Дефектовка клапанов
Самостоятельный ремонт клапанного механизма блока цилиндров ВАЗ своими руками
Ремонт клапанного механизма
Проверка
При большом пробеге происходит износ седел, фасок тарелок, стержней и торцов клапанов, рабочих поверхностей толкателей, регулировочных шайб, направляющих втулок клапанов, кулачков, шеек и подшипников распредвала, рычагов и регулировочных болтов, пружин и маслоотражательных колпачков. Шум под крышкой головки указывает на износ многих деталей.У рычагов клапанов проверяют состояние рабочих поверхностей, соприкасающихся с торцом стержня клапана и со сферическим концом регулировочного болта. Если на них имеются задиры и риски, рычаги следует заменить.
Если замечены дефекты на втулке регулировочного болта или на самом болте, их необходимо заменить. При дефектовке проверяют размеры клапанов и втулок, зазоры между ними, биение клапанов во втулках. Размеры втулок и клапанов приведены в таблицах.
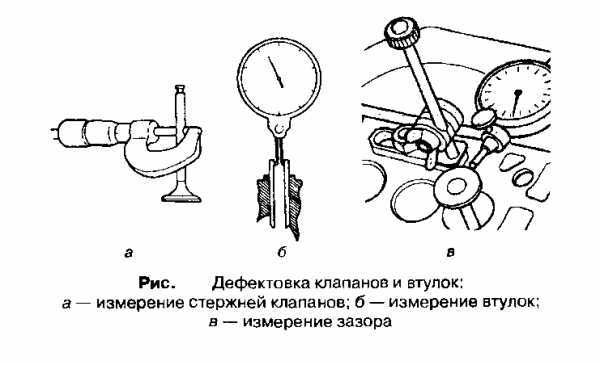
Контролируемые размеры направляющих втулок клапанов
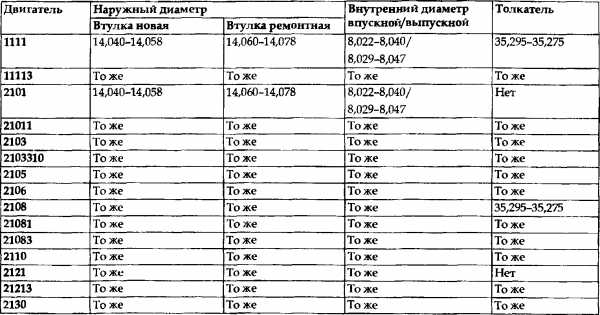
Контролируемые размеры клапанов
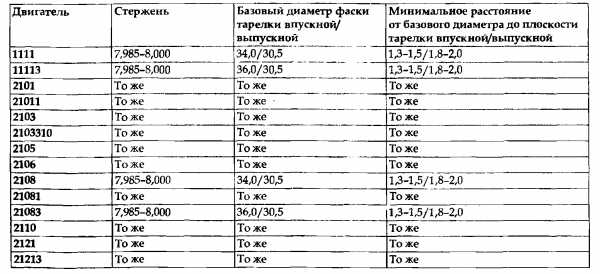
При дефектовке также проверяют состояние и упругость пружин. Их параметры должны соответствовать приведенным в таблице. Размер 11 пружины рычага должен быть равен 35 мм, а размер 12 пружины под нагрузкой 5,2-7,5 кгс — 43 мм.
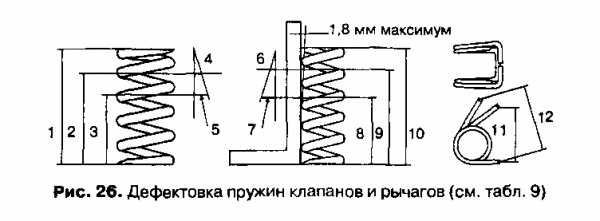
Регулировочные шайбы не должны иметь ступенек от износа, натира металла.
Регулировочные шайбы не должны иметь ступенек от износа, натира металла. Следует очистить клапаны от нагара железной щеткой. Износ седел, рычагов, кулачков вала, клапанов заметен при осмотре. Кроме того, необходимо убедиться в отсутствии деформации стержней клапанов: допустимая кривизна — не более 0,015 мм.
Нужноубедиться в отсутствии трещин на головке клапана. Выработка торца стержня должна бьггь не более 0,4-0,5 мм. При наличии ступеньки на стержне в районе контакта с маслоотражательным колпачком клапан необходимо заменить. Следует также проверить состояние рабочей фаски тарелки клапана. Износ стержня клапана — разница диаметров верхней и нижней частей, замеренных микрометром в разных положениях, чтобы учесть возможную овальность, — не должен превышать 0,03 мм. Для определения степени износа направляющих втулок и стержней на головке, лежащей камерами сгорания вверх, слегка приподнимают клапан за тарелку и покачивают его в разных направлениях. Если люфт ощутим, проверяют микрометром диаметр стержня клапана. Если стержень не изношен, значит, изношена втулка. Когда же стержень не отвечает требованиям, повторяют испытание с новым клапаном. ВАЗ рекомендует проверять люфт индикатором. Если зазоры между стержнями старых клапанов и старыми направляющими втулками выше предельно допустимого (0,15 мм), клапаны заменяют новыми. Но часто этого недостаточно и необходимо заменять или восстанавливать втулки.
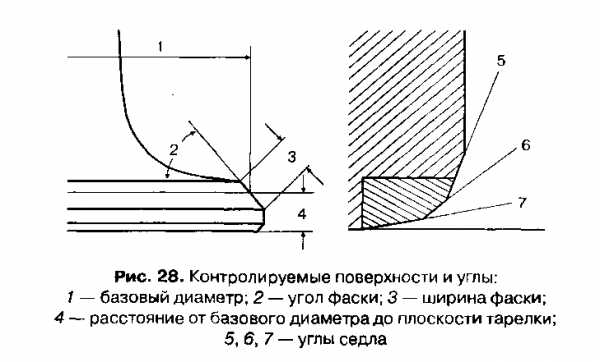
Если зазор в паре «старая втулка — новый стержень» превышает 0,08 мм, втулку нужно восстанавливать или менять. Нормальный зазор для новых втулок и клапанов составляет 0,022-0,055 мм для впускных клапанов и 0,029-0,062 мм для выпускных клапанов.
