Поршень и цилиндр
поршень двигателя
Поршень двигателя является одной из самых главных деталей и конечно же от материала и качества поршней зависит успешная эксплуатация мотора и его долгий ресурс. В этой статье, больше рассчитанной на новичков, будет описано всё (ну или почти всё), что связано с поршнем, а именно: назначение поршня, его устройство, материалы и технология изготовления поршней и другие нюансы.
Сразу хочу предупредить уважаемых читателей, что если какой то важный нюанс, связанный с поршнями, или с технологией их изготовления, я уже написал более подробно в другой статье, то разумеется мне нет смысла повторяться в этой статье. Я просто напросто буду ставить соответствующую ссылку, перейдя по которой уважаемый читатель при желании сможет перейти на другую более подробную статью и в ней ознакомиться с нужной информацией о поршнях более подробно.
На первый взгляд многим новичкам может показаться, что поршень довольно простая деталь и придумать уже что то более совершенное в его технологии производства, форме и конструкции невозможно. Но на самом деле всё не так просто и не смотря на внешнюю простоту формы, поршни и технологии их изготовления до сих пор совершенствуются, особенно на самых современных (серийных или спортивных) более высоко-оборотистых форсированных двигателях. Но не будем забегать вперёд и начнём от простого к сложному.
Для начала разберём для чего нужен поршень (поршни) в двигателе, как он устроен, какие формы поршней бывают для разных двигателей и далее уже плавно перейдём к технологиям изготовления.
Для чего нужен поршень двигателя.
Поршень, за счёт кривошипно-шатунного механизма (коленвала и шатуна — см. рисунок чуть ниже), перемещаясь возвратно-поступательно в цилиндре двигателя, например перемещаясь вверх — для засасывания в цилиндр и сжатия в камере сгорания рабочей смеси, а так же за счёт расширения сгораемых газов перемещаясь в цилиндре вниз, совершает работу, преобразуя тепловую энергию сгораемого топлива в энергию движения, которая способствует (через трансмиссию) вращению ведущих колёс транспортного средства.
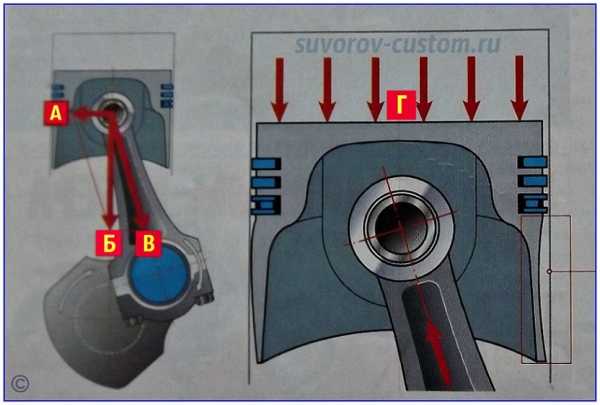
Поршень двигателя и силы действующие на него: А — сила, прижимающая поршень к стенкам цилиндра; Б — сила, перемещающая поршень вниз; В — сила передаваемая усилие от поршня к шатуну и наоборот, Г — сила давления сгораемых газов, перемещающая поршень вниз.
То есть по сути без поршня в одноцилиндровом двигателе, или без поршней в многоцилиндровом двигателе — невозможно движение транспортного средства, на которое установлен двигатель.
Кроме того, как видно из рисунка, на поршень действуют несколько сил, (также на том же рисунке не показаны противоположные силы, давящие на поршень снизу вверх).
И исходя из того, что на поршень давят и довольно сильно несколько сил, у поршня должны быть некоторые важные свойства, а именно:
- способность поршня двигателя противостоять огромному давлению газов, расширяющихся в камере сгорания.
- способность сжать и противостоять большому давлению сжимаемого топлива (особенно на дизелях).
- способность противостоять прорыву газов между стенками цилиндра и своими стенками.
- способность передавать огромное давление на шатун, через поршневой палец, без поломок.
- способность не изнашиваться долгое время от трения о стенки цилиндра.
- способность не заклиниваться в цилиндре от теплового расширения материала, из которого он изготовлен.
- поршень двигателя должен иметь способность противостоять высокой температуре сгорания топлива.
- иметь большую прочность при небольшой массе, чтобы исключить вибрацию и инерционность.
И это далеко не все требования, предъявляемые к поршням, особенно на современных высоко-оборотистых моторах. О полезных свойствах и требованиях современных поршней мы ещё поговорим, а для начала давайте рассмотрим устройство современного поршня.
Как видно на рисунке, современный поршень можно разделить на несколько частей, каждая из которых имеет важное значение и свои функции. Но ниже будут описаны основные наиболее важные части поршня двигателя и начнём с наиболее важной и ответственной части — с днища поршня.
Донышко (днище) поршня двигателя.
Это самая верхняя и наиболее нагруженная поверхность поршня, которая обращена непосредственно к камере сгорания двигателя. И нагружено донышко любого поршня не только большой давящей силой от расширяющихся с огромной скоростью газов, но и высокой температурой сгорания рабочей смеси.
Кроме того, донышко поршня своим профилем определяет нижнюю поверхность самой камеры сгорания и также определяет такой важный параметр, как степень сжатия. Кстати, зависеть форма донышка поршня может от некоторых параметров, например от расположения в камере сгорания свечей, или форсунок, от расположения и величины открытия клапанов, от диаметра тарелок клапанов — на фото слева хорошо видны выемки для тарелок клапанов в донышке поршня, которые исключают встречу клапанов с донышком.
Так же форма и размеры донышка поршня зависят от объёма и формы камеры сгорания двигателя, или от особенностей подачи в нее топливно-воздушной смеси — например на некоторых старых двухтактных двигателях на донышке поршня делали характерный выступ-гребень, играющий роль отражателя и направляющий поток продуктов горения при продувке. Этот выступ показан на рисунке 2 (выступ на донышке также виден на рисунке выше, где показано устройство поршня). Кстати, на рисунке 2 так же показан рабочий процесс древнего двухтактного двигателя и то, как влияет выступ на донышке поршня на наполнение рабочей смесью и на выпуск отработанных газов (то есть на улучшение продувки).
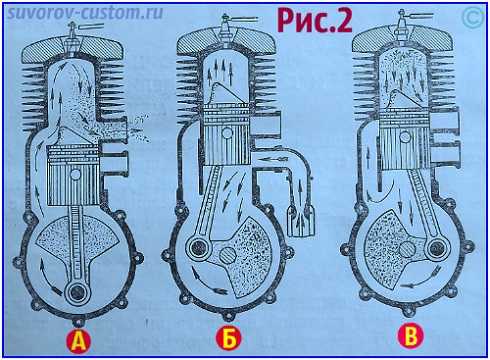
Двухтактный двигатель мотоцикла — рабочий процесс
Но на некоторых двигателях (например на некоторых дизелях) на донышке поршня в центре наоборот имеется круглая выемка, благодаря которой увеличивается объем камеры сгорания и соответственно уменьшается степень сжатия.
Но, поскольку выемка небольшого диаметра в центре донышка является не желательной для благоприятного наполнения рабочей смесью (появляются нежелательные завихрения), то на многих двигателях на донышках поршней в центре перестали делать выемки.
А для уменьшения объема камеры сгорания приходится делать так называемые вытеснители, то есть изготавливать донышко с определенным объёмом материала, который располагают немного выше основной плоскости донышка поршня.
Ну и ещё один важный показатель — это толщина донышка поршня. Чем она толще, тем прочнее поршень и тем большую тепловую и силовую нагрузку он сможет выдержать довольно долго. А чем тоньше толщина донышка поршня, тем бóльшая вероятность прогара, или физического разрушения донышка.
Но с увеличением толщины донышка поршня, соответственно увеличивается и масса поршня, что для форсированных высоко-оборотистых моторов очень нежелательно. И поэтому конструкторы идут на компромисс, то есть «ловят» золотую середину между прочностью и массой, ну и конечно же постоянно стараются усовершенствовать технологии производства поршней для современных моторов (о технологиях позже).
Жаровой пояс поршня.
Как видно на рисунке выше, где показано устройство поршня двигателя, жаровым поясом считается расстояние от донышка поршня до его самого верхнего компрессионного кольца. Следует учесть, что чем меньше расстояние от донышка поршня до верхнего кольца, то есть чем тоньше жаровой пояс, тем более высокую тепловую напряжённость будут испытывать нижние элементы поршня, и тем быстрее они будут изнашиваться.
Поэтому для высоко напряжённых форсированных двигателей желательно делать жаровой пояс потолще, однако это делают не всегда, так как это тоже может увеличить высоту и массу поршня, что для форсированных и высоко-оборотистых двигателей нежелательно. Тут так же как и с толщиной донышка поршня, важно найти золотую середину.
Уплотняющий участок поршня.
Этот участок начинается от нижней части жарового пояса до того места, где заканчивается канавка самого нижнего поршневого кольца. На уплотняющем участке поршня расположены канавки поршневых колец и вставлены сами кольца (компрессионные и масло-съёмные).
Канавки колец не только удерживают поршневые кольца на месте, но ещё и обеспечивают их подвижность (благодаря определённым зазорам между кольцами и канавками), что позволяет поршневым кольцам свободно сжиматься и разжиматься за счёт своей упругости (что очень важно если цилиндр изношен и имеет форму бочки). Это также способствует прижиму поршневых колец к стенкам цилиндра, что исключает прорыв газов и способствует хорошей компрессии, даже если цилиндр немного изношен.
Как видно на рисунке с устройством поршня, в канавке (канавках), предназначенной для маслосъёмного кольца имеются отверстия для обратного стока моторного масла, которое масло-съёмное кольцо (или кольца) снимает со стенок цилиндра, при движении поршня в цилиндре.
Кроме основной функции (не допустить прорыва газов) уплотняющего участка, у него есть ещё одно важное свойство — это отвод (точнее распределение) части тепла от поршня на цилиндр и весь двигатель. Разумеется для эффективного распределения (отвода) тепла и для предотвращения прорыва газов важно, что бы поршневые кольца довольно плотно прилегали к своим канавкам, но особенно к поверхности стенки цилиндра.
Головка поршня двигателя.
Головка поршня представляет из себя общий участок, который включает в себя уже описанные мной выше донышко поршня и его и уплотняющий участок. Чем больше и мощнее головка поршня, тем выше его прочность, лучше отвод тепла и соответственно больше ресурс, но и масса тоже больше, что как было сказано выше, нежелательно для высоко-оборотистых моторов. А снизить массу, без уменьшения ресурса, можно если увеличить прочность поршня путём усовершенствования технологии изготовления, но об этом я подробнее напишу позже.
Кстати, чуть не забыл сказать, что в некоторых конструкциях современных поршней, изготавливаемых из алюминиевых сплавов, в головке поршня делают нирезистовую вставку, то есть в головку поршня заливают ободок из нирезиста (специального прочного и стойкого к коррозии чугуна).
В этом ободке прорезают канавку для самого верхнего и наиболее нагруженного компрессионного поршневого кольца. И хотя благодаря вставке немного увеличивается масса поршня, зато существенно увеличивается его прочность и износостойкость (к примеру нирезистовую вставку имеют наши отечественные Тутаевские поршни, изготовленные на ТМЗ).
Компрессионная высота поршня.
Компрессионная высота — это расстояние в миллиметрах, которое отсчитывается от донышка поршня до оси поршневого пальца (или наоборот). У разных поршней компрессионная высота разная и разумеется чем больше расстояние от оси пальца до донышка, тем она больше, а чем она больше, тем лучше компрессия и меньшая вероятность прорыва газов, но и больше сила трения и нагрев поршня.
На старых тихоходных и мало-оборотистых моторах компрессионная высота поршня была больше, а на современных более высоко-оборотистых двигателях стала меньше. Здесь тоже важно найти золотую середину, которая зависит от форсировки мотора (чем выше обороты, тем меньше должно быть трение и меньшая компрессионная высота).
