Мотор цилиндр клапан шатун
Автомобильный двигатель: основные детали и принцип работы AutoRemka
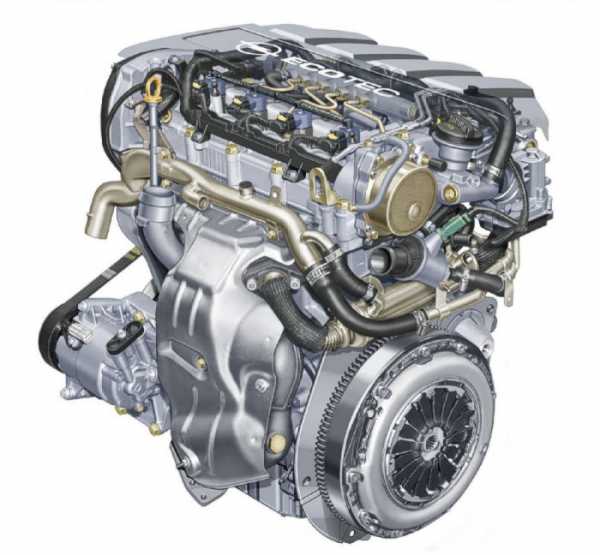
Мотор автомобиля работает на бензине или на каком-либо другом горючем, которое легко воспламеняется. Двигатель машины чаще называют двигателем внутреннего сгорания, так как внутри цилиндра происходит процесс горения топлива.
Детали мотора
Коленчатый вал четырехцилиндрового мотора представляет собой круглые точеные элементы, на которых крепятся шатуны и поршни.
Две головки шатуна – это верхний и нижний подшипники, благодаря которым шатун подвижно крепит меж собой коленчатый вал и поршень.
Поршень – это цилиндрическое тело в двигателя, на которое оказывают воздействия действие газы. Специальные пружинящие кольца служат для того, чтобы удержать внутри газы большого давления. Они устанавливаются в выступах поршня, и называются поршневыми шашками.
В цилиндре мотора автомобиля происходит процесс сгорания топлива и воздуха. Следует отметить, что при этом вырабатывается высокая температура, которая довольно вредно воздействует на цилиндр, поэтому автомобильные цилиндры оборудованы водным охладителем. Для данного действия в верхней части цилиндра имеется двойная стенка, по которой циркулирует вода.
Нужно отметить, что цилиндры мотора машины закрепляются болтами на картере, который одновременно является разъемной коробкой, имеющей посередине коленчатый вал. На нем укреплены прибор зажигания, охлаждения и смазки мотора.
Внутри цилиндра поршень двигается вверх и вниз, вдоль оси, при этом коленчатый вал крутится подшипниками; при помощи шатуна, от поршня движение передается к коленчатому валу. Предназначение клапанов мотора состоит в запуске свежего газа в цилиндр и выпуска из него перегоревшего. Поднятие клапанов происходит с помощью толкателей, которые движутся кулачковыми валиками и связанными с коленчатым валом цилиндрическими шестернями.
В моторе машины происходит сжигание смеси паров бензина (или другого горючего) и воздуха. Отметим, что данная смесь воспламеняется электрической искрой, при этом сама смесь должна хорошо сгорать. Число горючего и воздуха должно составлять около 15 кг кислорода на 1 кг топлива, при этом горючее должно полностью испариться и смещаться с воздухом. Для этого в двигателе имеется карбюратор. К нему по особой трубке из бака поступает топливо, которое, в свою очередь, внутри карбюратора распыляется и смешивается с воздухом в четком количестве.
Чтобы элементы мотора имели меж собой малое трение, в моторе имеется специальный масляный насос, с помощью которого масло подается к трущимся деталям.
Особенности работы двигателя
Итак, мы рассмотрели основные детали двигатели и узнали, что мотор работает за счет внутреннего сгорания горючего в цилиндрах, а также за счет тепла, которое выделяется в процессе этого.
Следовательно, работа двигателя – это общность процессов, а именно: заполнение цилиндра двигателя рабочим раствором, сгорание которого и чистит цилиндр от остатков продуктов сгорания.
Обычно, двигатель машины имеет от двух до двенадцати цилиндров, однако рабочие процессы в них всегда одинаковы. При обороте коленчатого вала вправо, движущийся поршень создает в цилиндре давление газа меньше внешнего. Вал расположен так, что позволяет под толкателем открывать всасывающий клапан. В цилиндр через клапан засасывается консистенция бензина и воздуха, которая образовалась в карбюраторе.
Процесс всасывания необходим для того, чтобы зарядить цилиндр новой рабочей смесью и является первый шагом к запуску мотора. За этот период поршень сделает один ход, а коленчатый вал пройдет половину оборота.
Вал, вращаясь, приводит поршень из нижнего положения в верхнее, а кулачковые валики не подходят к толкателям клапанов, поэтому они остаются прикрытыми, когда поршень движется вверх. В этот момент полость цилиндра не соприкасается с воздухом и внутри цилиндра совершается сокращение консистенции. При верхнем положении поршня сокращение является максимальным, не менее 6—6,5 атмосфер. Это второй шаг рабочего процесса мотора.
Поршень двигается вверх и сжимает рабочую смесь, затем на короткий промежуток времени останавливается в верхнем положении. В этот момент через свечу проходит электрическая искра, которая и воспламеняет смесь. Горючая смесь быстро сгорает, повышая ее температуру и давление до 25—30 атмосфер.
Процедура расширения перегоревших газов и передачи их на коленчатый вал двигателя считается третьим шагом в работе мотора.
Тогда, когда поршень будет приближаться к нижней точке расположения, кулачковый вал развернется так, что его кулачок поднимет выпускной клапан и газы начнут извергаться вовне. Потом клапан остается раскрытым во время всех движений поршня вверх, через него будет выталкиваться с цилиндра перегоревшее топливо.
Эта процедура очистки цилиндра от перегоревшего топлива является четвертым тактом рабочего хода мотора.
Во время того, как поршень за процедуру выталкивания дойдет до собственного верхнего состояния, выпускной клапан прикрывается, так как кулачок уже минует толкач клапана. Кулачок валика к этому времени дойдет к толкателю всасывающего клапана и приоткроет последний, после чего все процессы начнутся сначала, и будут меняться друг за другом — всасывание, сжатие, расширение и выталкивание.
Тут же клапаны открываются по 1 разу, следовательно, за 2 оборота вала кулачки приблизятся по 1 разу к толкателям всасывающего и выпускного клапанов.
Для того, чтобы снизить колебания скорости оборотов коленчатого вала за рабочий процесс мотора, на коленчатый вал прикрепляется большой элемент — маховик. Чем он массивнее, тем правильнее ход двигателя и тем лучше он работает. В многоцилиндровом моторе за 2 оборота коленчатого вала такое количество рабочих ходов равно количеству цилиндров. Иными словами, чем больше имеется цилиндров у мотора, тем плавнее движется автомобиль.
autoremka.ru
Ремонт КШМ и ГРМ — Инструкции по эксплуатации и ремонту автомобилей МАЗ на Мазбука.ру
2.3 Ремонт кривошипно-шатунного и газораспределительных механизмов двигателя
Снятие и установка головки цилиндров
Для замены головки цилиндров и её деталей, а также деталей цилиндропоршневой группы, прокладки головки цилиндров, клапанов и сёдел клапанов снятие головки цилиндров необходимо произвести в следующей последовательности:
слить из системы охлаждения двигателя охлаждающую жидкость;отсоединить все трубопроводы от головки цилиндров и защитить их внутренние полости от попадания пыли и грязи;снять крышку головки цилиндров, а затем форсунки, предохраняя распылители от ударов и засорения отверстий;снять ось коромысел вместе с коромыслами и вытянуть штанги;ослабить гайки крепления головки цилиндров, соблюдая ту же последовательность, что и при затяжке (см.рис 4), а затем отвернуть их;снять головку цилиндров с двигателя и проверить её состояние;снять осторожно прокладку головки цилиндров избегая повреждений, при необходимости при сборке заменить прокладку.
Головку цилиндров заменяют при наличие трещин, проходящих через отверстия под направляющие втулки клапанов, отверстия под стаканы форсунок и гнёзда под сёдла клапанов, трещин на стенках рубашки охлаждения в местах, недоступных для ремонта. Наличие трещин определяется внешним осмотром (Старым (дедовским) испытанным способом проверки является обрызгивание топливом поверхности головки цилиндров между клапанами при работающем двигателе. В местах прорыва, трещин головки наблюдается выход воздуха. Но при этом необходимо проявлять осторожность вследствие снятия крышки клапанов и работе двигателя). Также провести проверку головок цилиндров на герметичность водой под давлением 4кгс/см².
Герметичность рубашки охлаждения можно проверить, подведя к ней воздух и опустив головку цилиндров в ванну с водой. Трещины и пробоины на головке цилиндров не допускаются. Допускаются лишь мелкие трещины на привалочных поверхностях между отверстиями под распылители форсунок и клапаны, не захватывающие рабочие фаски впускного клапана и не нарушающие герметичность. Если при испытании головки цилиндров на герметичность обнаружится нарушение уплотнения стакана форсунки, следует подтянуть гайку крепления стакана. Если при этом течь не устраняется, стакан снимают и заменяют уплотнительное кольцо и шайбу, а в случае необходимости и стакан. Гайку крепления стакана форсунки затягивают моментом 9-11кгс.м. Головку цилиндров устанавливают на двигатель в последовательности, обратной разборке. При этом привалочные поверхности головки блока цилиндров и блока необходимо протереть чистой ветошью, обращая внимание на правильность установки прокладки головки цилиндров на штифты и окантовок прокладки на бурты гильз цилиндров. Гайки крепления головок цилиндров затягивают в порядке возрастания номеров, как показано на рис.4 с приложением момента 22-24 кгс.м. После первой затяжки необходимо повторной операцией проверить требуемый крутящий момент на каждой гайке, соблюдая указанную последовательность.
Замена деталей шатунно-поршневой группы
При нормальных износах деталей цилиндро-поршневой группы (отсутствие трещин, задиров и т. д) поршень, гильзу, палец и кольца, как правило, заменяют одновременно. Поршневые кольца обычно приходится менять чаще, чем весь комплект.
Для снятия поршней и гильз с двигателя необходимо:
установить автомобиль на смотровую канаву и слить масло и охлаждающую жидкость из двигателя;снять головки цилиндров и поддон картера двигателя;отогнуть замковые шайбы и отвернуть болты крепления крышек нижних головок шатунов, убедитесь меток спаренности на стыке со стороны длинного болта (при отсутствии меток или плохой видимости, их необходимо нанести вновь). При сборке замены крышек или переустановка их в другие места не допускается:
снять поршень в сборе с шатуном через цилиндр, а затем гильзы из блока цилиндров при помощи приспособления (см. рис 5).
Для разборки комплекта поршень-шатун необходимо:
снять кольца с поршня специальными щипцами (см.рис 6), ограничивающими расширение кольца до диаметра 142,5мм;вытянуть стопорное кольцо поршневого пальца круглогубцами;вытянуть поршневой палец, предварительно выдержав поршень в сборе с шатуном в масле в течение 10мин при температуре масла 80-100°С.
После разборки поршень и кольца очищают от нагара и промывают (очищают) отверстия для отвода масла. После очистки детали тщательно промеряют и выявляют дефекты.
Замена поршней и гильз
Номинальный зазор между внутренней поверхностью гильзы и юбкой поршня в холодном состоянии должен быть 0,19-0,22мм. Если зазор превышает 0,45мм поршневую группу нужно заменить. Гильзу цилиндров заменяют, если имеются трещины, обломы, задиры внутренней поверхности, вмятины и забоины на буртике, кавитационные раковины выходящие на канавки под уплотнительные кольца, если внутренний диаметр в результате износа превышает 130,18мм (при установке в гильзу поршня с поршневыми кольцами, которые не работали до разборки, диаметр можно увеличить до 130,25мм), овальность и конусность гильзы превышает 0,06мм. Диаметр следует замерять в двух взаимно перпендикулярных направлениях. Поршень заменяют, если есть задиры на боковой поверхности, выгорания на днище поршня, трещины, если диаметр юбки поршня меньше 129,6мм (замер следует делать в плоскости перпендикулярной поршневым пальцам, на расстоянии 153мм от днища поршня), если есть задиры на поверхности отверстия под поршневой палец, диаметр отверстия под поршневой палец превышает 50,03мм, а овальность и конусность отверстия превышает 0,015 мм, торцевые зазоры между новыми поршневыми кольцами и канавками поршня превышает: для верхнего компрессионного кольца (размер «а» рис. 7) 0,35мм, для второго и третьего компрессионных колец (размер «б») 0,30мм, для масленых колец (размер «в») 0,25мм. Для замеров торцевых зазоров поршень в сборе с новыми кольцами вставляют в калиброванную шайбу с внутреннем диаметром 130,00-130,01мм. Замер нужно производить одновременно с двух диаметрально противоположных сторон поршня.
