, выходящий из отверстий, проделанных в надетом на носик чайника наперстке. В 1792 году он устроил газовое освещение в собственном доме; он также использовал угольный газ, закачанный в бычий пузырь, для переносного светильника. [12]
После контрольного осмотра в случае отсутствия дефектов двигатели подвергают дополнительной горячей обкатке по сокращенному режиму, равному 50 % времени первоначальной обкатки. При замене комплекта коренных и шатунных вкладышей двигатели подвергают повторно горячей обкатке. При замене коленчатого вала и деталей цилиндро-поршневой группы подвергают повторно обкатке по полному режиму. [13]
Следовательно, замена поршней одновременно с заменой поршневых колец экономически не оправдана. Дальнейшее группирование должно выполняться относительно поршней, средний ресурс которых составляет 220 0 тыс. км. На этом же пробеге должна планироваться замена коленчатого вала с вкладышами и поршневых колец, так как их ресурс после замены не превышает 60 - 70 % от первоначального. [14]
За период до КР по разработанной структуре предусматривается проведение одного предупредительного ремонта ( ПР), при котором на пробеге 97 6 тыс. км производится замена вкладышей коренных и шатунных подшипников коленчатого вала, прокладок головок блока цилиндров, и четырех узловых ремонтов. Первый узловой ремонт ( Yi) производится на пробеге 150 тыс. км и заключается он в замене шатунно-поршневой группы. Второй ( У2) выполняется на пробеге 176 0 тыс. км и состоит из замены коленчатого вала с вкладышами коренных и шатунных подшипников. [15]
Страницы: 1 2
www.ngpedia.ru
Ремонт коленчатого вала.
Коленчатый вал компрессора является ответственной и дорогостоящей деталью машины и его восстановление требует дорогого оборудования.
При эксплуатации компрессора происходит не равномерный износ коренных и мотылевых шеек вала. Шатунные шейки изнашиваются быстрее, чем коренные из-за более тяжелых условий работы. Износ шеек вала происходит из-за неравномерности нагрузки вала за один оборот. Неравномерный износ шеек по сечению овальность, по образующей конусность предельно допустимые значения овальности и конусности шеек вала устанавливаются заводскими чертежами и инструкциями.
К. валы изготавливают из стали 40, 45, или 40х. Ст 45 используют в тех случаях когда желательно получить большую жесткость вала и большую износоустойчивость поверхностей.
Заготовки для коленвалов компрессора массой средней производительности получают методом горячей штамповки, а большой производительности – путем ковки.
Для повышения износоустойчивости поверхности шеек валов, сопрягаемые с подшипниками скольжения, подвергают поверхностной закалке ТВЧ на глубину 2-3 мм. Для повышения усталостной прочности валов не подвергают закалке частями на длину 8-10 мм, а также зоны диаметром 8-10 мм в местах расположения отверстий для выхода смазки. Не подвергаются также шейки закалке шейки валов, сопряжение с кольцами подшипников качения и др. поверхности не подверженные трению. Т.е. сплошной закалке валы не подвергают, чтобы избежать внутренних напряжений, вызывающих деформацию.
Основные дефекты коленвала:
1. Отклонение от цилиндрической формы коренных и шатунных шеек не должно превышать 0,5 допуска на диаметр.
2. Биение поверхностей коренных шеек относительно от вала также не должно превышать 0,5 допуска на диаметр.
3. Радиальное биение шеек валов сопрягаемых с сальником ротором не должно превышать 0,03мм. Не параллельность осей шатунных шеек относительно от вала не должно превышать 0,02 мм на 100 мм длины.
Кроме овальности м.б. – конусность поршней и шатунной шейки. К.в. в подшипниках.
Если к.в. опирается конусной шейкой на нижний вкладыш коренного подшипника, то движущая сила Р при действии на поверхность конусной шейки имеет 2 составляющие, одна из которых Р2 – стремиться сдвинуть вал по наклонной поверхности в сторону большего диаметра шейки. Если несколько коренных шеек будут иметь конусность направленную в сторону , то вал отожмется в одну сторону и создает значительное осевое усилие на опорный подшипник компрессора. При перемещении вала в сторону большего диаметра шейки зазор увеличится, вызовет большую утечку масла и следующий нагрев и плавление подшипника. Аналогично если вал будет перемещен в сторону меньшего диаметра шейки зазор уменьшится и подшипник будет нагреваться.