Юбка поршня двигателя.
Юбкой называют нижнюю часть поршня (её ещё называют направляющей частью). Юбка включает в себя бобышки поршня с отверстиями, в которые вставляется поршневой палец. Внешняя поверхность юбки поршня является направляющей (опорной) поверхностью поршня и эта поверхность также как и поршневые кольца трётся о стенки цилиндра.
Примерно в средней части юбки поршня имеются приливы, в которых имеются отверстия для поршневого пальца. А так как вес материала поршня у приливов тяжелее, чем в других местах юбки, то деформации от воздействия температуры в плоскости бобышек будут больше, чем в других частях поршня.
Поэтому для снижения температурных воздействий (и напряжений) на поршне с двух сторон с поверхности юбки снимают часть материала, примерно на глубину 0,5-1,5 мм и получаются небольшие углубления. Эти углубления, называемые холодильниками, не только способствуют устранению температурных воздействий и деформаций, но ещё и препятствуют образованию задиров, а так же улучшают смазку поршня при движении его в цилиндре.
Следует так же отметить, что юбка поршня имеет форму конуса (в верху у донышка уже, внизу шире), а в плоскости, перпендикулярной оси поршневого пальца имеет форму овала. Эти отклонения от идеальной цилиндрической формы минимальные, то есть имеют всего несколько соток мм (эти величины разные — чем больше диаметр, тем больше отклонения).
Конус нужен для того, что бы поршень расширялся от нагрева равномерно, ведь в верху температура поршня выше, а зн
Ну а овал предназначен для компенсации быстрого износа на стенках юбки, которые стираются быстрее там где трение выше, а выше оно в плоскости движения шатуна.
Благодаря юбке поршня (точнее её боковой поверхности) обеспечивается нужное и правильное положение оси поршня к оси цилиндра мотора. С помощью боковой поверхности юбки, к цилиндру двигателя передаются поперечные усилия от действия боковой силы А (см. самый верхний рисунок в тексте, а так же рисунок справа) которая периодически воздействует на поршни и цилиндры, при перекладке поршней во время вращения коленвала (кривошипно-шатунного механизма).
Также благодаря боковой поверхности юбки осуществляется отвод тепла от поршня к цилиндру (так же как и от поршневых колец). Чем больше боковая поверхность юбки, тем лучше идёт отвод тепла, меньше утечка газов, меньше стук поршня при некотором износе втулки верхней головки шатуна (или при неточной обработке втулки — см. рисунок слева), впрочем как и при трёх компрессионных кольцах, а не двух (об этом я подробнее написал вот тут).
Но при слишком длинной юбке поршня больше его масса, больше трения возникает о стенки цилиндров (на современных поршнях для уменьшения трения и износа стали наносить антифрикционное покрытие на юбку), а лишняя масса и трение очень нежелательны в высоко-оборотистых форсированных современных (или спортивных) моторах и поэтому на таких двигателях юбку постепенно стали делать очень короткой (так называемая миниюбка) и постепенно почти от неё избавились — так и появился Т-образный поршень, показанный на фото справа.
Но и у Т-образных поршней есть недостатки, например у них опять же могут быть проблемы с трением о стенки цилиндра, из-за недостаточной смазываемой поверхности очень короткой юбки (причём на малых оборотах).
Более подробно об этих проблемах, а так же в каких случаях Т-образные поршни с мини юбкой нужны в некоторых двигателях, а в каких нет, я написал отдельную подробную статью вот здесь. Там же написано об эволюции формы поршня двигателя — советую почитать. Ну а мы думаю уже разобрались с устройством поршней и плавно переходим к технологиям изготовления поршней, чтобы понять какие поршни, изготовленные разными способами лучше, а какие хуже (менее прочные).
Поршни для двигателей — материалы изготовления.
При выборе материала для изготовления поршней предъявляют строгие требования, а именно:
- материал поршня должен иметь отличные антифрикционные (антизадирные) свойства.
- материал поршня двигателя должен иметь довольно высокую механическую прочность.
- материал поршня должен иметь малую плотность и хорошую теплопроводность.
- материал поршня должен быть стоек к коррозии.
- материал поршня должен иметь малый коэффициент линейного расширения и быть по возможности близок или равен коэффициенту расширения материала стенок цилиндра.
Чугун.
Раньше, на заре двигателестроения, ещё со времён самых первых автомобилей, мотоциклов и самолётов (аэропланов), для материала поршней применяли серый чугун (кстати для поршней компрессоров тоже). Конечно же, как и у любого материала, у чугуна имеются как достоинства, так и недостатки.
Из достоинств следует отметить хорошую износостойкость и достаточную прочность. Но наиболее важное достоинство чугунных поршней, устанавливаемых в двигатели с чугунными блоками (или гильзами) — это такой же коэффициент теплового расширения, как и чугунного цилиндра двигателя. А значит тепловые зазоры можно сделать минимальными, то есть гораздо меньше, чем у алюминиевого поршня, работающего в чугунном цилиндре. Это позволяло существенно увеличить компрессию и ресурс поршневой группы.
Ещё один существенный плюс чугунных поршней — это небольшое (всего 10 %) снижение механической прочности при нагреве поршня. У алюминиевого поршня снижение механической прочности при нагреве ощутимо больше, но об этом ниже.
Но с появлением более оборотистых двигателей, при использовании чугунных поршней, на больших оборотах стал выявляться их главный недостаток — довольно большая масса, по сравнению с алюминиевыми поршнями. И постепенно перешли к изготовлению поршней из алюминиевых сплавов, даже в двигателях с чугунным блоком, или гильзой, хоть и пришлось делать алюминиевые поршни с гораздо бóльшими тепловыми зазорами, чтобы исключить клин алюминиевого поршня в чугунном цилиндре.
Кстати, раньше на поршнях некоторых двигателей делали косой разрез юбки, который обеспечивал пружинящие свойства юбки алюминиевого поршня и исключал его заклинивание в чугунном цилиндре — пример такого поршня можно увидеть на двигателе мотоцикла ИЖ-49).
А с появлением современных цилиндров, или блоков цилиндров, полностью выполненных из алюминия, в которых уже нет чугунных гильз (то есть покрытых никасилем или керонайтом) появилась возможность изготавливать алюминиевые поршни тоже с минимальными тепловыми зазорами, ведь тепловое расширение легкосплавного цилиндра стало практически таким же, как и у легкосплавного поршня.
Алюминиевые сплавы. Практически все современные поршни на серийных двигателях сейчас изготавливают из алюминиевых сплавов (кроме пластиковых поршней на дешёвых китайских компрессорах).
У поршней, выполненных из алюминиевых сплавов тоже имеются как достоинства, так и недостатки. Из основных достоинств следует отметить небольшой вес легкосплавного поршня, что очень важно для современных высокооборотистых двигателей. Вес алюминиевого поршня конечно же зависит от состава сплава и от технологии изготовления поршня, ведь кованный поршень весит значительно меньше, чем выполненный из того же сплава методом литья, но о технологиях я напишу чуть позже.
Ещё одно достоинство легкосплавных поршней, о которой мало кто знает — это довольно высокая теплопроводность, которая примерно в 3-4 раза выше, чем теплопроводность серого чугуна. Но почему достоинство, ведь при высокой теплопроводности и тепловое расширение довольно не малое и придётся и придётся и тепловые зазоры делать больше, если конечно цилиндр чугунный (но с современными алюминиевыми цилиндрами это стало не нужно).
А дело в том, что высокая теплопроводность не позволяет нагреваться донышку поршня более чем 250 °C, а это способствует гораздо лучшему наполнению цилиндров двигателей и конечно же позволяет ещё более повысить степень сжатия в бензиновых моторах и тем самым поднять их мощность.
Кстати, чтобы как то усилить отлитые из лёгкого сплава поршни, в их конструкцию инженеры добавляют различные усиливающие элементы — например делают стенки и донышко поршня толще, а бобышки под поршневой палец отливают более массивными. Ну или делают вставки из того же чугуна, я об этом уже писал выше. И конечно же все эти усиления увеличивают массу поршня, и в итоге получается, что более древний и прочный поршень, изготовленный из чугуна, проигрывает в весе легкосплавному поршню совсем чуть чуть, где то процентов на 10 — 15.
И тут любому напрашивается вопрос, а стоит ли овчинка выделки? Стóит, ведь у алюминиевых сплавов есть ещё одно отличное свойство — они раза в три лучше отводят тепло, чем тот же чугун. И это важное свойство незаменимо в современных высоко-оборотистых (форсированных и горячих) двигателях, у которых довольно высокая степень сжатия.
К тому же современные технологии производства кованных поршней (о них чуть позже) существенно повышают прочность и уменьшают вес деталей и уже не требуется усиление таких поршней различными вставками, или более массивными отливками.
К недостаткам поршней, выполненных из алюминиевых сплавов относятся такие как: довольно большой коэффициент линейного расширения алюминиевых сплавов, у которых оно составляет примерно в два раза больше, чем у поршней выполненных из чугуна.
Ещё одним существенным недостатком алюминиевых поршней является довольно большое снижение механической прочности, при повышении температуры поршня. К примеру: если легкосплавный поршень нагреть до трёхсот градусов, то это приведёт к снижению его прочности аж в два раза (примерно на 55 — 50 процентов). А у чугунного поршня при его нагреве прочность снижается ощутимо меньше — всего на 10 — 15%. Хотя современные поршни, выполненные из алюминиевых сплавов методом поковки, а не с помощью литья, при нагреве теряют прочность гораздо меньше.
На многих современных алюминиевых поршнях снижение механической прочности и слишком большое тепловое расширение устраняется более совершенными технологиями производства, которые заменили традиционное литьё (об этом ниже), а так же специальными компенсационными вставками (например упомянутые мной выше — вставки из нирезиста), которые не только увеличивают прочность, но и значительно уменьшают тепловое расширение стенок юбки поршня.
Поршень двигателя — технологии изготовления.
Ни для кого не секрет, что со временем, чтобы увеличить мощность двигателей, постепенно начали повышать степень сжатия и обороты моторов. А чтобы поднять мощность без особого ущерба для ресурса поршней, постепенно совершенствовались технологии их изготовления. Но начнём всё по порядку — с обычных литых поршней.
Поршни изготовленные методом обычного литья.
Эта технология самая простая и древняя, она применяется с самого начала истории авто и двигателестроения, ещё со времён первых чугунных поршней.
Технология производства поршней для самых современных двигателей обычным литьём уже почти не применяется. Ведь на выходе получается продукт имеющий изъяны (поры и т.д.) значительно снижающие прочность детали. Да и технология обычного литья в форму (кокиль) довольно древняя, она позаимствована ещё у наших древних предков, которые много веков назад отливали бронзовые топоры.
И залитый в кокиль сплав алюминия повторяет форму кокиля (матрицы), а потом деталь ещё нужно обработать термически и на станках, снимая лишний материал, что отнимает не мало времени (даже на станках с ЧПУ).
Литьё под давлением.
У поршня, изготовленного методом простого литья прочность не высока, из-за пористости детали и постепенно многие фирмы от этого способа отошли и начали отливать поршни под давлением, что значительно улучшило прочность, так как пористость почти отсутствует.
Технология литья под давлением, существенно отличается от технологии обычного литья топоров бронзового века и конечно же на выходе получается более аккуратная и прочная деталь, имеющая несколько лучшую структуру. Кстати, литьём алюминиевых сплавов под давлением в форму (ещё эту технологию называют жидкой штамповкой) отливают не только поршни, но и рамы некоторых современных мотоциклов и автомобилей.
Но всё же и эта технология не идеальна и если даже вы возьмёте в руки отлитый под давлением поршень и рассмотрев его, ничего не обнаружите на его поверхности, но это не значит, что и внутри всё идеально. Ведь в процессе литья, даже под давлением, не исключено появления внутренних пустот и каверн (мельчайших пузырьков), уменьшающих прочность детали.