Контролируемая высота пружин клапанов
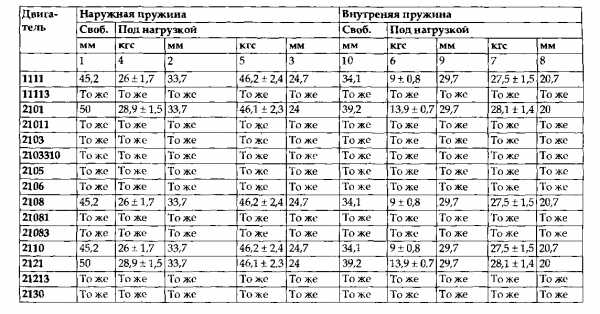
Традиционный метод ремонта
Направляющие втулки заменяют, если зазор в соединении со стержнем клапана более 0,15 мм не устраняется установкой нового клапана, а восстановление втулок невозможно из-за их непригодности или отсутствия современных инструментов. Выпрессовка старых и запрессовка новых втулок в любой мастерской редко обходятся без потери качества посадки и искажения геометрии узла «втулка — клапан — седло». Исправление геометрии требует обработки «по месту» седел клапанов зенкером или шарошкой и долгой притирки клапанов. На заводе чугунные втулки запрессовывают в алюминиевый корпус с натягом от 0,06 до 0,11 мм, предварительно охлаждая их в жидком азоте до -196 °С, а корпус подогревая до 160-170 °С, чтобы избежать микротрещин. Все это невозможно в условиях автосервисов. Для выпрессовки старых втулок лучше применять винтовые прессы — так меньше риск повреждения гнезда. Головку перед выпрессовкой следует нагреть примерно до 150 °С
Перед запрессовкой новых втулок нужно промерить гнезда и втулки, чтобы убедиться, что натяг будет соответствовать норме. При завышенном натяге можно повредить гнездо, а при слабом — придется растачивать гнездо и ставить ремонтные втулки или применять современные химические фиксирующие составы.
Перед запрессовкой следует хотя бы примерно имитировать заводской режим: нагреть головку до 150 °С, а втулки охладить в морозильной камере. Запрессовка «вхолодную» очень скоро даст о себе знать: клапаны будут перегреваться, втулки — шататься в гнездах, увеличится расход масла.
Новую направляющую втулку с надетым на нее стопорным кольцом запрессовывают оправкой до упора этого кольца в плоскость головки цилиндра.
После запрессовки втулок обработка отверстий производится разверткой со стороны верхнего конца втулки. Более долговечными и точными являются алмазные развертки.
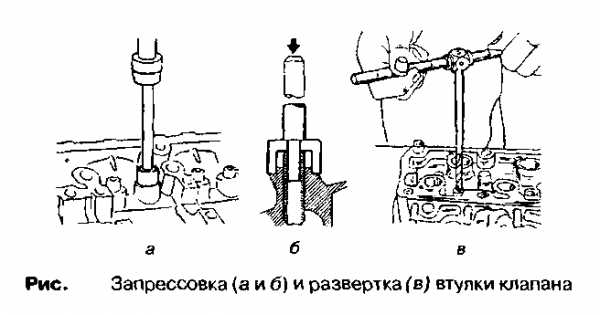
Перед заменой направляющих втулок впускного и выпускного клапанов первого и четвертого цилиндров необходимо отвернуть две шпильки крепления корпуса подшипников распределительного вала.
После запрессовки нужно развернуть отверстия в направляющих втулках развертками, а затем прошлифовать седла клапанов. Если менялись или восстанавливались направляющие втулки клапанов, то шлифовку седел ведут после завершения работы с втулками, чтобы направляющие стержни центрировались по новой поверхности втулок и обеспечивали соосность фасок с отверстиями втулок.
Для обеспечения точности диаметра отверстия и его расположения по отношению к рабочих фаскам седла и клапаны отверстия во втулках обрабатываются после запрессовки втулок в головку цилиндров.
Для устранения мелких дефектов фаску тарелки клапана шлифуют на обычных круглошлифовальных станках с углом фаски 45°25'-45°35' После шлифовки расстояние от базового диаметра фаски до плоскости тарелки не должно быть менее указанного в табллце.
У выпускного клапана не должен быть сошлифован слой твердого сплава, наплавленный на фаску. Биение рабочей фаски клапана относительно стержня должно составлять не более 0,02 мм.
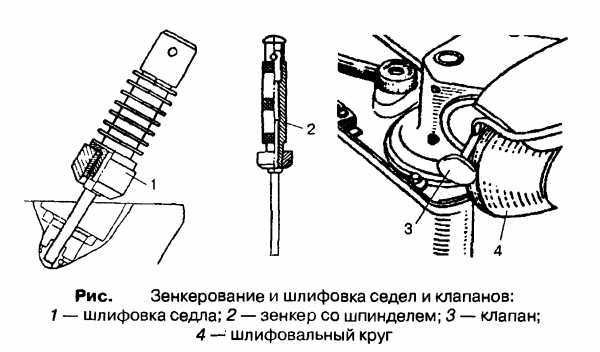
Головку нужно установить на подставку, очистить от нагара фаски седел клапанов соответствующими зенкерами, зенкеры надеть на шпиндель и центрировать направляющим стержнем, который вставляется в направляющие втулки клапанов(позиция 2). На направляющий стержень необходимо надеть пружину, установить на шпиндель конический круг для седел выпускных клапанов или круг для седел впускных клапанов (позиция 2), закрепить шпиндель в шлифовальной машинке и прошлифовать седло. При шлифовке фаски следует снимать как можно меньше металла. Во избежание вибрации и порчи фаски в момент соприкосновения круга с седлом машинка должна быть выключена. До работы следует выправить шлифовальный круг алмазом.Ширину рабочей фаски седел выпускных клапанов необходимо шлифовать до нужных размеров зенкером под углом 20° и зенкером, которым устраняется наклеп на внутреннем диаметре. Зенкеры следует применять с тем же шпинделем и стержнем. Сначала нужно шлифовать внутреннюю фаску до размера 0,33 мм, а затем фаску 20° — до ширины рабочей фаски 1,9-2,0 мм.
Перед установкой клапанов (и старых и новых) необходимо притереть их к седлам. Для этого следует надеть на стержень притираемого клапана легкую отжимную пружинку подходящих размеров и нанести на его фаску тонкий слой притирочной пасты зернистостью не более 20-50 мкм.Алмазные пасты желательно не применять, так как алмазная крошка иногда внедряется в седло и остается в нем, ускоряя его износ.Далее нужно вставить клапан с пружиной в направляющую втулку, надеть на его стержень приспособление или подобрать резиновую трубку так, чтобы она плотно надевалась одним концом на стержень клапана, а другим — на жало крестовой отвертки или на круглый напильник с ручкой. С помощью этого приспособления необходимо вращать клапан попеременно в обе стороны, слегка прижимая его к седлу. Вести притирку следует аккуратно, стараясь не снимать много металла, чтобы оставить возможность для последующих ремонтов. При появлении притертого пояска на деталях нужно разбавить пасту маслом, а когда притираемые поверхности станут совершенно гладкими, вести притирку на одном масле до получения матово-серого цвета рабочих поверхностей фаски клапана и его седла и блестящего цельного пояска.