Замена поршневых колец
Поршневые кольца заменяют при расходе масла двигателем, превышающим 3% расхода топлива и повышенном дымление через сапун. Если вышеуказанные явления не наблюдаются, а двигатель по каким – либо причинам поступил в текущий ремонт, то кольца заменяют только при наработке двигателем более 150тыс. км, полностью или частично сработанных канавках на рабочей поверхности второго и третьего компрессионных колец, наличии задиров на внешне цилиндрической поверхности.
Замена поршневого пальца
Поршневой палец заменяют при наличии грубых рисок, задиров, наволакиваний металлов и прожогах, если наружний диаметр менее 49,98мм, а овальность и конусность превышают 0,015мм.
Замена шатуна
Шатун заменяют при наличии трещин. Если внутренний диаметр отверстия головки шатуна (под втулку), который должен быть не более 56,04мм. Проверять диаметр нужно как при ослаблении посадки, так и при повороте втулки. При запрессовке новой втулки натяг должен быть в пределах 0,5-0,12мм. Внутренний диаметр нижней головки шатуна проверяют после контрольной затяжки шатунных болтов с моментом 20-22кгс.м. Предельно допустимый диаметр должен составлять 92,98-93,05мм, если среднее арифметическое диаметров в плоскости стыка и сечении, перпендикулярном стыку, не выходит за пределы 93,00-93,021мм. Ширина нижней кривошипной головки должна быть не менее 41,25мм. При меньшей ширине нижней головки шатуна следует заменить. Непараллельность осей отверстий верхних и нижней головок шатуна (изгиб) без ремонта допускается не более 0,08мм на длине 100мм, а отклонение осей указанных отверстий от положения одной плоскости (скручивание) не более 0,1мм на длине 100мм. Если не параллельность и скручивание осей верхней и нижней головок шатуна выше допустимых, шатун нужно заменить. Допускается установка новой втулки в отверстие верхней головки с последующей расточкой внутреннего диаметра до 50+0,040мм, обеспечив при этом отклонение от параллельности осей не более 0,04мм на длине 100мм, положение осей в одной плоскости в пределах 0,04мм на длине 100мм и расстояние между указанными осями 265±0,04мм. Правка шатуна не допускается. При ремонте запрещается установка крышек с другого шатуна. Проверять шатуны и крышки по меткам спаренности.
Сборка шатунно-поршневой группы
Гильзы цилиндров по наименьшему внутреннему диаметру цилиндра, а поршень по наибольшему диаметру юбки делятся на следующие шесть размерных групп обозначаемых индексами А, Б, В, Г, Е, Ж на верхнем торце гильзы и на днище поршня.
При установке поршни и цилиндры подбираются по одноименным размерным группам. Установка не совпадающих по группам узлов может вызвать задиры на поверхности гильз и заклинивание поршня. Втулки шатуна и поршневой палец перед сборкой необходимо смазать моторным маслом. Поршневой палец устанавливают в поршень после его нагрева в течение 10мин в масленой ванне при температуре 80-100ºС, при этом поршневой палец должен заходить в отверстия от усилия большим пальцем руки. Запрессовка поршневого пальца в поршень не допускается. При сборке поршня с шатуном необходимо отследить направление смещения камеры сгорания. Смещение должно быть направлено в сторону большого болта шатунной крышки. В каждый поршень подбирают три компрессионных и два маслосъемных кольца; наружная цилиндрическая поверхность верхнего компрессионного кольца должна быть хромирована, второе компрессионное кольцо имеет луженые канавки.
Компрессионные кольца устанавливаются на поршень скошенной поверхностью в сторону днища поршня. Тепловой зазор в замках поршневых колец, вставленных в гильзу цилиндра должен составлять 0,45-0,65мм. Просветов между стенками гильзы и поверхностью колец не допускается. При величине зазора менее 0,45мм можно пропилить концы стыка, обеспечив параллельность сторон в сжатом состоянии. Тепловой зазор в замках поршневых колец проверяют щупом; поршневое кольцо должно находиться в 25мм от верхней кромки гильзы. Кольца на поршень устанавливают при помощи специальных щипцов (см. рис 6). Замки смежных колец должны располагаться относительно друг друга под углом 180º.
Установка шатунно-поршневой группы
Перед установкой гильзы в блок цилиндров необходимо тщательно протереть все поверхности, а уплотнительные кольца смазать моторным маслом. Гильзу с уплотнительными кольцами устанавливают в блок усилием руки. Буртики гильз цилиндров должны выступать над поверхность блока на 0,065-0,165мм. Перед установкой поршня с шатунами зеркало цилиндра необходимо тщательно протереть и смазать моторным маслом. Поршень устанавливают в цилиндр так, чтобы камера сгорания была смещена внутрь двигателя (в сторону топливного насоса). Поршневые кольца должны быть обжаты обоймой, внутренний диаметр которой должен быть равен диаметру цилиндра (см рис 8). При сборке шатунных подшипников необходимо, чтобы клейма спаренности на шатуне и крышке были одинаковыми, а риски спаренности совпадали. Болты крепления крышки шатунов затягиваются моментом 20-22кгс.м. Затяжку болтов начинают с длинного болта и выполняют в два приёма, сначала половинным усилием, а затем в полным. Замковые шайбы шатунных болтов при каждой сборке заменяют. После установки шатанно-поршневой группы коленчатый вал должен плавно, без заеданий проворачиваться за головку болта крепления шкива коленчатого вала с помощью рычага длиной 550мм.
Ремонт коленчатого вала
Коленчатый вал заменяют при наличии трещин любого размера и расположения, задиров на шатунных или коренных шейках, при биении коренных шеек, не устраняемых методом шлифования под последний ремонтный размер. Биение средних коренных шеек относительно крайних допускается не свыше 0,08мм. Проверка производится индикатором при установленных на призмы крайних коренных шейках. При износе хотя бы одной коренной или шатунной шейки сверх допустимого (табл. 1), а также при наличие хотя бы на одной из шеек глубоких рисок или задиров все коренные или шатунные шейки перешлифовываются под единый размер. Номер ремонтного размера коренных шеек может отличаться от номера ремонтного размера шатунных шеек. Шлифовка шеек коленчатого вала производится в пределах величин указанных в табл. 1.
При этом необходимо выполнить следующие условия:
переход цилиндрических участков шеек в галтели должен быть плавным (радиус галтели 5,5-6,0мм), без подрезов, прожогов, грубых рисок: шероховатость поверхностей шеек не должна превышать 0,20мкм, шероховатость галтелей не ниже 0,32мкм;величина радиусов осей всех кривошипов вала должна быть 70±0,12мм;не параллельность средних осей коренных шеек относительно общей оси крайних коренных шеек не должна превышать 0,010мм, не параллельность шатунных шеек относительно общей оси крайних коренных шеек не должна превышать 0,015мм;овальность, конусность, вогнутость, бочкообразность коренных и шатунных шеек не допускается более 0,01мм.
Отсутствие трещин проверяется магнитным дефектоскопом с обязательным последующим размагничиванием.
При каждом снятии коленчатого вала с двигателя для замены вкладышей полости шатунных шеек рекомендуется очищать, предварительно удалив заглушки, которыми закрыты полости. Повторное использование заглушек не допускается. Перед установкой заглушек вспученный металл у кромок отверстий от предыдущей раскерновки запиливают, промывают вал и прочищаются масленые каналы. Заглушки запрессовывают на 5-6мм и раскернивают внутри отверстия в трех точках, равномерно расположенных по окружности, для предотвращения само производительного выпрессовывания заглушек.
Шестерню коленчатого вала заменяют при контактном разрушении зубьев, сколах, трещинах, выработке в виде канавок, а также при боковом зазоре в зацеплении с шестерней распределительного вала более 0,3мм. Шестерню коленчатого вала можно заменить без снятия коленчатого вала с двигателя. При снятых шкиве и передней крышке блока передний противовес и шестерня спрессовываются при помощи съемника. Перед установкой шестерню и противовес необходимо нагреть до температуры 105°С произвести последовательную на прессовку.
Замена вкладышей коренных и шатунных подшипников
Коленчатые валы двигателей ЯМЗ обладают высокой износостойкостью. После 80-100тыс.км пробега рекомендуется профилактическая замена вкладышей, которая продлит срок службы коленчатого вала до пере шлифовки. Для замены вкладышей коренных и шатунных подшипников двигатель снимают с автомобиля. Вклады необходимо заменять в условиях исключающих попадание грязи. Новые вкладыши должны иметь номинальные размеры. Шатунные вкладыши меняют по порядку, начиная с первого цилиндра. Снятые вкладыши тщательно осматриваю. При наличии повреждений не свойственных естественному износу, выясняют их причину. Масляные каналы коленчатого вала очищают от загрязнённого масла и отложений, протирают шейку и осматриваю её. Перед установкой вкладышей шейку и вкладыши смазываю моторным маслом. Болты крепления шатунных подшипников затягивают моментом 20-22кгс.м. Вкладыши коренных подшипников можно заменить при помощи штифта. Штифт представляет собой стальной стержень длиной 250мм, диаметром 6мм и имеет головку диаметром 15мм, высотой 3мм. Для снятия верхнего вкладыша коренного подшипника, штифт вставляют в отверстие масленого канала коренной шейки. Для выталкивания вкладыша коленчатый вал вращают. Для установки вкладыша в постель его накладывают на шейку и усилием руки частично вводят в зазор между шейкой и постелью. Затем штифт вводят в отверстие масленого канала и проворачивают вал до полной установки вкладыша. Вертикальные болты крышек коренных подшипников затягивают с приложением момента 43-47кгс.м, а горизонтальные – 10-12кгс.м.
Необходимость замены вкладышей определяется величиной износа по толщине и диаметральным зазором в сопряжении (табл. 2). Если износ по толщине превышает 0,05мм или диаметральный зазор более 0,23мм, вкладыши заменяют новыми. Толщина вкладыша измеряется по его середине. Зазор проверяют измерением толщины шейки коленчатого вала и внутреннего диаметра подшипника (после затяжки болтов крепления крышки). Вкладыши также заменяются при наличие механических повреждений.
При повторной установке вкладышей, их устанавливают только на старое место. Верхний вкладыш имеет канал и отверстие для подвода и разбрызгивания масла. Вкладыши нижней головки шатуна взаимозаменяемые.Для ремонта шатуна предусматривается шесть ремонтных размеров вкладышей. Клеймо размера нанесено на тыльной стороне вкладыша недалеко от стыка. Номер ремонтного размера вкладыша должен соответствовать номеру ремонтного размера шейки коленчатого вала. Вкладыши подшипников коленчатого вала следует менять целиком во всём двигателе.
Восстановление герметичности клапанов
Для восстановления герметичности клапанов нужно снять головку (или головки) блока цилиндров снять с двигателя. Очистить их от грязи и масла, нанести на тарелки клапаном метки для установки их при сборке на старое место. Пользуясь приспособлением (рис. 9) сжать пружины клапанов и вытащить сухари клапанов, снять клапан, тщательно очистить их от нагара, промыть в керосине, определить степень износа. При незначительных износах и раковинах на клапане и седле, клапан восстанавливается притиркой клапана и седла пастой, которая приготавливается перемешиванием 1,5 частей (объема) микропорошок зелёного карбида кремния 63С-М28 ОСТ 2-144-71 с одной частью летнего моторного масла и 0,5 части дизельного топлива Л-0,2-40 ГОСТ 305-82.
Процесс притирки состоит из вращательно-поступательного движения при помощи специального инструмента (притирочная дрель), либо в ручную с использованием зажима. Вращение должно выполняться в различных направлениях по ½ оборота с возможностью поступления пасты под фаску. Внешним признаком нормальной притирки является наличие матового пояска на клапане и седле не менее 1,5мм. Разрывов, рисок на пояске не допускается. После притирки клапан промывают в керосине, вытирают и устанавливают. Проверяют герметичность залив керосин во впускные и выпускные окна и выдержав 3мин. При любом повороте клапана, не должно быть протечек и потёков. Правильность притирки можно проверить при помощи графита. Для этого на фаску мягким грифелем карандаша нанося 10-15 рисок через одинаковые промежутки. Клапан вставляют в седло, сильно нажимают на него и делают поворот на ¼ оборота. Грифель после этого должен быть стёрт. Если не удаётся добиться герметичности притиркой, то производится прошлифовка клапана и седла процедура притирки повторяется. Для шлифовки клапана применяется шлифовочные устройства или электродрели. Шлифовку седел производят специальными головками. Если необходимо произвести замену направляющих втулок клапана, то шлифовку седла производят только после их замены.
Ремонт клапанных седел
Риски, выработки и вмятины от нагара на седле устраняются методом зенкерования и шлифовки фаски седла, обеспечив минимальное снятие металла. Предельное утопание тарелок нового клапана от плоскости головки при восстановлении фаски седла допускается: 2,5мм для впускного клапана; 3,0мм для выпускного. Режущий инструмент должен иметь фиксацию во внутренней втулке клапана, для совмещения соосности клапана и фаски седла в пределах 0,025мм (биение 0,05мм).
