Дефектовка поршневой группы
Автомобили Hyundai - Hyundai Tucson - Двигатель - Ремонт двигателя
После разборки тщательно очистите, промойте и просушите все детали.Вам потребуются: переносная лампа, набор плоских щупов, линейка, штангенциркуль, нутромер, микрометр, шабер.1. Очистите головку поршня от нагара. Если на поршне есть задиры, следы прогара, глубокие царапины, трещины, замените поршень. Прочистите канавки под поршневые кольца. Это удобно делать обломком старого кольца.2. Прочистите отверстия для стока масла подходящим куском проволоки.
3. Проверьте зазоры между кольцами и канавками на поршне, предварительно очистив кольца от нагара.
4. Номинальный зазор, мм:0,04—0,08 - верхнее компрессионное кольцо 1;0,03—0,07 - нижнее компрессионное кольцо 2.Предельно допустимый зазор для обоих колец 0,1 мм.Если хотя бы один из зазоров превышает предельно допустимое значение, замените поршень с кольцами.
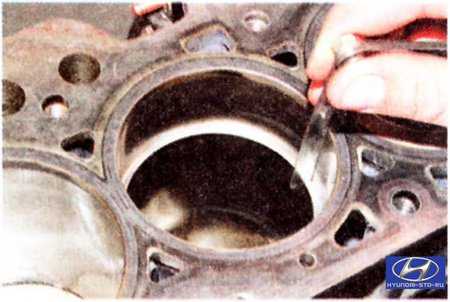
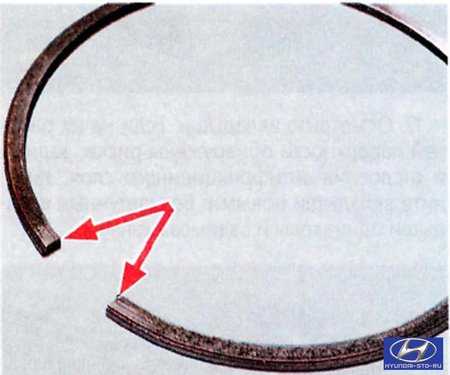
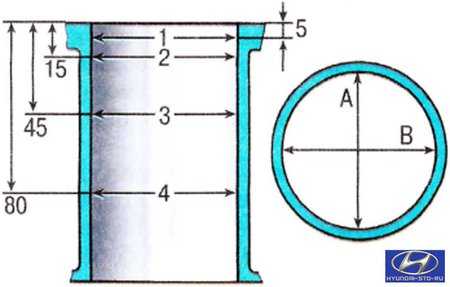
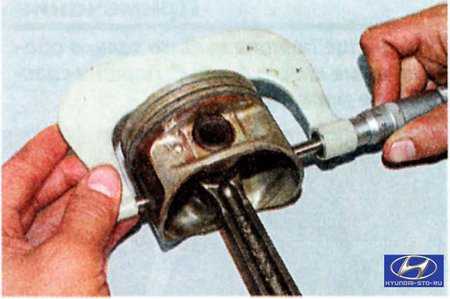
Таблица 5.1 Номинальные размеры цилиндров и поршней
Класс | Диаметр, мм | |
цилиндра | поршня | |
А | 82,00-82,01 | 81,97-81,98 |
В | 82,01-82,02 | 81,98-81,99 |
С | 82,02-82,03 |
В запасные части поставляют поршни номинального размера трех классов (А, В, С) и двух ремонтных размеров (1-й ремонтный размер - увеличенный на 0,25 мм, 2-й -на 0,50 мм).Для поршней ремонтных размеров в запчасти поставляют кольца ремонтных размеров, увеличенных на 0,25 и 0,50 мм.12. Обозначения класса цилиндров выбиты на нижней поверхности блока (привалочная поверхность под масляный картер) в ее задней части.
13. Обозначение класса поршня по диаметру выбито на днище поршня.
ПримечаниеНа днище поршня выбито только обозначение класса А или С. Поршни класса В не маркируют.
14. Поршневые пальцы с трещинами замените. Палец установлен в бобышки поршня с зазором 0,01-0,02 мм, он должен легко входить в поршень от усилия большого пальца руки. Вставьте палец в поршень. Если при покачивании пальца ощущается люфт, замените поршень. При замене поршня подберите к нему палец. Номинальный диаметр пальца 20,001-20,002 мм.
ПредупреждениеШатуны обрабатывают совместно с крышками, поэтому их нельзя разукомплектовывать.
16. Поршневой палец установлен в верхнюю головку шатуна с натягом 0,016-0,032 мм. Поэтому он не должен входить в отверстие головки от усилия пальца руки. Если он входит в отверстие от усилия пальца и, более того, при его покачивании ощущается люфт, замените шатун. При замене шатуна подберите к нему палец.17. Осмотрите вкладыши. Если на их рабочей поверхности обнаружены риски, задиры и отслоения антифрикционного слоя, замените вкладыши новыми. Все шатунные вкладыши одинаковы и взаимозаменяемы.
18. Измерьте нутромером внутренний диаметр Db посадочного места шатуна в сборе с крышкой.
ПримечаниеПеред измерением затяните гайки шатунных болтов номинальным моментом.
19. Измерьте толщину (Т) шатунных вкладышей штангенциркулем.20. Измерьте микрометром диаметр (Dh) шатунных шеек. Номинальный диаметр шеек 45,0 мм.21. Рассчитайте зазор z между шатунными вкладышами и шейками коленчатого вала по формуле z = Db - 2Т - Dh. Номинальный расчетный зазор составляет не более 0,01 мм.Если фактический расчетный зазор меньше предельного, можно снова использовать вкладыши, которые были установлены.Если зазор больше предельного, замените вкладыши на этих шейках новыми номинальной толщины.Если шейки коленчатого вала изношены и перешлифованы до ремонтного размера, уменьшенного на 0,25 мм, замените вкладыши ремонтными (увеличенной толщины).Шейки шлифуют помимо наличия общего износа, если на них есть забоины и риски или овальность составляет более 0,004 мм, а конусность - более 0,005 мм. Существуют три ремонтных размера с уменьшением диаметра шеек, мм:- первый - на 0,25;- второй - на 0,5;- третий - на 0,75.
ПредупреждениеПри перешлифовке шатунных шеек коленчатого вала на ремонтный размер необходимо ставить соответствующее клеймо на первую щеку коленчатого вала, например «Ш 0,25».