Если нет разрывов слоя краски, нанесенной на седло и фаску тарелки клапана, при их контакте или если керосин, залитый в камеру сгорания при свободно вставленных в свои седла притертых впускном и выпускном клапанах, в течение 10 секунд не просачивается, значит, притирка сделана хорошо. После притирки нужно тщательно промыть обработанные детали и камеры сгорания от следов притирочной пасты.
Новый метод ремонта.
В последние годы применяется методика восстановления изношенной внутренней поверхности направляющих втулок без их выпрессовки специальным ручным инструментом (например, фирмы Neway) с роликовыми резцами для пластической деформации металла до 0,5 мм, компенсирующей износ внутренней поверхности втулки, и последующей разверткой до нужного размера. Резцы также формируют во втулке спиральный желобок для масла, улучшающий условия смазки стержня клапана. Зазор 0,03-0,05 мм между стержнем клапана и втулкой и этот желобок работают как лабиринтный сальник, обеспечивая смазку и отталкивая излишнее количество масла, помогая маслоотражательным колпачкам и уменьшая угар масла
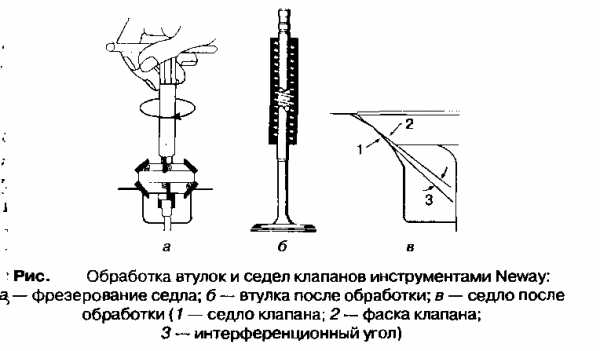
При традиционном методе обработки седел клапанов направляющая шарошки или зенкера свободно вращается во втулке клапана. При новом методе, предложенном фирмой Neway, фреза надевается на неподвижную ось, которая плотно фиксируется в ранее восстановленной втулке самоусганавливающей-ся цанговой направляющей. Фреза сидит на оси с зазором всего 0,5 мкм, обеспечивая минимальный допуск обработки.Каждая из трех предусмотренных технологией фасок на седле клапана получается за 3-4 оборота ручного инструмента. Фреза за счет уникальной заточки и формы режущих кромок формирует на поверхности седла клапана специальный микрорельеф, благодаря которому приработка клапана и седла на двигателе происходит быстро, а надобность в притирке отпадает.
Восстановление рабочих фасок клапанов выполняют специальным ручным инструментом Gizmatic-2 той же фирмы.
Клапан неподвижно фиксируют в специальной оправке, зажатой в слесарные тиски. После нескольких вращений фрезы с осевой подачей микролифтом получается идеальная концентрическая поверхность фаски клапана. На ней также формируется специальный микрорельеф, как и при обработке седла.
При работе инструментами Neway притирка не нужна совсем. После обработки клапанов и седел их идеальное сопряжение происходит по узкому пояску и обеспечивается не только формируемым микрорельефом поверхностей деталей, но и интерференционным углом между фасками. Достигается это небольшим (менее 1°) расхождением углов обработки рабочих поверхностей седла и клапана. В первые же секунды работы двигателя поясок сопряжения увеличивается за счет смятия выступов созданного микрорельефа на фасках, а затем происходит и полное уплотнение поверхности по всей ширине фаски.
Комплект инструментов фирмы Neway покупать не обязательно. Нужно только узнать, в какой мастерской он имеется, и отдать туда головку блока для обработки втулок и седел, а также клапанов.
ВАЗ 2115 | Осмотр, дефектовка и ремонт деталей головки блока цилиндров
automn.ru
КОВШ. Обслуживание двигателей внутреннего сгорания
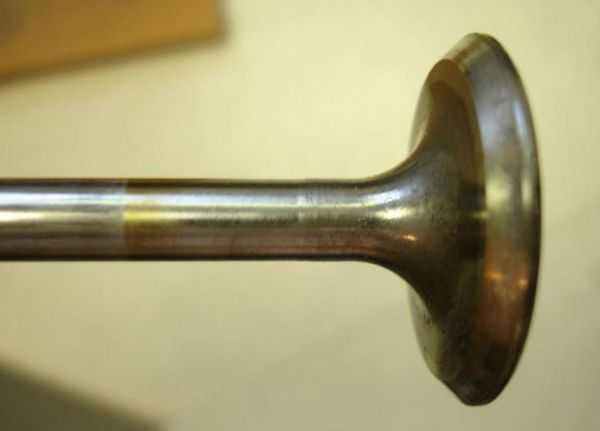
Исправные клапаны должны быстро и надёжно уплотнять камеру сгорания, выдерживать большие перепады температур и иметь хорошую износостойкость для обеспечения долговечности двигателя. Выход клапанов (или даже одного клапана) из строя приводит к нарушению работы двигателя. А в самом тяжёлом случае - к разрушению поршня, цилиндра или головки блока. Поэтому тщательная дефектовка клапанов очень важна при ремонте мотора.
Дефект 1. Сильный износ, задиры и царапины на стержне клапана.
Причины:
- Работа двигателя с недостаточным уровнем масла в картере.
- Работа двигателя на некачественном или грязном масле.
- Сильный перегрев, приводящий к разжижению масла.
- Попадание в масло топлива (бензина или дизтоплива) и, как следствие, разжижение масла.
Действия:
- Ремонт головки блока: замена направляющих втулок и клапанов, правка седёл клапанов. Проверка системы смазки, масляного насоса и при необходимости ремонт или замена масляного насоса. Чистка, промывка и продувка масляных каналов блока цилиндров и головки блока. Применение моторного масла надлежащего качества и регулярная, в предписанные производителем сроки, замена моторного масла и фильтра. Проверка системы охлаждения и при необходимости её ремонт. Проверка и при необходимости ремонт системы питания.
Дефект 2. Износ (выработка и раковины) на рабочей фаске тарелки клапана. Трещины и прогары тарелки клапана.
Причины:
- Перегрев двигателя.