Обработку фаски впускного клапана производить в следующем порядке:
фрезеровать рабочую фаску зенкером под углом 120° (рис 10, а) до получения чистой и ровной поверхности;фрезеровать нижнюю кромку рабочей фаски зенкером под углом 150° (рис 10, б), выдерживая рабочую фаску в пределах 59,4 +0,7мм;фрезеровать верхнюю кромку фаски зенкером под углом 60° (рис 10, в) до получения ширины фаски, равной 2,0-2,5мм.Обработку фаски выпускного клапана производить в следующем порядке:
фрезеровать рабочую фаску зенкером под углом 90° (рис 11, а) до получения чистой и ровной поверхности;фрезеровать нижнюю кромку рабочей фаски зенкером под углом 150° (рис 11, б), до получения ширины фаски, равной 1,5-2,0мм.
Риски и незначительную выработку на сёдлах клапанов устраняется шлифовкой и притиркой. Если невозможно получить ширину рабочей фаски на седле выпускного клапана, равной 1,55-2,0мм, а также при наличии прогара, трещин, раковин и других дефектов седла выпускного клапана, не устраняемых обработкой, седло необходимо заменить. При запрессовке нового седла головку цилиндров нагревают в кипящей воде до 90°С. Запрессовывают седло лёгким ударами молотка через мягкую (медную, латунную) проставку, обеспечив натяг не менее 0,02мм. Прилегание седла к головке цилиндров проверяют щупом. Щуп толщиной 0,05мм проходить не должен. Если необходимо заменить направляющие втулки клапанов, то рабочие фаски на седлах клапанов шлифуют после замены втулок. Направляющие втулки клапана при износе внутреннего диаметров более чем 12,06мм заменяют новыми. После запрессовки новую втулку развертывают на размер 12+0,019мм. Выступание втулки из тела головки должно быть 32±0,5мм.
Замена впускного клапана
На рабочей поверхности тарелки не допускается наличие рисок, раковин, углублений.
Если имеются данные дефекты, то рабочую поверхность клапана необходимо перешлифовать, выдержав толщину цилиндрической тарелки на менее 0,75мм, угол 121-122°, шероховатость поверхности не ниже 1,25мкм, биение рабочей поверхности относительно стержне не более 0,03мм. Износ стержня допускается до 11,92мм.
Замена выпускного клапана
На рабочей поверхности тарелки не допускается наличие рисок, раковин, углублений. Если имеются данные дефекты, то рабочую поверхность клапана необходимо перешлифовать, выдержав толщину пояса цилиндрической поверхности тарелки на менее 1,00мм, угол 91-92°, шероховатость поверхности не ниже 0,63 мкм, биение рабочей поверхности относительно стержне не более 0,03мм. Отклонение при проверке стержня клапана от прямолинейности допускается не более 0,01мм. Износ стержня допускается до 11,68мм.
Замена штанг, коромысел и их осей
Коромысло заменяют при обнаружении трещин или обнаружении облома. При износе отверстия под ось коромысла до диаметра 25,15мм заменяют только втулку. Кроме того, втулку заменяют при прославлении её посадки в коромысле. Посадку проверяют лёгким ударом через медную выколотку. Новая втулка должна утопать в тело коромысла по 1мм с каждой стороны. Масленые отверстия во втулке и коромысле должны совпадать, а стык втулки должен находиться в верхней части отверстия. После запрессовки втулки необходимо развернуть под размер 25+0,025мм.
Ось коромысла бракуют при наличие трещин или облома. Допускается износ оси до диаметра 25,00мм.Штанга толкателя не должна иметь задиров или выкрашивания цементированного слоя на рабочих поверхности наконечников. Погнутость штанги проверяют индикатором на призмах. Если биение штанги превышает 0,5мм, её необходимо править. После сборки необходимо проверить тепловые зазоры в клапанном механизме и при необходимости отрегулировать их.
mazbuka.ru
Часть 1 — Кривошипо-шатунный механизм
Итак, наша первая задача это понять, что же такое двигатель (Engine). Результатом работы двигателя является наличие крутящего момента на его коленчатом валу.
Двигатель состоит из двух механизмов:
1- Кривошипно-шатунный механизм (КШМ, Crank mechanism) предназначен для преобразования возвратно-поступательного движения поршня в цилиндре во вращательное движение коленчатого вала двигателя.
2 — Газораспределительный механизм (ГРМ, gas distribution mechanism) предназначен для своевременного снабжения двигателя горючей смесью, а так же для выпуска выхлопных газов.
В данной части разберём те детали двигателя, которые относятся к КШМ. Забегая вперёд, оглашу весь список тех деталей, из которых состоит КШМ.
Итак, Кривошипно-шатунный механизм состоит из:
- Коленчатый вал
- Маховик
- Шатуны
- Поршни с кольцами и пальцами
- Блок цилиндров с картером
- Головки блока цилиндров,
- поддона картера двигателя
Если результатом работы является наличие крутящего момента на коленчатом валу, следовательно одна из деталей двигателей это Коленчатый Вал.
1. Коленчатый Вал(crankshaft)
Коленчатый вал представлен на рисунке снизу:
Коленчатый вал двигателя с маховиком состоит из:1 — коленчатый вал двигателя; 2 — маховик с зубчатым венцом;3 — шатунная шейка; 4 — коренная (опорная) шейка; 5 — противовес
Маховик (flywheel) — это массивный металлический диск, который крепится на коленчатом валу двигателя. маховик всегда пытается сохранить то состояние, из которого его выводят. Он долго набирает обороты, сглаживая тем самым скачки. Так же долго сбрасывает обороты. Короче говоря, благодаря своей инертности, создает плавность в переходах с одной частоты вращения на другую. Кроме того, его инертность играет роль аккумулятора энергии. Уж если вы раскрутили маховик, затратив при этом работу, он в состоянии такую же работу выполнить, пока не остановится. Грубо говоря, это некий стабилизатор, который предохраняет работу двигателя от скачков и ударов.
Теперь, давайте уделим внимание шатунной шейке. Такое название она имеет потому, что на ней крепится шатун.
2. Шатун(connecting rod)
Шатун (connecting rod) — подвижная деталь кривошипно-шатунного механизма двигателя, соединяющая поршень и коленвал и передающая усилие от поршня к коленчатому валу Двигателя Внутреннего Сгорания(ДВС), преобразуя поступательное движение поршня во вращательное движение коленчатого вала.
Коленчатый вал и детали шатунно-поршневой группы представлены на рисунке снизу:
1 – коленчатый вал; 2 – вкладыш шатунного подшипника; 3 – болт крепления крышки шатуна; 4 – поршневой палец; 5 – стопорное кольцо; 6 – втулка головки шатуна; 7 – шатун; 8 – крышка шатуна; 9 – гайка крепления крышки шатуна
Итак, значит на коленчатом валу крепится шатун. А шатун, в свою очередь соединён с поршнем.
3. Поршень(piston)
Поршень — деталь кривошипно-шатунного механизма двигателя, непосредственно воспринимающая давление от сгорающей в цилиндре рабочей смеси
Поршень представлен на рисунке снизу:
Поршень состоит из:1 — головка поршня; 2 — Юбка поршня; 3 — Первое компрессионное кольцо; 4 — второе компрессионное кольцо; 5 — маслосъёмное кольцо; 6 — поршневой палец; 7 — стопорное кольцо.
Поршневые кольца по назначению разделяют на компрессионные кольца и маслосъемные кольца. Компрессионные кольца предотвращают порыв газов изкамеры сгорания в картер. Наружный диаметр кольца в свободном состоянии больше внутреннегодиаметра цилиндра, поэтому часть кольца вырезана. Вырез в поршневом кольценазывают замком.Маслосъемные кольца препятствуют проникновению масла из картера в камерусгорания, снимая излишки масла со стенки цилиндра. Их устанавливают ниже уровнякомпрессионных. Они в отличии от компрессионных колец имеют сквозные прорези.Основная задача второго компрессионного кольца — обеспечение дополнительного уплотнения после верхнего кольца.
Итак, что мы имеем? Мы имеем коленчатый вал, на котором крепятся шатуны, соединённые с поршнями. Выглядит всё это примерно вот так:
И что дальше? А дальше мы видим нечто синее. Что это? Это гильзы цилиндров.
4. Гильзы цилиндров(sleeves of cylinders)
Внутренние стенки цилиндра образуют гильзу цилиндра, а внешние, более тонкие, стенки – его рубашку(Рубашка охлаждения — cooling jacket). Так что можно сказать, что гильза цилиндра — составная часть цилиндра. Стенки рубашки охватывают гильзовую часть цилиндра так, что между ними образуется полость для циркуляции охлаждающей жидкости.
Существует два вида гильз:
1 — Вставки, запрессовываемые на всю длину цилиндране соприкасаются с охлаждающей жидкостью, вследствие чего их называют сухими гильзами
2 — Легкосъемные гильзы устанавливают в цилиндры свободно с гарантированным зазором (≈ 0,08 мм). Это большое их достоинство. В случае износа их легко заменяют новыми или другими, заранее отремонтированными. Легкосъемные гильзы непосредственно омываются охлаждающей жидкостью, циркулирующей в рубашке охлаждения, в связи с чем их называют мокрыми гильзами
Итак, теперь мы имеем коленчатый вал, на котором крепятся шатуны, на которых крепятся поршни. Поршни, в свою очередь, ходят внутри цилиндров, а точнее внутри гильз цилиндров. Отлично, но маленькое но. Как же всё это держится и в чём? А всё это устанавливается в блок-картер.
5. Блок картер(cylinder block/engine block/crankcase)
Картер является главным из элементов остова (корпуса) двигателя. С внешней стороны к нему крепят цилиндры, а внутреннюю его полость занимает коленчатый вал с его опорами. В картере размещают также основные устройства механизма газораспределения, различные узлы системы смазки с ее сложной сетью каналов и чаще всего с емкостью для смазочного масла и другое вспомогательное оборудование. К одной из торцовых стенок картера в автомобильных двигателях крепят кожух маховика, к боковым – кронштейны или лапы для установки двигателя на подмоторную раму.
Для большей жесткости внутри кратера сделаны поперечные перегородки – ребра, в которых выполнены гнезда для опорных подшипников коленчатого и распределительного валов.
В общем случае блок-картер представляет собой сложную пространственную конструкцию коробчатой формы, которая воспринимает все силовые нагрузки, возникающие в процессе осуществления рабочего цикла, действующие на остов двигателя.
Блок-картер показан на рисунке снизу:
Вид блока-картера зависит от двигателя(число цилиндров и их расположение). Сверху приведена картинка живого блока-картера, чтобы было понятно, как оно выглядит )
А вот блок-картер уже другого по виду двигателя:
К обработанным плоскостям блок-картера крепят составные детали остова двигателя (См.рисунок снизу): сверху — головки цилиндров, сзади — картер маховика 13, впереди — картер распределительных шестерен 7, снизу — поддон картера 11.
6. Поддон картера(sump)
Поддон картера защищает кривошипно-шатунный механизм от попадания грязи и одновременно является резервуаром для масла. Поддон крепится к картеру болтами, для уплотнения устанавливается картонная или пробковая прокладка. В нижней части поддона для слива есть отверстие, закрываемое пробкой.
7. Храповик (ratchet)
На самом деле, этот пункт я решил добавить после написания статьи. Мы уже узнали, как выглядит коленчатый вал, не правда ли? Так вот, при дальнейшем чтении других разделов возникнет вопрос (он обязательно возникнет), а как же от коленчатого вала берут привод остальные механизмы? А всё потому, что абсолютное большинство (если не все, за что моя лютая ненависть к ним) «писателей» не удосуживаются это объяснить. Так давайте разберёмся. Итак, взглянем на рисунок:
1 — Коленчатый вал; 2 — Крышка коренного подшипника; 3 — Звездочка коленчатого вала; 4 — Шкиф коленчатого вала; 5 — Шпонка шкива и звездочки коленчатого вала; 6 — Храповик; 7 — Передний сальник коленчатого вала; 8 — Крыщка привода механизма газораспределения; 9 — Шкив генератора; 10 — Звездочка валика привода вспомогательных агрегатов; 11 — Ремень вентилятора,водяного насоса и генератора; 12 — Валик привода вспомогательных агрегатов
Отсюда понятно крепление. Более менее) При показанном исполнении двигателя на коленчатом валу 1 крепится звёздочка коленчатого вала 3, от которой берёт свой привод распределительный вал системы газораспределения(о ней рассказано в следующей статье). Так же установлен сальник 7, который служит для герметизации. На вал устанавливается шкиф 4. Всё это дело крепится при помощи шпонки 5 и храповика 6.