Но всё же литьё поршней под давлением (жидкая штамповка) существенно лучше обычного литья и эта технология до сих пор применяется на многих заводах при изготовлении поршней, рам, деталей ходовой и других деталей автомобилей и мотоциклов. А кому интересно более подробно почитать о том, как делают жидко-штампованные поршни и о их преимуществах, то читаем о них вот здесь.
Кованные поршни автомобиля (мотоцикла).
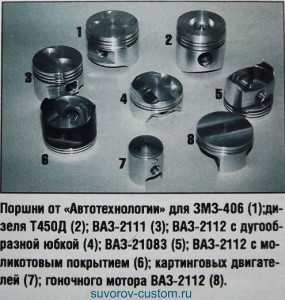
Кованые поршни для отечественных автомобилей.
Эта наиболее прогрессивная на данный момент технология производства современных легкосплавных поршней, которые имеют множество преимуществ перед литыми и которые устанавливают на самые современные высоко-оборотистые моторы, с высокой степенью сжатия. У кованных поршней, изготовленных авторитетными фирмами, практически нет недостатков.
Но мне нет смысла писать о кованных поршнях подробно в этой статье, так как я написал о них две очень подробные статьи, которые каждый желающий сможет почитать, кликнув на ссылки ниже.
Кованные поршни 1
Кованные поршни 2
Вот вроде бы и всё, если что нибудь вспомню ещё о такой важной детали, как поршень двигателя, то обязательно допишу, успехов всем.
suvorov-castom.ru
Поршень двигателя
Строительные машины и оборудование, справочник
Категория:
Устройство и работа двигателя
Поршень двигателяПоршень представляет собой металлический стакан, установленный в цилиндре с некоторым зазором. При рабочем ходе поршень днищем воспринимает давление газов, а при других ходах осуществляет вспомогательные такты. Верхняя усиленная часть поршня, воспринимающая давление газов, называется головкой, а нижняя направляющая часть — юбкой. Приливы в стенках юбки, служащие для установки поршневого пальца, называются бобышками.
Поршни карбюраторных двигателей изготовляют из алюминиевых сплавов. Алюминиевые поршни обладают малым весом, вследствие чего уменьшаются силы инерции, а следовательно, и нагрузки на детали двигателя при его работе. Кроме того, алюминиевые поршни, так же как и алюминиевые головки, обладают лучшей теплопроводностью, поэтому они меньше нагреваются при работе и способствуют снижению температуры рабочей смеси.
В результате этого можно повысить степень сжатия двигателя, не опасаясь, что возникнет детонационное сгорание топлива.
В целях повышения износостойкости поршней для их изготовления в последние годы стали применять высококремнистые алюминиевые сплавы с большим содержанием кремния (до 20—25%). Поршни из алюминиевых сплавов изготовляют путем отливки в металлические формы. Для снятия внутренних напряжений в материале литые заготовки поршней подвергают длительному отжигу, а затем подвергают механической обработке.
В карбюраторных двигателях головка поршня имеет плоское днище и толстые стенки с внутренними ребрами, повышающими ее прочность и обеспечивающими хороший отвод тепла. В головке на боковой наружной поверхности имеются канавки для установки поршневых колец. В верхней части головки поршня у двигателей некоторых типов (ГАЗ) делают глубокую узкую канавку, уменьшающую передачу тепла от днища к верхнему компрессионному кольцу, работающему в особенно неблагоприятных условиях, чтобы устранить опасность его пригорания. В некоторых двигателях (ЗИЛ) в головку при заливке поршня заделывается чугунная кольцевая вставка, в которой протачивается канавка для верхнего компрессионного кольца. Такое мероприятие повышает долговечность поршня.
Для улучшения приработки поршней в цилиндрах и для уменьшения износа на юбку 2 поршня наносят специальные покрытия. Обычно трущуюся поверхность юбки лудят — покрывают очень тонким слоем олова (толщиной 0,004—0,006 мм). В средней части юбки делают приливы-бобышки 3 с отверстиями для установки поршневого пальца.
Для того чтобы при нагревании поршень мог расширяться без заедания в цилиндре, поршень устанавливают с зазором между стенкой цилиндра и юбкой. Алюминий расширяется при нагревании значительно больше, чем чугун. Чтобы в холодном двигателе зазор между поршнем и цилиндром не был чрезмерно большим, что может вызвать стуки поршня и утечку газов из цилиндра, в алюминиевых поршнях применяют пружинящие разрезные юбки. При боковом разрезе по всей длине юбка несколько пружинит, и поршень вставляется в цилиндр холодного двигателя плотно, с малым зазором. При нагревании поршня разрез дает возможность юбке расшириться без заедания поршня в цилиндре. Применяют также поршни с частичным, несквозным разрезом Т- или П-образной формы, что повышает жесткость юбки.
Для уменьшения бокового зазора сечение юбки делают не круглой формы, а овальной. Величина овальности (разность осей овала) юбки равна примерно 0,15—0,29 мм. Поршень устанавливают в цилиндре холодного двигателя с минимальным зазором по большой оси овала юбки, располагаемой в плоскости качания шатуна, где действуют боковые силы, прижимающие поршень к стенкам цилиндра. При нагревании поршня юбка может расширяться в направлении малой оси овала, где между юбкой и цилиндром имеется большой зазор. Поршни по длине изготовляют ступенчатыми или конусными, так как зазор вверху между стенкой цилиндра и головкой поршня должен быть больше, чем внизу, вследствие большего нагревания головки. Величина зазора между юбкой поршня и цилиндром для двигателей разных марок колеблется в пределах 0,012—0,08 мм.
Рис. 1. Конструкция поршня
Чтобы при нагревании поршни меньше расширялись, а также для повышения их прочности, в поршни двигателей некоторых марок при отливке заделывают пластинки из специальной малорасширяющейся стали. Для уменьшения веса у некоторых поршней вырезают нерабочую часть юбки. Эти вырезы служат также для прохода противовесов при вращении коленчатого вала у короткоходных двигателей.
Для обеспечения лучшего уравновешивания двигателя поршни к каждому двигателю подбирают равного веса. С этой целью на днище поршня, кроме указания группы по размеру, выбивают соответствующую метку весовой группы. Разница в весе поршней, подбираемых для одного двигателя, не должна превышать 6—8 г.
При сборке поршни обычно устанавливают разрезом на левую сторону двигателя, так как во время работы к этой стороне поршень прижимается с меньшей силой. Для удобства сборки на днище поршня в этом случае делают специальную метку, которая должна быть обращена к передней части двигателя.
Рис. 2. Типы поршней
В дизелях применяют поршни из специального чугуна (двухтактные дизели ЯАЗ) или из высококремнистого алюминиевого сплава (четырехтактные дизели ЯМЗ) с неразрезной юбкой, имеющей большую жесткость. Так как в дизелях боковая сила, прижимающая поршень к стенке цилиндра, достигает значительной величины, то для получения нормального удельного давления между цилиндром и поршнем юбку делают большей длины, Днище поршня, воспринимающее значительное давление газов, делают более прочным с усилением его внутренней стороны большим количеством ребер. Для обеспечения хорошего смесеобразования при непосредственном впрыске топлива в днище поршня располагается камера сгорания специальной формы.
Читать далее: Поршневые кольца
Категория: - Устройство и работа двигателя
Главная → Справочник → Статьи → Форум
stroy-technics.ru
Проверка поршней и цилиндров | СКУТЕР ЭКСПЕРТ
Проверка цилиндра и поршня
Цилиндр и поршень проверяются внешним осмотром на предмет неравномерного износа, наличия трещин и повреждений. Кроме того, измерением проверяется износ поршня и сравнивается с предельным значением износа, которое приводится в Руководстве по ремонту. Если даже величина износа наход
приводится в Руководстве по ремонту. Если даже величина износа находится в допустимых пределах, поршень подлежит замене при наличии повреждений или неравномерного износа. Аналогично, даже при отсутствии повреждений или неравномерного износа поршень нужно заменить, если его износ превысил допустимую величину.
Проверка поршня
• Царапины и другие повреждения на поверхности поршня
Если нарушается процесс сгорания, то на днище поршня и на жаровом поясе возникает недопустимая деформация или появляются повреждения. Более того, если поршень работает в жёстких условиях или масло потеряло свои качества, то на поверхности поршня появляются следы сильного износа или трещины.
• Неравномерный износ и повреждения канавок для поршневых колец
Неравномерный износ канавки приводит к сильной вибрации кольца, которая вызывает повышенный расход масла и прорыв картерных газов. Большое значение имеет не только измерение износа, но и визуальная оценка его равномерности.
• Забитые дренажные отверстия
Маслосъёмное кольцо удаляет со стенки цилиндра излишки масла, которое попадает в цилиндр разбрызгиванием из картера коленчатого вала. То масло, которое кольцо соскребает со стенки цилиндра, возвращается в картер через дренажные отверстия в нижней канавке под кольцо. Если дренажные отверстия засоряются, то масло начинает угорать. В некоторых поршнях дренажные отверстия выполняются в нижней части канавки под кольцо.
• Измерение наружного диаметра поршня
По мере роста пробега увеличивается износ поверхностей трения поршня. При сильном износе увеличивается зазор между юбкой и цилиндром - это приводит к увеличению шума работающего двигателя и к росту угара масла. Место измерения диаметра юбки и значение предельного износа указаны в Руководстве по ремонту. Если износ больше допустимого, то поршень подлежит замене. Далее, если износ поршня находится в допустимых пределах, но после измерения диаметра цилиндра становится очевидно, что зазор между юбкой и цилиндром все же превышает допустимое значение, то поршень нужно поменять, если это поможет вернуть зазор к норме.
• Проверка зеркала цилиндра
Почти всегда верхняя часть цилиндра изнашивается быстрее нижней из-занеравномерности условий трения между кольцами и цилиндром по высоте. Кроме того, цилиндр изнашивается быстрее в направлении перпендикулярном оси пальца, поскольку в этом направлении поршень давит на цилиндр сильнее. Цилиндр никогда не изнашивается равномерно: профиль износа имеет вид воронки с расширением вверх и форму овала в плане. Уступ, который образуется в ВМТ верхнего компрессионного кольца можно оценить визуально и пальцем, на ощупь. Далее, измерьте диаметр вверху, в среднем поясе и внизу, в двух плоскостях: параллельно оси поршневого пальца (Х) и поперёк оси пальца (Y). Эти измерения позволят определить конусность и овальность цилиндра. Если на зеркале цилиндра имеются царапины, задиры или износ превышает допустимое значение, то цилиндр нужно расточить под поршни ремонтного размера (если выпускаются). Если блок цилиндров по каким-то причинам не допускает расточки, то блок нужно заменить.
• Проверка поршневого пальца и отверстий в бобышке пальца
Оба конца поршневого пальца работают внутри поршневых бобышек, а средняя его часть работает в верхней головке шатуна. Для проверки износа и величины фактического зазора нужно измерить диаметр поршневого пальца в тех местах, которыми он работает в отверстиях и диаметры соответствующих отверстий.
Если результат одного из измерений выходит за допустимые пределы поршень с пальцем нужно заменить.
Характер износа отверстия в поршневой бобышке зависит от условий работы двигателя. Равномерный износ практически не встречается - обычно он имеет форму овала. По этой причине диаметр отверстия нужно измерять в двух плоскостях: в вертикальной и в горизонтальной (X и Y). Если результат одного измерения выходит из допустимых пределов, то поршень с пальцем нужно менять.
Измерьте диаметр отверстия в верхней головке шатуна в вертикальной плоскости, поскольку в этом направлении износ всегда больше. Если результат одного выходит из допустимых пределов, то шатун нужно заменить.
Поскольку масло в парах трения поршень-палец и шатун-палец обеспечивается масляным клином определённой толщины, то при увеличении зазора сверх допустимого значения перечисленные детали нужно заменить. Замена обязательна, даже если износ отдельной детали в паре трения не превысил допустимого значения. Вычислите величину зазоров в перечисленных выше парах трения и замените детали, если величина зазора превысит допустимое значение.