- Неверно установленное опережение зажигания.
- Неотрегулированный зазор в клапанном механизме.
- Дефекты гидрокомпенсаторов.
- Дефекты и повреждения деталей газораспределительного механизма (толкателей, штанг, коромысел, распредвала, приводных шестерён).
- Неверно установленные фазы газораспределения.
Действия:
- Если выработка фаски клапана невелика - возможна шлифовка фаски. При прогарах или сильном износе - замена повреждённого клапана. Правка седла клапана обязательна в любом случае. Проверка, регулировка и при необходимости ремонт или замена деталей газораспределительного механизма. Замена гидрокомпенсаторов. Проверка системы охлаждения и при необходимости её ремонт. Проверка и при необходимости ремонт системы питания. Проверка и при необходимости ремонт системы зажигания.
Дефект 3. Изгиб стержня клапана. Повреждения (трещины и забоины) канавок под сухари.
Причины:
- Попадание в цилиндр посторонних предметов.
- Разрушение ремня или цепи привода газораспределительного механизма.
- Неверно установленные фазы газораспределения.
Действия:
- Замена повреждённого клапана, замена повреждённой направляющей втулки, правка седла клапана. Проверка, регулировка и при необходимости замена или ремонт других деталей клапанного механизма.
Примечание: Как правило, в результате описанных причин происходит соударение поршней и клапанов, что приводит к повреждению направляющих втулок, а также поршней, гильз цилиндров и головки блока цилиндров. В большинстве случаев необходима дефектовка указанных деталей и узлов.
Дефект 4. Повреждения (износ и деформация) торца стержня клапана.
Причины:
- Неотрегулированный зазор в клапанном механизме.
- Дефекты гидрокомпенсаторов.
- Дефекты и повреждения деталей привода клапанов (толкателей, штанг, коромысел).
- Неверно установленные фазы газораспределения.
Действия:
- При незначительных повреждениях возможна шлифовка торца клапана. В противном случае - замена клапана. Проверка, регулировка и при необходимости замена или ремонт других деталей газораспределительного механизма.
kovsh.com
Когда неисправен клапан - Моторный Центр на Федосеенко
Хорошо, когда машина новая - двигатель работает тихо, его не слышно даже на разгоне с полным «газом». Но идет время - и однажды вы замечаете, что от былой «тишины» не осталось и следа, а, открыв капот, видите некоего грохочущего зверя, который вместо привычного пения издает явно оскорбляющие слух звуки.
Шумность работы двигателя чаще всего связана с газораспределительным механизмом - большие зазоры и стук всегда соседствуют друг с другом. Первое, что приходит в голову - отрегулировать зазоры в приводе клапанов. Часто это помогает, но иногда после регулировки кажется, что стук стал даже сильнее: один или несколько клапанов продолжают стучать. И совершенно непонятно почему: ведь зазоры в норме, да и распределительный вал с виду хороший. Причина, похоже, не лежит на поверхности, она где-то внутри, но где? Надо бы разобраться, да некогда. А стук становится все громче.
То, что клапан - деталь ответственная, никому объяснять не надо. И то, что неисправности клапанов - штука не только серьезная, но и опасная, многим известно не понаслышке. Возникают подобные неисправности по разным причинам.
И встречаются среди них совершенно неочевидные, так что при ремонте не удается ограничиться только заменой неисправной детали.
Кстати, в любом случае перед тем, как что-либо ремонтировать или менять, полезно найти причину конкретной неисправности. Иначе та же участь в скором будущем может постигнуть и совсем новую, только что установленную деталь. А чтобы этого не случилось, желательно знать, в каких условиях она работает.
Как работает клапанОсновная задача клапанов - управление потоками топливовоздушной смеси и продуктов сгорания, поступающих в цилиндр или вытекающих из него. Следовательно, клапан при его открытии должен свободно пропускать смесь или газы, то есть обладать минимальным гидравлическим сопротивлением. В то же время закрытый клапан должен обеспечивать герметичность и полностью отделять полость цилиндра от впускной или выпускной системы двигателя.Kлапаны работают в условиях сильного нагрева от горячих газов, обтекающих их тарелки. И если впускной клапан при открывании периодически охлаждается поступающей в цилиндр топливовоздушной смесью, то выпускной работает в гораздо более жестких условиях. Открываясь на такте выпуска, он еще больше нагревается горячими выхлопными газами, и температура его тарелки достигает 850-900°С.Для того чтобы клапаны могли противостоять таким тепловым нагрузкам, их приходится изготавливать из специальных жаростойких сталей и сплавов с большим содержанием хрома, никеля, молибдена и даже вольфрама.Эти материалы весьма недешевы, из-за чего нередко выпускные клапаны изготавливают из разнородных материалов: тарелку - из жаростойкого сплава, а стержень - из легированной стали. Кстати, впускные и выпускные клапаны самых разных моторов очень легко отличить: тарелки выпускных клапанов не обладают магнитными свойствами.Чтобы снизить износ фаски при высоких рабочих температурах, на нее нередко наплавляют специальный твердый материал - стеллит. Реже применяют натриевое охлаждение клапана: натрий, перемещающийся во внутренней полости клапана при его открытии и закрытии, переносит тепло от горячей тарелки к более холодному стержню.Практика тем не менее показывает, что даже самый жаростойкий клапан все равно прогорит, если не будут выполнены и некоторые другие условия, главное из которых - плотная посадка тарелки в седле. Дело в том, что только хороший контакт клапана с седлом позволяет надежно отвести тепло от нагретой тарелки. Ведь седло довольно холодное, оно запрессовано в тело головки блока, охлаждаемой жидкостью.Через седло отводится до 75% всего тепла, поступающего к тарелке, - весьма и весьма значительная часть. Естественно, если контакт с седлом нарушен, тарелка сразу начинает перегреваться. Значит, до прогара жить клапану остается недолго. Ознакомиться с современными принципами обработки сёдел и клапанов можно прямо сейчас!Выглядит это как цепная реакция. Небольшая неплотность в сопряжении тарелки и седла приводит к прорыву газов. Отвод тепла от тарелки в этом месте отсутствует, и тарелка перегревается. Неплотность увеличивается, а вместе с ней растет и температура тарелки. В конце концов материал начинает разрушаться, туда устремляется еще больше горячих газов, и дефект тарелки быстро распространяется до тех пор, пока цилиндр полностью не выключается из работы из-за отсутствия компрессии.Как видим, хорошее сопряжение тарелки с седлом «убивает» сразу «двух зайцев»: снижает температуру клапана до приемлемого уровня и обеспечивает герметичность. И трудно сказать, что важнее. По крайней мере, для работоспособности самого клапана важно первое, а для двигателя в целом - второе (имеются в виду хорошие пусковые свойства, мощностные характеристики, экономичность).Кроме указанных условий, работа клапана (открытие и закрытие) должна быть достаточно «мягкой» и не вызывать излишнего шума. Шум или, точнее, стук клапанов - верный признак неисправности, а возникающие при стуке ударные нагрузки нередко сами по себе вызывают еще более серьезные неисправности и даже поломки клапанов.Откуда берется стук?Причин несколько. Самая простая уже упомянута - большой зазор в приводе. Кулачок распредвала из-за этого набегает на толкатель (рычаг или коромысло) не плавно, а с ударом, который тем сильнее, чем больше зазор.