А что такое храповик? Храповик — зубчатый механизм прерывистого движения, предназначенный для преобразования возвратно-вращательного движения в прерывистое вращательное движение в одном направлении. Проще говоря, храповик позволяет оси вращаться в одном направлении и не позволяет вращаться в другом.
Теперь, переместимся выше по блоку картеру.
8. Головка блока цилиндров(Head of cylinder block)
Головка блока цилиндров — общая для всех цилиндров. Головка крепится к блоку-картеру болтами. Между блоком и головкой установлена металлоасбестовая прокладка. Затяжку болтов головки производят на холодном двигателе, так как требуемое уплотнение обеспечивается только за счет некоторого предварительного натяжения, учитывающего разницу коэффициентов линейного расширения болтов и головки блока.
В головке блока цилиндров имеются камеры сгорания, впускные и выпускные каналы, резьбовые отверстия для установки свечей зажигания и протоки для охлаждающей жидкости. Седла и направляющие втулки клапанов, изготовленные из специального жаростойкого чугуна, вставляют в предварительно нагретую головку охлажденными, благодаря чему после уравнивания температуры обеспечивается большое натяжение в соединении.
Вот мы и узнали, что из себя представляет часть сердца автомобиля, называемая кривошипо-шатунным механизмом. Теперь мы знаем, что двигатель состоит из блока-картера, в котором установлен коленчатый вал с маховиком. На коленчатом валу крепятся шатуны, а на шатунах крепятся поршни. Поршни, в свою очередь, ходят в гильзах цилиндров. Всю эту конструкцию накрывает головка блока цилиндров. Последнее же служит началом для рассказа про другую сторону двигателя — газораспределительный механизм. О нём я напишу в следующем сообщении.
Советую видео для закрепления:
P.S. Жду ваших пожеланий, предложений, мнений и замечаний.
Понравилось это:
Нравится Загрузка...
whatisvehicle.wordpress.com
Масляное голодание, Гидроудар, задиры в циллиндрах - что и почему
МЕТОДИКА ОПРЕДЕЛЕНИЯ ПРИЧИНЫ НЕИСПРАВНОСТИ ДВС ПРИ ТЯЖЕЛЫХ ЭКСПЛУАТАЦИОННЫХ ПОВРЕЖДЕНИЯХ.Представлен общий подход к исследованию причин неисправностей ДВС, возникающих при нарушении кинематической связи между вращательно и поступательно движущимися деталями, что приводит к тяжелым повреждениям и разрушениям деталей. Показано, что определение причины неисправности при данном виде разрушений представляет собой наибольшую сложность для исследования в связи с большим количеством обломков и значительной деформацией деталей. На конкретных примерах рассмотрены основные причины тяжелых повреждений ДВС, среди которых как эксплуатационные повреждения при попадании жидкости в цилиндр и масляном голодании, так и производственные дефекты, возникающие при изготовлении и/или сборке клапанного механизма и поршневых пальцев. Приведены и проанализированы основные признаки рассматриваемых видов повреждений, на основании разделения этих признаков на главные, подтверждающие и уточняющие разработана простая методика определения причин неисправности при тяжелых повреждениях ДВС.
Постановка задачи
Большие усилия и средства, вкладываемые в научные исследования, проектно-конструкторские работы и производство ДВС, нередко не соответствуют сложности проблем, возникающих в эксплуатации ДВС. В результате наблюдается определенный разрыв между производителем и эксплуатантом транспортных средств, когда производитель не всегда имеет достоверную информацию о неисправностях, возникающих при эксплуатации его продукции. Одним из факторов, препятствующих получению такой информации, является отсутствие методик, с помощью которых можно было бы определять причины неисправностей с необходимой степенью достоверности. Особенно это касается тяжелых повреждений, когда большое количество разрушенных деталей и деформация обломковпрепятствуют правильному выявлению причинноследственных связей. Цель работы - разработка методики для определения причин неисправностей ДВС в эксплуатации при тяжелых повреждениях.
Особенности повреждений ДВС и их исследований
К тяжелым повреждениям можно условно отнести такие, при которых происходит нарушение связей между вращательно и поступательно движущимися деталями, в том числе, при разрушении поршней, шатунов и клапанов, что сопровождается пробоем стенок блока цилиндров, деформацией стенок головки цилиндра, разрушением других узлов и деталей (маслонасос, распределительный вал, поддон картера) и обычно приводит к потере двигателем ремонтопригодности.Все первичные разрушения деталей ДВС, очевидно, носят усталостный характер и связаны, главным образом, с нештатным (нерасчетным, не предусмотренным конструкцией) ростом нагрузок на деталь в результате некоего ее начального повреждения [1-12]. Вторичное разрушение деталей, сопряженных и/или взаимодействующих с первично разрушенной, напротив, носит мгновенный, ударный и хрупкий характер и вызвано превышением предела временной прочности материала деталей в результате их вторичного взаимодействия с образовавшимися обломками. Многолетняя практика расследования различных видов неисправностей ДВС [5,7,9] показывает, что наиболее распространенными тяжелыми повреждениями ДВС и их причинами являются (рис.1):1) деформация и последующее разрушение стержня шатуна в результате попадания жидкости в полость цилиндра (т.н. гидроудар),2) разрушение шатунного подшипника и кривошипной головки шатуна вследствие масляного голодания,3) разрушение клапана преимущественно из-за ошибок сборки, 4) разрушение поршневого пальца при наличии производственного дефекта.
Одной из главных проблем в случае возникновения неисправностей и повреждений ДВС в эксплуатации и необходимости установления их причины является отсутствие методик исследования, что связано с трудностями объективного характера – например, сложностью или даже невозможностью, в отличие от научных исследований процессов и конструирования ДВС, формализовать процессы, а при их моделировании выявлять закономерности, пригодные для составления универсальных методик [1]. Трудности вносят и особенности конструкции ДВС различных типов, что требует сбора статистических данных по характеру и особенностям неисправностей и разрушений для конкретных марок и моделей ДВС. Тем не менее, для тяжелых повреждений может быть предложена простая методика, по которой причина неисправности определяется достаточно точно. Для этого необходимо рассмотреть признаки каждого вида поврежденийболее подробно.
Тяжелые повреждения ДВС при попадании жидкости в цилиндр
В подавляющем большинстве известных случаев в цилиндр попадает вода, прошедшая через систему впуска в результате проезда транспортнымсредством глубоких луж, падения в водоемы, затопления и проч. [5]. Однако возможно попадание в цилиндр и других жидкостей – топлива из неисправных форсунок и агрегатов топливной системы, масла из неисправных агрегатов систем турбонаддува или при длительном нахождении транспортного средства в нештатном перевернутом положении. Прочие случаи, например, попадание в цилиндр охлаждающей жидкости, встречаются крайне редко и связаны, главным образом, с натеканием ее в цилиндр при нарушении технологии ремонтных работ. Жидкость, попавшая в цилиндр, естественным образом занимает объем сжимаемого воздуха. На такте сжатия это приводит к резкому возрастанию давления в цилиндре и нагрузок на шатуннопоршневую группу. При большом по сравнению с объемом камеры сгорания количестве попавшей в цилиндр жидкости и продолжении вращения коленвала по инерции происходит осевое сжатие шатуна вдоль стержня с потерей им устойчивости, а также деформация юбки поршня от чрезмерных нагрузок. Данное явление получило название "гидроудар", и, хотя такое название не вполне отражает суть происходящих процессов, ниже именно оно будет использовано для краткости. В зависимости от степени деформации стержня шатуна после гидроудара возможны различные варианты дальнейшего развития событий. Так, при сильной деформации коленчатый вал будет заклинен вследствие упора поршня, расположенного на укороченном шатуне, в противовесы при подходе к НМТ, или, реже – при упоре сильно деформированного стержня шатуна в нижний край цилиндра. При средней (условно) деформации стержня шатуна двигатель сохранит работоспособность, новследствие уменьшения степени сжатия и компрессии нарушится баланс мощностей по цилиндрам (возникнет неравномерность работ двигателя и потеря мощности), а также появится стук. И только при слабой деформации никаких явных признаков повреждения может не проявиться вообще.
Общим для средней и слабой деформации шатуна является появление при дальнейшей эксплуатации нештатных изгибающих нагрузок на деформированный стержень шатуна, при наличии которых стержень практически неизбежно разрушится от усталости через определенное время эксплуатации (рис.2).Современные системы самодиагностики некоторых транспортных средств позволяют зафиксировать и идентифицировать момент начального повреждения данного типа (например, по самопроизвольному останову ДВС при гидроударе, скачкообразному изменению параметров и т.д.), при этом даже можно получить точное время от начального повреждения до усталостного разрушения шатуна. Однако использовать эти данные для создания каких-то количественных закономерностей невозможно из-за влияния особенностей конструкции конкретных ДВС, режимов работы после повреждения, особенностей записи и хранения информации вбольшинстве систем самодиагностики (в том числе, стирание информации после снятия питания) и, как следствие, значительных трудностей в сборе необходимой статистики.
В результате чаще всего эксперт исследователь сталкивается только с конечным результатом гидроудара, а именно, с большим количеством обломков шатуна, поршня и блока цилиндров [1,5,6]. При этом решить прямую задачу, а именно только по характеру разрушения (излома) отдельных деталей определить причину, по которой они превратились в обломки, невозможно. Для правильного определения причины необходимо решать обратную задачу, а именно – установить признаки, которые появились на деталях вследствие их начального повреждения еще в то время, когда детали сохраняли работоспособность. Тогда, если знать и обнаружить все такие признаки, можно установить не только факт, но и причину гидроудара. Например, несмотря на то, что шатун мог превратиться во множество обломков, величину деформации шатуна, которую он имел до разрушения, всегда можно легко измерить.
Совершенно очевидно, что у поршня, "осевшего" из-за осевого сжатия шатуна, верхнее поршневое кольцо не доходит до своего штатного положения в ВМТ, в результате чего пояс нагара в верхней части цилиндра при сгорании топлива расширяется вниз на величину осевого сжатия стержня шатуна (рис.3). При исследовании пояса нагара практически всегда можно установить, что начальное положение верхнего кольца в ВМТ было штатным, однако затем изменилось. Такое изменение и является главным (уникальным) признаком гидроудара [5]. Есть и другие признаки гидроудара, которые можно условно разделить на подтверждающие (главный признак) и уточняющие (тип жидкости, попавшей в цилиндр). Подтверждающими признаками являются те, которые, так же как и главный признак, говорят о деформации шатуна и работе ДВС с деформированным шатуном. К таким признакам относятся, в том числе, диагональный износюбки поршня, деформация юбки, след стертого нагара над отверстием поршневого пальца на поршне и на ответной поршню верхней части цилиндра, износ края торцов поршневого пальца и ответный износ стопорного кольца от ударов пальца, разбивание канавки стопорного кольца, повреждение нижнего края юбки и бобышек поршня при задевании им противовесов в НМТ, диагональный износ шатунных подшипников, измененный цвет нагара на днище поршня и на камере сгорания по сравнению с другими цилиндрами и некоторые другие. Однако ни один из указанных признаков не устанавливает тип жидкости, попавшей в цилиндр– для этого нужны уточняющие признаки.
Так, при попадании в двигатель воды (водяной гидроудар) уточняющими признаками будут коробление гофров воздушного фильтра, следы намокания на картоне фильтра (рис.4), следы высохших капель воды под крышкой фильтра, в гофрах воздуховодов и на дроссельной заслонке, а также нередко кольцевые следы коррозии на поверхности цилиндра в зоне остановки поршневых колец. Гидроудар от натекания в цилиндр топлива (топливный гидроудар) и попадания в цилиндр масла (масляный гидроудар) случаются намного реже, при этом имеется определенная сложность выделения уточняющих признаков этих видов гидроудара, поскольку масло и топливо не оставляют следов на деталях. Тяжелые повреждения ДВС при разрушении выпускного клапана Основная причина разрушения клапанов – это ошибки при ремонте и обслуживании, причем конструкции клапанных механизмов современных автомобильных ДВС стали особенно чувствительны к таким ошибкам в связи с всеобщим уменьшением диаметра стержня клапана (до 5 мм). В практике ремонта встречаются два основных вида разрушения клапанов, а именно, обрыв стержня в верхней части по канавке для сухаря и отрыв головки клапана от стержня в нижней части [9,10,11]. Так же как и в случае гидроудара, пытаться определить причину такой неисправности только по характеру разрушения отдельных деталей, превратившихся в многочисленные деформированные вторичными ударами обломки, совершенно бессмысленно, и в данном случае следует решать обратную задачу – выявлять признаки, соответствующие конкретной причине, чтобы затем подтвердить эту причину по совпадению признаков. Главным признаком неисправности данноговида, очевидно, является отсутствие головки клапана на ее штатном месте в седле (рис.5). Однако в отличие от главного признака гидроудара, отрывголовки может иметь не только первичный (усталостное разрушение), но и вторичный характер (мгновенное ударное разрушение от взаимодействия с обломками поршня)
Поэтому для определения причины разрушения данного типа не менее важны подтверждающие признаки, например, имеются ли следы ударов клапанов на поршнях соседних цилиндров (рис.6), разрушен ли шатун и поршневой палец, поврежден или полностью разрушен поршень, а также какова степень износа кривошипной головки шатуна и шатунного подшипника.