* Проверка верхней плоскости блока цилиндров на коробление
Если происходит коробление верхней плоскости блока цилиндров, то обжатие прокладки головки блока цилиндров не будет происходить так, как нужно. Там где удельное давление на прокладку будет ниже нормы, может наблюдаться прорыв охлаждающей жидкости или, что ещё хуже - отработавших газов. В большинстве случаев названные выше неприятности случаются из-за коробления верхней плоскости блока цилиндров, неправильной затяжки болтов крепления головки цилиндров, коробления нижней плоскости головки блока или из-за сочетания названных причин.
В одноцилиндровых двигателях с небольшим рабочим объёмом коробление верхней плоскости блока цилиндров редко является причиной прорыва газового стыка. Хотя для многоцилиндровых двигателей причиной проблем с газовым стыком является в основном коробление нижней плоскости головки цилиндров и неправильная затяжка болтов крепления головки, нужно проверять верхнюю плоскость блока цилиндров.
При помощи поверочной линейки проверьте верхнюю плоскость блока цилиндров на просвет и измерьте зазор плоским щупом. Если коробление превышает допустимое значение, замените блок цилиндров. Если обнаружено коробление блока цилиндров, то велика вероятность того, что головка цилиндров также пострадала. Проверьте на коробление и головку цилиндров.
scooterexpert.ru
Конструкция поршней
Поршень можно разделить на три части, выполняющие различные функции: днище, уплотняющая часть и направляющая часть (юбка). Днище и уплотняющая часть образуют головку поршня.
Днище поршня, образующее с головкой цилиндра камеру сгорания, кончается у верхней кромки канавки под верхнее поршневое кольцо. Эту часть поршня иногда называют жаровым поясом. Форма днища поршня зависит от формы камеры сгорания и расположения клапанов, а в двухтактных двигателях также от системы газораспределения.
При вогнутом днище форма камеры сгорания приближается к сферической (при верхнем расположении клапанов), увеличивается поверхность, омываемая горячими газами, и возрастает возможность образования нагара, при котором резко повышается тепловой режим. Прочность вогнутого днища меньше, чем плоского, поэтому в ряде случаев его усиливают. Обработка такого днища также затруднительна.
Выпуклое днище придает камере сгорания щеле-видную форму, что ухудшает процесс смесеобразования. Из-за выпуклости температура днища возрастает, но уменьшается нага-рообразование. Основным преимуществом такого днища является уменьшение массы поршня из-за большой прочности днища и отсутствия усиливающих ребер.
Плоское днище является промежуточным по своим показателям между двумя первыми и имеет наибольшее распространение вкарбюраторных двигателях.
В некоторых двигателях поршни имеют так называемые вытеснители,которые способствуют в процессе сжатия достижению желаемого направления движения заряда, а в процессе сгорания — осуществлению плавного нарастания давления.
У дизелей днище поршня имеет разнообразные и в ряде случаев сложные формы, зависящие от степени сжатия, способа смесеобразования, расположения форсунок и других факторов. Так, в дизеле с однополостной камерой сгорания днище придает камере сгорания благоприятную форму. Для увеличения скорости вихря и улучшения смесеобразования камеру сгорания располагают в днище поршня. Для повышения прочности днища поршня и лучшего отвода теплоты с внутренней стороны оно имеет ребра, форма которых определяется опытным путем.
Размеры днища поршня выбирают, исходя из максимального давления сгорания, необходимой жесткости поршня и максимальной интенсивности отвода от него теплоты. Как правило, переходы от днища поршня к его уплотняющей части в плоскости бобышек делают массивными в виде сплошных приливов или ребер. С внутренней стороны днища теплота от него отводится воздухом и маслом. Наличие ребер не улучшает теплоотвода от днища.
В дизелях, где в днище поршня располагается камера сгорания, применяют принудительное охлаждение днища путем опрыскивания его внутренней поверхности маслом. Для этого масло подводится непосредственно от коленчатого вала по каналу в стержне шатуна к распылителю с калиброванным отверстием, расположенному в поршневой головке шатуна, или распыливается через неподвижныефорсунки,закрепленныевнижнейчастигильзы.
Уплотняющая часть поршня начинается от верхней кромки канавки под верхнее поршневое кольцо и кончается у нижней кромки канавки под нижнее поршневое кольцо (последнее кольцо перед поршневым пальцем), т. е. это та часть поршня, где расположены канавки для поршневых колец.
Уплотняющая часть имеет диаметр, увеличивающийся к низу поршня. Она передает стенкам цилиндра до 80% теплоты, воспринимаемой днищем.
Практически уплотняющая часть поршня почти не участвует в передаче боковых сил. Поверхность этой части поршня имеет канавки, вследствие чего невозможно создать устойчивую масляную пленку. Величину зазора между цилиндром и уплотняющей частью поршня выбирают из условия предохранения поршневых колец от воздействия горячих газов и предотвращения попадания масла в камеру сгорания. Как правило, этот зазор делают очень малым (близким к нулю). Число компрессионных колец устанавливают в зависимости от быстроходности и типа двигателя.
Для уменьшения тепловой напряженности верхнего поршневого кольца канавку под него следует делать на некотором расстоянии от днища поршня , при этом увеличивается высота поршня. В некоторых случаях перед первым поршневым кольцом делают выточку, которая является воздушным экраном . Опыт работы с такими поршнями показал, что эта выточка закоксовывается и влияние ее на работу первого кольца уменьшается. В некоторых конструкциях применяют жароупор ные вставки для верхнего поршневого кольца (двигатель ЗИЛ-130 и др.), которые в 2—2,5 раза повышают долговечность поршня.
Для уплотнения цилиндра быстроходного двигателя достаточно двух-трех компрессионных и одного или двух маслосъемных поршневых колец.
Большинство двигателей имеет одно маслосъемное поршневое кольцо (нижнее) для сбрасывания излишков масла.
В канавках для маслосъемных колец сверлят один или два ряда отверстий для отвода масла внутрь поршня. В случае двух рядов отверстий один ряд сверлят в самой канавке, а другой — непосредственно под ней. Диаметр отверстий для отвода масла почти совпадает с высотой канавки для масляпого кольца. В поршнях карбюраторных двигателей поперечные прорези, отделяющие уплотняющий пояс, делают обычно в канавке масло-съемного кольца.
Отвод излишков масла необходим из-за насосного действия колец и перепада давлений при впуске , когда масло постепенно подается к камере сгорания, где оно сгорает и образует нагар на стенках камеры сгорания и на свече зажигания. Это происходит особенно интенсивно при изношенных поршневых кольцах.
Наличиемаслосъемногокольцаспособствуетэффективному отводу масла через специальные отверстия в картер. Перемычку между первым и вторым кольцами, как правило, делают более высокой. По мере удаления от днища высота перемычек уменьшается. Для повышения прочности перемычекпри той же высотеследует уменьшить их ширину и увеличитьрадиус сопряжения торцовых плоскостей с боковыми стенками канавок.
Направляющей частью (юбкой)называется часть поршня от нижней кромкиканавкипод последнее поршневое кольцо перед поршневым пальцем до концапоршня.Эта часть поршня служит ДЛЯ равномерного распределениябокового давления на зеркало цилиндра от силы iVjj, направленной по нормали к зеркалу цилиндра, а также для направления поршня при движении соосно цилиндру. В этой части поршня размещаются бобышки для поршневого пальца.
Длина направляющей части поршня и расположение оси бобышек по его длине влияют на — трение и износ поршня. Поскольку у различных двигателей боковая сила N% имеет различное значение, то и длина направляющей части поршня, зависящая от величины этой силы, различна. Чем больше сила iV2, тем длиннее должна быть направляющая часть поршня. В передаче боковой силы 7V2 от поршня к цилиндру участвует только часть боковой поверхности юбки, ограниченная в поперечном сечении дугой с центральным углом р = 80 ч — 100° . Поэтому в ряде конструкций для уменьшения массы поршня и потерь на трение части юбки, соответствующие углам у, удаляют (двигатели ГАЗ-21, МЗМА-408 и др.).
Выбор внешнего очертания направляющей части поршня в основном зависит от деформации зоны расположения бобышек. В результате неравномерности тепловых деформаций, прогибающего действия давления рг газов на поршень и силы Nxна его боковую поверхность сечениена-правляющеи части принимает овальную форму, что может вызвать заедание поршня. Для устранения деформации сошлифовывают часть поверхности поршня около поршневого пальца. Толщина снимаемого слоя может быть установлена только опытным путем. В ряде случаев направляющей части поршня при механической обработке придают овальную форму. Большая ось 1 овала должна быть перпендикулярна оси 2 поршневого пальца (рис. 194, г), а малая совпадать с направлением оси поршневого пальца. Разница в длине осей овала обычно составляет 0,1—0,3 мм. При холодном поршне обеспечивается ходовая посадка соответственно размерам большой оси овала. При работе двигателя вследствие тепловых деформаций поршень принимает цилиндрическую форму. Стенки юбки имеют постоянную по длине толщину, которая может несколько уменьшаться к низу поршня.
Для уменьшения передачи теплоты от головки поршня, изготовленного из легких сплавов, к его юбке иногда делают прорезь по окружности между головкой и юбкой.
Для устранения стуков и перекосов поршня в непрогретом двигателе и предупреждения заедания при работе поршни из легких сплавов выполняют с разрезными и овальными юбками. П — или Т-образная прорезь может быть сделана как по всей, так и не по всей длине Еобки с той стороны, где боковая сила N% меньше.
В некоторых автомобильных двигателях для уменьшения стуков ось поршневого пальца смещают относительно оси поршня в сторону более нагруженной поверхности поршня. Для уменьшения монтажных зазоров и обеспечения бесшумной работы поршневой группы поршни из легких сплавов иногда снабжают при литье специальными инварными1 или стальными вставками 1.
Инварные вставки заделывают в несущую часть поршня, имеющую наибольшую тенденцию к расширению в области бобышек. Такие поршрипринагреваниирасширяютсяменьше,чемчугунные.
У большинства современных зарубежных автомобильных двигателей поршень имеет юбку без разрезов с залитыми в ее стенку инварнымиилистальнымитерморегулирующимиэлементами.
При такой конструкции юбки повышается надежность поршня, увеличивается поверхность соприкосновения его с цилиндром и поршень можно устанавливать в цилиндр с минимальными зазорами, почти не изменяющимися на всех режимах работы двигателя.
Конструкции поршней новых отечественных карбюраторных двигателей характеризуются следующими особенностями: днище — плоское снаружи и гладкое (без ребер) внутри; юбка поршня без разрезов имеет кольцевую терморегулирующую вставку; в горизонтальной плоскости сечение юбки — овал, по высоте она имеет коническую или бочкообразную поверхность; тепловые прорези расположены в канавке маслосъемного кольца; каждая бобышка поршневого пальца связанас днищем поршня двумя ребрами.