Что страдает в данном случае в первую очередь? То, что воспринимает ударную нагрузку: рабочие поверхности кулачка распредвала и толкателя, а также опорная поверхность толкателя и торец стержня клапана. На них нередко образуются повреждения в виде точечных раковин, которые в дальнейшем расширяются и углубляются.Но этим дело не ограничивается. Клапан не только с ударом открывается, но также резко, со стуком, закрывается. А это значит, что ударная нагрузка при закрытии приходится на уплотнительную фаску клапана и седло. Кроме того, в момент удара при посадке на седло на стержень клапана действует большая растягивающая нагрузка от пружины. Длительная работа в таких условиях весьма опасна: тарелка может просто оторваться от стержня либо стержень разрушится по другому слабому месту - канавке для сухарей.Но допустим, что зазоры в приводе клапанов нормальные, а стук все равно прослушивается.Чаще всего причина такого стука кроется в большом зазоре между стержнем клапана и направляющей втулкой. Ситуация эта наиболее характерна для старых, изрядно походивших, моторов. Иногда стук клапана связан с неконцентричностью седла и отверстия направляющей втулки, что является следствием перегрева головки блока или неправильно выполненного ремонта. При этом клапан садится на седло сначала одним краем тарелки, и только затем, перекатываясь во втулке в пределах зазора, полностью. Из-за этого, кстати, износ направляющей втулки быстро прогрессирует.Быстрый износ направляющей втулки и стук клапана возникают и по другим, более сложным, причинам. Например, когда гнездо цилиндрического толкателя клапана несоосно, либо имеет перекос по отношению ко втулке. Подобный дефект иногда встречается на отечественных моторах. Стук возможен также из-за повышенных зазоров в деталях привода - в осях коромысел, в гнездах цилиндрических толкателей, а также в подшипниках распределительного вала.Все эти стуки на слух достаточно похожи, и поэтому часто выделить конкретную причину без разборки и внимательной ревизии состояния деталей не удается. Но в любом случае нужно иметь в виду, что раз есть стук, значит, нагрузки в местах контакта деталей носят ударный характер. Как правило, такой стук быстро прогрессирует, что грозит не только износом клапанов и сопряженных с ними деталей, но и их поломкой.Почему сломался клапан?Сам по себе стук может и не вызвать поломку. Но в любом случае важно понять, почему клапан начал стучать? А причин, спровоцировавших появление стука, оказывается, немало...Самая распространенная - неграмотная эксплуатация, неквалифицированное и несвоевременное обслуживание двигателя. Очевидно, регулировка зазоров в приводе клапанов от случая к случаю - верный способ ускорить износы, вызвать стуки, а затем и поломки.Очень опасно при регулировке устанавливать слишком малые зазоры: при работе двигателя клапаны нагреются, их длина увеличится, и, когда зазор выберется полностью, клапаны «повиснут». А тогда неплотная посадка на седло приведет к перегреву тарелок и прогару.Довольно распространенная причина прогара выпускных клапанов - слишком позднее зажигание. Особенно если двигатель длительное время работает на больших частотах вращения и нагрузках. Но и раннее зажигание - тоже для клапанов не подарок, ведь температура газов в цилиндре в этом случае максимальна. Значит, неправильная установка опережения зажигания вызывает не только потерю мощности и увеличение расхода топлива, но и неисправности клапанов.Использование некачественного масла - тоже возможная причина износа втулок и стержней клапанов. Кроме того, такое масло имеет свойство коксоваться в нижней части стержней клапанов. Из-за этого клапан будет все туже ходить во втулке, а затем и вовсе может заклинить в ней.В конце концов он получит-таки поршнем по тарелке со всеми вытекающими последствиями.Нагар, откладывающийся на тарелках клапанов (особенно впускных), например, из-за износа маслосъемных колпачков, тоже небезобидная вещь. Достигая солидной толщины, нагар начинает откалываться. И частицы довольно крупных размеров легко могут попасть между фаской и седлом клапана. А после этого плохой контакт с седлом и перегрев тарелки неминуем.Интересно отметить, что значительные отложения нагара на клапанах, вызывающие подобные неприятности, далеко не всегда связаны с износом маслосъемных колпачков. Судите сами: повышенное давление в картере из-за неисправности системы вентиляции или износа цилиндропоршневой группы легко может выдавливать масло к тарелкам клапанов даже через самые новые колпачки.Некоторые «горячие головы» предпочитают отсоединять шланг вентиляции картера от воздушного фильтра и выводить его куда-нибудь под днище автомобиля - так якобы мотору «легче дышится». И невдомек им, что на некоторых режимах в картере создается разрежение, и пыль, засасываемая в двигатель через шланг, не только быстро загрязняет масло и масляный фильтр, но и попадает к направляющим втулкам и стержням клапанов. Комментарии, как говорится, излишни.Но, пожалуй, самые серьезные последствия для клапанов таит в себе несоблюдение сроков замены ремня привода распределительного вала. О том, что на многих современных моторах клапаны в случае обрыва ремня деформируются, мы уже писали (см. «АБС-авто», 1999 г., № 6). Добавим только, что попытки поставить новый ремень и так доехать, к примеру, до гаража, редко оканчиваются благополучно. Деформированные клапаны каждый раз при посадке на седло испытывают большие изгибающие нагрузки и через 10-15 минут работы, как правило, ломаются. А такая поломка клапана - это, как минимум, замена поршня, головки блока, шатуна.Целый ряд проблем вносит в работу клапанов некачественно выполненный ремонт. Например, наиболее «опытные» механики не утруждают себя использованием специальных приспособлений для сжатия пружин клапанов. Их «коронные» инструменты - стальная труба и молоток: стукнул посильнее - и порядок. Только вот клапан может получить повреждение по канавке для сухарей. А потом, много позже, в этом месте сломаться.Очень опасно попадание абразивной пасты в направляющую втулку во время притирки клапана к седлу. Промыть такую втулку - целая история. Но если этого не сделать, история получится с продолжением максимум на 5-10 тысяч километров пробега. После этого износ втулки и стержня, скорее всего, превысит все разумные пределы.Некоторые механики стремятся сделать зазор клапана во втулке как можно меньше. Это заблуждение нередко приводит к заклиниванию клапана с весьма неприятными последствиями.Еще одна ошибка - притирка клапанов без правки седел. Как показывает практика, после длительной эксплуатации и особенно после замены направляющих втулок их несоосность с седлами - обычное дело. В подобных случаях одна лишь притирка, скорее всего, приведет к стуку клапанов и быстрому износу деталей.Когда головка блока полностью собрана с клапанами, очень легко испортить всю работу, обстукивая клапаны молотком. Результат может быть тот же, что и при «ударной» разборке, особенно у современных многоклапанных двигателей с клапанами малого диаметра.Из всех этих факторов складывается довольно ясная картина: когда клапан неисправен, ему, скорее всего, кто-то в этом «помог».И задача механика - не только не стать очередным «помощником», но ликвидировать все последствия прежней «помощи», которые обычно несут на себе после долгой работы клапаны и другие детали. Только так можно быть уверенным, что клапан не подведет.?