Очень важными для исследования данного вида неисправности являются уточняющие признаки локализации разрушения. Так, если стержень клапана остается в направляющей втулке, то разрушение произошло в нижней части стержня с отделением от него головки клапана, причиной чего являются ударные изгибающие нагрузки на головке клапана [2]. Тогда уточняющие признаки – это следы ударов головки клапана на днище всех поршней (рис.6), а также усталостный характер излома в нижней части стержня клапана. Если же в цилиндре имеются фрагменты разрушенного стержня клапана (рис.6), это показывает, что разрушение произошло по канавке для сухарей, причиной чего является некачественная сборка (попадание в сопряжение грязи или использование изношенных старых деталей). Тогда после разрушения клапана тарелка пружины сохраняется неповрежденной в сборе с сухарями и обломком стержня, а излом стержня по канавке имеет специфическую микроструктуру (с включениями частиц материала направляющей втулки [10]), что говорит о чрезмерных изгибающих нагрузках в зоне сопряжения сухарей со стержнем.
Тяжелые повреждения ДВС вследствие масляного голодания
Данная неисправность возникает при нарушении подачи масла по различным причинам, среди которых преобладают эксплуатационные [1,3,7]. Главный признак неисправности – это усталостное разрушение шатуна по кривошипной головке, оно происходит вследствие износа, перегрева и разрушения шатунного подшипника с потерей прочности кривошипной головки шатуна при одновременном появлении ударных нагрузок от больших зазоров в подшипнике. Разрушение (в том числе, болтов крышки шатуна) обычно происходит с повреждениями и/или пробоем стенки блока цилиндров, блока крышек коренных опор (если крышки в одном блоке), масляной форсунки (если они есть в конструкции двигателя) и даже маслонасоса с поддоном картера. У двигателей старой конструкции снижним расположением распредвала может быть разрушен и распредвал.
Подтверждающие признаки данной неисправности – это, очевидно, полное или частичное разрушение вкладыша, износ и перегрев шейки коленвала и кривошипной головки шатуна (рис.7), а также повреждение днища поршня от ударов по головке цилиндров (из-за смещения шатуннопоршневой группы вверх при разрушении вкладыша), что в некоторых случаях приводит к частичному или даже полному разрушению поршня. Уточняющие признаки локализуют саму причину неисправности, среди них наиболее распространенными являются недостаточный уровень масла, неисправность маслонасоса, засорение маслоси-стемы отложениями, а также различные ошибки при ремонте и прочие причины.
Тяжелые повреждения ДВС при разрушении поршневого пальца
С разрушением поршневого пальца связаны очень тяжелые повреждения ДВС обычно в начальный период эксплуатации. Разрушение данного вида характерно для случая, когда в отверстии пальца после механической обработки остаются нештатные, т.е. не предусмотренные конструкцией, концентраторы напряжений. Такие концентраторы могут появиться при нарушениях технологического процесса – например, когда при обработке перехода между внутренними поверхностями ступенчатого отверстия не выдержан радиус, или когда вместо одной галтели выполнены две (рис.8).
Концентраторы напряжения в отверстии обычно расположены в средней части пальца, опирающейся на поршневую головку шатуна. Поскольку нагрузки на палец в этой области знакопеременны и по величине близки к максимальным, наличие концентраторов приводит к появлению усталостной трещины и ее распространению в поперечном направлении. Появление трещины сопровождается увеличением деформации пальца (поскольку трещина "дышит"), что может вызвать слабый посторонний звук в двигателе, однако поскольку этот звук, а тем более его причину выявить до разрушения пальца не представляется возможным, предотвратить разрушение, и его последствия обычно также невозможно. После разделения пальца на два фрагмента происходит резкое изменение характера нагрузок на бобышки поршня. Один из фрагментов – меньший, расположенный в одной из бобышек поршня, обычно полностью выходит из контакта с шатуном, что также полностью разгружает эту бобышку от каких-либо сил. Однако другой фрагмент – больший, оказывается по-прежнему в сопряжении ипоршня, и шатуна, но не симметрично, а консольно. Это приводит к появлению в сопряжении чрезмерно высоких перекашивающих нагрузок (рис.9).За счет перекоса на бобышке остаются характерные зоны деформации. Так, у внутреннего края отверстия бобышки это сравнительно широкая зонас блестящей поверхностью в направлении вверх и вниз, которую оставляет фрагмент пальца, установленный в поршневую головку шатуна, при взаимодействии с бобышкой. Ближе к наружному краю отверстия бобышки наблюдаются узкие отпечатки от воздействия кромки поршневого пальца (рис.9), которые при постепенном осевом перемещении фрагмента превращаются в характерные мелкие "ступеньки". Выдержать подобные нештатные нагрузки не сможет ни поршневая головка шатуна, ни бобышка поршня, однако на практике разрушение (вследствие так называемой малоцикловой усталости) всегда происходит по бобышке поршня. Дальнейшее взаимодействие шатуна с отделенным от него поршнем быстро приводит к их дальнейшему разрушению, в которое могут быть втянуты блок цилиндров и клапаны. Достаточно близкой по характеру повреждений и последствий разновидностью данной неисправности является нарушение осевой фиксации поршневого пальца в бобышках поршня, причем картина разрушений в данном случае может быть настолько близка к описанной выше, что позволяет объединить обе неисправности в общую, связанную с поршневым пальцем. Нарушение осевой фиксации пальца также является производственным дефектом, поскольку вызывается, как правило, некачественным ремонтом (ремонтным производством), причем возможны два варианта в зависимости от способа фиксации пальца. Так, для плавающего пальца это выскакивание стопорного кольца из канавки в отверстии бобышки поршня из-за износа от чрезмерных ударных нагрузок на стопорное кольцо или неправильной его установки. Для неподвижного пальца нарушение фиксации связано с его смещением в отверстии поршневой головки шатуна вследствие нештатного зазора в этом сопряжении, образованного в результате перегрева поршневой головки шатуна при установке пальца во время ремонта двигателя. При нарушении фиксации палец прогнозируемо сдвигается вбок до упора в поверхность цилиндра, чем наносит на поверхность длинную и глубокую вертикальную канаву, а на кромке пальца появляется характерная полировка, что является главным признаком данной неисправности (рис.10). Однако в отличие от поломки пальца, при нарушении его осевой фиксации картина развития неисправности сильно зависит от конструкции поршня.
Так, старые двигатели имеют сравнительно длинный палец, который при смещении вбок до упора в цилиндр остается в контакте с поверхностью отверстия обоих бобышек, что нередко вызывает только повреждение цилиндра и резкое увеличение расхода масла на угар. Напротив, у подавляющего большинства современных двигателей короткий палец при смещении до упора вбок либо вообще выходит из сопряжения с противоположной бобышкой поршня, и тогда картина становится в точности тождественной поломке пальца, либо у него остается опора только на край отверстия противоположной бобышки. В последнем случае чрезвычайно высокие удельные нагрузки на небольшую поверхность опоры вызывают катастрофический износ отверстия по узкому поясу, после чегонарастающие знакопеременные изгибающие усилия ломают ближнюю к упору бобышку точно так же, как и при поломке пальца. Таким образом, близость процессов разрушения позволяет объединить оба варианта – поломки пальца и нарушения его осевой фиксации. Разница между процессами только в подтверждающих и уточняющих признаках. Например, при нарушении осевой фиксации поршневой палец не может быть разрушен поперечно, и даже если он попадает между вращающимися и неподвижными деталями, разрушение носит хрупкий характер и происходит вдоль его оси, а не поперек (рис.8). Соответственно, при усталостной поломке пальца не возникает повреждения цилиндра в виде вертикальной канавы от упора в нее пальца, нет и других признаков нарушения осевой фиксации, связанных с перегревом головки шатуна либо со стопорным кольцом и его канавкой (или они выражены слабо).
Причины тяжелых повреждений ДВС, возникающих вследствие разрушения деталей и рассогласования их возвратно-поступательного и/иливращательного движения, могут быть определены с высокой достоверностью, если использовать простую методику, в которой все известные признакиповреждений разбить на главные, подтверждающие и уточняющие, чтобы проверять наличие указанных признаков при расследовании причин неисправностей.Проверочное применение такой методики по базе данных выполненных досудебных и судебных экспертиз (более 90 исследований за 8 лет) показало, что с ее помощью можно практически исключить грубые ошибки при расследовании причин неисправности, включая явные несоответствия заключений экспертиз, таких как путаница между причинами и следствиями, в том числе, при недостаточной квалификации исследователя.
А.Э.Хрулев, Ю.В.Кочуренко
dvs39.ru
Кривошипно-шатунный и газораспределительный механизмы двигателя
Строительные машины и оборудование, справочник
Категория:
Техническое обслуживание автомобилей
Кривошипно-шатунный и газораспределительный механизмы двигателяВ кривошипно-шатунный механизм многоцилиндрового двигателя входят блок цилиндров, головки цилиндров с уплотнительными прокладками, поршни, поршневые кольца, поршневые пальцы, шатуны, коленчатый вал, маховик, поддон картера.
Блок цилиндров отливается из серого чугуна или алюминиевого сплава.
У автомобильных двигателей применяют рядное расположение цилиндров, когда цилиндры располагаются в ряд один за другим в одной плоскости, и V-образные, при котором один ряд цилиндров расположен к другому ряду обычно под углом 90°.
Цилиндры двигателей могут быть образованы стенками самого блока или выполнены в виде сменных гильз.
Головка цилиндров изготовляется общей все цилиндры одного ряда в виде отливки из алюминиевого сплава чугуна. Против каждого из цилиндров она имеет углубление, образующее камеру сгорания. Головка блока цилиндров крепится к блоку цилиндров шпильками или болтами.
Блок цилиндров закрывается снизу подвдном. Для устранения пропуска газов при работе двигателя и утечки охлаждающей жидкости между блоком и головками цилиндров устанавливаются уплотнительные прокладки.
Коленчатый вал воспринимает усилия от поршней и передает образующийся крутящий момент механизмам трансмиссии. Коленчатый вал состоит из коренных и шатунных шеек, носка, фланца и противовесов. Шейки коленчатого вала соединяются щеками, которые с шатунными шейками образуют кривошипы коленчатого вала. Количество и расположение шеек зависят от числа и расположения цилиндров и числа тактов двигателя.
На переднем конце (носке) вала устанавливают шестерню, шкив, храповик для пусковой рукоятки. Шестерня коленчатого вала находится в постоянном зацеплении с шестерней распределительного вала. Шкив коленчатого вала служит для привода вентилятора, водяного насоса, компрессора, генератора и насоса гидроусилителя рулевого управления.
На заднем конце коленчатого вала к фланцу крепится маховик.
Противовесы предназначаются для равномерного вращения коленчатого вала и разгрузки коренных подшипников от действия центробежных сил. Противовесы обычно выполняют заодно с валом.
Для поступления смазки к шатунным шейкам вала е щеках имеются сквозные каналы.
Коленчатые валы штампуют из качественной стали или отлиЕают из магниевого чугуна (двигатели ЗМЗ и ВАЗ).
Шатун соединяет поршень с шатунной шейкой коленчатого вала состоит из стержня двутаврового сечения, верхней неразъемной головки и нижней разъемной головки.
Рис. 1. Головка блока цилиндров (а), блок цилиндров (б) и поддон картера (в): 1 — головка блока цилиндров, 2 — прокладка крышки головки блока цилиндров, 3 — крышка головки блока цилиндров, 4, 7 — прокладки выпускного трубопровода,-5 — выпускной трубопровод, 6 — прокладка головки блока цилиндров, 8 — блок цилиндров, 9 — втулка передней шейки распределительного вала, 10 — крышка распределительных шестерен, 11— прокладка крышки распределительных шестерен, 12 — крышки коренных подшипников, 13 — поддон картера, 14 — прокладка, 15 — картер сцепления
Рис. 88. Детали кривошипно-шатунного механизма восьмицилиндрового V-образного двигателя: 1 — храповик, 2 — шкив, 3 — носок коленчатого вала, 4 — шестерни коленчатого вала, 5, 8, 9 — крышки коренных подшипников, 6 — противовес, 7 — вкладыш коренного подшипника, 10 — фланец, 11 — зубчатый венец маховика, 12 — маховик, 13 — поршень, 14 — шатун, 15 — шатунная шейка, 16 — коренная шейка, 17 — нижняя крышка шатуна, 18 — нижняя (кривошипная) головка шатуна, 19 — стержень шатуна, 20 — верхняя (поршневая) головка шатуна, 21 — втулка верхней головки шатуна, 22 — вкладыш шатунного подшипника, 23 — стопорное кольцо, 24 — поршневой палец, 25 — поршневые компрессионные кольца, 26, 27, 28 — детали составного маслосъемного кольца
Так как при работе поршень, сильно нагреваясь, расширяется, то его устанавливают в цилиндре с определенным зазором, а направляющую часть поршня делают разрезной (пружинной).