Исследования поршней описанной выше конструкции показали возможность увеличения точности изготовления профиля юбки в 3—5 раз и повышения прочности поршней на 6—8%. На основании стендовых испытаний поршней, проведенных на двигателях ГАЗ-21 и ГАЗ-53, установлено, что контактная поверхность юбки поршня новой конструкции с гильзой в 1,4—2,2 раза больше контактной поверхности юбки поршня двигателя ГАЗ-53. Кроме того, температура головки нового поршня на 10—30° ниже температуры головки поршня двигателя ГАЗ-53. Эксплуатационные испытания двигателяпоказалихорошуюработоспособностьинадежность поршней новой конструкции.
maestria.ru
Поршень с цилиндром - Справочник химика 21
В сопряжении поршень—цилиндр различают два возможных зазора (по диаметру, на обе стороны) эксплуатационный А, создающийся при установившемся тепловом режиме работы компрессора и необходимый для размещения смазки, 70 [c.70]Для бескрейцкопфных одноступенчатых компрессоров в настоящее время в паре поршень—цилиндр (диаметр до 300 мм) применяются различные посадки 2-го класса точности, выдерживаемые при сборке и установке поршневой группы в цилиндр. [c.70]
Необходимо рассматривать зазоры между цилиндром и поршнем в плоскости качания шатуна и в плоскости оси поршневого пальца, так как при выборе зазора одни и те же факторы влияют различно в этих плоскостях. Так, например, температурные и силовые деформации поршня в этих плоскостях по-разному влияют на величину зазора в сопряжении поршень— цилиндр. В плоскости качания шатуна они увеличивают величину зазора, а в плоскости оси вращения коленчатого вала и оси поршневого пальца уменьшают ее. За счет зазора в сопряжении поршень—цилиндр в плоскости качания шатуна обеспечивается жидкостное трение поршня о зеркало цилиндра. [c.71]
Фиг. 20. Интенсивность износа цилиндра в зависимости от первоначальных зазоров в сопряжении поршень—цилиндр (п= = 1600 об/.чин, /ц = 120°С)-. ось абсцисс — зазор в юбке в мм ось ординат— износ за 1000 миль пробега автомобиля в дм. |
В механизме пара трения поршень-цилиндр. Прибор омывается внутри паром из котла. С наружной стороны сопла часть омывается горячими топочными газами. Механизм оборудован специальным отверстием для подвода смазки к трущимся поверхностям [c.155]
Нагар, находящийся на распылителях форсунок дизельных двигателей, способствует закоксовыванию отверстий распылителей, нарушению подачи и ухудшению распыливания топлива, обрыву сопла форсунки. Во всех типах поршневых ДВС твердые частички нагара, проникая в сопряжения поршень — цилиндр, вызывают ускоренный абразивный износ н приводят к загрязнению картерного масла. [c.40]
Так, например, у компрессоров 4АУ-15 и 2АВ-15 в сопряжениях поршень—цилиндр, изготовленных с минимальными зазорами, наблюдались задиры поршня и цилиндра, а также увеличивалась на 15—25% потребляемая мощность на единицу производительности. Пришлось изменить допуск на изготовление [c.70]
В настоящее время при выборе конструктивного зазора в сопряжении поршень—цилиндр поступают следующим образом. Учитывая, что при работе компрессора диаметр поршня увеличивается больше, чем диаметр цилиндра, вследствие различия рабочих температур поршня и цилиндра, зазоры между поршнем и зеркалом цилиндра при сборке специально увеличивают с таким расчетом, чтобы при работе компрессора на эксплуатационных режимах они уменьшились до нормальных. [c.71]
При этом в расчетах не учитывается ряд факторов, оказывающих влияние на выбор конструктивного зазора в сопряжении поршень—цилиндр, и не рассчитывается величина эксплуатационного зазора Д, что приводит к задирам поршня и зеркала цилиндра при минимально допустимых зазорах. [c.73]Зазоры в сопряжении поршень—цилиндр должны выбираться из условия обеспечения оптимальных показателей работы компрессора производительности, конечного давления сжатия, затрачиваемой мошности на единицу производительности, расхода масла на смазку в г/ч, расхода воды на охлаждение рубашек цилиндров, отнесенного к единице производительности и износостойкости деталей, т. е. к долговечности работы компрессора без капитального ремонта. [c.73]
При определении величин конструктивного зазора в сопряжении поршень—цилиндр следует учитывать увеличение удельного объема ( рост ) чугуна. [c.79]
Исходя из этого можно утверждать, что на величину зазора в сопряжении поршень—цилиндр влияют следующие факторы, изложенные ниже. [c.73]
Экспериментальные работы М. П. Новикова показали, что мощность двигателя внутреннего сгорания с увеличением зазора в сопряжении поршень—цилиндр вначале увеличивается, а затем резко падает (фиг. 24). [c.82]
Наблюдение за работой компрессоров 4АУ-15, АУ-200, 2АВ-15, 4АУ-8 и др. на холодильниках показало, что срок службы бескрейцкопфного компрессора определяется долговечностью работы сопряжения поршень—цилиндр. [c.74]
Средний годичный износ зеркала цилиндра компрессора (4500 ч работы) в верхнем сечении, где износ максимальный, равен 0,07—0,1 мм. Износ поршней по наружным диаметрам за этот же период был заметен только в верхних и нижних сечениях. Эти значения износа были получены на основании работ ВНИХИ и путем непосредственного измерения деталей компрессоров 4АУ-15, 2АВ-15 с диаметром зеркала цилиндра 150 мм и компрессора 2АВ-8 с диаметром цилиндра 80 мм. Следовательно, сопряжение поршень—цилиндр с минимальным конструктивным зазором прослужит при равных условиях примерно на год больше, чем сопряжение с максимальным конструктивным зазором, так как для принятых в практике посадок раз-74 [c.74]
Долговечность работы сопряжения поршень—цилиндр определяется максимально допустимым зазором (см. фиг. 18). [c.75]
Увеличение зазора в сопряжении поршень—цилиндр за счет износа деталей согласно инструкциям, по эксплуатации компрессоров [42] приближенно равно удвоенному максимальному конструктивному зазору (табл. 7), т. е. время эксплуатации сопряжения ограничивается 4—6 годами. Следовательно, наличие поля допуска зазора понижает срок службы сопряжения на 16—25 /о. [c.75]
Марка, диаметр цилиндра и ход поршня компрессора Линейное мертвое пространство Зазор в сопряжении поршень—цилиндр [c.75]
В целях повышения срока службы сопряжения поршень— цилиндр, зазор между ними и поля допусков на изготовление зеркала цилиндра Ш и на наружный диаметр поршня М следует устанавливать минимальными. [c.75]
При проектировании поршней компрессоров и определении зазора в сопряжении поршень—цилиндр принимается во внимание равномерное распределение по диаметру поршня теплового напряжения. Характер же влияния разностенности (в местах перехода к бобышкам) на тепловое расширение не учитывается. [c.76]
Научно-исследовательские работы, проведенные П. Н. Соловьевым [39] и М. И. Френкелем, показали, что в сопряжении поршень—цилиндр имеет место жидкостное трение. [c.81]
В сопряжении поршень—цилиндр имеет место жидкостное трение, поэтому необходимый минимальный эксплуатационный зазор может быть приближенно найден в соответствии с гидродинамической теорией смазки из следующих соображений. [c.82]Определение минимального зазора в сопряжении поршень—цилиндр [c.85]
ВЛИЯНИЕ ЗАЗОРА В СОПРЯЖЕНИИ ПОРШЕНЬ—ЦИЛИНДР НА ЭКСПЛУАТАЦИОННЫЕ ПОКАЗАТЕЛИ РАБОТЫ КОМПРЕССОРА [c.89]
Цель испытаний заключалась в том, чтобы экспериментально определить основные эксплуатационные показатели работы компрессора, влияющие на выбор зазора в сопряжении поршень—цилиндр работоспособность компрессора при минимальных зазорах в этом сопряжении, рассчитанных по формуле (92) величины уменьшения зеркала цилиндра и наружного диаметра поршня за счет увеличения удельного объема чугуна максимально допустимый зазор износа в сопряжении поршень— цилиндр- для регламентации величины поля допуска зазора ремонтные размеры наружных диаметров поршней и поршневых колец. [c.89]
Первый этап испытаний был проведен с зазором в сопряжении поршень—цилиндр, равным 0,095 мм. Поршни подбирались так, чтобы обеспечить расчетный зазор, определенный по формуле (89). Минимальный допустимый зазор в сопряжении поршень—цилиндр 0,093 мм. [c.94]
Основные результаты исследований представлены в виде графиков на фиг. 32—36. Расходы воды на охлаждение рубашек блока цилиндров с возрастанием зазора в сопряжении поршень-цилиндр для одних и тех же оборотов коленчатого вала и одного и того же перепада температур оставался постоянным. [c.96]
Расход смазки возрастал пропорционально росту зазора (до 0,7 мм) в сопряжении поршень—цилиндр. Далее из-за больших протечек газа увеличение его замедлилось и при зазоре , мм несколько упало (фиг. 35). [c.96]
Изменение индикаторной диаграммы в зависимости от величины зазора в сопряжении поршень—цилиндр показано на фиг. 36. Изменение индикаторной диаграммы говорит о наличии пропусков газа с увеличением этого зазора. [c.96]
Испытания были прекращены при зазоре в сопряжении поршень—цилиндр, равном 1,3 мм. [c.96]
Исследования показали, что с увеличением зазора в сопряжении поршень—цилиндр производительность компрессоров падает в зависимости от скорости перемещения поршня резко увеличивается расход смазки компрессоров уменьшается индикаторная мощность и сокращается срок их службы. Затрачиваемая на работу компрессора мощность с увеличением зазора в данном сопряжении оставалась постоянной. [c.99]При выборе минимального зазора в сопряжении поршень—цилиндр доминирующим эксплуатационным показателем является долговечность работы сопряжения. [c.99]
Величины допустимого максимального износа, регламентируемые инструкциями по эксплуатации компрессоров, а значит и срок службы сопряжения поршень—цилиндр могут быть увеличены без значительного ухудшения эксплуатационных показателей работы компрессора. [c.99]
Величина допустимого максимального зазора в сопряжении поршень—цилиндр должна регламентироваться в зависимости от предъявляемых эксплуатационных требований к поршневой машине, допустимого уменьшения производительности, долговечности и увеличения расхода смазки. [c.99]
ТОГО вала поршень цилиндра Б начнет движение влево, его правая Topof а через клапан 2 будет всасывать, а левая через клапан 4 нагнетать жидкость, поршень цилиндра А продолжит движение вправо и левой стороной через клапан 1 продолжит всасыиание, а правой через клапаи 3 нагнетание жидкости. Прн крайнем правом положении поршня цилиндра А в нем нет ни всасывания, ни нагнетания. В этот мо.мент поршень цилиндра Б займет среднее положение и одной стороной будет всасывать, а другой нагнетать жидкость. [c.95]
По мнению зарубежных специалистов [57, 58], специфический фракционный состав синтетического арктического моторного масла предопределяет его работоспособность в теплонапряженных дизелях в зоне поршень—цилиндр при этом расход синтетического масла на 13—36% меньше, чем масла по спецификации MIL-L-10295В, а расход масла SAE 30 (MIL-L-2104B) в условиях длительного пробега автомобилей ( 50 000 км) был лишь на 5% ниже, чем синтетического арктического моторного масла. [c.40]
Рядом спаренные цилиндры, сообщающиеся между собой в полости головки (рис. 16). Движение поршней происходит со сдвигом по фазе поршень цилиндра II несколько отстает от поршня цилиндра I (22—ЗО" полного оборота коленчатого вала). Цилиндр I заполняется обогащенной бензовоздушной смесью, а цилиндр II — чистым воздухом. [c.60]
Для сопряжения поршень—цилиндр (см. фиг. 18), в котором действительный размер диаметра цилиндра—минимально допустимый Dmin И дизметр поршня—максимально допустимый max, срок эксплузтации будет наибольшим, так как толщина изнашиваемого слоя равна сумме величин SD , bd , ID и bd. Если действительные размеры деталей будут равны и drain, ТО изнашиваемый слой металла равен [c.74]
Коэффициент подачи (фиг. 32) и удельная холодопроиз-водительность компрессора Ке (фиг. 33) с увеличением зазора в сопряжении поршень—цилиндр уменьшались, но и Л .. (фиг. 34) даже при условии обеспечения лучшей смазки из-за увеличенных зазоров оставались посгоянными. Следовательно, часть мощности электродвигателя затрачивалась на ударное вэздейсгвие поршней о зеркало цилиндра. [c.96]
chem21.info
Устройство и ремонт мотоциклов.
Очистка от нагара.