www.motornn.ru
Дефектовка головки цилиндров ВАЗ-2109
Параметры пружин клапанов для определения их упругости.Наружная пружина:высота в свободном состоянии 45,2 ммвысота под нагрузкой 26,0± 1,7 кгс 33,7 ммвысота под нагрузкой 46,2±2,4 кгс 24,7 мм
Внутренняя пружина:высота в свободном состоянии 34,1 ммвысота под нагрузкой 9,0 ± 0,8 кгс 29,7 ммвысота под нагрузкой 27,5 ± 1,5 кгс 20,7 мм.
а — седло впускного клапанаб — седло выпускного клапанаI — новое седлоII — седло после ремонтаВеличина зазоров между клапаном и направляющей втулкой, мм:
номинальный зазор для впускных клапанов 0,022-0,055номинальный зазор для выпускных клапанов 0,029-0,062предельно допустимый зазор для впускных и выпускных клапанов--- 0,3Если зазор меньше предельно допустимого, попробуйте заменить клапан.
Если зазор превышает предельно допустимый, замените направляющую втулку.1. Промойте детали головки блока в бензине, протрите и просушите их.
2. Очистите камеры сгорания от нагара. Осмотрите головку. Если на ней есть трещины или следы прогара в камерах сгорания, замените головку. |
3. Проверьте плоскостность поверхности, прилегающей к блоку цилиндров. Для этого поставьте металлическую линейку ребром на поверхность головки по центру вдоль, а затем по диагоналям и замерьте щупом зазор между плоскостью головки и линейкой. Замените головку, если зазор превысит 0,1 мм. |
4. Очистите нагар с клапанов. Это можно сделать подходящим металлическим инструментом |
5. Осмотрите клапаны. Замените клапаны со следующими дефектами: глубокие риски и царапины на рабочей фаске, трещины, деформация стержня клапана, коробление тарелки клапана, следы прогара. Неглубокие риски и царапины на рабочей фаске можно удалить притиркой клапанов. |
6. Повреждения рабочей фаски клапанов, которые невозможно вывести притиркой, можно прошлифовать на специальном станке. При шлифовке надо выдержать размеры, указанные на рисунке. В скобках даны отличающиеся размеры для двигателя ВАЗ-21083. 7. Проверьте состояние пружин клапанов. Искривленные, поломанные или имеющие трещины пружины замените. Проверьте упругость пружин. для этого измерьте высоту пружин в свободном состоянии, а затем под двумя различными нагрузками. Если пружина не соответствует требуемым параметрам, замените ее. |
8. Проверьте состояние седел клапанов. На рабочих фасках седел не должно быть следов износа, раковин и коррозии. Незначительные повреждения (мелкие риски, царапины и т.п.) можно удалить притиркой клапанов. |
9. Более значительные дефекты седел клапанов устраняются шлифовкой. При шлифовке выдержите размеры, указанные на рисунке. Сначала шлифуется фаска под углом 20˚, затем фаска под углом 45°. После шлифовки надо притереть клапаны, затем тщательно очистить и продуть сжатым воздухом головку блока, чтобы в каналах и камерах сгорания не осталось частиц абразива. В скобках даны отличающиеся размеры для двигателя ВАЗ-21083.
10. Проверьте зазор между направляющими втулками и клапанами. Зазор вычисляется как разность между диаметром отверстия во втулке и диаметром стержня клапана.
11. Осмотрите толкатели клапанов. Если на рабочей поверхности толкателя имеются задиры, царапины или другие повреждения, замените толкатели. |
12. Осмотрите регулировочные шайбы. На их рабочих поверхностях не должно быть задиров, забоин, царапин, следов ступенчатого или неравномерного износа металла. При таких дефектах шайбы надо заменить. На шайбах допускаютсяконцентрические следы приработки с кулачками распредвала. |
13. Измерьте длину болтов крепления головки блока, так как при многократной затяжке они вытягиваются. Если длина болтов превышает 135,5 мм, замените болты. |
14. для проверки герметичности головки заглушите отверстие в патрубке рубашки охлаждения в заднем торце головки, переверните головку камерами сгорания вверх и залейте керосин в каналы рубашки охлаждения. Если появились течи керосина, значит головка не герметична и ее надо заменить. |
autoruk.ru
7. Клапаны
Клапаны (рис. IV.4.7) впускные изготавливают у двигателей ЗИЛ-130 из стали 40Х10С2М, HRC 28—38, у ЗМЗ-53 — из стали 40Х9С2, HRC 30—40, ЯМЗ — из стали 4Х10СМ2, HRC 35 — 40; выпускные у ЗИЛ-130 из стали ЭИ-992, HRC 28—38, у. ЗМЗ-53 — из стали ЭП-303, HRC 30, у ЯМЗ — из стали 4Х14Н14В2М, HRC 25—30, торец стержня клапана изготавливается из стали 40ХН. Рабочие фаски клапанов двигателей ЗИЛ и ЗМЗ имеют жаростойкую наплавку из сплава ВХН-1, HRC20—30, твердость торцов стержней всех клапанов HRC 43—57. Выпускные клапаны двигателей ЗИЛ-130 имеют полость, заполненную для лучшего охлаждения головки металлическим натрием; стержень его покрыт слоем хрома толщиной 0,002—0,006 мм для повышения износостойкости.