Внутри поршня имеются две бобышки с отверстиями для установки поршневого пальца. Нагреваясь, поршень расширяется в направлении оси поршневого пальца больше, так как в бобышках сосредоточена большая часть массы металла. Чтобы поршень при нагреве получил цилиндрическую форму, его диаметр в плоскости, перпендикулярной оси пальца, делают на 0,3—0,5 мм больше, чем в осевом направлении.
Для равномерной работы двигателя поршни всех цилиндров подбирают равной массы.
Поршневой палец служит для соединения поршня с верхней головкой шатуна. Обычно применяют пальцы
плавающего типа, которые могут поворачиваться и в отверстиях бобы шек поршня и в верхней головке шатуна. Для предотвращения продоль”| ного (бокового) перемещения пальца в поршне, что может привести к повреждению зеркала гильзы, палец закрепляют стопорными коль-цами 23.
Поршневые кольца, устанавливаемые на поршне, отливаются из чугуна и подразделяются на компрессионные и маслосъемные. Компрессионные кольца уплотняют соединения поршня с цилиндром и служат для предотвращения прорыва газов через зазор между юбкой поршня и гильзой.
Маслосъемные кольца служат для снятия излишков масла с зеркала гильз и препятствуют его проникновению в камеру сгорания. Поршневые кольца изготовляют несколько большего диаметра, чем поршни. На кольцах делается разрез, называемый замком, который позволяет кольцам пружинить. При установке колец в гильзу вместе с поршнем их предварительно сжимают. Зазор в замке должен составлять 0,2— 0,4 мм.
Маслосъемное кольцо имеет сквозные прорези для отвода масла. Устанавливается оно на поршне ниже компрессионных колец. Маслосъемные кольца двигателей автомобилей ГАЗ-БЗА, ЗИЛ-130 и ГАЗ-24 «Волга» состоят из двух стальных кольцевых дисков 26, осевого 27 и радиального 28 расширителей.
Шатунные и коренные подшипники. Шатунные подшипники, расположенные в нижней головке шатуна, изготовлены в виде разрезных сменных вкладышей 22, чтобы их можно было надеть на шейку коленчатого вала. Они взаимозаменяемые.
Коренные подшипники также представляют собой сменные тонкостенные вкладыши. Верхние вкладыши коренных подшипников устанавливаются в гнезда блока цилиндров, а нижние — в крышки, которые крепятся к картеру болтами.
Вкладыши коренных и шатунных подшипников бывают сталеалюми-ниевые или триметаллические. У сталеалюминиевых вкладышей антифрикционный слой содержит 19—24% олова, около 1% меди, остальное алюминий, у триметаллических на стальную ленту наносят медно-никелевый подслой и сплав СОС6-6 (олово 6%, сурьма 6%, остальное свинец).
Маховик служит для обеспечения равномерного вращения коленчатого вала и крепится к его фланцу болтами. На маховик напрессован зубчатый венец, с которым зацепляется шестерня электродвигателя пускового устройства — стартера.
Порядок работы двигателя. В каждом цилиндре многоцилиндрового двигателя происходит один и тот же рабочий цикл, но одноименные такты происходят в разные моменты. Последовательное чередование одноименных тактов в разных цилиндрах называется порядком работы двигателя. Принято указывать порядок работы двигателя по чередованию такта рабочего хода, начиная с первого цилиндра.
Для правильного чередования рабочих ходов коленчатый вал двигателя имеет определенное расположение кривошипов.
Рис. 3. Рабочий процесс четырехцилиндрового карбюраторного двигателя: полуобороты коленчатого вала: а — первый, б — второй; в — третий, г — четвертый; 1, 2, 3, 4 — поршни
При первом полуобороте (180°) коленчатого вала двигателя (рис. 3, а) с порядком работы 1—3—4—2 крайние поршни опускаются, а средние поднимаются. В первом цилиндре происходит впуск, а в третьем — выпуск, в четвертом — рабочий ход, во втором – сжатие.
в первом цилиндре происходит рабочий ход, в третьем — сжатц« в четвертом — впуск, во втором — выпуск.
При четвертом полуобороте (720°) коленчатого вала (рис. 89) поршни поднимаются, а поршни опускаются; при этом в первом цилиндре происходит выпуск, в третьем — рабочий ход в четвертом — сжатие, во втором — впуск.
При дальнейшем вращении коленчатого вала рабочие процессы повторяются в той же последовательности.
У четырехтактного четырехцилиндрового двигателя автомобиля ГАЗ-24 «Волга» порядок работы 1—2—4—3.
В четырехтактном шестицилиндровом двигателе за два оборота коленчатого вала произойдет 6 рабочих ходов, чередоваться он и будут через 120°. Порядок работы двигателя будет 1—5—3—6—2—| (ГАЗ-52) или 1—4—2—5—3—6 (двигатель ЯМЗ-236).
В восьмицилиндровых двигателях автомобилей ГАЭ-53А и ЭИЛ-130 рабочие ходы чередуются через 90°. Порядок работы 1—5—4—2— 6—3—7—8.
Неисправности кривошипно-шатунного механизма. В процессе эксплуатации автомобиля могут выявиться следующие наиболее характерные неисправности кривошипно-шатун-ного механизма: пригорание, износ и поломка поршневых колец; износ поршней и гильз цилиндров; износ шатунных и коренных подшипнп-ков; нарушение уплотнения прокладки головки цилиндров при слабой или неравномерной затяжке гаек крепления; обрыв шпилек и повреждение резьбы вследствие слабой или неравномерной затяжки; нага-рообразование в камерах сгорания и др.
Газораспределительный механизм служит для своевременного впуска в цилиндры горючей смеси и выпуска отработавших газов. На современных карбюраторных двигателях впуск смеси и выпуск отработавших газов производится клапанами, которые могут иметь нижнее или верхнее расположение.
Большинство современных двигателей имеют газораспределительный механизм с верхним расположением клапанов (рис. 4). Распределительный вал располагается в блоке между двумя рядами цилиндров. От него при помощи толкателей, толкающих штанг и коромысел приводятся в действие клапаны как правого, так и левого рядов цилиндров.
Распределительный вал имеет кулачки, опорные шейки, эксцентрик для привода топливного насоса и шестерню для привода масляного насоса и прерывателя-распределителя (вал изготовляется заодно с кулачками и опорными шейками).
У каждого цилиндра на валу имеется два кулачка — впускной и выпускной. Одноименные кулачки располагаются в четырехцилиндровом двигателе под углом 90е, в шестицилиидровом под углом 60°, в восьмицилиндровом под углом 45°.
На переднем конце распределительного вала устанавливается на шпонке шестерня, которая находится в зацеплении с шестерней, установленной на коленчатом валу.
Рис. 4. Детали газораспределительного механизма восьмицилиндрового V-образного двигателя: 1 — распределительный вал, 2 — распределительная шестерня, 3 — упорный фланец, 4 — опорная шейка, 5 — эксцентрик привода топливного насоса, 6 — втулка шейки распределительного вала, 7 — кулачки распределительного вала, 8 — шестерня привода масляного насоса и прерывателя-распределителя. 9 — стойка коромысел клапана, 10 — коромысло клапана, 11 — ось коромысла, 12 — толкатели клапана, 13 — толкающая штанга, 14 — выпускной клапан, /5 — механизм вращения выпускного клапана. 16 — регулировочный винт, 17 — пружина клапана. 18 — направляющая втулка клапана, 19 — впускной клапан, 20 — сухарь, 21 — опорная шайба пружины клапана, 22 — седло клапана, 23 — металлический натрий
В четырехтактных двигателях рабочий цикл происходит за два оборота коленчатого вала. За это время должны последовательно открыться все клапаны, поэтому распределительный вал должен вра щаться в два раза медленнее коленчатого вала. Таким образом, шестерня имеет в два раза больше зубьев, чем шестерня на коленчатом валу.
Шестерни изготавливают из чугуна или текстолита, шестерни коленчатого вала — из стали.
В двигателях, у которых распределительные валы располагаются на головках цилиндров («Москвич-412», ВАЗ-2101 «Жигули»), привод распределительного вала осуществляется от коленчатого вала двухрядной роликовой цепью.
Для правильной работы двигателя коленчатый и распределительный валы должны находиться в строго определенном положении относительно друг друга. Поэтому при сборке распределительные шестерни вводятся в зацепление по имеющимся на их зубьях меткам.
Осевые перемещения распределительного вала у большинства карбюраторных двигателей ограничиваются упорным фланцем, закрепленным на блоке между торцом передней шейки вала и ступицей распределительной шестерни. Опорные шейки распределительного вала, вращаются в стальных втулках 6, залитых сплавом СОС6-6, или металлокерамических втулках.
Клапаны состоят из головок и стержней. Впускные клапаны изготовляют из хромистой, а выпускные — из жаростойкой стали. Головка клапана имеет узкую, скошенную под углом 45 или 30° кромку, называемую фаской, которой она прилегает к седлу, запрессованному в головку цилиндров.
Для лучшего наполнения цилиндров горючей смесью диаметр головки впускного клапана выполняют большим, чем диаметр головки выпускного клапана. Клапаны установлены в направляющих втулках, изготовляемых из чугуна или металлокерамики.
Для улучшения охлаждения стержни выпускных клапанов двигателей ГАЭ-53А и ЗИЛ-130 выполняют полыми. В них помещают металлический натрий с температурой плавления 97 °С. Во время работы двигателя натрий плавится и, переливаясь, при встряхивании переносит теплоту от головки клапана к стержню, а от последнего к направляющей втулке.
Плотное прижатие клапана к седлу обеспечивается давлением клапанной пружины, закрепленной при помощи опорной шайбы и конических разрезных сухарей. Головка выпускного клапана имеет жаростойкую наплавку посадочной фаски.
Выпускные клапаны для уменьшения неравномерной выработки седла и фаски головки клапана принудительно поворачиваются во время работы двигателя специальным механизмом поворота.
Толкатели представляют собой стальные стаканы, на внутреннюю сферическую поверхность которых опираются толкаю-, щие штанги. Для повышения износостойкости торцы толкателей, соприкасающиеся с кулачками, наплавляют специальным чугуном.
Для устранения неисправностей газораспределительного механизма необходимо: отрегулировать зазоры между стержнями клапанов и носками коромысел, притереть клапаны к седлам, заменить сломанные пружины или изношенные детали (втулки коромысел, втулки распределительного вала и др.).
Читать далее: Система охлаждения двигателей автомобиля
Категория: - Техническое обслуживание автомобилей
Главная → Справочник → Статьи → Форум
stroy-technics.ru
4 2 кривошипно-шатунный механизм - стр.4
4.2. Кривошипно-шатунный механизм
Кривошипно-шатунный механизм воспринимает давление газов при такте сгорание — расширение и преобразовывает прямолинейное, возвратно-поступательное движение поршня во вращательное движение коленчатого вала. Кривошипно-шатунныймеханизм состоит из блока цилиндров с картером, головки цилиндров, поршней с кольцами, поршневых пальцев, шатунов, коленчатого вала, маховика и поддона картера.
Блок цилиндров является основной деталью двигателя, к которой крепятся все механизмы и детали.
Цилиндры в блоках изучаемых двигателей расположены V-образно в два ряда под углом 90°.
Блоки цилиндров отливают из чугуна (ЗИЛ-130, КамАЗ) или алюминиевого сплава (ЗМЗ-53). В той же отливке выполнены картер и стенки полости охлаждения, окружающие цилиндры двигателя.
В блоках изучаемых двигателей устанавливают вставные гильзы, омываемые охлаждающей жидкостью. Внутренняя поверхность гильзы служит направляющей для поршней. Гильзу растачивают под требуемый размер и шлифуют. Гильзы, омываемые охлаждающей жидкостью, называются мокрыми. Они в нижней части имеют уплотняющие кольца из специальной резины (ЗИЛ-130 и КамАЗ-740) или медные (ЗМЗ-53). Вверху уплотнение гильз достигается за счет прокладки головки цилиндров. Блок цилиндров V-образного двигателя ЗИЛ-130 и ЗМЗ-53 вверху закрыт двумя головками изалюминиевого сплава. В двигателе КамАЗ-740 каждый цилиндр имеет свою головку. В головке цилиндров двигателей ЗИЛ-130 и ЗМЗ-53 размещены камеры сгорания, в которых имеются резьбовые отверстия для свечей зажигания. Для охлаждения камер сгорания в головке вокруг них выполнена специальная полость.