§51. Дефектация деталей распределительного устройства и навешенных агрегатов двс
Распределительные валы. Для опргделсния износа patпроделительных ватов необходимо измерять опорные шейки микрометрической еко бой в трех сечениях по длине и двух взаимно перпендикулярных плоскостях. Допустимая эллиптичность шейки нала 0,05 • (1.07 мм
Износ кулачных шайб определяют с помощью шаблона и щупа. Допустимое» отклонение конфигурации шайбы от первоннчалыкш формы I—3 мм. Износ зубьев шестерен проверяют шаблоном и mvnnw. Нормальный зазор между зубьями ие должен превышать 0.! мм.
Топливная аппаратура. В процессе дефектации пповеряют давление подъема иглы, качество распыла топлива форсунками, отсутствие заеданий в подвижных узлах (плунжерной паре, игле и распылителе н др.!; определяют износ и выявляют повреждения деталей, проверяю-! гидравлическую плотность прецизионных пар.
Форсунки испытывают на специальном стенде на качество распыла и герметичность запорного конуса. Если результаты этих испытаний неудовлетворительны, форсунки разбирают к проводят дефектацию деталей.
Прецизионные пары осматривают с помощью лупы 10-кратного увеличения Царапины на рабочих поверхностях, выкрашивание на отсечной кромке плунжера и па кромке приемного окна втулки со стороны рабочей поверхности являются дефектами, при наличии которы* детали бракуют. Иглу распылителя бракуют при подъеме выше нормы.
При увеличении диаметра сопловых отверстий, обгорании или выкрашивании выходных кромок, увеличении ширины запорного конуса более 0,5 мм распылитель заменяю). Допустимое увеличение диаметра сопловых отверстий 10%. Изменение диаметра проверяют эталонными проволочками проходного и непроходного диаметров.
Прямолинейность толкателя иглы можно проверить прокатыванием на плите. контролируя шуном зазор между штоком и плитой Перед дефектацией детали тщательно очищают
Агрегаты, навешенные на двигатель. Гидравлической опрессовкой проверяют наличие трещин в корпусе газотурбонагнетателя (ГТН) и плотность соединений; проверяют зазоры в проточной части ГТН.
Визуальным осмотром выявляют трешины, забоины. задиры на деталях корпуса наддувочных агрегатоя. На плите проверяют плотность прилегания сонрикасаемых поверхностей на краску. Визуально осматривают роторы, лабиринтовые уплотнения, лопатки турбин и компрессора ГТН для выявления забоин, задиров.
Трещины в валах роторов выявляют магнитным способом, трещины в дисках турбин, лопатках, компрессорных колесах — капиллярным способом
Визуальному осмотру подвергают поншишшки качения. Не /(опускается выкрашивание поверхности шариков и роликов, закатывание металлических частиц в беговые дорожки, наличие цветов побежалости на шариках и обоймах. Визуально осматривают и подвергают дефектации магнитным способом шестерни приводных нагнетателей.
Корпус турбины. При удаленных роторе и диафрагмах выявляют коробление корпуса. Верхнюю часть корпуса накладывают на нижнюю без мастики, и при помощи щупа проверяют наличие зазоров и стыке горизонтального разъема при свободном положении верхней части без затягивании и после ззтягиванйя шпилек. Гайки затягивают через одну-дво шпильки в месте высокого давления и через три-четыре — в месте среднего н низкого давления. Крайние шпильки у уплотнений должны быть затя нуты.
Разъем считается плотным при зазоре 0,8— I мм. который затем при затягивании шпилек полностью ликвидируют (чтобы щуп толщиной 0,05 мм не проходил).
.Затягиванием гаек плоскости разъема не всегда возможно выявить н устранить местные неплотности в виде углублений, поэтому рекомендуется иногда проверять плоскость разъема фланца длинной линейкой. Местонахождение впадин и местных неплотностей устанавливают по следам краски, оставляемой предварительно накрашенной линейкой. Проверку линейкой делают в том случае, если путем обтяжки шпилек не устраняются неплотности разъема и предстоит шабрение.
Трещины в корпусе, раковины, вмятины на плоскости разъема, эрозия, коррозия и, как следствие этого, утонение стенок корпуса выявляют при тщательном визуальном осмотре. Применение луны, травление, мелокеросиновая проба помогают выявлению трещин; глубину коррозионного поражения можно определить снятием слепков.
Диафрагмы. Дефектация диафрагм заюиочается во внешнем осмотре для обнаружения следов касания деталей ротора, трещин, коррозионного и эрозионного разрушений лопаток, нарушения заливки лопаток у чугунных диафрагм.
Прогиб диафрагм проверяют на плите линейкой и щупом. Линейку прикладывают к диафрагме вблизи разъема со стороны входа пара, и щупом проверяют зазор между линейкой и диафрагмой. При наличии остаточного прогиба более 0,15—0,2 мм (у чугунных диафрагм) и более 0,2—0,3 мм (у стальных) необходимо реш-ать вопрос о дальнейшей эксплуатации диафрагм. При отсутствии уверенности в прочности диафрагмы прибегают к испытанию на изгиб давлением, соответствующим максимальной нагрузке.
Проверяют правильность установки диафрагмы в корпусе по осевым зазорам между корпусами турбины и диафрагмой Осевые зазоры должны быть равны 0,05—0.1 мм. За падение плоскостей разъема верхней и нижней половин диафрагмы должно составлять 0.5—0,1 мм для теплового расширения.
Уплотнительные устройства. Визуальным осмотром выявляют смятие и разрыв уплотнительных гребешков. Щупом проверяют радиальные' зазоры в уплотнениях в плоскости горизонтального разъема корпуса турбины. Для концевых упругих уплотнений эти зазоры при монтаже должны быть 0,1—0,3 мм, при эксплуатации —0,4—0,5 мм.
S яиафрагменкых уплотнениях монтажные зазоры 0.2—0.35 мм, предельно допустимые 0,5—0,6 мм. Д.пя жег-тких уплотнений монтажные и предельно допустимые величины зазоров несколько больше.
studfiles.net
Дефектовка блока цилиндров с коленчатым валом и деталей поршневой группы двигателя 4B12 Citroen C-Crosser 2007
Инструменты:
- Нож (или скребок)
- Шабер
- Поверочная линейка
- Щуп плоский
- Компрессор
- Пневмопистолет для обдувки
- Нутромер
- Микрометр
- Измерительная головка часового типа с штативом
- Стенд для измерения осевого биения
- Ключ трещоточный
- Головка на 16 мм
- Динамометрический ключ
- Приспособление для измерения скручивания и изгиба шатуна
- Специальный инструмент с угловым индикатором МВ991614
- Кисть флейцевая
Детали и расходники:
- Коленчатый вал 0501.L8 (при необходимости)
- Упорное полукольцо 0118.G0 - 2 шт. (при необходимости)
- Верхний вкладыш коренного подшипника коленчатого вала 0113.Y3 - 5 шт. (при необходимости)
- Нижний вкладыш коренного подшипника коленчатого вала 0113.X9 - 5 шт. (при необходимости)
- Вкладыш шатунного подшипника коленчатого вала 0606.Y6 - 8 шт. (при необходимости)
- Маховик двигателя 0532.S2 (при необходимости)
- Пластина привода гидротрансформатора 0535.A9 (при необходимости)
- Переходная пластина 0535.A7 (при необходимости)
- Задний сальник коленчатого вала 0127.51 (при необходимости)
- Блок цилиндров двигателя 1050A750 (при необходимости)
- Шатун в сборе 0603.A5 - 4 шт. (при необходимости)
- Поршень с поршневым пальцем 0627.63/0627.64/0627.65/0627.62 - 4 шт. (при необходимости)
- Комплект поршневых колец 0627.66/0627.67 - 4 шт.