Сила Р2 сдвигает подшипник вдоль шейки в сторону шейки в сторону меньшего диаметра. Возникает таким образом, перекос в шатунном подшипнике, который в свою очередь приводит к перекосу поршня в цилиндре.
Смещение от коренной шейки кол. вала от геометрической оси вала – получается в результате прогиба вала или при неправильной обработки его на станке. При работе вала смещенная шейка вала будет бить на величину S2=200=25. Смещение коренной шейки допускается в пределах 0,02-0,03 мм.
Непараллельное расположение шатунной шейки.
При непараллельной шейке «прекладка» шатуна будет неизбежной. Возникают следующие дефекты: 1) ненормальный нагрев и быстрый износ шатунного подшипника. 2) перегрев и быстрая разработка подшипника верхней головки шатуна . 3) местные износы поверхности цилиндра.
Измерения диаметра шейки, их овальность и конусность производят в 2-х плоскостях:
1) Шатунных – в плоскости их кривошипа и перпендикулярно им.
2) В коренных – в плоскости первого кривошипа и перпендикулярно и ней.
По длине шеек замеры производятся в 2-х,3-х поясах : около …. и в середине шеек.
Прогиб вала оценивают по наибольшему биению средней коренной шейки. При этом необходимо учитывать, что в этом случае индикатор покажет не только прогиб вала, но и овальность средней шейки.
При значительных повреждениях шеек вала их ремонтируют путем проточки на станке с последующей шлифовкой.
Непараллельность образующей поверхности коренных и шатунных шеек от вала определяют перемещением измерительного штифта индикатора вдоль этих шеек. Измерение выполняют при горизонтальном и вертикальном положении кривошипа.
При значительных износах шейки рекомендуется ремонт при помощи вибродуговой наплавки, при помощи втулки и накладки.
Вал вертикального компрессора, имеющий износ шейки до 6 мм в области работы сальниковой набивки, ремонтируют с помощью накладки цельной втулки. Для этого изношенную часть вала протачивают на 6-8 мм и шлифуют.
Овальность и конусность после этой операции д.б. не более 0,03 мм. Втулку изготавливают из полосовой стали марки Ст40,45 или 40х, толщиной 8-10 мм. Стук втулки заваривают эл.дуговой сваркой. Внутренний диаметр протачивают с небольшим натягом, наружний – с припуском на шлифовку. Перед посадкой втулку нагревают до светло красного цвета, затем напрессовывают на проточенную часть вала и охлаждают водой для закалки, потом шлифуют до наминального размера.
При повышенном износе волов их ремонтируют способом металлизации, т.е. нанесением расплавленного распыленного метала на изношенную часть вала.
При наличии трещин любого расположения и размера вал окончательно бракуют.
Коленчатый вал как наиболее нагруженная деталь компрессора испытывает большие переменные нагрузки кручения и изгиба.
Дефектация и ремонт. Основными дефектами коленчатых валов являются искажения геометрической формы шеек и уменьшение их диаметра; наличие рисок, задиров, забоин на поверхностях шеек, увеличение размеров и смятие кромок шпоночных пазов, износ резьбовых участков, повреждение центровых отверстий вала: усталостные трещины и изломы.
Искажение геометрической формы шеек (рис. 2.43) и уменьшение их диаметра определяют измерение диаметра шеек микрометром (рис. 2.44) или индикаторной скобой в двух взаимно перпендикулярных плоскостях и в трех сечениях по длине, биение коленчатого вала - индикатором (рис. 2.45).
Овальность и конусообразность устраняют шлифованием или протачиванием и шлифованием до ближайшего ремонтного размера с последующим полированием поверхности. Шлифование выполняют на круглошлифовальных станках (или на токарных станках, оборудованных приспособлениями) электрокорундовыми кругами зернистостью 50...25 на керамической связке.
Для шлифования коренных шеек вначале у вала проверяют шаблоном центровые отверстия, затем вал закрепляют в центрах станка. Шатунные шейки шлифуют (или протачивают) на специализированных станках (рис. 2.46, а) сиспользованием планшайб с перемещающимися кронштейнами (зажимами) и на универсальных станках с помощью приспособлений - центросмесителей (рис. 2.46, б). Валы закрепляют в зажимах или центросмесителях за обработанные коренные шейки, поверхности которых служат базами для выверки положения шатунных шеек. В центросмесителях обычно предусматривают две центровочные втулки, расположенные под углом 180°.
Коленчатый вал с закрепленными на нем центросмесителями при обработке второй шатунной шейки снимают с центром станка и снова закрепляют, используя вторую пару центровочных втулок.