На головке цилиндров закреплены детали газораспределительного механизма. В головке цилиндров выполнены впускные и выпускные каналы и установлены вставные седла и направляющие втулки клапанов. Для создания герметичности между блоком и головкой цилиндров установлена прокладка, а крепление головки к блоку цилиндров осуществлено шпильками с гайками. Прокладка должна быть прочной, жаростойкой и эластичной. В двигателе ЗИЛ-130 и ЗМЗ-53 она сталеасбестовая, в КамАЗ-740 — из стали. Для уплотнения стальной прокладки в расточку на нижней плоскости головки цилиндра запрессовано стальное кольцо с острым выступом.
В двигателе ЗМЗ-53 гильзы цилиндров в верхней части удерживаются только головкой цилиндров, поэтому при сборке необходимо подбирать комплект медных уплотнительных колец нижней части гильзы так, чтобы гильза выступала над плоскостью разъема блока и головки цилиндров на. 0,02 ... 0,09 мм. Головка цилиндров сверху закрыта штампованной крышкой. Между крышкой и головкой устанавливают прокладки из маслоустойчивой резины. Головка цилиндра двигателя КамАЗ закрыта алюминиевой крышкой, уплотненной прокладкой.
Снизу картер двигателя закрыт поддоном, выштампованным из листовой стали. Поддон защищает картер от попадания пыли и грязи и используется в качестве резервуара для масла.
Штампованный поддон крепится к плоскости разъема болтами, а для обеспечения герметичности соединения применяют прокладки из картона или из клееной пробковой крошки.
Во время работы двигателя в картер проникают газы, что может повлечь за собой повышение давления, прорыв прокладок и вытекание масла. Чтобы не допустить этого, картер через специальную трубку (сапун) сообщается с атмосферой.
Рис.5.Поршни в сборе с шатунами :
а- двигателя ЗМЗ- 53; б- двигателя ЗИЛ- 130
1-крышка нижней головки шатуна; 2-номер шатуна; 3-надпись, указывающая положение поршня в цилиндре; 4-поршневой палец; 5-днище поршня; 6-поршень; 7-стопорное кольцо; 8-шатун; 9-метка, указывающая положение поршня в цилиндре
Рис.6.Поршневые кольца:
а — поршень в сборе с поршневыми кольцами; в — маслосъемное кольцо; в — последовательность установки элементов маслосъемного кольца на поршень; 1 — верхнее компрессионное кольцо; 2— среднее и нижнее компрессионные кольца; 3 — маслосъемное кольцо; 4 — кольцевые диски маслосъемного кольца; 5 — радиальный расширитель; 6 — осевой расширитель; 7 — установка радиального расширителя; 8 — установка нижнего кольцевого диска;9 — установка осевого расширителя; 10 — установка верхнего кольцевого диска
Поршень (Рис.5)воспринимает давление газов при рабочем такте и передает его через поршневой палец и шатун на коленчатый вал. Поршень представляет собой перевернутый цилиндрический стакан, отлитый из алюминиевого сплава. В верхней части поршня расположена головка с канавками, в которые вставлены поршневые кольца.
Ниже головки выполнена юбка, направляющая движение поршня. В юбке поршня имеются приливы-бобышки с отверстиями для поршневого пальца.
При работе двигателя поршень, нагреваясь, расширится и, если между ним и зеркалом цилиндра не будет . необходимого зазора, заклинится в цилиндре, и двигатель прекратит работу. Однако большой зазор между поршнем и зеркалом цилиндра также нежелателен, так как это приводит к прорыву части газов в картер двигателя, падению давления в цилиндре и уменьшению мощности двигателя. Чтобы поршень не заклинивался при прогретом двигателе, головку поршня выполняют меньшего диаметра, чем юбку, а саму юбку в поперечном сечении изготавливают не цилиндрической формы, а в виде эллипса с большей осью его в плоскости, перпендикулярной поршневому пальцу. На юбке поршня может быть разрез. Благодаря овальной форме и разрезу юбки предотвращается заклинивание поршня.
Общее устройство поршней всех изучаемых двигателей принципиально одинаковое, но каждый из них отличается диаметром и рядом особенностей, присущих только данному двигателю. Например, в головке поршня двигателя ЗИЛ-130 залито чугунное кольцо, в котором сделана канавка под верхнее компрессионное кольцо. Такая конструкция способствует уменьшению износа канавки под поршневое кольцо.
В днище поршня двигателя КамАЗ-740 выполнена камера сгорания. Головка имеет вставку из жаропрочного чугуна под верхнее компрессионное кольцо и коллоидно-графитовое покрытие юбки.
Для правильной сборки поршня с шатуном на днищах головок большинства поршней выбита стрелка с надписью «Вперед», а на боковых поверхностях поршней двигателей ЗМЗ-53 выполнена надпись «Назад».
Поршни двигателей ЗИЛ-130 и ЗМЗ-53 после механической обработки покрывают оловом, что способствует лучшей приработке и уменьшению износа их в первоначальный период работы двигателя.
Поршневые кольца, применяемые в двигателях( Рис.6), подразделяются на компрессионные и маслосъемные. Компрессионные кольца уплотняют зазор между поршнем и цилиндром и служат для уменьшения прорыва газов из цилиндров в картер, а маслосъемные снимают излишки масла с зеркала цилиндров и не допускают проникновения масла в камеру сгорания. Кольца, изготовленные из чугуна или стали, имеют разрез (замок).
При установке поршня в цилиндр поршневое кольцо предварительно сжимают, в результате чего обеспечивается его плотное прилегание к зеркалу цилиндра при разжатии. На кольцах имеются фаски, за счет которых кольцо несколько перекашивается и быстрее притирается к зеркалу цилиндра, и уменьшается насосное действие колец.
Количество колец, устанавливаемых на поршнях изучаемых двигателей, неодинаковое. На поршнях двигателей ЗИЛ-130 три компрессионных кольца, два верхних хромированы по поверхности, соприкасающейся с гильзой.
В двигателях ЗМЗ-53 и КамАЗ-740 по два компрессионных кольца. Рабочая поверхность нижнего компрессионного кольца двигателя КамАЗ-740 покрыта молибденом.
Маслосъемных колец в изучаемых двигателях по одному. Маслосъемное кольцо собрано из четырех отдельных элементов — двух тонких стальных разрезных колец и двух гофрированных стальных расширителей (осевого и радиального).На двигателе КамАЗ маслосъемное кольцо коробчатого сеченияс витым пружинным расширителем. При установке колец на поршень их замки следует размещать в разные стороны.
Поршневой палец шарнирно соединяет поршень с верхней головкой шатуна. Палец изготовлен в виде пустотелого цилиндрического стержня, наружная поверхность которого закалена нагревом током высокой частоты.
На изучаемых двигателях применяются «плавающие» пальцы, т. е. такие, которые могут свободно поворачиваться как в верхней головке шатуна, так и в бобышках поршня, что способствует равномерному износу пальца..
Во избежание задиров цилиндров при выходе пальца из бобышек осевое перемещение его ограничивается двумя разрезными стальными кольцами, установленными в выточках в бобышках поршня.
Шатун служит для соединения коленчатого вала с поршнем. Через шатун давление на поршень при рабочем ходе передается на коленчатый вал.
В двигателе КамАЗ затяжку гаек производят до удлинения шатунных болтов на 0,25 ... 0,27 мм. На стержне шатуна выштампован номер детали, а на крышке метка. Номер на шатуне и метка на его крышке всегда должны быть обращены в одну сторону. К верхней и нижней головкам шатуна подводится масло: к нижней головке — через канал в коленчатом валу, а к верхней — через прорезь. Из нижней головки шатуна масло через, отверстие выбрызгивается на стенки цилиндров.
В изучаемых двигателях на одной шатунной шейке коленчатого вала закреплено по два шатуна. Для правильной их сборки с поршнями нужно помнить, что шатуны правого ряда цилиндров собраны с поршнями так, что номер на шатуне обращен назад по ходу автомобіля, а левого ряда — вперед, т. е. совпадает с надписью на поршне.
Коленчатый вал воспринимает усилия, передаваемые от поршней шатунами, и преобразует их в крутящий момент, который затем через маховик передается агрегатам трансмиссии.
В двигателях ЗИЛ-130 и КамАЗ-740 коленчатый вал стальной, а в ЗМЗ-53 — отлит из высокопрочного чугуна.
Коленчатый вал (рис.7) состоит из шатунных и коренных шлифованных шеек, щек и противовесов. На переднем конце вала имеется углубление для шпонки распределительной шестерни и шкива привода вентилятора, а также нарезное отверстие для крепления храповика; задняя часть вала выполнена в виде фланца, к которому болтами прикреплен маховик. В углублении задней
торцевой части коленчатого вала расположен подшипник ведущего вала коробки передач.Количество и расположение шатунных шеек коленчатого вала зависит от числа цилиндров. В V-образном двигателе количество шатунных шеек в два раза меньше числа цилиндров, так как на одну шатунную шейку вала установлено по два шатуна — один левого1 и другой правого рядов цилиндров.
Рис.7.Коленчатый вал и поршневая группа:
1 – шкив; 2 – храповик; 3 – шестерня привода газораспределительного механизма; 4 – поршень; 5 – маховик; 6 – зубчатый венец; 7 – грязеуловители; 8 – вкладыш; 9 – крышка; 10 – противовес; 11, 12 – коренные и шатунные шейки
В восьмицилиндровых V-образных двигателях коленчатые валы имеют по четыре шатунных шейки, расположенных под углом в 90°.
В изучаемых двигателях число коренных шеек коленчатого вала на одну больше, чем шатунных, т. е. каждая шатунная шейка с двух сторон имеет коренную. Такие коленчатые валы называют полноопорными.
Коренные и шатунные шейки коленчатого вала соединены между собой щеками.
Для уменьшения центробежных сил, создаваемых кривошипами, на коленчатом валу выполнены противовесы, а шатунные шейки сделаны полыми. Для.повышения твердости и увеличения срока службы поверхность коренных и шатунных шеек стальных валов закаливают нагревом токами высокой частоты.
Коренные и шатунные шейки вала соединены каналами (сверлениями) в щеках вала. Эти каналы предназначены для подвода масла от коренных подшипников к шатунным.
В каждой шатунной шейке вала имеется полость, которая выполняет роль грязеуловителя. Сюда поступает масло от коренных шеек. При вращении вала частицы грязи, находящиеся в масле, под действием центробежных сил отделяются от масла и оседают на стенке грязеуловителя, а к шатунным шейкам поступает очищенное масло. Очистка грязеуловителей осуществляется через завернутые в их торцах резьбовые пробки только при разборке двигателя.
Перемещение вала в продольном направлении ограничивается упорными баббитовыми шайбами, которые расположены по обе стороны первого коренного подшипника или четырьмя сталеалюминиевыми полукольцами, установленными в выточке задней коренной опоры (КамАЗ-740).
В местах выхода коленчатого вала из картера двигателя имеются сальники и уплотнители, предотвращающие утечку масла.
На переднем конце вала установлен резиновый самоподжимный сальник, а на заднем конце выполнена маслосгонная резьба или маслоотражательный буртик.
В заднем коренном подшипнике сделаны маслоуловительные каналы, в которые сбрасывается масло с маслосгонной резьбы или маслоотражательного буртика и установлен сальник, состоящий из двух кусков асбестового шнура.
Шатунные и коренные подшипники. В работающем двигателе нагрузки на шатунные и коренные шейки коленчатого вала очень велики. Для уменьшения трения коренные шейки, как и шатунные, расположены в подшипниках скольжения, которые выполнены в виде вкладышей, аналогичных шатунным. Вкладыши каждого коренного или шатунного подшипника состоят из двух половинок, устанавливаемых в нижней разъемной головке шатуна и в гнезде блока и крышке коренного подшипника. От проворачивания вкладыши удерживаются выступом, входящим в паз шатунного или коренного подшипника. Крышки коренных подшипников закреплены при помощи болтов и гаек, которые для предотвращения от самоотвертывания зашплинтованы проволокой либо застопорены замковыми пластинами.
В двигателе ЗМЗ-53 для предотвращения заклинивания коленчатого вала в коренных подшипниках блока (изготовленного из алюминиевого сплава), что имеет место при низких температурах, крышки коренных подшипников выполнены из чугуна.
Маховик уменьшает неравномерность работы двигателя, выводит поршни из мертвых точек, облегчает пуск двигателя и способствует плавномутроганию автомобиля с места. Маховик изготовлен в виде массивного чугунного диска и прикреплен к фланцу коленчатого вала болтами с гайками. При изготовлении маховик балансируется вместе с коленчатым валом. Для предотвращения нарушения балансировки при разборке двигателя маховик установлен на несимметрично расположенные штифты или болты. На ободе маховика двигателя КамАЗ-740 имеется углубление для определения в. м. т. поршня первого цилиндра при установке топливного насоса высокого давления. Зубчатый венец, напрессованный на маховик, служит для запуска двигателя стартером.
Картер двигателя, отлитый заодно с блоком цилиндров, является базисной (основной) деталью. К картеру крепятся детали кривошипно-шатунного и газораспределительного механизмов. Для повышения жесткости внутри картера выполнены ребра, в которых расточены гнезда коренных подшипников коленчатого вала и опорных шеек распределительного вала. В двигателе КамАЗ-740 картерная часть блока связана с крышками коренных подшипников поперечными болтами — стяжками, что увеличивает жесткость картера. Снизу картер закрыт поддоном, выштампованным из тонкого стального листа.