- Пластиковый калибр Plastigauge PL-А (0,025 - 0,175 мм)
- Очиститель (или растворитель)
- Обезжириватель
- Проникающий краситель
- Моторное масло
- Краска
- Ветошь
Примечания:
Как снять двигатель Кроссер и провести его разборку, а также какие инструменты при этом используются, смотрите здесь и здесь. При диагностике блока цилиндров, коленчатого вала и деталей поршневой группы необходимо проводить такие работы, как: проверка зазора в коренных подшипниках коленчатого вала, некруглости и конусности коренных и шатунных шеек коленчатого вала, биение маховика, проверка износа цилиндра, зазора между поршнем и цилиндром.
Проверка блока цилиндров
1. Перед очисткой блока цилиндров проверьте отсутствие следов течей охлаждающей жидкости или каких-либо очевидных повреждений.
Примечание:
При выявлении повреждений, которые нельзя отремонтировать без потери свойств материалов, рекомендуется заменить блок цилиндров.
2. Очистите детали от грязи, масла, углеродных остатков, накипи и других видов отложений, после чего можно приступить к проверке и ремонтным операциям.
3. Удалите осадки с масляных отверстий и убедитесь, что эти отверстия не забиты грязью и отложениями. При необходимости продуйте сжатым воздухом отверстия каналов системы смазки и системы охлаждения.
4. Все детали должны быть аккуратно разложены в соответствии с порядком сборки.
5. Визуально проверьте блок цилиндров на отсутствие остатков прокладки или других посторонних частиц и повреждений. При обнаружении дефектов устраните их или замените блок цилиндров.
6. Проверьте блок цилиндров с помощью жидкого раствора (проникающего красителя) для определения наличия трещин. Если дефекты очевидны, то замените блок цилиндров.
7. С помощью поверочной линейки и плоского щупа проверьте степень коробления рабочих поверхностей блока цилиндров в направлениях, показанных на рисунке. Поверхность блока цилиндров должна быть очищена от посторонних частиц.
Примечание:
Номинальное значение – 0,05 мм или меньше; предельно допустимое значение – 0,1 мм.
8. Если коробление значительно, то исправьте дефект до допустимой величины или замените блок цилиндров.
Примечание:
Предельно допустимая глубина шлифования – 0,20 мм. Общая толщина снимаемого металла с привалочных поверхностей головки блока цилиндров и блока цилиндров не должна превышать в сумме 0,2 мм.
9. Проверьте зеркало цилиндра на отсутствие царапин и следов заедания (задиров). Если дефекты очевидны, отремонтируйте или замените блок цилиндров.
10. Проверьте износ цилиндров с помощью индикатора-нутромера. Для этого измерьте диаметр цилиндра, а также овальность (отклонение от крутости) и конусность (отклонение от цилиндричности) цилиндра.
Примечание:
Номинальное значение внутреннего диаметра цилиндра двигателя – 88,00 - 88,03 мм. Предельно допустимая конусность (отклонение от цилиндричности) – 0,15 мм. Измерения проводите в местах, показанных на рисунке (в трех поясах по высоте).
11. При наличии сильного износа цилиндра либо если конусность или некруглость (овальность) цилиндра больше предельно допустимого значения, то замените блок цилиндров.
Примечание:
После замены блока цилиндров необходимо подобрать соответствующие поршни и поршневые кольца.
12. Измерьте наружный диаметр поршня в месте, показанном на рисунке.
Примечание:
Наружный диаметр поршня – 87,97 - 88,00 мм.
13. По результатам измерения диаметра цилиндра и наружного диаметра поршня, определите зазор между поршнем и цилиндром, который должен находится в указанном диапазоне: 0,02 - 0,04 мм.
14. Если определенный (вычисленный) зазор не соответствует указанному значению, то замените блок цилиндров.
Примечание:
После замены блока цилиндров необходимо подобрать соответствующие поршни и поршневые кольца.
Проверка коленчатого вала
1. Проверьте коренные и шатунные шейки коленчатого вала на отсутствие повреждений (задиры, прихваты), чрезмерного износа (см. первое фото ниже) и трещин (см. второе фото ниже). Кроме того, проверьте отверстия масляных каналов на отсутствие засорения. При необходимости, замените коленчатый вал.
Примечание:
В случае замены коленчатого вала необходимо подобрать новые вкладыши коренных и шатунных подшипников коленчатого вала. Процедура подбора вкладышей шатунных и коренных подшипников коленчатого вала приведена здесь.
2. Проверьте некруглость и конусность коренных и шатунных шеек, как показано на рисунке.
Примечание:
Предельно допустимые значения: некруглость – не более 0,003 мм; конусность – не более 0,005 мм.
3. Если некруглость или конусность больше предельно допустимого значения, то замените коленчатый вал.
4. Измерьте наружный диаметр коренной шейки коленчатого вала и внутренний диаметр вкладыша коренного подшипника коленчатого вала в двух взаимно перпендикулярных направлениях (на рисунке обозначены "А" и "В") и в двух сечениях по длине (на рисунке обозначены "1" и "2").
Примечание:
Наружный диаметр коренной шейки коленчатого вала – 51,973 - 51,988 мм. Зазор в коренном подшипнике: номинальный – 0,012 - 0,030 мм; предельно допустимый – 0,08 мм.Здесь смотрите, как определить величину зазора в коренных подшипниках коленчатого вала методом пластикового калибра.
5. Если величина зазора превосходит предельно допустимое значение, то замените вкладыши коренного подшипника и, если необходимо, коленчатый вал.
Примечание:
Не подвергайте механической обработке подшипник или постель коленчатого вала для регулировки зазора. Если нельзя получить номинальный зазор, используя подбор вкладышей, то замените коленчатый вал.