Камеры сгорания цилиндров чаще требуется очищать от нагара у двухтактных двигателей, чем у четырехтактных, причем тем чаще, чем меньше рабочий объем цилиндра. У двухтактных двигателей, имеющих рабочий объем 125 см3, нагар следует очищать после 2000 км пробега мотоцикла, а у двигателей, рабочий объем которых равен 350 см3, — после 4000 км. В четырехтактных двигателях очистку от нагара производят после 5000—6000 км пробега, а при малом расходе масла и применении бензина А-74 этот срок увеличивается вдвое.
Канавки для поршневых колец очищают при замене их. Специально очищать канавки требуется только в случае уменьшения компрессии вследствие недостаточной подвижности колец.
Глушители двухтактного двигателя чистят по мере надобности, примерно после 4000—8000 км пробега мотоцикла (больший пробег относится к двигателям с большим рабочим объемом цилиндра). У четырехтактного двигателя необходимость очистки глушителя наступает не ранее чем после 10 000 км пробега мотоцикла.
Удаляемый нагар желательно предварительно размягчить, смочив его растворителями. Для этого, например, на головку поршня кладут на некоторое время тряпку, намоченную в керосине с растворителем (ацетоном). После этого нагар можно легко удалить. Сухой нагар соскабливают ножом, шабером или любым другим скребком.
Нагар в канавках удобно снимать специальным приспособлением (рис. 31) или обломком поршневого кольца. При соскабливании нельзя повреждать адюминиевые детали, в особенности боковые стенки канавок поршня. К концу очистки для ускорения работы можно использовать щетку из медной проволоки.
Нагар в двигателях, работавших на этилированном бензине, содержит ядовитые отложения свинца. При удалении нагара необходимо соблюдать меры предосторожности. Очищаемые детали предварительно следует выдержать в керосине; эту работу нельзя производить в жилом помещении.
Для удаления нагара из двигателя снимают головку цилиндра и выпускную трубу. При отделении головки от цилиндра надо следить за тем, чтобы не была повреждена прокладка. На ней ставят метку для установки при сборке в прежнее положение. Гайку, крепящую выпускную трубу к патрубку цилиндра или головки, следует отвертывать не ударами, а ключом для круглых гаек; при этом нужно следить за тем, чтобы не была повреждена прокладка, находящаяся между трубой и патрубком.
Перед очисткой головки поршня он должен быть установлен в в. м. т.
У двухтактных двигателей очищенный поршень устанавливают в н. м. т., закрывают тряпкой продувочные окна и очищают нагар в выпускных окнах
Очищенные от нагара детали и крепящие их болты и гайки промывают керосином и вытирают чистой тряпкой. Перед установкой головки на цилиндр осматривают соединяемые поверхности и прокладку. Обнаруженные неровности осторожно спиливают бархатным напильником, а прокладку, имеющую разрывы, заменяют новой. При отсутствии прокладки заводского изготовления ее вырубают вручную из армированного асбестового полотна. Сначала в прокладке делают малые отверстия, потом — большое, после чего обрезают по контуру. Можно также вырубить прокладку из листовой красной меди или алюминия толщиной 0,3—1 мм. Медную прокладку перед установкой нужно нагреть докрасна и быстро опустить в воду для того, чтобы она была мягкой.
Устанавливая головку, вначале слегка завертывают две гайки (или два болта), расположенные по диагонали; потом также попарно завертывают противолежащие гайки, затем, начиная с первой пары, окончательно затягивают гайки, постепенно увеличивая усилие, прилагаемое к ключу. При таком порядке затяжки гаек или болтов головки прокладка зажимается равномерно. Попытки чрезмерно тугим завертыванием достигнуть герметичности при испорченной прокладке приводят к повреждению резьбы или обрыву болтов. После нескольких часов работы двигателя, дав ему остыть, подтягивают на холодном двигателе ослабевшие болты и гайки головки.
Для очистки от нагара канавок поршня снимают цилиндр, стремясь не повредить прокладки под ним. Новую прокладку вырубают из любой плотной той же толщины бумаги и пропитывают олифой или маслом. Если в верхней части цилиндра имелась ступенька вследствие износа его зеркала, то при установке прокладки из более тонкой бумаги во время работы двигателя будет слышен стук. При глубоких повреждениях на соединяемых плоскостях цилиндра и картера прокладку надо смазать бакелитовым или шеллачным лаком или нитрокраской.
Для защиты от поломки юбки поршня при случайном ударе о шатун, когда цилиндр снят, под поршень устанавливают деревянный брусок 1 с прорезью (рис. 32, а) или внутрь поршня втискивают свернутую чистую тряпку 2 (рис. 32, б). Для предохранения картера от попадания посторонних предметов его прикрывают фартуком, завязанным веревкой вокруг шатуна.
Кольца вынимают из канавок и устанавливают в канавки поршня обязательно с помощью трех-четырех стальных пластинок (рис. 33). Две пластинки просовывают под концы кольца в стыке, а с помощью других выводят кольцо из канавки. Мотоциклисты часто не пользуются стальными пластинками и считают, что если кольцо не сломалось, то операция выполнена правильно. Но при снятии и надевании кольца без пластинок неизбежна его деформация, вследствие чего нарушаются точность формы кольца, его приработка и равномерность давления на стенки цилиндра. При снятии колец отмечают их размещение по канавкам и при сборке устанавливают на прежние места. При этом необходимо убедиться в том, что все углы канавок поршня очищены от нагара; особенно тщательно надо очищать канавки около стопоров (у двухтактного двигателя). Замки колец у двухтактных двигателей располагают точно на стопорах. У четырехтактных двигателей замки колец размещают в канавках в шахматном порядке. Желательно, чтобы замки были обращены к боковым и передней стенкам цилиндра, которые менее нагружены (рис. 34). У двигателей типа М-62 менее нагруженная стенка в правом цилиндре — верхняя, а в левом — нижняя. Перед установкой цилиндра поршень с кольцами слегка смазывают маслом.
При надевании цилиндра на поршень применяют для сжатия колец хомут из жести (рис. 35, а) или массивное кольцо с конусным отверстием и вырезанным участком для прохода шатуна (рис. 35, б).
Последнее приспособление более удобно, так как при его использовании можно следить за расположением стыков колец в сомкнутом состоянии, что особенно важно при сборке двухтактного двигателя. Однако цилиндр можно надевать на поршень, сжимая кольцо, например, поясным ремнем или придерживая концы кольца отверткой. При сжатии кольца следят за тем, чтобы замок сомкнулся, и слегка нажимают на цилиндр. При сильном нажатии на цилиндр кольца ломаются. Застревание цилиндра на кольце соответствующего диаметра у двухтактных двигателей свидетельствует о неточном совпадении замка кольца со стопором в канавке поршня. Во время установки цилиндра отверстия в его фланце должны находиться против соответствующих шпилек картера. При повертывании цилиндра вокруг продольной оси в четырехтактном двигателе нарушается правильное расположение замков колец, а в двухтактном двигателе могут сломаться кольца в результате попадания их концов в окна цилиндра. Гайки крепления цилиндра завертывают так же, как и гайки головки, о чем было указано выше.
Замена поршневых колец.
Примерный срок службы поршневых колец в четырехтактных двигателях соответствует 10 000 — 15 000 км пробега мотоцикла. У двухтактных двигателей этот срок значительно меньше (4000—8000 км). Меньшие цифры относятся к двигателям, имеющим меньший объем цилиндра. При применении высококачественных масла и бензина и установке фильтра тонкой очистки и эффективного воздушного фильтра можно значительно увеличить срок службы поршневых колец. Компрессионные поршневые кольца заменяют в случае уменьшения компрессии, а масло-съемные — при увеличении расхода масла, если установлено, что они неисправны.
Признаками износа поршневого кольца, при котором его необходимо заменить, являются увеличение зазора в замке (больше 3 мм), потемнение отдельных участков рабочей поверхности и значительное уменьшение его упругости. Замена колец при увеличении зазора в пределах 1 мм мало целесообразна. У маслосъемных колец дополнительным признаком необходимости замены их является износ рабочих кромок.
Для определения износа кольцо вставляют в цилиндр. Затем положение кольца выравнивают, вводя поршень. Зазор в замке кольца измеряют щупом 3 (см. рис. 24)..
Перед установкой нового кольца следует проверить зазор в замке, соответствие высоты кольца ширине канавки и толщины кольца глубине канавки, а также прилегание кольца к зеркалу цилиндра. Ориентировочно зазор в замке должен быть равен 0,2— 0,3 мм или примерно 0,1 мм на каждые 25 мм диаметра цилиндра. У верхнего кольца зазор в замке должен быть несколько больше, чем у нижних колец, так как при работе двигателя оно нагревается сильнее. Если зазор мал или отсутствует, то спиливают торцы кольца в стыке зазора (рис. 36, а). При недостаточном зазоре кольцо, расширившееся во время работы двигателя, вызовет заклинивание поршня в цилиндре. Для работы в цилиндре, имеющем допустимый износ, кольца в стыке необходимо спилить так, чтобы нормальный зазор в замке получался у середины цилиндра и был меньше у нижней, менее изношенной части зеркала.
Для проверки соответствия высоты кольца ширине канавки кольцо вставляют наружной стороной в канавку. Кольцо должно под действием своего веса плотно входить в канавку и свободно в ней перекатываться. Зазор между кольцом 2 и боковой стенкой канавки поршня 1 при измерении щупами (рис. 36, 6) составляет примерно 0,02—0,06 мм у четырехтактных двигателей и 0,05 — 0,1 мм у некоторых двухтактных двигателей. При тугой посадке кольцо будет недостаточно подвижно, пригорит и заклинится в канавке. При увеличении зазора во время работы двигателя кольцо будет перемещаться между боковыми стенками и угар масла увеличится, а боковые стенки канавки и торцы кольца быстро износятся; возможна даже поломка кольца. Поэтому если между кольцом и боковой стенкой канавки зазор будет очень большим, то такое кольцо не пригодно для использования.
Толщину кольца можно уменьшить до нужного размера, шлифуя его торцы мелкой наждачной шкуркой, положенной на ровную поверхность.
Соответствие толщины кольца глубине канавки проверяют следующим способом. Кольцо 2 наружной стороной вставляют в канавку поршня 1 и к поршню, параллельно его продольной оси, прикладывают ребром линейку 3, как показано на рис. 36, в. Кольцо должно утапливаться в канавке на 0,5—0,65 мм и свободно перемещаться в радиальном направлении между дном канавки и линейкой. Если перемещение кольца отсутствует, то при расширении поршня и образовании под кольцом нагара кольцо наружной поверхностью сильно будет давить на зеркало, и поршень заклинится в цилиндре. Поэтому необходимо подбирать кольцо с меньшей радиальной толщиной или, в крайнем случае, спилить кольцо изнутри.
Для проверки прилегания кольца к зеркалу цилиндра кольцо вставляют в цилиндр и смотрят, нет ли просвета между кольцом и зеркалом. При больших просветах кольцо бракуют.
У двухтактных двигателей перед установкой колец дополнительно проверяют сопряжение выемки в замке кольца со стопором в канавке поршня. В некоторых случаях приходится ставить кольца несколько большего размера. У таких колец следует спиливать торцы в замке до получения нужного зазора. Кольцо со спиленными торцами будет удовлетворительно работать, если его диаметр до спиливания торцов в замке превышал диаметр цилиндра не более чем на 1—1,5 мм. При большем первоначальном несоответствии диаметров кольцо, установленное в цилиндр, приобретает форму овала (рис. 36, г) и не будет плотно прилегать к зеркалу. Опиливание торцов колец дает худший результат при установке их в цилиндрах малого диаметра. Лучше поставить приработанное кольцо с увеличенным зазором в стыке, чем кольцо, плохо прилегающее к зеркалу цилиндра.
При установке приработанного кольца с увеличенным зазором в стыке меньше проходит газов в камеру сгорания через зазоры между поршнем и цилиндром. В случае установки кольца, плохо прилегающего к зеркалу цилиндра, возрастает температура поршня, вследствие малой площади контакта кольца с зеркалом цилиндра.
Замена поршня.