Основные дефекты клапанов приведены в табл. IV.4.7.
Износ, риски и раковины на рабочей фаске устраняются шлифованием на специальном станке МШ-29 шли фовальным кругом ПП 500X20X305 марки Э60СМ1К «как чис то». Угол фаски впускного клапана равен 60°30'+15', выпускного 45°30/+15'. После шлифования размер а должен быть не менее допустимого. ' >•
- Изгиб стержня устраняют правкой на плите вручную.
Изношенный торец стержня шлифуют «как чисто» на заточном станке ЗА64 шлифовальным кругом Ц1П 1000X13X20 марки Э46СМ1К. После шлифования, размер б у клапанов должен быть не менее 138,0 мм.
, Таблица IV.4.7 Дефекты клапана7
Позиция на рис. ' IV.4.7 | Дефекты. | размеры, допустимые без ремонта, мм | |
"/',■'; | Трещины, коробление, выкрашивание на- | Браковать | |
плавленного слоя | |||
2 | Износ стержня клапана: | ||
, впускного | ii ,«_0,085 | ||
выпускного | ii n-0,080 ■ , ii.u-0,005 | ||
3 | Износ на торце -стержня | Браковать при б. менее 138,0; | |
V, * | Изгиб стержня , | Непрямолинейность поверхности А не более 0,020 | |
5 | Износ, риски и раковины на рабочей | ||
фаске клапана: | |||
впускного | Браковать при а менее- 2,0 | ||
выпускного . | Браковать при а менее 2,5 |
266
Изношенные стержни восстанавливают шлифованием их на бесцентровошлйфо-вальных станках 3180 шлифовальным кругом ПП 500Х XI50X305 марки Э60СМ2К до ремонтного размера (впу-
» «то -0,060
Рис. IV.4.7. Основные дефекты. выпускного клапана двигателя ЗИЛ-130
скнои fc910,o_o,o85' выпускной 010,8 -о',оо5 мм). Клапаны ре монтного размера клеймят ся индексом Р на поверхности Г. При повторном восстановле нии стержни хромируют или осталивают с последующим шлифованием под размер рабочего чертежа. • •■■■'•■'■'
После восстановления клапаны должны отвечать следующим техническим требованиям: . .
нецилиндричность поверхности Л (см. рис. IV.4.7) должна быть не более 0,010 мм; биение поверхности'Б1 относительно'поверхности Л не более 0,030 мм; торцовое биение поверхности Г относительно поверхности Л не более 0,030 мм;
шероховатость поверхностей должна соответствовать: Л—86 классу (#а = 0,504-0,40), £—76 классу (#а= 1,04-0,8), ' Г—7а классу (#а= 1,254-1,0).
Чашки коробки дифференциалов (рис. IV.8.9) изготавливают у автомобилей ЗИЛ-130 из стали 45, НВ 163—197, у ГАЗ-53А — из ковкого чугуна КЧ 35-10, НВ 121 — 149, у МАЗ-500 —из КЧ 37-12.
Основные дефекты чашки коробки дифференциала приведе ны в табл. IV.8.9. ■
В процессе разборки правая и левая чашки не должны раз укомплектовываться. При наличии на. чашках трещин их бра куют. •' !■■■■".
Задиры, риски или неравномерный износ торца под шайбу, шестерни полуоси устраняют обработкой его до ремонтного раз мера с компенсацией размера а за счет постановки* при сборке шайб того же ремонтного размера. Размер а по рабочему черте жу 49,0+0'2 мм, первый ремонтный — 49,2+0-2 мм, второй — 49,4+0'2 мм, третий — 49,6+0'2 мм, при соответствующей толщине шайб: основного размера 1Дч>,к> мм, первого — 2,0-оло мм, вто рого — 2,2_о,ю мм, третьего — 2,4-0,ю мм. При размере а более 49„8 мм чашку бракуют. Чашки коробки дифференциала ремонт ного размера маркируют по поверхности Е индексами клеймения IT, 2T, ЗТ. ...-'■
Изношенные отверстия под шипы крестовины восстанавливают еверлением новых отверстий, расположенных под углом 45° к изношенным, с последующим развертыванием их под размер рабочего чертежа (028+°о'°!>° мм).
При задирах, рисках или износе сферической поверхности чашки коробки дифференциала ее растачивают фасонным резцом под один из ремонтных размеров с компенсацией увеличенного размера при сборке ремонтными шайбам-и. Все ремонтные разме-
ры маркируют клеймением по поверхности -Е индексами 1С, 2С, ЗС, 4С, 5С, 6С. %
При износе отверстий под стяжные болты чашку закрепляют в кондукторе на столе сверлильного станка 2118 и сверлят новые отверстия в промежутке между старыми 014,0 +о'24 мм>и зенкуют их с двух сторон.
Износ шейки под роликовый подшипник устраняют хромированием, осталиванием, вибродуговой наплавкой или раздачей. Вибродуговую наплавку производят по следующей технологии: чашку устанавливают в приспособление, обтачивают шейку до 073 мм, затем на установке УАНЖ-4 ее наплавляют до диаметра 78 мм при режиме; электродная проволока Св-08 01,6 мм, скорость подачи 1,3—1,4 м/мин, частота вращения детали 2,0 об/мин, расход охлаждающей жидкости 0,05 л/мин. После наплавки шейку обтачивают с припуском 0,15 мм и шлифуют под размер ]рабочего чертежа (075+°'о2о мм)-
Отверстие под шейку шестерни полуоси восстанавливают вне-ванным осталиванием, вибродуговой наплавкой или постановкой ДРД с последующей расточкой под размер рабочего чертежа.
Восстановленная чашка коробки дифференциала должна отвечать следующим техническим требованиям:
при установке по поверхности А и опоре на поверхность Д: биение поверхности В не более 0,060 мм, радиальное биение поверхностей К и И не более 0,080 мм, торцовое биение поверхности Ж не более 0,040 мм, а поверхности Б не более 0,050 мм;-
шероховатость поверхности И должна соответствовать 7а классу (Ra = 1,25ч-1,0).
Полуоси (рис. IV.8.10) изготавливают у автомобилей ЗИЛ-130 из стали 45РП, HRC 52—58 в зоне Б, у ГАЗ-53А — из стали 40, HRС 42 не менее, у МАЗ-500 — из стали 38ХГС, HRC 44—50.
Основные дефекты полуоси приведены в табл. IV.8.10.