Проверка вкладышей коренных подшипников
1. Визуально проверьте состояние поверхности вкладыша коренного подшипника (неравномерный контакт, полосы, царапины, задиры и др.). В случае очевидного наличия дефектов замените вкладыши коренного подшипника.
Примечание:
Если вкладыш нуждается в замене, то выберите и установите вкладыш требуемого размера. Как это сделать, смотрите здесь.
2. Если имеются дефекты (полосы и задиры), то проверьте соответствующие шейки коленчатого вала (см. выше в разделе проверки коленчатого вала).
3. Проверьте зазор в коренном подшипнике, как описано в п.4 выше (раздел проверки коленчатого вала) или здесь.
Проверка заднего сальника коленчатого вала
1. Проверьте рабочую кромку сальника коленчатого вала на отсутствие износа или повреждения.
2. Проверьте резиновую часть сальника на отсутствие затвердевания или разрушения.
Примечание:
При выявлении дефектов замените задний сальник коленчатого вала.
Проверка маховика или пластины привода гидротрансформатора
1. Как проверить маховик (пластину привода гидротрансформатора), смотрите здесь.
Примечание:
При необходимости, замените маховик (пластину привода гидротрансформатора).
Проверка упорных полуколец
1. Проверьте состояние поверхности каждого полукольца (отслаивание, неравномерный контакт, риски, задиры и износ). Замените при необходимости.
2. Установите вкладыши коренных подшипников на блок цилиндров и упорные полукольца. Уложите коленчатый вал на подшипники и проверьте, что осевой зазор коленчатого вала соответствует номинальному значению. Если осевой зазор превышает предельно допустимое значение, то замените упорные полукольца.
Примечание:
Осевой зазор коленчатого вала: номинальное значение – 0,05 - 0,25 мм; предельно допустимое значение – 0,40 мм.
Проверка поршня и поршневого пальца
Примечание:
Поршень и поршневой палец необходимо заменять как комплект.
1. Проверьте поршни Ситроен на отсутствие царапин, задиров, износа и других дефектов (особенно на упорных поверхностях). Замените поршень при наличии дефектов.
Примечание:
Перед проверкой поршня, удалите отложения нагара с его верхней поверхности. Если на поршне имеется какие-либо дефекты, то проверьте также зеркало цилиндра (см. раздел проверки блока цилиндров). При необходимости замены поршня одновременно следует заменить его поршневые кольца.
2. Попытайтесь вставить поршневой палец в отверстие поршня усилием большого пальца. При этом должно чувствоваться сопротивление. Замените палец, если он легко входит в отверстие или имеется значительный люфт.
Проверка поршневых колец
Примечание:
Если поршень заменяется новым, то поршневые кольца также необходимо заменить новыми.
1. Проверьте каждое поршневое кольцо на отсутствие изломов, повреждений или значительного износа. Замените дефектные кольца.
2. Измерьте зазор между поршневым кольцом и канавкой поршня. Если измеренный зазор превышает предельно допустимое значение, то установите новое поршневое кольцо и повторно измерьте зазор. Если измеренный зазор снова превышает предельно допустимое значение, то замените поршень. Если измеренный зазор меньше предельно допустимого значения, то замените только поршневые кольца.
Примечание:
Зазор между компрессионным кольцом и канавкой под него: номинальное значение – 0,03 - 0,07 мм; предельно допустимое значение – 0,10 мм. Перед выполнением измерений удалите отложения нагара из всех канавок поршня. Измерение зазора между кольцом и канавкой поршня выполните по всей окружности кольца.
3. Установите поршневое кольцо в отверстие цилиндра. Переместите кольцо поршнем, как показано на рисунке, это позволит кольцу встать под прямым углом к образующей стенки цилиндра. Измерьте зазор в замке кольца с помощью плоского щупа. Если зазор больше предельно допустимого значения, то замените поршневое кольцо.
Примечание:
Номинальное значение зазора в замке поршневого кольца: компрессионное кольцо №1: 0,15 - 0,25 мм; компрессионное кольцо №2 – 0,30 - 0,45 мм; маслосъемное кольцо – 0,10-0,35 мм. Предельно допустимое значение зазора в замке поршневого кольца: компрессионные кольца №1 и №2 – 0,8 мм; маслосъемное кольцо – 1,0 мм.
4. При замене поршневых колец без замены блока цилиндров (или если не выполнялась механическая обработка цилиндров), проверяйте зазор в замке поршневых колец в точке, расположенной в нижней части цилиндра (зона наименьшего износа).
Проверка вкладышей шатунных подшипников
1. Визуально проверьте состояние поверхности вкладыша шатунного подшипника (неравномерный контакт, полосы, царапины, задиры и др.). В случае очевидного наличия дефектов замените вкладыши шатунного подшипника.
2. Если имеются дефекты (полосы и задиры), то проверьте соответствующие шейки коленчатого вала (см. в разделе проверки коленчатого вала и блока цилиндров выше). Если имеются дефекты на шейках коленчатого вала, то замените коленчатый вал.
Примечание:
В случае замены коленчатого вала необходимо подобрать новые вкладыши коренных и шатунных подшипников коленчатого вала. Как правильно подобрать вкладыши, смотрите здесь.
3. Измерьте внутренний диаметр шатунного подшипника и наружный диаметр шатунной шейки коленчатого вала, затем определите зазор в шатунном подшипнике.
Примечание:
Для измерения зазора в шатунном подшипнике можно использовать пластиковый калибр. Наружный диаметр шатунной шейки коленчатого вала – 47,954 - 47,972 мм. Зазор в шатунном подшипнике: номинальный – 0,018 - 0,045 мм; предельно допустимый – 0,10 мм.
4. Если масляный зазор превышает предельно допустимое значение, то замените, если необходимо, вкладыши шатунного подшипника или коленчатый вал, или обе детали.
Проверка шатуна
1. Установите поршневой палец в шатун, если он был снят.
2. Установите шатун в специальный прибор "С" вместе с установленными верхним и нижним вкладышами шатунного подшипника (см. рисунок ниже, в п.4).
3. Затяните болты крепления крышки шатуна в соответствии со специальной процедурой.
4. Проверьте изгиб "А" и скручивание "В" шатуна, как показано на рисунке.
Примечание:
Предельно допустимое значение (на 100 мм длины): изгиб – 0,05 мм; скручивание – 0,10 мм.
5. Измерьте геометрические параметры шатуна.
Примечание:
Диаметр верхней головки шатуна (d) – 20,974 - 20,985 мм. Диаметр нижней головки шатуна (D) – 51,000 - 51,018 мм. Длина шатуна (L) – 143,75 мм. Длина шатуна (L) – расстояние между центрами верхней и нижней головок шатуна.