Предельное уменьшение диаметра шеек вследствие ремонтной обработки и износа не должно превышать 2…6 % номинального размера. При уменьшении диаметра шейки ниже предельного ремонтного размера шейку восстанавливают вибродуговой наплавкой или металлизацией.
Изношенные шейки валов, участки под кольца подшипников качения и ступицу маховика протачивают, направляют и обрабатывают до номинального размера. При нанесении подслоя и основного слоя покрытия на резьбовую часть вала наворачивают гайку, предохраняющую резьбу от попадания расплавленных частиц металла, вал закрепляют в центрах токарного станка, а металлизатор устанавливают на суппорте. Шейки вала, подлежащие напылению, в течение 5...10 с подогревают пламенем металлизатора до 70...900 С. затем включают подачу проволоки и наносят подслой толщиной 0.1...0,5 мм. Основной
слой покрытия толщиной не более 1,5 мм наносят не позже .1 ч после нанесения подслоя, используя проволоку марки 30x13 или 20x13 диаметром
Риски, задиры, забоины на поверхностях шеек валов определяют осмотром. Коленчатый вал годен к эксплуатации без ремонта при наличии незначительных рисок только на поверхностях шеек под кольца подшипников качения и ступицу маховика.
Дефекты шеек валов в зависимости от их характера и величины устраняют шлифованием и полированием на станках или (вручную).
Вручную шлифование производят с помощью отрезков плоских приводных ремней, разъемных хомутов или жимков. Перед шлифованием отверстия масляных каналов заглушают пробками, поверхность шейки смазывают маслом. Между ремнем (или вкладышами хомута) и шейкой вала закладывают шлифовальную шкурку с абразивом из электрокорунда зернистостью 80…16.
Полирование выполняют порошком или шкуркой зернистостью 5...3, а также пастой ГОИ. Поверхность шейки вала после обработки очищают от остатка абразивов, из отверстий каналов удаляют пробки и промывают масляные каналы. Допускается зачистка небольших забоин личным напильником с последующим полированием шейки жимками.
Увеличение размеров и смятие кромок шпоночных пазов измеряют калибрами. Шпоночный паз при износе менее чем 15% его ширины расширяют под ремонтный размер фрезерованием и используют шпонку ремонтного размера.
Усталостные трещины и изломы выявляют цветной или люминесцентной пробой. При наличии трещин вал бракуют.
Изгиб выявляют по величине радиального биения коренных шеек, шейки под сальник и конусной шейки под маховик. Для этого вал устанавливают в центрах проверочного приспособления или токарного станка. Величину биения определяют индикатором. Вал поворачивают в центрах на 360°. В результате индикатор показывает двойную величину биения, в которой одновременно учитываются величина прогиба вала и величина овальности шейки.
Примерный допустимый прогиб валов бескрейцкопфных компрессоров под действием собственной массы составляет 0,1 мм нa 1 м длины Прогиб, превышающий допустимую величину,устраняют правкой в холодном состоянии с помощью пресса или местным наклепом шеек вала. Правка коленчатого вала под прессом вызывает снижение его усталостной прочности, так как под действием изгибающего усилия, приложенного к одной шейке, происходят местная пластическая деформация в наиболее податливом месте и сосредоточение усталостных напряжений у галтелей. Боковые грани паза наваривают вибродуговой наплавкой и фрезеруют до номинального размера.
Износ резьбовых участков обнаруживается в виде износа по диаметру, срыва резьбовых ниток, выкрашиваний, забоин, вмятин, заусенцев. Незначительные вмятины, заусенцы и забоины резьбы на конце вала исправляют прогонкой плашкой на токарном станке или вручную. При значительном износе профиля и срыве ниток старую резьбу срезают, диаметр участка восстанавливают вибродуговой наплавкой, протачивают и нарезают резьбу номинального размера. Если конструкция вала позволяет, то на резьбовом участке срезают изношенную; резьбу и нарезают новую меньшего диаметра. Сопрягаемую деталь изготовляют с учетом нового размера.
Повреждение центровых отверстий вала проверяют осмотром и шаблоном. Положение основных поверхностей центровых отверстий относительно торцов вала проверяют по рискам, нанесенным на шаблон для проверки отверстий. Забоины на кромках отверстий и незначительные повреждения поверхности устраняют зачисткой.