304
Таблица IV.8.10
Дефекты полуоси | , - | |
Позиции 'на рис. IV.8.10 | • Дефекты . . | Размеры, допустимые без ремонта, мм |
/ 2 3 4 | Погнутость полуоси Износ шлицев по толщине Износ конусных отверстий под разжимные втулки Погнутость фланца | ' 55,0 |
При наличии обломов или трещин, а также скручивания полуоси бракуют.
Погнутость определяют после установки полуоси в центрах При помощи индикаторной головки. Величина радиального биения должна быть: поверхности В не более 0,30 мм, поверхности Д не более 1,0 мм. При больших значениях погнутости полуоси правят на прессе ГАРО типа 208 до устранения дефекта с последующим подрезанием поверхности Г «как чисто», выдерживая при этом толщину фланца не менее 11,0 *мм.' :
Погнутость фланца определяют наличием торцового биения, которое при установке полуоси в центрах должно быть на поверхности Г не более 0,10 мм. При большем значении биения фланца поверхность Г подрезают «как чисто». При размере а менее 11,0 мм полуось бракуют.
Состояние конусных отверстий под разжимные втулки проверяют конусным калибром с углом конуса 39° и большим диаметром -24 мм. При несовпадении торцов детали и калибра более чем на 1,0 мм отверстия подлежат восстановлению по следующей технологии: их рассверливают до 022 мм и заплавляют (сила постоянного тока 160—190 А, электроды Э-42, 04 мм), затем с двух сторон подрезают торцы . фланца и сверлят отверстия 012,5 мм с последующей зенковкой до 020 мм.
Изношенные по толщине шлицы восстанавливают на плавкой -под слоем флюса на установке УАНЖ-514 НИИАТ. Впадины между шлицами и шлицевую шейку наплавляют продольными швами. Наплавку ведут до 057 мм (сила постоян ного тока 230 А, напряжение 27 В, проволока марки
Нп-ЗОХГСА диаметром 1,8 мм, скорость наплавки 14,4 м/ч, ско- РисIV81L основные дефекты сту- рость подачи проволоки Пицы заднего колеса автомобиля
137 м/ч, флюс АН-348А). ЗИЛ-130
Таблица IV.8.11 Дефекты ступиц задних колес
Позиции на рис. 1У.8Л1 | Дефекты | Размеры, допустимые без ремонта, мм |
/ 2 3 4 5 | Трещины на ребрах Износ отверстия под наружное '' кольцо дружного подшипника Износ отверстия под наружный сальник Срыв резьбы Износ отверстия под наружное кольцо внутреннего подшипника | i .134,990 136,400 Не более двух ниток ;, 149,990 |
Затем полуось проверяют на биение и при необходимости правят, шлицёвую (лейку протачивают, снимают фаску и фрезеруют шлицы на фрезерном станке 5350А. Шлицевой конец затем закаливают ТВЧ С нагревом до температуры 850—900°С и охлаждением в масле и отпускают при температуре 575—600°С с-последующим охлаждением на воздухе.
Валы рулевых сошек (рис. IV.9.3) изготавливают у автомобилей ЗИЛ-130 из стали 20ХГН4А, HRC 56—62 в зоне Б, в зоне В HRC 25—35, у ГАЗ-53А — из стали 30Х, HRC не менее 40, у МАЗ-500 — из стали ЙОХНЗА, HRC 60—64.
Рис. IV.9.3. Основные де фекты вала рулевой со шки автомобиля ЗИЛ-130
дона Б
315
Таблица fV.9.3
studfiles.net
Дефектовка деталей газораспределительного механизма Mitsubishi Outlander XL 2007
Инструменты:
- Микрометр
- Нутромер
Детали и расходники:
- Впускные и выпускные клапаны для замены
- Пружины клапанов для замены
- Распределительный вал для замены
Проверка впускных и выпускных клапанов.
1. Очистите нагар с клапанов подходящим инструментом (например, металлической щеткой). Затем внимательно осмотрите клапаны.
2. Заменить клапаны необходимо при наличии таких дефектов: глубокие риски и следы прогара на рабочей фаске, коробление тарелки, деформация стержня, износ торца от контакта с нажимным болтом. Неглубокие риски и царапины на рабочей фаске можно вывести притиркой клапанов.
Составляющие клапана:
1 - рабочая фаска;
2 - тарелка клапана;
3 - стержень;
4 - торец клапана.
3. Проверьте состояние седел клапанов. На рабочих фасках седел не должно быть следов износа, раковин, коррозии и прочего. Седла клапанов можно заменить в специализированной мастерской. Незначительные повреждения (мелкие риски, царапины и прочее) можно вывести притиркой клапанов. Более значительные дефекты седел клапанов устраняют шлифованием. Седла рекомендуется шлифовать в специализированной мастерской.
4. Имея слесарный навык, эту работу можно выполнить вручную с помощью набора специальных фрез. Сначала обрабатывают фаску а под углом 44° затем фаску б под углом 30° и фаску в под углом 65°. После шлифования необходимо притереть клапаны.
Места обработки фасок седел клапанов
5. Проверьте состояние пружин клапанов. Искривленные, поломанные или с трещинами пружины замените.
Распределительный вал заменяют в следующих случаях:
- упало давление в системе смазки двигателя. Причиной этой неисправности часто бывает повышенный износ шеек распределительного вала и гнезд в корпусах подшипников вала. При износе гнезд заменяют головку блока в сборе;
- износ кулачков вала.
Кулачки распределительного вала:
1 - опорная шейка распределительного вала;
2 - низкоскоростные впускные кулачки;
3 - высокоскоростные впускные кулачки;
4 - выпускной кулачок.
1. Осмотрите распределительный вал. На рабочих поверхностях шеек не допускаются задиры, забоины, царапины, наволакивание алюминия от гнезд в головке блока. На рабочих поверхностях кулачков не допускается износ, задиры и износ кулачков в виде огранки. Вал с обнаруженными дефектами замените.
2. В мастерских, оборудованных специальными инструментами и приспособлениями, можно проверить радиальное биение шеек распределительного вала.
3. Осмотрите опоры распределительного вала в головке блока. На рабочих поверхностях опор под шейки не допускаются риски, царапины, задиры, чрезмерный износ.
4. Измерьте микрометром диаметры опорных шеек вала. Диаметр шеек должен составлять 45,00 мм.
5. Измерьте микрометром диаметры впускных и выпускных кулачков вала.
6. Если значения отличаются от параметров нормы, замените распределительные валы.
Таблица нормы диаметров кулачков распределительного вала
В статье не хватает:
- Фото инструментов
- Фото деталей и расходников
- Качественных фото ремонта
Источник: http://carpedia.club
carpedia.club