Срок службы поршня соответствует примерно времени износа на нем двух комплектов поршневых колец. У поршня изнашиваются канавки для колец, отверстие под палец и юбка. Пределом износа поршня можно считать образование между нижней частью юбки и зеркалом цилиндра зазора, составляющего 0,005 диаметра цилиндра, что при диаметре цилиндров 50, 60, 70 и 80 мм соответствует 0,25; 0,30; 0,35 и 0,4 мм. Зазор измеряют у нижнего края передней или задней стороны юбки при расположении поршня в нижней части цилиндра.
У четырехтактного двигателя диаметр нового поршня внизу юбки (по которому подбирают поршень к цилиндру), измеряемый на расстоянии 5—10 мм от ее края, меньше диаметра цилиндра примерно на 0,05—0,1 мм (см. рис. 24). Большие зазоры относятся к цилиндрам с большим диаметром. У двигателей мотоциклов М-61 и К-750 и других двигателей, имеющих такой же диаметр цилиндра, зазор составляет 0,08—0,1 мм. Диаметр юбкя поршня этих двигателей выбит на днище поршня.
У двухтактных двигателей при подборе поршня зазор измеряют или внизу юбки, или в IV поясе, под нижним поршневым кольцом. Например, у двигателей мотоциклов М-104, К-58, Ява и у других двигателей с небольшим диаметром цилиндра поршень обычно подбирают к цилиндру с зазором внизу юбки не менее 0,06—0,07 мм. Зазор между цилиндром и поршнем у мотоцикла «Ковровец-175А» измеряют на расстоянии 20 мм от нижнего края поршня. Этот зазор равен 0,06—0,08 мм для алюминиевого цилиндра с гильзами и 0,04—0,06 или — для чугунного цилиндра. При установке поршня от алюминиевого цилиндра в чугунный может произойти заклинивание поршня. При использовании поршня чугунного цилиндра в алюминиевом зазор между поршнем и цилиндром будет несколько увеличенным, что несущественно отразится на работе двигателя. При измерении зазора между поршнем и цилиндром под нижним кольцом зазор должен быть в пределах 0,13—0,15 мм. Поршни мотоцикла «Ковровец- 175А» разделены на размерные группы, обозначенные цифрами 0; 1 и 2. Цифра 0 соответствует большему диаметру, а цифра 2 — меньшему.
У двигателя мотоциклов ИЖ-56 и ИЖ «Планета» зазор между поршнем и цилиндром одинаковых размерных групп в поясе под нижним кольцом на высоте 55 мм от нижнего края юбки равен 0,06 мм. В этом случае между разрезной юбкой поршня и цилиндром нет зазора. Поршни и цилиндры двигателя маркируют цифрами 1; 0 и 00. Цифра 1 соответствует меньшему диаметру, а цифры 00 — большему. Размерная группа указана на фланце цилиндра и на головке поршня.
У двигателя мотоцикла ИЖ «Юпитер» зазор между поршнем и цилиндром одинаковых размерных групп в поясе под нижним кольцом, измеренный на расстоянии 58 мм от нижнего края юбки, равен 0,15 мм, а внизу юбки 0,4 мм. У двигателя мотоцикла «Панония» зазор между цилиндром и поршнем внизу поршня составляет 0,8 мм, над первым кольцом 0,32 мм, над третьим кольцом 0,14 мм.
Поршни и цилиндры двигателей мотороллеров, подбираемые с соблюдением тех же правил, разделены на размерные группы, обозначенные цифрами 0; 1 и 2. Цифра 0 соответствует большему диаметру, а цифра 2 — меньшему. Например, у двигателя мотороллера ВП-150 цилиндр с обозначением 0. имеет диаметр 57,02—57,01 мм, а поршень с таким же обозначением — диаметр 56,92 мм, т. е. между поршнем и цилиндром имеется зазор 0,1 мм. У двигателя мотороллера Т-200 цилиндр с обозначением 0 имеет диаметр 62, 02—62, 01 мм, а поршень с таким же обозначением — диаметр 61,96—61,95 мм; таким образом, зазор между цилиндром и поршнем составляет 0,6 мм.
Указанные выше зазоры, устанавливаемые заводом, нужно стремиться выдержать и при ремонте. Однако, если трудно точно подобрать поршень к цилиндру, то допускается увеличивать или уменьшать установленный зазор на 0,01— 0,03 мм, в особенности при комплектовании двигателя с допустимым износом цилиндра. Важно только при меньшем зазоре во время обкатки двигателя строго придерживаться всех правил обкатки, чтобы не допустить заклинивания поршня в цилиндре.
При износе юбки во время работы двигателя слышен стук поршня о стенки цилиндра, увеличивается расход масла и ухудшается компрессия вследствие плохого прилегания колец к зеркалу цилиндра. В двухтактных двигателях, кроме того, неплотно закрываются газораспределительные окна и уменьшается компрессия в картере, из-за чего резко ухудшается продувка, затрудняется пуск двигателя и снижается его мощность. Срок службы изношенного поршня путем установки новых колец можно продлить только на короткое время, так как в этом случае износ колец происходит быстрее.
Перед установкой поршня, осматривая его боковую поверхность, проверяют, не работал ли поршень в цилиндре с перекосом (рис.37). Эта неисправность часто является следствием перекоса втулки поршневого пальца, неумело обработанной разверткой, или искривления шатуна. Шатун искривляется при неосторожной выпрессовке и запрессовке поршневого пальца, а также в том случае, если двигатель переносят с места на место, держа за шатун.
При установке поршня нужно соблюдать определенные правила. У четырехтактных двигателей поршни с разрезной юбкой (при отсутствии указаний завода-изготовителя) устанавливают разрезом к передней менее нагруженной стенке цилиндра. У двухтактных двигателей на головке поршня имеются стрелка и надписи, указывающие расположение поршня в цилиндре. При установке поршня на двигатель мотоцикла ИЖ «Планета» стрелка, выбитая на головке поршня, должна быть направлена вперед, а при установке поршня на двигатель мотоцикла ИЖ «Юпитер» — назад. В случае несоблюдения этих указаний возможны западание концов поршневых колец в окна цилиндра и поломка колец при движении поршня (см. рис. 23).
Замена поршневого пальца и его втулки.
При нормальном износе двигателя ослабление посадки поршневого пальца в бобышках поршня и образование зазора между пальцем и втулкой в шатуне происходят одновременно с износом поршня. Поэтому желательно поршень, палец и втулку заменять одновременно. Однако если новый палец в старой втулке можно установить достаточно плотно, то втулку не меняют. На поршневых пальцах и бобышках поршня завод ставит цветные метки. При комплектовке палец и поршень должны иметь метки одинакового цвета.
При замене втулки 2 (рис. 38) верхней головки шатуна 1 ее выпрессовывают и запрессовывают или в тисках 5 с помощью оправки 3 и отрезка трубы 4 (рис. 38, а) или посредством вспомогательного болта 6 с гайкой и шайбой 7 (рис. 38, б). При подгонке пальца ко втулке надо учесть следующее.
Вследствие нагревания поршня при работе двигателя посадка пальца в бобышках ослабевает. Поэтому палец следует устанавливать более плотно в бобышках поршня и менее плотно — во втулке шатуна. Если этого не удается добиться подбором пальца, то втулку слегка развертывают раздвижной разверткой. При использовании простой развертки для точной подгонки можно на ее грани на V3 окружности наложить полоску тонкой бумаги. Развертка прорежет бумагу, но все же снимет во втулке небольшую стружку. Поршневой палец, смазанный маслом, должен легко вдвигаться во втулку шатуна при слабом нажиме большого пальца. Более тугая посадка или покачивание пальца во втулке недопустимы. В бобышки поршня палец должен вдвигаться с усилием. Желательно установить палец с натягом 0—0,002 мм. В этом случае палец, нагретый до температуры 20° С, можно вдвинуть в обе бобышки поршня сильным нажатием пальца руки. При такой посадке поршневой палец перемещается в осевом направлении, но не вращается. Если нагретый до указанной температуры палец можно вдвинуть в бобышки, только смазав маслом (или в крайнем случае при нагревании поршня до температуры 40° С), то натяг равен примерно 0,004 мм. При повторной выпрессовке и запрессовке сухого пальца нарушается точность подгонки его к поршню.
Туго сидящий в поршне палец лучше выпрессовывать посредством хомута с винтом (рис. 39). При выполнении этой операции с помощью молотка и оправки 1 поршень надежно подпирают массивным деревянным бруском 3. Для облегчения установки пальца поршень предварительно нагревают в кипящей воде. Отверстия в бобышках поршня 5 и во втулке шатуна 4 совмещают, продевая в них оправку 6. Вторым концом оправку вставляют внутрь поршневого пальца. В нагретый поршень палец входит легко только до тех пор, пока он не нагреется; поэтому слегка смазанный маслом палец вталкивают в поршень возможно быстрее.
Замена кривошипа.
Неразборный кривошип при обнаружении износа подшипника шатуна (см. раздел «Определение износа деталей, расположенных в картере») желательно заменить новым кривошипом. Однако при наличии необходимых запасных частей, токарного станка, индикатора и пресса изношенный подшипник шатуна можно восстановить, не обращаясь к услугам мастерской. Эту работу может выполнить квалифицированный механик; поэтому ниже приводятся рекомендации только относительно некоторых важнейших особенностей ремонта кривошипа.
В случае износа кривошипа, при работе которого слышен стук, не следует эксплуатировать мотоцикл. На поверхностях кривошипного пальца и шатуна при этом образуются повреждения от наклепа и выкрашивания, которые не удается устранить шлифованием. Ролики также нельзя больше использовать.
Кривошип можно распрессовать небольшим прессом или специальным съемником. На рис. 40 показан съемник, изготовленный на токарном станке и предназначенный для разборки кривошипов двигателей М-61 и ему подобных. Съемник надевают на съемочные выступы наружной щеки кривошипа так, чтобы винт (диаметром 27 мм, шаг резьбы 3 мм) упирался в кривошипный палец. Съемник закрепляют в больших тисках или приваривают к стальной балке. Под винт съемника надо подложить шайбу и густо смазать ее и резьбу универсальной среднеплавкой смазкой (солидолом). При завинчивании винта съемника надо пользоваться длинным воротком. Для выпрессовки кривошипа двухтактного двигателя можно обойтись без подобного съемника и пользоваться прессом.
При сборке коленчатого вала двигателя типа М-61 на прессе можно прежде запрессовать кривошипные пальцы цилиндрическими концами в среднюю щеку и затем напрессовать на конусные концы крайние щеки, обеспечивая осевое перемещение шатуна между щеками в пределах 0,04—0,14 мм. Центрирование коленчатого вала производят в центрах токарного станка с помощью индикатора. Биение коренных шеек на длине 20 мм не должно превышать 0,05 мм.
Если шейки параллельны, но не соосны, то их положение выравнивают ударами алюминиевого молотка по щекам (рис. 41, б), а если расположены под углом, то сжимают в тисках (рис. 41, а).
У кривошипа одноцилиндрового двухтактного двигателя М-103 и ИЖ «Юпитер» биение шеек на длине 20 мм не должно превышать 0,02 мм, у двигателей ИЖ 56, ЙЖ «Планета» — не более 0,03 мм.
При установке новых шатуна, пальца и роликов необходимо, чтобы радиальный зазор в подшипнике шатуна двигателя мотоцикла М-61 был равен 0,01—0,02 мм (причем шатуны с подшипником правого и левого цилиндров должны иметь одинаковую массу), двигателей мотоциклов М-103 — не более 0,012 мм и двигателей мотоциклов ИЖ-56, ИЖ «Планета», ИЖ «Юпитер» — не более 0,016 мм. При незначительном увеличении радиального зазора срок службы роликоподшипника шатуна немного уменьшится; в результате сборки без зазора роликоподшипник может разрушиться в течение первых часов работы двигателя. Кроме того, следует обеспечить правильный осевой зазор роликов подшипника. В противном случав ролики будут притормаживаться с торца и скользить (а не катиться), вследствие чего на них образуются лыски и подшипник выйдет из строя.