6. Если изгиб или скручивание шатуна превысили предельно допустимое значение по техническим требованиям, то замените шатун в сборе с крышкой.
В статье не хватает:
- Фото инструмента
- Фото деталей и расходников
Источник: carpedia.club
carpedia.club
Основные неисправности цилиндро-поршневой группы двигателей ЯМЗ
Внешние проявления неисправностей деталей цилиндро-поршневой группы (ЦПГ) (поршни, гильзы и поршневые кольца) следующие:
- увеличение расхода масла на долив;
- ухудшение пусковых качеств двигателя;
- снижение мощностных и экономических показателей;
- увеличение расхода картерных газов;
- существенное ухудшение состояния картерного масла.
N | Номер по каталогу | Количество | Наименование |
1 | 236-1004063-Б | 6 | Болт крышки шатуна длинный |
2 | 236-1004062-Б | 6 | Болт крышки шатуна короткий |
3 | 236-1002023 | 6 | Кольцо уплотнительное нижнее |
4 | 236-1002024-А | 6 | Кольцо уплотнительное верхнее |
5 | 236-1002040 | 6 | Кольцо антикавитационное |
6 | 236-1002021-А | 6 | Гильза цилиндра |
7 | 236-1004020 | 6 | Палец |
8 | 236-1004015-Д | 6 | Поршень |
9 | 236-1004006 | 6 | Гильза, поршень, палец |
10 | 236-1004022-Б | 12 | Кольцо стопорное |
11 | 236-1000106-БЗ | 6 | Кольца поршневые (комплект на один поршень) |
12 | 236-1004038-Б | 6 | Расширитель |
13 | 236-1004035-В | 6 | Кольцо маслосъемное |
14 | 236-1004034-А | 6 | Кольцо маслосъемное с расширителем |
15 | 236-1004025-В | 6 | Кольцо компрессионное третье |
16 | 236-1004032-АЗ | 6 | Кольцо компрессионное второе |
17 | 236-1004030 | 6 | Кольцо компрессионное верхнее |
18 | 236-1004052-Б2 | 6 | Втулка шатуна |
19 | 236-1004045-Б2 | 6 | Шатун |
20 | 236-100405 8-В | 12 | Вкладыш |
При диагностировании деталей ЦПГ необходимо убедиться в исправности других узлов и систем двигателя, оказывающих влияние на работоспособность рассматриваемых деталей. Так, в случаях повышенного расхода масла на долив (выше 1,5%) необходимо убедиться в отсутствии течи масла из двигателя наружу и разгерметизации впускного тракта.
Диагностирование до разборки двигателя необходимо начинать с выяснения условий работы двигателя, качества и объема проведенных обслуживаний и текущих ремонтов. В условиях работы необходимо оценить нагруженность двигателя по эксплуатационному расходу топлива в л/100 км (л/моточас), тепловой режим и наличие шума или стука при работе. Необходимо также определить возможные остановки двигателя по неустановленным причинам, расход масла на долив и характер его изменения за общее время работы двигателя в эксплуатации.
Источник фото: 24ri.ruДиагностирование до разборки необходимо начинать с выяснения условий работы ДВС
После выполнения указанных работ при возможности запустить двигатель и прослушать его работу на режимах холостого хода от минимальной до максимальной частоты вращения коленчатого вала. Необходимо осмотреть отложения на шторах бумажного элемента полнопоточного масляного фильтра, а также в фильтре центробежной очистки масла. Обратить особое внимание на количество отложений и наличие металлической стружки. Необходимо отобрать пробу масла из картера двигателя в количестве 250 -500 мл и отправить ее в химическую лабораторию на предмет определения физико-химических показателей масла (вязкость, щелочное число, количество нерастворимых осадков, наличие воды в масле, диспергирующие свойства и др.).
Источник фото: dymz.ruБумажный элемент масляного фильтра осматривают на предмет наличия металлической стружки
Могут быть использованы также методы инструментального (приборного) диагностирования. Так, замеряется давление в конце такта сжатия в цилиндрах двигателя. Оно определяется в абсолютных единицах с помощью компрессометра или в относительных единицах с помощью специальной аппаратуры, фиксирующей изменение силы тока в цепи стартера при прокрутке коленчатого вала в процессе последовательного отключения цилиндров двигателя.
Компрессометром замеряется давление сжатия при прокрутке коленчатого вала стартером или в режиме работы двигателя при минимальной частоте холостого хода. Последний вариант испытаний является более предпочтительным, т.к. точность измерения возрастает за счет поддержания определенного скоростного режима двигателя. Величина давления сжатия при nx/x = 800 мин-1 для двигателей ЯМЗ должна составлять pc = 3,0...3,5 МПа (30...35 кг/см2). Особое внимание следует обращать на разность давлений pc по цилиндрам. Это сравнение позволит определить цилиндр с дефектными деталями ЦПГ.
Источник фото: 24ri.ruДавление сжатия лучше замерять в режиме работы ДВС при минимальной частоте холостого хода
По замерам значений pc можно определить следующие дефекты деталей ЦПГ: прогар поршня, поломку компрессионного кольца, изношенность деталей, закоксовку колец, задиры поршней и негерметичность клапанов механизма газораспределения. При указанных дефектах обычно значение pc в цилиндре бывает меньше 2,0...2,1 МПа (20...21 кг/см2).
Дополнительную информацию о состоянии деталей ЦПГ можно получить с помощью физико-химического и спектрального анализов картерного масла.
Наибольший объем информации о причинах выхода из строя деталей ЦПГ можно получить после разборки двигателя и анализа состояния деталей. Состояние деталей ЦПГ и возможные причины их дефектов приведены в таблице 2.
Таблица 2.
Состояние деталей ЦПГ и причины их дефектов.