Центровые отверстия со значительными повреждениями исправляют резцом или центровочным сверлом на токарном станке с центровкой вала в люнете относительно неизношенных шеек. Этот способ применяют при значительном прогибе валов, имеющих достаточный запас прочности. Изгиб при величине прогиба от 0,02 до 0,04% длины вала устраняют местным наклепом щек с помощью пневматического молотка со специальной угловой надставкой. Если выпуклость погнутого вала обращена наружу, наклепывают внутренние поверхности шеек, при обратной деформации - наружные поверхности шеек. Места приложения усилий после правки проверяют на отсутствие трещин.
Скрученность вала определяют по угловому смещению шпоночных пазов. Вал для проверки устанавливают на призмах, на проверочной плите. Угол скручивания измеряют
слой покрытия толщиной не более 1,5 мм наносят не позже .1 ч после нанесения подслоя, используя проволоку марки 30x13 или 20x13 диаметром
Риски, задиры, забоины на поверхностях шеек валов определяют осмотром. Коленчатый вал годен к эксплуатации без ремонта при наличии незначительных рисок только на поверхностях шеек под кольца подшипников качения и ступицу маховика.
Дефекты шеек валов в зависимости от их характера и величины устраняют шлифованием и полированием на станках или (вручную).
Вручную шлифование производят с помощью отрезков плоских приводных ремней, разъемных хомутов или жимков. Перед шлифованием отверстия масляных каналов заглушают пробками, поверхность шейки смазывают маслом. Между ремнем (или вкладышами хомута) и шейкой вала закладывают шлифовальную шкурку с абразивом из электрокорунда зернистостью 80…16.
Полирование выполняют порошком или шкуркой зернистостью 5...3, а также пастой ГОИ. Поверхность шейки вала после обработки очищают от остатка абразивов, из отверстий каналов удаляют пробки и промывают масляные каналы. Допускается зачистка небольших забоин личным напильником с последующим полированием шейки жимками.
Увеличение размеров и смятие кромок шпоночных пазов измеряют калибрами. Шпоночный паз при износе менее чем 15% его ширины расширяют под ремонтный размер фрезерованием и используют шпонку ремонтного размера.
Усталостные трещины и изломы выявляют цветной или люминесцентной пробой. При наличии трещин вал бракуют.
Изгиб выявляют по величине радиального биения коренных шеек, шейки под сальник и конусной шейки под маховик. Для этого вал устанавливают в центрах проверочного приспособления или токарного станка. Величину биения определяют индикатором. Вал поворачивают в центрах на 360°. В результате индикатор показывает двойную величину биения, в которой одновременно учитываются величина прогиба вала и величина овальности шейки.
Примерный допустимый прогиб валов бескрейцкопфных компрессоров под действием собственной массы составляет 0,1 мм нa 1 м длины Прогиб, превышающий допустимую величину,устраняют правкой в холодном состоянии с помощью пресса или местным наклепом шеек вала. Правка коленчатого вала под прессом вызывает снижение его усталостной прочности, так как под действием изгибающего усилия, приложенного к одной шейке, происходят местная пластическая деформация в наиболее податливом месте и сосредоточение усталостных напряжений у галтелей. Боковые грани паза наваривают вибродуговой наплавкой и фрезеруют до номинального размера.
Износ резьбовых участков обнаруживается в виде износа по диаметру, срыва резьбовых ниток, выкрашиваний, забоин, вмятин, заусенцев. Незначительные вмятины, заусенцы и забоины резьбы на конце вала исправляют прогонкой плашкой на токарном станке или вручную. При значительном износе профиля и срыве ниток старую резьбу срезают, диаметр участка восстанавливают вибродуговой наплавкой, протачивают и нарезают резьбу номинального размера. Если конструкция вала позволяет, то на резьбовом участке срезают изношенную; резьбу и нарезают новую меньшего диаметра. Сопрягаемую деталь изготовляют с учетом нового размера.
Повреждение центровых отверстий вала проверяют осмотром и шаблоном. Положение основных поверхностей центровых отверстий относительно торцов вала проверяют по рискам, нанесенным на шаблон для проверки отверстий. Забоины на кромках отверстий и незначительные повреждения поверхности устраняют зачисткой.
Центровые отверстия со значительными повреждениями исправляют резцом или центровочным сверлом на токарном станке с центровкой вала в люнете относительно неизношенных шеек. Этот способ применяют при значительном прогибе валов, имеющих достаточный запас прочности. Изгиб при величине прогиба от 0,02 до 0,04% длины вала устраняют местным наклепом щек с помощью пневматического молотка со специальной угловой надставкой. Если выпуклость погнутого вала обращена наружу, наклепывают внутренние поверхности шеек, при обратной деформации - наружные поверхности шеек. Места приложения усилий после правки проверяют на отсутствие трещин.
