Диаметр клапана ваз 2101
ВАЗ 2101 | Номинальные и ремонтные размеры деталей и пределы допустимых износов
впускной клапан
выпускной клапан
37,2
32,4 (32,8 для DS выпуска до сентября 1985 г.)
2,0
2,4
9,2
9,7
45
45
30
30
8,013 – 8,035
8,013 – 8,035
1,0
1,3
28,0
33,0
7,97
7,95
3,5
шлифовке не подлежит
0,5
шлифовке не подлежит
98,7 (91,0 для двигателя NP)
98,5 (90,8 для двигателя NP)
98,2 (90,5 для двигателя NP)
98,0 (90,3 для двигателя NP)
45
45
0,25 ± 0,05
0,45 ± 0,05
0,20 ± 0,05
0,40 ± 0,05
0,03
0,08
81,01
81,26
81,51
82,01
коренных
шатунных
54,0-0,022 -0,042
47,8-0,022 -0,042
53,75-0,022 -0,042
47,55-0,022 -0,042
53,5-0,022 -0,042
47,3-0,022 -0,042
53,2-0,022 -0,042
47,05-0,022 -0,042
53,96 – 53,98
47,76 – 47,79
53,71 – 53,73
47,51 – 47,53
53,46 – 53,48
47,26 – 47,29
53,21 – 53,23
47,01 – 47,03
0,03
0,07 – 0,17
0,25
0,03 – 0,08
0,17
80,98
81,23
81,48
81,98
DR 8,1
DS, NP4,4
57 (54 выпуска до июля 1985 г.)
компрессионное
маслосъемное
0,3 – 0,45
0,25 – 0,5
1,0
1,0
0,02 – 0,05
–
1,05
–
0,12
0,37
0,15
0,01
26,0
25,75
132,6
0,05
0,2
0,15
впускной клапан
выпускной клапан
37,2
30,8
2,0
2,0
9,6
9,0
45
45
30
30
8,013 – 8,035
8,013 – 8,035
1,0
38,0
33,0
7,97
7,95
3,5
шлифовке не подлежит
0,5
шлифовке не подлежит
91,0
90,8
90,05
90,3
45
45
0,25 ± 0,05
0,45 ± 0,05
0,20 ± 0,05
0,40 ± 0,05
0,07
79,51
79,76
80,01
80,51
81,01 (82,51 для двиг. NF)
81,26 (82,76 для двиг. NF)
81,51 (83,01 для двиг. NF)
коренных
шатунных
57,96 – 57,98
45,96 – 45,98 (47,76 – 47,78 двигатели 2 л с июля 1983 г. остальные не турбо с июля 1984 г.)
57,71 – 57,73
45,71 – 45,73 (47,51 – 47,53 двигатели 2 л с июля 1983 г. остальные не турбо с июля 1984 г.)
57,46 – 57,48
45,46 – 45,48 (47,26 – 47,28 двигатели 2 л с июля 1983 г. остальные не турбо с июля 1984 г.)
57,21 – 57,23
45,21 – 45,23 (47,01 – 47,03 двигатели 2 л с июля 1983 г. остальные не турбо с июля 1984 г.)
0,07 – 0,18 (0,07 – 0,23 с 1984 г.)
0,25
0,16
79,48
79,73
79,98
80,48
80,98 (82,48 для двиг. NF)
81,23 (82,74 для двиг. NF)
81,48 (82,98 для двиг. NF)
0,25 – 0,5
1,0
0,02 – 0,08
0,1
0,12
0,4
0,15
132,75
automn.ru
Головка цилиндров и клапанный механизм Вики о ВАЗ 2101 и ВАЗ 2102
Головка цилиндров и клапанный механизм
Основные размеры головки цилиндров, клапанов и направляющих втулок
Головка цилиндров – общая для четырех цилиндров, отлита из алюминиевого сплава. Она унифицированная, т.е. одинаковая для двигателей 2101, 21011 и 2103.
В головку цилиндров запрессованы чугунные седла и направляюшие втулки клапанов. Рабочие фаски седел обрабатываются после запрессовки в сборе с головкой цилиндров, чтобы обеспечить точную соосность фасок с отверстиями направляющих втулок клапанов.
Отверстия во втулках обрабатываются также после запрессовки втулок в головку цилиндров. Это делается для обеспечения точности диаметра отверстия и его расположения по отношению к рабочим фаскам седла и клапана. В отверстиях направляющих втулок имеются спиральные канавки для смазки. У втулок впускных клапанов канавки нарезаны до половины длины отверстия, а у втулок выпускных клапанов – на всей длине отверстия.
Сверху на направляющие втулки надеваются маслоотражательные колпачки из тепломаслостойкой резины со стальным арматурным кольцом. Колпачки охватывают стержни клапанов и служат для уменьшения проникновения масла в камеру сгорания через зазоры между направляющей втулкой и стержнем клапана.
Каждый клапан имеет две цилиндрические пружины: наружную и внутреннюю, опирающиеся на две опорные шайбы. Вверху пружины упираются в тарелку, которая удерживается на стержне клапана двумя сухарями, имеющими в сложенном виде форму усеченного конуса.
Снятие и установка на автомобиле
Головку цилиндров снимают с двигателя на автомобиле, если для устранения неисправности не нужно снимать сам двигатель или если необходимо только удалить нагар с поверхности камеры сгорания и клапанов.
Снятие
1. Слейте охлаждающую жидкость из радиатора и блока цилиндров и снимите воздушный фильтр.