Состояние деталей ЦПГ | Возможные причины дефектов ЦПГ | Примечание |
1. Задир цилиндрической части поршня с переносом его материала на поверхность гильзы. | 1. Неправильно подобран зазор в системе поршень-гильза (меньше или больше рекомендуемого). | |
2. Перегрев двигателя в эксплуатации. | Задир начинает развиваться на участках поршня, расположенных под углом 45° к оси кольца. | |
3. Зависание (закоксовывание) колец в канавках из-за недопустимой переработки картерного масла или применения масла, не соответствующего заводской инструкции по эксплуатации. | Задир может быть только на головке или на всей поверхности юбки поршня. | |
4. Увеличена цикловая подача топлива секций ТНВД. | Необходима проверка и регулировка ТНВД на стенде. | |
5. Превышение номинальной частоты вращения коленчатого вала (более 2100 мин.) из-за неисправности регулятора ТНВД. | Проверить и отрегулировать максимальную частоту вращения при испытаниях ТНВД на стенде. | |
2. Обрыв поршня по бобышкам поршневого пальца. | Обрыв является следствием задира и заклинивания поршня в гильзе. | Обрыв происходит чаще на многоцилиндровых двигателях. |
3. Обгорание днища поршня. | Увеличение угла опережения впрыска топлива от нормы, повышение цикловой подачи секций ТНВД. | Проверка регулировок ТНВД на стенде. |
4. Закоксование (зависание) компрессионных колец. | Переработка масла или использование масел, не соответствующих заводской инструкции по эксплуатации. | |
5. Износ маслосъемных колец вплоть до срабатывания хромированного покрытия. | Низкое качество фильтрации картерного масла. | Необходима проверка состояния элементов масляного фильтра и перепускного клапана. |
6. Повышенный износ колец, канавок поршня и гильз. | Низкое качество фильтрации воздуха, поступающего в цилиндры двигателя. | Проверить состояние элементов воздухоочистителя и герметичность впускного тракта автомобиля или трактора. |
7. Поломка поршневых колец, возможно разбивание межкольцевых перемычек поршня частями разрушенного кольца. | Чрезмерный износ деталей ЦПГ из-за низкого качества фильтрации воздуха или нарушения герметичности впускного тракта, приведшего к пропуску в цилиндры двигателя нефильтрованного воздуха. | Проверить состояние элементов воздухоочистителя и герметичность впускного тракта автомобиля или трактора. |
Особое внимание при эксплуатации двигателей необходимо обращать на состояние воздухоочистки, при нарушении которой преждевременно вырабатывается ресурс деталей ЦПГ. Многолетний опыт эксплуатации двигателей ЯМЗ показывает, что износ деталей ЦПГ, как правило, носит абразивный характер и вызван нарушением фильтрации воздуха.
Источник фото: carnovato.ruПри эксплуатации ДВС необходимо обращать внимание на состояние воздухоочистки
Абразивный износ двигателя (иногда его называют пылевым) определяется по снижению мощности ("плохо тянет"), повышенному дымлению, выбросу масла из сапуна и, как следствие, увеличенному расходу масла (обычно выше 2...3% от расхода топлива). В отдельных случаях работа двигателя сопровождается металлическим стуком, хорошо прослушиваемым при средней частоте вращения коленчатого вала на холостом ходу. Причиной стука, как правило, является поломка первого компрессионного кольца, вызванная повышенной его вибрацией вследствие чрезмерного износа канавки поршня и самого кольца по высоте.
Процесс обслуживания воздушного фильтра и проверка герметичности впускного тракта двигателя е составе изделия подробно описаны в инструкциях по эксплуатации двигателя. К сожалению, практика показывает, что в эксплуатации зачастую пренебрегают этими операциями ТО, что приводит к преждевременному аварийному износу ЦПГ.
Статья из журнала"Техническое обслуживание", № 2-3, сентябрь 2004
exkavator.ru
Дефектовка и ремонт шатунно-поршневой группы Волги ГАЗ-3110
gaz-3110.ru
ДЕФЕКТОВКА ПОРШНЕЙ. Дефектовка поршней двигателя ваз класического семейства.
Дефектовка поршней
Прежде чем приступить к ознакомлению с материалом раздела работы с двигателем не будет лишним напомнить некоторые моменты, связанные с техникой безопасности. Речь идёт о том, что дефектовка поршнейтребует применения жидких средств для размачивания нагара. Автолюбители за неимением керосина применяют бензин, растворители разных марок, некоторые используют тормозную жидкость. В общем, все, что есть под рукой. Пары перечисленных ранее материалов токсичны, что в свою очередь может привести к отравлению. Решать, конечно, вам, но здоровье важнее.
Далее для отчистки деталей от нагара вам понадобится шабер, шабер можно изготовить самостоятельно из старого трёхгранного напильника. Для этого заточите грани напильника на наждаке.
1. Очистите шабером днище поршня от нагара.2. Острой гранью старого кольца отчистите от нагара посадочную канавку поршневых колец.3. Осмотрите на предмет трещин, крышки шатунов, шатуны, поршни, если трещины обнаружены, замените деталь.4. Замените вкладыши новыми, если при осмотре были обнаружены дефекты: отслоения антифрикционного слоя, задиры и риски на рабочей поверхности. Все шатунные вкладыши являются взаимозаменяемыми.
5. При помощи микрометра и штангенциркуля измерьте диаметры поршней, как показано на изображении. Расстояние от днища поршня до точки измерения микрометром должно быть- 52,4 мм.
Определите зазор между поршнем и цилиндром по результатам замеров. Зазор не должен превышать 0,15мм, для двигателя, бывшего в эксплуатации, а для новых деталей 0,05-0,07 мм. Если зазор превышает максимально допустимый, поршни подлежат замене новыми.
6. вставьте палец, смазанный чистым моторным маслом, в отверстие бобышки поршня.
Пальцы делятся на три категории по наружному диаметру, которая отмечена на торце пальца краской,Синяя метка-21,970- 21,974мм.Зелёная метка-21,974-21,978ммКрасная метка-21,978-21,982мм.Смазанный моторным маслом палец, должен с усилием, но без заедания входить в отверстие бобышки.
Проверить палец можно следующим образом, поверните поршень вертикально как показано на изображении, при этом палец не должен выпадать со своего посадочного места. Если палец выпадает, замените его другим, категорией большей по диаметру. Если и последняя категория не подходит, замените палец вместе с поршнем.
7. По высоте в посадочных местах колец плоским щупом проверьте зазор.
Расчётный зазор составляет, для верхнего компрессионного кольца:0,045-0,08мм,Для следующего компрессионного кольца-0,025-0,06мм,Для маслосъёмного кольца 0,02-0,055мм.При износе максимально допустимый зазор не должен превышать 0,15мм
8. Утопите кольцо вглубь цилиндра примерно на 50мм, используйте при этом поршень, для того чтобы не было перекосов. Проверьте зазор в замке колец при помощи плоского щупа.
При износе зазор не должен превышать 1,0мм, а для нового кольца он должен быть-0,25- 0,45мм. Если зазор малый допускается спиливание стыковых поверхностей кольца. Кольцо требует замены, если зазор превышает предельно допустимый.
9. Так же необходимо взвесить поршня двигателя, поршня по весу не должны иметь расхождение больше чем на ±2,5 грамма. Так же возможно подогнать поршня друг к другу по весу снятием лишнего метала в местах, показанных на изображении. Глубина снятия не должна превышать 4,5мм.