Скрученность вала определяют по угловому смещению шпоночных пазов. Вал для проверки устанавливают на призмах, на проверочной плите.
28. Подшипники скольжения подвергаются износу в результате воздействия сил трения, повышенных нагрузок и температур.
Дефектация и ремонт. Основными дефектами подшипников скольжений являются уменьшение толщины антифрикционного слоя задиры, риски, трещины, выкрашивания, частичные отслоения баббитовой заливки, ослабление посадки подшипника в базовой детали, заплавление смазочных канавок.
Уменьшение толщины антифрикционного слоя сопровождается увеличением радиального зазора между подшипником скольжения и сопрягаемой с ним деталью (рис. 2.34). Угол соприкосновения вала с подшипником у нового сопряжения составляет 60...800. По мере износа угол соприкосновения увеличивается и достигнет 1200 при этом увеличивается радиальный зазор (S1), нарушается работа масляного клина и начинается ускоренный износ подшипника и вала.
При определении величины масляного зазора щупом следует знать, что измерение занижает фактическое значение зазора на 0,01...0,015 мм.
Зазор разъемных подшипников измеряют с помощью выжимок. Отрезки свинцовой проволоки толщиной на 0,2...0,3 мм больше величины предполагаемого зазора закладывают между верхним вкладышем и шейкой вала (расстояние от торца вкладыша до проволоки 10...15 мм), собирают подшипники и затягивают гайки болтов до рабочего состояния. После разборки подшипника измеряют толщину выжимок.
Зазор в сопряжении коленчатый вал - шатунный подшипник в процессе эксплуатации не должен увеличиваться более чем в 1,5…2,5 раза по отношению к максимальной величине начального зазора.
Изношенные бронзовые втулки заменяют новыми, растачивают под ремонтный размер или восстанавливают осадкой. После запрессовки новой втулки или осадки старой отверстие втулки растачивают или развертывают. Втулки с баббитовой заливкой перезаливают с последующим растачиванием.
Тонкостенные вкладыши заменяют новыми (вкладыши компрессоров с ходом поршня 130 мм могут быть перезалиты). Толстостенные вкладыши, а также подшипники в виде заливки баббита ремонтируют перезаливкой с последующим растачиванием. У разъемных подшипников с набором прокладок зазор в сопряжении восстанавливают перетяжкой.
Втулки верхних головок шатунов и вкладыши компрессоров с ходом поршня 130 мм после замены целесообразно растачивать на координатно-расточном станке. При этом обеспечивается параллельность и отсутствие скручивания осей расточки вкладышей и втулки.
Задиры, риски, трещины, наволакивание антифрикционного сплава, выкрашивания и частичные отслоения баббитовой заливки могут быть обнаружены при осмотре подшипника. Трещины 1, выкрашивания 2 и отслоения заливки (рис. 2.35) выявляют внешним осмотром и простукиванием подвешенных подшипников (вкладышей) молотком или металлическим прутом.
Подшипник при ударе должен издавать чистый звук; дребезжание или глухой звук указывают на наличие трещин или отслоений баббита. Наличие этих же дефектов может быть выявлено проверкой на выжимание масла или керосиновой пробой. На рабочих поверхностях тонкостенных вкладышей не допускаются местные участки выплавления и отслоения баббита, наволакивание сплава, кольцевые риски шириной 0,5…1,0 мм и глубиной более половины толщины антифрикционного слоя; трещины и точечные выкрашивания баббита. Тонкостенные вкладыши с подобными дефектами заменяют новыми.
Площадь местных повреждений рабочей поверхности толстостенных подшипников не должна превышать 5% ее общей, площади. Отдельные раковины и выкрашивания нарабочей поверхности баббитовой заливки заплавляют баббитом той же марки.
Глубокие риски, задиры, наволакивание сплава, выкрашивания на торцах подшипников зачищают; если есть необходимость, заливают или наплавляют.
Изношенные по торцам подшипники восстанавливают наплавкой, при значительных разрушениях перезаливают или заменяют.
Ослабление посадки подшипника в базовой детали устраняют металлизацией, осталиванием или меднением. Изношенные отверстия в базовых деталях растачивают под втулки ремонтных размеров.