Диаметры роликов не должны отличаться один от другого более чем на 0,002 мм. Так точно измерить диаметр роликов вне заводских условий нелегко. Поэтому надо проверить размеры роликов в комплекте микрометром, чтобы не допустить большого отклонения в размере отдельных роликов. Даже при наличии в комплекте одного ролика, диаметр которого значительно больше диаметра остальных роликов, подшипник при работе выйдет из строя. Следует обращать внимание на качество шлифования новых роликов и на формы роликов, бывших в употреблении, на наличие и полировку закругления перехода цилиндрической части в торец.
В случае отсутствия запасных частей умеренно изношенные кривошипный палец и отверстие в шатуне иногда восстанавливают шлифованием на станке или с помощью притира и устанавливают ролики увеличенного диаметра. При отсутствии запасной сменной втулки нижней головки шатуна, например у двигателей типа М-72, можно расточить головку (лучше отшлифовать) шатуна и установить в нее кольцо толщиной 2,5—3 мм, сделанное из стали 12ХНЗА и подвергнутое цементации и закалке. Кроме того, можно использовать внутреннее кольцо шарикоподшипника (сталь- ШХ15) соответствующего внутреннего диаметра (50 мм), отшлифовав его снаружи под размер шатуна. При запрессовке кольцо охлаждают сухим льдом, а шатун подогревают.
Замена, растачивание цилиндра и установка в него гильз.
Цилиндр заменяют новым; растачивают под поршень увеличенного размера или вставляют в него гильзу, если износ верхней части зеркала составляет примерно 0,15— 0,2 мм, а также при образовании на нем задиров и рисок. Вследствие износа зеркала цилиндр становится конусным (вверху шире, внизу уже) и овальным (вытянутым по оси, обычно перпендикулярной к поршневому пальцу). Увеличенный износ верхней части цилиндра — следствие высокой температуры и недостаточной смазки этой части цилиндра. Овальность получается в результате большего. воздействия поршня на переднюю и заднюю стенки. Образование овальности вызывается также смыванием смазки с зеркала потоком смеси из карбюратора, деформацией и местными перегревами цилиндра.
Износ цилиндра определяют, измеряя его с помощью нутромера с индикатором. Приближенно конусность цилиндра можно определить с помощью поршневого кольца и щупов, измеряя зазор в замке кольца, которое последовательно устанавливают в верхнем неработающем поясе цилиндра, ниже, в месте наибольшего износа, в средней и нижней частях цилиндра.
Нормальную компрессию нельзя восстановить путем установки в изношенный цилиндр нового поршня и колец, так как поршень и кольца не могут хорошо приработаться к зеркалу овального сечения. В особенности плохо прирабатываются хромированные кольца. Их не следует ставить в изношенный цилиндр. Изношенный цилиндр растачивают и шлифуют до размера, соответствующего ремонтному размеру поршня. Для таких цилиндров заводы выпускают поршни ремонтных размеров.
При правильной установке гильзы в изношенный цилиндр износостойкость зеркала повышается. Например, для цилиндров диаметром около 78 мм можно использовать гильзы из специального чугуна от двигателя автомобиля «Москвич-407; отличающиеся высокой износостойкостью (необходимость шлифования их возникает примерно через 100000 км пробега). Для облегчения установки гильзу следует охладить искусственным льдом, а цилиндр нагреть в кипящей, воде. Чтобы установить гильзу из чугуна СЧ 24- 44 в цилиндр, изготовленный из алюминиевого сплава АЛ108 (двигатель мотоциклов «Ковровец-175А» и др.), его нагревают до 220—250° С, а затем запрессовывают гильзу с натягом 0,08—0,2 мм. При установке гильзы в цилиндр необходимо учесть следующее. Проникновение масла между гильзой и цилиндром резко ухудшает охлаждение. В случае установки даже с зазором гильза не будет перегреваться, так как она при нагревании расширяется, вследствие чего зазор устраняется кроме того, при этом лучше сохраняется цилиндрическая форма гильзы.
bike78.narod.ru
Замена поршня в двигателе мотоцикла - Мои статьи - Каталог статей
Срок службы поршня соответствует примерно времени износа на нем двух комплектов поршневых колец. У поршня изнашиваются боковые стенки канавок для колец, отверстие под палец и юбка. Первоначальную прямоугольную форму изношенных канавок восстанавливают протачиванием на токарном с гайке и ставят в них более высокие поршневые кольца. Для устранения овальности, образующейся при износе, отверстие в бобышках обрабатывают разверткой под размер пальца увеличенного диаметра. Поршень с сильно износившейся юбкой, как правило, бракуют и заменяют новым.
Пределом изношенности поршня можно считать образование между нижней частью юбки и зеркалом зазора около 0,5% от диаметра цилиндра, что составляет при диаметре цилиндров 50, 70 и 80 мм соответственно 0,25; 0,35 и 0,4 мм. Величину зазора измеряют внизу поршня, отступив на 5—10 мм от нижнего края передней или задней стороны юбки при расположении поршня в нижней, менее изношенной части цилиндра.
Диаметр нового поршня в его верхней части (участок поршневых колец) должен быть меньше его диаметра в нижней части юбки. Поршень расширяется от донышка к юбке конусом или ступенчато. Например, при диаметре цилиндра 52, 72 или 78 мм поршень должен быть меньше в верхнем и следующем за ним пояске между кольцами соответственно на 0,17 мм, на 0,25 и 0,19 м и на 0,6 и 0,55 мм.
Диаметр нового поршня внизу юбки, по которому производят подбор поршня к цилиндру (правильный диаметр поршня на участке поршневых колец обеспечивается заводом-изготовителем),. должен быть меньше диаметра цилиндра примерно на 0,05—0,1 мм. Большие зазоры относятся к цилиндрам с большими диаметрами.-
При использовании поршней из сплавов, тепловое расширение которых неизвестно, величину необходимого зазора между цилиндром и поршнем уточняют следующим образом: цилиндр и поршень нагревают примерно до 150°, в этих условиях поршень должен опускаться в цилиндр под влиянием своего веса.
В виде примера верного подбора поршня к цилиндру приводим данные по двигателям более, как большая часть из нас постоянно говорит, популярных мотоциклов. Отмеченные ниже зазоры наконец-то соблюдаются при приготовлении двигателя на заводе. К ним необходимо устремляться и при починке. Надо сказать то, что впрочем невозможно также считать целесообразным прекращать применение мотоцикла в связи затруднений в точном подборе поршня к цилиндру. Всем известно о том, что повышение или же сокращение промежутка напротив общепризнанных мерок на 0,01—0,03 мм позволительно, в особенности если комплектуют двигатель, в прошлом в эксплуатации. Важно только принимать во внимание, собственно при меньшем зазоре, наконец, следует проявить своеобразную предосторожность в период обкатки двигателя в последствии починки, дабы не разрешить вероятного заклинивания поршня в цилиндре. У двигателя мотоциклов Ml А и К-125 поршень, наконец, ставят в цилиндре с зазором 0,065—0,085 мм, измеряемым, будто было произнесено, щупом у нижнего, как мы с вами постоянно говорим, края юбки. На днище поршня выбит номер, как многие выражаются, одной из размерных групп: 0; 1 или же 2. Поршни соседних размерных групп выделяются 1 от иного диаметром юбки на 0,01 мм. Как бы это было не странно, но эти же номера выбиты на верхнем торце цилиндра. Все давно знают то, что разница в диаметре цилиндров 2, как мы с вами постоянно говорим, соседних размерных групп тоже 0,01 мм. Поршень и цилиндр так сказать выбирают с одним и тем же номером размерной группы.
На бобышках поршня имеются цветные метки — белая, черная или красная — для подбора поршневых пальцев, также имеющих на торце цветные метки. При комплектовке поршень и палец подбирают с одинаковыми цветными метками, учитывая изложенные ниже указания о подборе поршневого пальца.
Кроме номинального размера, заводы выпускают поршни первого и второго ремонтных размеров, с соответствующим обозначением на днище. Например, у поршней двигателя мотоцикла М1А: буквы БР означают первый ремонтный размер, буквы ВР — второй ремонтный размер. Поршни первого и второго ремонтных размеров диаметром 52,17 мм и 52,42 мм предназначены для цилиндров, расшлифованных соответственно до 52,25 и 52,5 мм.
Для двигателя мотоцикла поршень к цилиндру подбирают с зазором 0,08—0,1мм. По диаметру юбки поршни разделяются на три размерные группы: 1 — 77,94 мм, 2 — 77,93 мм, 3 — 77,92 мм. Диаметр юбки поршня выбит на донышке поршня. Цилиндры также разделяются по диаметру на три размерные группы: 1—78,03 мм, 2 — 78,02 мм, 3 — 78,01 мм. Диаметр цилиндра выбит на приливе цилиндра для клапанных пружин.
Вес поршня 330~ г. Комплекты поршня с поршневыми кольцами и пальцем разделяются по весу на три группы и соответственно клеймятся. К первой группе относятся комплекты весом 453—457 г, ко второй — 458—462 г и к третьей — 463—467 г.
Для двигателя следует подобрать два комплекта одинаковой весовой группы, т. е. отличающиеся по весу не более чем на 4 г.
На бобышках поршня нанесена одна из цветных меток: красная, белая или зеленая, которые указывают величину диаметра отверстия в бобышках под поршневой палец. На пальцах также имеются цветные метки. При комплектовке подбирают поршень и палец с одинаковыми цветными метками.
Выпускаются также поршни трех ремонтных групп размером 78,2; 78,5 и 79,0мм.
При подборе поршня для двигателя мотоцикла ИЖ-49 следует учесть, что поршень его имеет разрезную пружинящую юбку, которая во время изготовления, обточенная до размера 77,93 мм, после того как ее разрежут, может расшириться на 0,06 мм. Поэтому зазор между поршнем и цилиндром при подборе поршня следует измерять не внизу юбки, а в поясе между третьей, нижней канавкой поршневого кольца и отверстием для поршневого пальца. В этом месте зазор между поршнем и цилиндром должен быть в пределах 0,16—0,18 мм. Внизу юбки в этом случае будет обеспечен зазор 0,08—0,1 мм.
По диаметру в нижней части юбки поршни сортируют на следующие размерные группы: 00 — 71,93—71,92 мм, 0 — 71,92— 71,91 мм, 1—71,91—71,90 мм.Цилиндры также сортируют по диаметру на следующие размерные группы: 00 — 72,02—72,01 мм, 0 — 72,01—72,00 мм, 1—72,00—71,99 мм.
На донышке поршня имеется клеймо, указывающее размерную группу поршня и цветная — черная или белая метка для подбора * поршневого пальца.
Кроме номинального размера выпускаются поршни ремонтных размеров, имеющие на донышке соответствующее клеймо, с диаметром в нижней части юбки 72,43 мм и 72,93 мм для цилиндров, расточенных соответственно до диаметра 72,5 и 73,0 мм.
Для двигателей мотоциклов БМВ-Р-35 и БМВ-Р-75 поршни подбирают к цилиндру с зазором в пределах 0,07—0,08 мм.
При износе юбки поршень во время работы двигателя ударяет о стенки цилиндра, вызывая резкий стук, являющийся для водителя предупреждением о возможной поломке юбки; увеличивается расход масла и ослабевает компрессия, главным образом вследствие ухудшения прилегания колец к зеркалу. В двухтактных двигателях, в которых поршень служит основным распределительным органом, при износе юбки поршня, помимо появления стуков и ослабления компрессии в цилиндре, неплотно закрываются окна и уменьшается компрессия в картере, вследствие чего резко ухудшается заряд — наполнение и пуск и уменьшается мощность двигателя.
Продление срока службы изношенного поршня путем установки новых колец возможно лишь на короткое время; в этом случае кольца изнашиваются очень скоро.
motoskuter.my1.ru