В принципе на этом дефектовка поршня закончена, остаётся только выполнить все рекомендации и советы.
doctorvaz.ru
Детали шатунно-поршневой группы
Строительные машины и оборудование, справочник
Категория:
Эксплуатация и ремонт погрузочночных машин
Детали шатунно-поршневой группыШатуны в результате эксплуатации двигателей получают следующие неисправности: изгиб и скручивание, износ отверстия под втулку верхней головки, посадочных мест под вкладыши, поверхностей разъема шатуна и крышки, а также опорных поверхностей под головки и гайки шатунных болтов.
Проверить изгиб и скрученность шатуна можно на специальном приборе (рис. 112, а), который имеет подставку с вертикальной стойкой и поверочной плитой. Нижнюю головку шатуна надевают на раздвижную оправку со сменными сегментными шпонками и зажимают винтом.
Сменная оправка на приборе крепится зажимом. При постановке на прибор непогнутого и нескручен- ного шатуна калибр, размещенный на контрольном поршневом палы, будет касаться поверхности плиты тремя точками. Если шатун имеет изгиб, то плита коснется или одной верхней точки, или двух нижних. В случае скручивания шатуна только одна точка нижних опор калибра касается плиты.
Устраняют изгиб и скручивание шатуна в холодном состоянии с помощью специальных приспособлений. Скручивание ликвидируют воротком, предварительно зажимая шатун в тиски, а изгиб — винтовым приспособлением или прессом. Износ верхнего и нижнего отверстий шатуна определяется их диаметрами. Диаметры отверстий измеряют в двух взаимно перпендикулярных плоскостях и двух сечениях. Сечения выбирают от торцов отверстий головок шатуна на расстоянии 1/4 их толщины. Замер нижнего отверстия предусматривается при нормальном усилии затяжки шатунных болтов. Диаметр верхнего отверстия шатуна должен обеспечивать посадку втулки с натягом 0,06—0,15 мм.
Если наименьший натяг выполнить нельзя, то отверстие растачивают под ремонтную втулку, имеющую увеличенный наружный диаметр на 0,5 мм, на токарном станке, причем овальность и конусность полученного отверстия не должны превышать 0,02 мм.
Рис. 112. Приборы для проверки прямолинейности шатуна и упругости поршневого кольца
Восстановление опорных поверхностей шатуна и крышки проводят фрезерованием или опиливанием напильником. Обработка ведется до устранения следов повреждений, после чего пришабривают поверхности по плите. Допускается наплавка опорных поверхностей шатуна с предохранением отверстий под шатунные болты медными и графитовыми стержнями. Покоробленные поверхности разъема с нарушением параллельности восстанавливают пришабриванием или притиранием мелкозернистой шлифовальной шкуркой на плите. После обработки поверхности разъема должны быть перпендикулярны осям отверстий под болтьГ Указанные поверхности должны лежать в одной плоскости с точностью до 0,03 мм, непараллельность образующей поверхности отверстий нижней головки шатуна не должна превышать 0,02 мм.
Поршни при ремонте могут иметь следующие дефекты: износ поршневых канавок, трещины и задиры на стенках, износ отверстий в бобышках и нагар на днище и канавках. Поршневые канавки изнашиваются неравномерно. Наиболее сильно изнашивается верхняя канавка, так как она находится в особо тяжелых условиях. Поршни с канавками, изношенными сверх допустимых значений, бракуют. Иногда канавки под кольца протачивают увеличенной ширины. Однако этот метод восстановления получил ограниченное распространение, так как работа двигателя с такими кольцами приводит к вибрациям, происходит пропуск газов в картер. Отверстия в бобышках развертывают под большой ремонтный размер поршневого пальца. Для соблюдения перпендикулярности осей поршня и пальца применяют развертку с направляющим хвостовиком, который позволяет удерживать инструмент сразу с двух сторон отверстия независимо от того, обрабатывается одна или две поверхности одновременно. Отклонение осей от перпендикулярного положения допускается не более 0,05 мм.
Поршни с трещинами и глубокими царапинами заменяют. Наличие трещин устанавливают по характеру звука, возникающему от удара по поршню небольшим металлическим предметом. В случае наличия трещины получается сухой дребезжащий звук.
Нагар удаляют металлическим инструментом, причем при очистке в канавки заправляют резцы, которые с помощью оправки вращают по окружности поршня.
Поршневые пальцы изнашиваются по всей длине. Если износ пальцев по диаметру превышает 0,03 мм, то их ремонтируют или заменяют.
При ремонте пальцы шлифуют под уменьшенный ремонтный размер или хромируют. Шлифуют на круглошлифовальном или токарном станке с использованием суппортно-шлифовального приспособления, которое имеет шлифовальный круг с приводом от электродвигателя и крепится на суппорте станка. Овальность обработанного пальца допускается не более 0,005 мм. Как правило, поршневые пальцы при восстановлении первоначального размера подвергают пористому хромированию, наиболее благо- 214 приятному для удержания смазочного материала по сравнению с гладким слоем хрома. Необходимый диаметр пальца получают путем шлифования.
Поршневые кольца, имеющие износ поверхностей и потерявшие необходимую упругость, бракуют. Бракованные кольца заменяют новыми, подобранными согласно ремонтным размерам поршня и цилиндра.
Проверяют упругость колец на приборе (рис. 112, б), состоящем из платформы и подвижного упора, между которыми устанавливают проверяемое кольцо, а также из механизма для определения массы с грузами отсчетными шкалами. При замере упругости стык кольца располагают сбоку, удерживая кольцо в вертикальном положении путем нажатия рукояткой с зажимным болтом. Затем перемещают грузы механизма для определения массы таким образом, чтобы зазор в стыке кольца соответствовал номинальному значению согласно техническим условиям. В этом положении по шкале весов определяют значение упругости.
Перед постановкой на поршень в кольцах проверяют зазор, для чего их устанавливают в калибр с диаметром, равным диаметру поршня. После этого щупом замеряют зазор и, если он меньше требуемого, производят подгонку стыка напильником до номинального значения. Зазоры в стыках компрессионных поршневых колец должны находиться в пределах 0,3—0,5 мм, а для маслосъемных колец —в пределах 0,15—0,45 мм. Кольца с большими зазорами для конкретного диаметра поршня (калибра) непригодны.
При комплектовании деталей шатунно-поршневой группы учитывают ремонтные размеры, которые на гильзах указываются на верхнем торце, а на поршне — на днище или нижнем торце. Поршневые кольца по канавкам поршня должны перемещаться свободно, но без качки и заеданий. Зазор между торцом кольца и канавкой замеряют щупом и при необходимости торцы обрабатывают шлифовальной шкуркой на ровной поверхности.