Заплавление или засорение смазочных канавок устраняют расчисткой или углублением канавок шабером.
Перед заменой тонкостенных вкладышей проверяют диаметр, правильность формы и шероховатость поверхности сопрягаемой шейки вала. Вкладыши подбирают по соответствующему ремонтному размеру. Их заменяют без любого вида подгонки и только попарно. Стыки установленного в гнезде вкладыша должны выступать над плоскостью разъёма базовой детали на 0,02…0,15 мм (суммарная величина), вследствие чего при затяжке болтов крепления создается посадка с натягом. Удерживаются вкладыши от перемещений в гнезде имеющимся на нем усом, утапливаемым в паз сопрягаемой детали.
Между вкладышем и его постелью запрещается закладывать прокладку (металлическую фольгу). После установки новых вкладышей проверяют зазор в сопряжении «шейка вала - подшипник скольжения».
Подшипники - втулки заменяют, устанавливая после сверления отверстий для подачи смазки и изготовления смазочных канавок.
Бронзовые втулки верхних головок шатунов, закрепляемые прессовыми посадками, устанавливают в предварительно нагретые до 80…1000 С головки или запрессовывают с помощью пресса. При запрессовке втулок следят за правильным расположением канавок и отверстий для масла. После охлаждения верхней головки шатуна или запрессовки втулка сжимается, и ее внутренний диаметр уменьшается примерно на 0,5 величин посадочного натяга. Поэтому после установки (запрессовки) проводят чистовое растачивание или развертывание отверстий втулок вала или корпуса.
Щуп толщиной 0,05 мм в любой зоне окружности не должен проходить между торцом кольца и упорной поверхностью заплечика. Наличие радиального зазора в кольце проверяют покачиванием в осевом направлении свободного кольца или щупом.
Установка кольца в требуемое положение достигается изменением толщины прокладки под крышку корпуса или с помощью регулировочной гайки. При монтаже упорных подшипников качения одно кольцо напрессовывают на вал, а другое устанавливают в корпус совместно с сепаратором. Диаметр отверстия в корпусе под неподвижное кольцо на 0,5...1,0 мм больше наружного диаметра этого кольца, что позволяет ему самоустанавливаться под действием осевых нагрузок, передаваемых телами качения.
При установке вала в двух подшипниках качения (что характерно для большинства поршневых компрессоров) кольца одного из подшипников закрепляют от перемещения в осевом направлении на валу и в корпусе, а у второго закрепляют только кольцо, имеющее посадку с натягом.
Парные радиально-упорные подшипники винтовых компрессоров устанавливают, как правило, с предварительным осевым натягом. Величину предварительного осевого натяга регулируют изменением толщины регулировочного кольца между внутренними кольцами спаренного комплекта подшипников.
Похожие статьи:
poznayka.org
Снятие и проверка состояния коленчатого вала
Снятие и проверка состояния коленчатого вала
Сборка коленчатого вала - общие сведенияКоленчатый вал откован из стали. Вал имеет три коренных и четыре шатунных шейки. Кривошипы с шатунными шейками первого и второго цилиндров расположены между первой и второй коренными шейками вала; между второй и третей коренными шейками расположены кривошипы третьей и четвертой шатунных шеек.
|
С целью снижения нагрузки, приходящейся на коренные подшипники кривошипы оснащены коваными противовесами, уравновешивающими центробежные силы, возникающие между двумя соседними опорами.
Все кривошипы и шейки коленчатого вала оборудованы внутренними маслотоками, по которым масло поступает к вкладышам подшипников.
Сами кривошипы не подлежат обработке. Что касается шеек и обеих цапф коленчатого вала, то они тщательно обрабатываются. Как коренные, так и шатунные шейки подвергаются поверхностной закалке током высокой частоты. Диаметр коренных шеек составляет 60 мм, шатунных - 45 мм.
Торец задней цапфы коленчатого вала оборудован фланцем под посадку маховика. Уплотнение посадки задней цапфы в блоке достигается при помощи сальника размера 85х105х12 мм.
Передняя цапфа вала представляет собой шейку, используемую под посадку зубчатого колеса/звездочки ременного/цепного привода распределительного вала, а также шкива клиновидного ремня привода вспомогательных агрегатов (водяной насос и генератор). Герметизация посадки передней цапфы обеспечивается передним сальником (42х58х8 мм).
Оба сальника изготавливаются из фторкаучука и отличаются повышенной надежностью и долговечностью.