Поддон является резервуаром для масла и в то же время защищает детали двигателя от пыли и грязи. В нижней части поддона предусмотрено отверстие для выпуска масла, закрываемое резьбовой пробкой. Поддон прикреплен к картеру болтами. Чтобы не было утечки масла, между поддоном и картером установлены прокладки и резиновые уплотнители.
Крепление двигателя к раме должно быть надежным и в то же время обеспечивать смягчение толчков, возникающих при работе двигателя и движении автомобиля. Каждый элемент крепления состоит из одной или двух резиновых подушек, стальных шайб, втулок и болтов. Двигатели могут быть закреплены к раме в трех или четырех точках.
Двигатель ЗИЛ-130 крепится в трех точках, а ЗМЗ-53 и КамАЗ-740 — в четырех.
Двигатель ЗМЗ-53 крепится к раме болтами — спереди на двух резиновых подушках, подложенных под кронштейны, привернутые к блоку цилиндров, а сзади — на двух резиновых подушках, подложенных под приливы картера сцепления. В этом двигателе передние опоры принимают на себя также продольные усилия, возникающие при торможении, трогании автомобиля и выключении сцепления.
У двигателя ЗИЛ-130 задние опоры устроены также, как у двигателя ЗМЗ-53, а передней опорой является кронштейн, установленный под крышкой распределительных шестерен. Силовой агрегат автомобиля КамАЗ-5320 крепится в четырех точках: передняя опора, две задние и одна поддерживающая.
4.3. Газораспределительный механизм
В двигателях внутреннего сгорания своевременный впуск в цилиндры свежего заряда горючей смеси и выпуск отработавших газов обеспечивается газораспределительным механизмом.
На изучаемых двигателях установлены газораспределительные механизмы с верхним расположением клапанов.
Газораспределительный механизм состоит из распределительной шестерни, распределительного вала, толкателей, штанг, коромысел с деталями крепления, клапанов, пружин г с деталями крепления и направляющих втулок клапанов (рис. 8).
Распределительный вал расположен между правым и левым рядами цилиндров.При вращении распределительного вала кулачок набегает на толкатель и поднимает его вместе со штангой. Верхний конец штанги надавливает на регулировочный винт во внутреннем плече коромысла, которое, провертываясь на своей оси, наружным плечом нажимает на стержень клапана и открывает отверстие впускного или выпускного канала в головке цилиндров. В рассматриваемых двигателях распределительный вал действует на толкатели правого и левого рядов цилиндров.улучшить форму камеры сгорания, наполнение цилиндров и условия сгорания рабочей смеси.
Лучшая форма камеры сгорания позволяет повысить также степень сжатия, мощность и экономичность двигателя.
Распределительный вал(см. рис.8.)служит для открытия клапанов в определенной последовательности в соответствии с порядком работы двигателя.
Рис.8.Газораспределительный механизм с верхним расположением клапанов.
Распределительные валы отливают из специального чугуна или отковывают из стали. Устанавливают его в отверстия стенок и ребрах картера. Для этой цели на валу имеются цилиндрические шлифованные опорные шейки. Для уменьшения трения между шейками вала и опорами в отверстия запрессовывают втулки, внутренняя поверхность которых покрыта антифрикционным слоем.
Для предупреждения осевого смещения вала при работе двигателя между шестерней и передней опорной шейкой вала установлен фланец, который закреплен двумя болтами к передней стенке блока цилиндров. Внутри фланца на носке вала установлено распорное кольцо, толщина которого несколько больше толщины фланца, в результате чего достигается небольшое осевое смещение распределительного вала.
В двигателе КамАЗ-740 привод распределительного вала осуществляется от шестерни коленчатого вала через промежуточные шестерни, расположенные на заднем торце блока двигателя. От осевого перемещения вал фиксируется корпусом подшипника задней опоры, который крепится к блоку тремя болтами
В четырехтактных двигателях рабочий процесс происходит за четыре хода поршня или два оборота коленчатого вала, т. е. за это время должны последовательно открыться впускные и выпускные клапаны каждого цилиндра, а это возможно, если число оборотов распределительного вала будет в 2 раза меньше числа оборотов коленчатого вала, поэтому диаметр шестерни, установленной на распределительном валу, делают в 2 раза большим, чем диаметр шестерни коленчатого вала.
Клапаны в цилиндрах двигателя должны открываться и закрываться в зависимости1 от направления движения и положения поршней в цилиндре. При такте впуска, когда поршень двигается от в. м. т. к н. м. т., впускной клапан должен быть открыт, а при такте сжатия, расширения (рабочего хода) и выпуска — закрыт. Чтобы обеспечить такую зависимость, на шестернях газораспределительного механизма делают метки: на зубе шестерни коленчатого вала и между двумя зубьями шестерни распределительного вала. При сборке двигателя эти метки должны совпадать. В газораспределительном механизме двигателя КамАЗ-740 шестерни устанавливаются также по меткам.
Толкатели предназначены для передачи усилия от кулачков распределительного вала к штангам.
Толкатели изготовлены в виде-малых цилиндрических стаканов, во внутренней части которых имеются сферические углубления для установки штанги. Изготовлены толкатели из чугуна или стали и размещены в направляющих, выполненных в блоке цилиндров или съемными (КамАЗ-740). При работе двигателя толкатели все время провертываются вокруг своих осей, что необходимо для их равномерного износа. Вращение толкателя достигается за счет выпуклой поверхности его нижней головки и скошенной поверхности кулачка распределительного вала.
Штанги передают усилие от толкателей к коромыслам и выполнены в виде стальных стержней с закаленными наконечниками (ЗИЛ-130) или дюралюминиевых трубок с запрессованными с обеих сторон сферическими стальными наконечниками. Наконечники упираются с одной стороны в углубление толкателя, а с другой — в сферическую поверхность болта коромысла.
Коромысла передают усилие от штанги клапану. Изготовляют их из стали в виде двуплечего рычага, посаженного на ось. В отверстие коромысла для уменьшения трения запрессовывают бронзовую втулку. -Полая ось закреплена в стойках на головке цилиндров. От продольного перемещения коромысло удерживается цилиндрической пружиной. На двигателях ЗИЛ-130 и ЗМЗ-53 коромысла не равноплечие. В короткое плечо завернут регулировочный винт с контргайкой, упирающийся в сферическую поверхность наконечника штанги.
Клапаны служат для периодического открытия и закрытия отверстий впускных и выпускных каналов в зависимости от положения поршней в цилиндре и от порядка работы двигателя.
В изучаемых двигателях впускные и выпускные каналы выполнены в головках цилиндров и заканчиваются вставными гнездами из жаропрочного чугуна. Клапан состоит из головки и стержня. Головка имеет узкую, скошенную под углом 45 или 30° кромку (рабочая поверхность), называемую фаской.
Клапан состоит из головки и стержня. Головка имеет узкую, скошенную под углом 45 или 30° кромку (рабочая поверхность), называемую фаской. Фаска клапана должна плотно прилегать к фаске седла, для чего эти поверхности взаимно притирают.
Головки впускных и выпускных клапанов имеют неодинаковый диаметр. Для лучшего наполнения цилиндров свежей горючей смесью диаметр головки впускного клапана делают большим, чем диаметр выпускного. В связи с тем что клапаны во время работы двигателя неодинаково нагреваются (выпускной клапан, омываемый горячими отработавшими газами, нагревается больше), изготавливаются они из разного материала: впускные клапаны — из хромистой, выпускные — из сильхромовой жароупорной стали. Для увеличения срока службы выпускных клапанов двигателя ЗИЛ-130 на их рабочую поверхность наплавлен жароупорный сплав, стержни изготовлены пустотелыми и имеют натриевое наполнение, способствующее лучшему отводу тепла от головки клапана к его стержню.
Стержень клапана цилиндрической формы, в верхней части имеет выточку для деталей крепления клапанной пружины. Стержни клапанов помещены в чугунных или металлокерамических направляющих втулках. Втулки запрессовывают в головку цилиндров и стопорят замочными кольцами.
Клапан прижимается к седлу цилиндрической стальной, пружиной, которая имеет переменный шаг витков, что необходимо для устранения ее вибрации. Пружина одной стороной опирается в шайбу, расположенную на головке цилиндров, а другой — в опорную шайбу. Опорная шайба удерживается на стержне клапана двумя коническими сухарями, внутренний буртик которых входит в выточку стержня клапана.
Для уменьшения проникновения масла по стержням клапанов в камеру сгорания двигателя в опорных шайбах установлены резиновые кольца или на стержни клапанов надеты резиновые колпачки. Для равномерного нагрева и износа клапана желательно, чтобы при работе двигателя он поворачивался.
В двигателе ЗМЗ-53 вращение клапана достигается установкой между опорной шайбой и сухарями каленой конической втулки, наружный конус которой не полностью совпадает с внутренним конусом упорной шайбы. Благодаря такой конструкции между втулкой и опорной шайбой возникает небольшое трение и при сжатии пружины, так как она несколько скручивается, клапан поворачивается.
gigabaza.ru
По ремонту китайских мопедов: октября 2012
Кривошипно-шатунный механизм (КШМ) служит для преобразования возвратно поступательного движения поршня во вращательное движение коленчатого вала. Конструкция КШМ представлена на рис. 2.3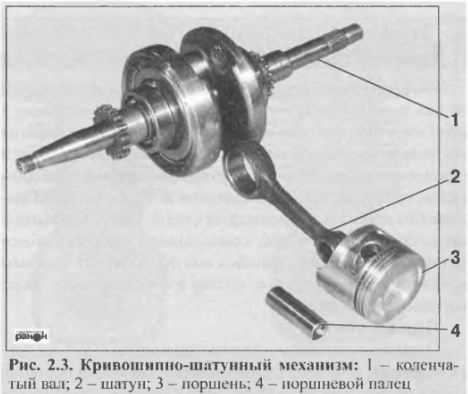
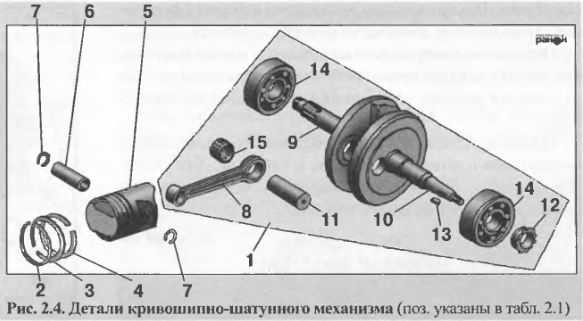
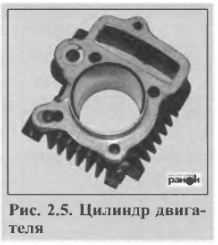
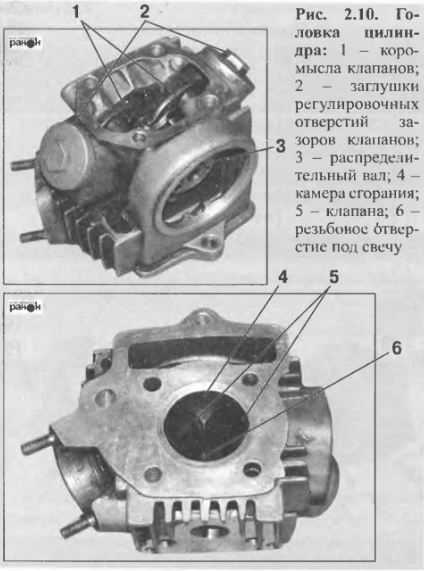
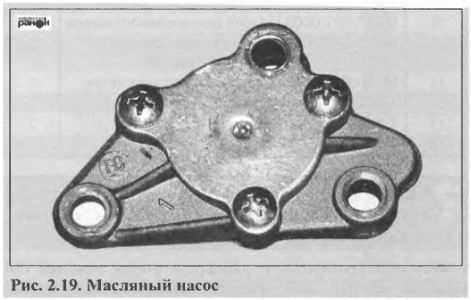
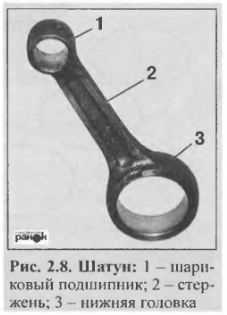
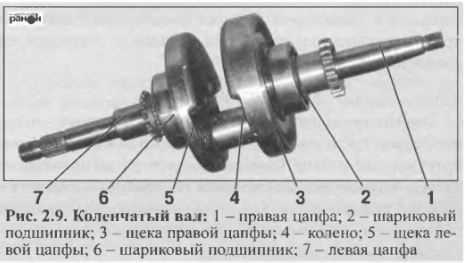
www.mopedaremont.ru