Укомплектованные поршневые кольца проверяют на плотность прилегания к стенкам цилиндра. Для этого их помещают в гильзу и щупом измеряют зазор по дуге, который на длине дуги 60 мм не должен быть более 0,03 мм. Кольца с большим-зазором заменяют.
Отремонтированные поршни, шатуны и поршневые пальцы собирают с помощью специального приспособления. Для этого поршень предварительно нагревают в ванне до 80—90 °С, протирают и смазывают верхнюю втулку шатуна и палец поршня. Затем вставляют шатун в поршень, с помощью оправки центрируют отверстия и до упора оправки запрессовывают поршневой палец в поршень. При этом необходимо обращать внимание на правильность их взаимного расположения.
После соединения шатуна с поршнем устанавливают стопорные кольца поршневых пальцев и проводят взвешивание. Разность масс собранных комплектов не должна превышать значений, регламентированных техническими условиями.
—-
Шатуны изготовляют из легированных сталей 40Х, 45Г2, 40Р. В шатунах образуются такие дефекты, как изгиб, скручивание стержня, износ отверстий нижней головки, втулки и отверстия под втулку верхней головки, износ и смятие плоскостей нижней головки.
Не подлежат использованию шатуны с обломами и трещинами, с аварийными изгибами. Допустимый изгиб шатунов, измеренный на длине 100 мм, составляет 0,03—0,04 мм, а допустимое скручивание — 0,04—0,06 мм. Для определения изгиба (непараллельности) и скрученности (перекоса) верхней головки шатуна относительно нижней шатун в сборе с крышкой устанавливают на прибор (рис. 78). В верхнюю головку шатуна (без втулки) устанавливают разжимную оправку, а на нее — призму с индикаторами. Шатун придвигают к плите и по отклонению стрелок индикатора определяют изгиб и скрученность. Эти дефекты устраняют правкой на специальных винтовых или гидравлических приспособлениях с последующим нагревом в печи до 400—450 °С. Шатуны выдерживают при этой температуре 1,5 ч, затем постепенно охлаждают на воздухе.
Смятые или изношенные плоскости разъема крышки и шатуна, не обезличивая, фрезеруют или шлифуют до выведения следов износа и достижения перпендикулярности осям отверстий под болты. Допустимо удалять слой металла толщиной до 0,3 мм с крышки и до 0,2 мм с шатуна. Площадки под гайки болтов фрезеруют до выведения следов износа, а при значительных износах наплавляют и фрезеруют.
Рис. 76. Притертые поверхности клапана и седла
Изношенным отверстиям под втулку верхней головки шатуна придают развертыванием ремонтный размер (ремонтный интервал 0,25 мм) или растачивают для установки стальной втулки с последующим развертыванием под номинальный размер. При выполнении операций по механической обработке отверстия под втулку и втулки верхней головки шатуна за базовую поверхность принимают уже восстановленное отверстие нижней головки шатуна.
Изношенные втулки головки шатуна восстанавливают меднением, обжатием с последующим осталиванием наружной поверхности. Отверстие нижней головки шатуна двигателей ЗИЛ-130 и ЯМЗ восстанавливают осталиванием или плоскости разъема шлифуют, а отверстие затем растачивают на номинальный размер. Иосле восстановления шатуны комплектуют по массе.
Основные дефекты поршней — это нагары на днище и канавках, износ канавок под кольца по высоте и отверстий в бобышках под пальцы, износ юбки поршня, образование трещин и царапин на стенках.
Нагар удаляют в ваннах с расплавом солей или обработкой косточковой крошкой. Состояние канавок определяют шаблоном (рис. 79). Поршень считается негодным, если соответствующая пластинка шаблона входит в канавку более чем на ‘А глубины. Выбраковывают поршни с износом юбки более допустимого, трещинами, глубокими царапинами. В повторно используемых поршнях отверстия в бобышках развертывают под палец увеличенного размера. Допустимое отклонение перпендикулярности оси отверстия под палец к оси поршня не должно превышать 0,035 мм на длине 100 мм. Допустимое отклонение массы поршней одного комплекта от 4 до 20 г.
Поршни к гильзам подбирают так, чтобы зазор в сопряжении был в пределах 0,03—0,05 мм.
Зазор контролируют в помощью ленты-щупа (рис. 80) толщиной 0,08, шириной 13 и длиной 200 мм. Усилие протягивания ленты определяется ручными пружинными весами.
Рис. 78. Проверка шатуна на изгиб и скручивание:1 — шатун; 2 — разжимная оправка; 3 — призма; 4 — индикатор
Рис. 79. Проверка высоты поршневой канавки шаблоном
Рис. 80. Подбор поршней по цилиндру измерительной лентой с динамометром
Рис. 81. Проверка поршневых колец на просвет
Поршневые пальцы с трещинами выбраковывают, а изношенные более допустимого восстанавливают холодной раздачей (после отжига) с последующей механической и термической обработкой или нанесением пористого хрома. Требуемые размеры и шероховатость пальцам придается шлифовкой и полировкой с пастой ГОИ. Изношенные пальцы увеличенного диаметра можно перешлифовывать на нормальный размер. Допустимая овальность пальцев 0,005 мм. Изношенные или потерявшие упругость поршневые кольца выбраковывают. Взамен их двигатели комплектуют новыми кольцами, которые подбирают по размерам поршня и цилиндра. При подборе колец по поршням щупом проверяют зазор кольца по высоте канавки, который должен находиться в заданных пределах. В случае заедания кольцо шлифуют на мелкозернистой наждачной бумаге.
Подбор колец по цилиндру заключается в определении щупом зазора в стыке и проверке прилегания кольца к стенке цилиндра. Для этого кольцо (рис. 81) устанавливают в эталонную гильзу в плоскости, перпендикулярной оси цилиндра, и при помощи электролампочки просвечиванием определяют зазор, который на длине дуги 60 мм не должен превышать 0,03 мм. Зазор в стыке колец должен быть в пределах: для компрессионных 0,3—0,6 мм, для маслосъемных 0,15—0,45 мм. Поршневые пальцы к поршням подбирают по размерной группе отверстий в бобышках таким образом, чтобы при 20 °С пальцы входили в поршень от усилия руки, а при нагреве поршня в воде до 70 °С входили в него свободно.
Читать далее: Коленчатый вал
Категория: - Эксплуатация и ремонт погрузочночных машин
Главная → Справочник → Статьи → Форум
stroy-technics.ru