Величина осевого люфта вала контролируется путем установки специальных дистанционных колец и упорной шайбы, которые устанавливаются на первую коренную шейку вала. Дистанционные кольца стопорятся от проворачивания предусмотренным на внешней стороне выступом. Допустимая величина осевого люфта коленчатого вала представлена в Спецификациях в начале настоящей Главы.
Упорные кольца помимо номинальной толщины (1.480 ÷ 1.490 мм), выпускаются также ремонтных размеров: 1.605 ÷ 1.615 мм, 1.703 ÷ 1.740 мм и 1.855 ÷ 1.865 мм.
Кольца большего размера всегда следует устанавливать со стороны прошлифованной боковой поверхности щеки кривошипа. Со стороны упорной шайбы всегда устанавливается кольцо номинального размера.
В случае износа упорная шайба (утрата гладкости боковых поверхностей) подлежит замене.
Все коленчатые валы на производстве подвергаются статической и динамической балансировке с точностью до 0.2 Нм.
Крышки коренных подшипников коленчатого вала выполнены из чугуна и крепятся к блоку цилиндров при помощи двусторонних болтов М11. На крышках отлиты метки в виде цифр "1", "2" или "3". При этом крышка с номером "1" должна устанавливаться на ближайший к приводу ГРМ подшипник, с номером "3" - на ближайший к маховику, а номер "2" - на средний.
Вкладыши подшипников коленчатого вала выполнены из тонкой стальной полосы, покрытой изнутри слоем сплава специального состава. Толщина слоя составляет 0.35 мм. Коренные вкладыши имеют ширину 24 мм при толщине 2.5 мм, шатунные - 22 м при 1.5 мм.
По всей длине каждого из верхних коренных вкладышей проходит канавка, служащая для подвода моторного масла, поступающего через отверстие овальной формы во вкладыше. На торцевых поверхностях полуколец вкладышей оборудованы замки, обеспечивающие однозначность посадки полуколец и фиксацию их от проворачивания. а - Коренные вкладыши b - Шатунные вкладыши 1 - Верхние вкладыши 2 - Нижние вкладыши |
Никакая маркировка, на вкладышах не предусмотрена, а потому, их толщина определяется при помощи микрометра.
Вкладыши остаются пригодными для дальнейшего употребления, если они не слишком изношены, не оставляют чрезмерный рабочий зазор подшипников, свободны от трещин, царапин и сколов поверхностного слоя. дефектные вкладыши подлежат замене в обязательном порядке. Составители настоящего Руководства рекомендуют производить замену вкладышей в комплекте для всех подшипников одновременно.
Прежде чем приступать к проверке состояния коленчатого вала, его необходимо очистить от следов смазки и грязи. В случае выявления очевидных дефектов, а также в случае отсутствия уверенности в оценке состояния вала, его следует заменить. По завершении любого вида восстановительного ремонта необходимо тщательно прочистить все маслотоки вала. (сначала воспользуйтесь керосином, затем продуйте отверстия сжатым воздухом).
СНЯТИЕ
|
|
ПРОВЕРКА
|
carmanz.com
5 Методы ремонта коленчатых валов
1) Основной операцией ремонта коленчатых валов является шлифование коренных и шатунных шеек на ремонтные размеры. Обычно для коленчатых валов многих автотракторных двигателей принято 3…4 ремонтных размера шеек (с интервалом 0,25 ... 0,5 мм), на которые имеются соответствующего размера стандартные ремонтные вкладыши. Шейки коленчатых валов шлифуют на круглошлифовальных станках типа 3423 или 3420, оснащенных необходимым набором приспособлений. После шлифования шейки, с целью уменьшения шероховатости и повышения усталостной прочности подвергаются полированию или суперфинишированию.
2) Валы, изношенные более последнего ремонтного размера, восстанавливаются нанесением металла на изношенные поверхности наплавкой, напеканием порошков, приваркой ленты, напылением и другими методами.
3) Восстановление размеров шеек под распределительную шестерню и шкивы производится теми же методами с последующей обработкой на номинальный размер.
4) Изношенные стенки шпоночных канавок восстанавливают обработкой на увеличенный размер.
5) При износе отверстии во фланце коленчатого вала под болты крепления маховика их рассверливают на увеличенный ремонтный размер по кондуктору или совместно с маховиком и нарезают в отверстиях резьбу большего размера.
6) Изгиб валов дизельных двигателей величиной не более 0,2 мм, двигателей с искровым зажиганием грузовых автомобилей не более 0,1 мм и легковых автомобилей — 0,05 мм самоустраняется при перешлифовке шеек на ремонтный размер. При более высоких значениях изгиба производят правку коленчатого вала под прессом или наклепом щек при помощи пневматических молотков.
7) После восстановления коленчатые валы проверяют на наличие трещин с помощью магнитных или ультразвуковых дефектоскопов и подвергают динамической балансировке на специальных машинах (типа БМУ-4). Допускаемая величина дисбаланса для коленчатых валов тракторных двигателей 100 ... 160 гсм, двигателей грузовых автомобилей — 70 ... 120 гсм, легковых автомобилей — 10 ... 50 гсм. Неуравновешенность устраняют высверливанием отверстий в противовесах вала.
Необходимо помнить: после ремонта коленчатый вал должен быть тщательно промыт и продут сжатым воздухом для удаления загрязнений, абразивных частиц, стружки и следов СОЖ.
6 Порядок выполнения работы
1 Дефектация коленчатого вала.
1.1 Установить коленчатый вал в призмах на поверочной плите.
Рисунок 1 Измерение изгиба коленвала. |
Рисунок 2 Схема замеров шеек коленвала. |
1.2 Провести измерение диаметра шеек коленчатого вала, согласно схеме замеров (см. рисунок 2). Результаты занести в микрометражную карту (таблица 2).
1.3 Измерить радиус кривошипа вала (рисунок 3), его изгиб (рисунок 1), радиус галтелей и биение цилиндрических поверхностей. Результаты занести в таблицу 3.
Рисунок 3 Измерение радиуса кривошипа
1.4 По результатам дефектации определить степень износа ремонтопригодность вала. Установить место максимального износа шеек и определить ремонтные размеры для перешлифовки коренных и шатунных шеек коленчатого вала.
2 Подготовка станка к работе
2.1 Проверить состояние шлифовального круга и при необходимости произвести его правку. Правка производится по периферии, торцам и по радиусу закругления круга алмазным карандашом при помощи специального приспособления к станку ЗА423. Алмазным карандашом при вращении круга и при обильной смазочно-охлаждающей жидкости производят съем материала круга. При этом удаляются "засаленные" слои, обнажаются новые режущие зерна и круг приобретает необходимую форму. Радиус закругления проверяется профильными радиусными щупами на просвет. Подача алмаза при правке составляет 0,02 ... 0,05 мм на один двойной ход. а продольная подача 0.03 ... 0,10 мм на один оборот круга.
2.2 Произвести настройку станка, установить принятую частоту вращения круга и изделия, при шлифовании шатунных шеек установить центросместители на радиус кривошипа шлифуемого коленчатого вала, подобрать и закрепить в планшайбах противовесы.
3 Шлифование шеек коленчатого вала.
3.1 Установить коленчатый вал в патронах: фланцем в передней бабке и шейкой под шкив в задней бабке.
3.2 Установить индикаторное приспособление и проверить биение шлифуемой шейки вала, которое должно быть не более 0.05 мм без учета овальности шейки. При большем биении производят выверку (центровку) вала при помощи центросместителей (в вертикальной плоскости) и поворотом вала в патронах (в горизонтальной плоскости).
3.3 Включить станок и прошлифовать шейку на необходимый размер.
Шлифование шеек коленчатых валов производится при следующих режимах: окружная скорость круга 25 ...30 м/с, частота вращения коленчатого вала при предварительном шлифовании - 28 ... 32 мин-1и подача по глубине 0,010 ... 0,015 мм/об. При чистовом шлифовании частота вращения вала 8... 15 мин-1, подача 0,003 ...0,005 мм /об.
Для шлифования применяют специальные круги из электрокорунда или карбида кремния (Э, ЭВ, КЗ) зернистостью 40 ...50 на керамической связке (твердость С 1 С М2, средняя структура).
Во избежание появления прожогов и микротрещин на шлифуемую поверхность
обильно подается СОЖ обычно 3…4% раствор кальцинированной соды или эмульсия (10 г эмульсола на 1 л воды).
4 Проверка отремонтированного коленчатого вала на соответствие техническим условиям.
4.1 Установить отремонтированный коленчатый вал в призмах на поверочной плите.
4.2 Проверить все параметры вала в соответствии с техническими требованиями на выдачу коленчатых валов из ремонта (см. таблицу 4). Результаты измерений занести в таблицу 3.
studfiles.net