2. Отсоедините провода от аккумуляторной батареи, свечей зажигания и от датчика указателя температуры охлаждающей жидкости.
3. Отсоедините трос привода воздушной заслонки от карбюратора.
4. Ключом 67.7812.9514 выверните свечи зажигания и датчик температуры охлаждающей жидкости.
5. Отсоедините тяги привода дроссельной заслонки от промежуточного рычага на крышке головки цилиндров и снимите крышку.
6. Поверните коленчатый вал до совмещения метки на шкиве с длинной меткой на крышке привода распределительного вала (см. рис. Расположение меток для установки зажигания), а метки на звездочке распределительного вала с меткой на корпусе подшипников распределительного вала (см. рис. Проверка совпадения установочной метки на звездочке распределительного вала с меткой на корпусе подшипников).
7. Отсоедините шланг от трубки подвода жидкости к отопителю, а от выпускного коллектора – кронштейн крепления трубки отвода жидкости из отопителя.
8. Отсоедините шланги от карбюратора, впускного трубопровода и от выпускного патрубка охлаждающей рубашки головки цилиндров.
9. Отсоедините от выпускного коллектора защитный щиток стартера и приемную трубу глушителей.
ВНИМАНИЕ: Выпускной коллектор и впускной трубопровод с карбюратором лучше оставить на головке. Их можно снять позже при разборке головки цилиндров.
10. Отпустите колпачковую гайку натяжителя цепи, отожмите монтажной лопаткой шток натяжителя и зафиксируйте его колпачковой гайкой.
11. Снимите звездочку распределительного вала и корпус подшипников вместе с распределительным валом.
12. Отверните болты крепления головки цилиндров к блоку и снимите головку.
Установка
1. Для того, чтобы снова установить и закрепить головку на блоке цилиндров, проведите описанные операции в обратной последовательности, при этом:
не забудьте поставить прокладку головки цилиндров и прокладку крышки головки;
затяните болты крепления головки в последовательности, указанной на рис Порядок затягивания болтов головки цилиндров, а гайки шпилек корпуса подшипников распределительного вала – в последовательности, указанной на рис. Порядок затягивания гаек корпуса подшипников распределительного вала.
2. Болты крепления головки цилиндров затягивайте в два приема:
предварительно моментом 33,3–41,16 Н·м (3,4–4,2 кгс·м) болты 1–10;
окончательно моментом 95,94–118,38 Н·м (9,79–12,08 кгс·м) болты 1–10 и моментом 31,36–39,1 Н·м (3,2–3,99 кгс·м) болт 11.
3. При установке цепи обращайте внимание на совпадение установочных меток (см. рис. Проверка совпадения установочной метки на звездочке распределительного вала с меткой на корпусе подшипников и рис. Расположение меток для установки зажигания). Натягивайте цепь, как указано в соответствующем подразделе.
4. При установке крышки головки цилиндров с прокладкой, гайки крепления крышки затягивайте моментом не более 7,85 Н·м (0,8 кгс·м), чтобы не вызвать разрыв прокладки по крепежным отверстиям и коробление крышки. При ремонте двигателя прокладку крышки рекомендуется заменять новой.
5. После установки головки цилиндров проверьте и отрегулируйте момент зажигания.
Разборка и сборка
ПОРЯДОК ВЫПОЛНЕНИЯ
1. Установите головку цилиндров на доску А.60335.
2. Отсоедините выпускной коллектор и впускной трубопровод с карбюратором (одновременно удаляется заборник горячего воздуха).
3. Отсоедините выпускной патрубок охлаждающей рубашки.
4. Отсоедините патрубок отвода жидкости к отопителю.
5. Снимите рычаги 11 (см. рис. Детали клапанного механизма) клапанов, освобождая их от пружин 12. Снимите пружины рычагов.
Детали клапанного механизма
1 – клапан; 2 – стопорное кольцо; 3 – направляющая втулка; 4 – маслоотражательный колпачок; 5 – опорная шайба наружной пружины; 6 – опорная шайба внутренней пружины; 7 – внутренняя пружина; 8 – наружная пружина; 9 – тарелка пружин; 10 – сухари; 11 – рычаг привода клапана; 12 – пружина рычага; 13 – регулировочный болт; 14 – контргайка регулировочного болта; 15 – втулка регулировочного болта; 16 – стопорная пластина пружины рычага
6. Ослабьте контргайки 14, выверните регулировочные болты 13 и втулки 15 регулировочных болтов.
7. Установите приспособление А.60311/R, сожмите пружины клапанов и освободите сухари (1 – приспособление А.60311/R; 2 – монтажная доска А.60335). Взамен переносного приспособления А.60311/R можно применять также стационарное приспособление 02.7823.9505.
8. Снимите пружины клапанов с тарелками и опорными шайбами.
9. Поверните головку цилиндров и выньте с нижней стороны клапаны.
10. Снимите маслоотражательные колпачки с направляющих втулок.
11. Собирайте головку цилиндров в обратной последовательности.
Очистка головки цилиндров
1. Установите головку на подставку А.60353.
2. Удалите нагар из камер сгорания и с поверхности выпускных каналов металлической щеткой, приводимой во вращение электрической дрелью. Очистите и осмотрите впускные каналы и каналы подвода масла к рычагам привода клапанов.
Проверка и шлифование седел клапанов
Профиль седла впускного клапана
![]() | |
I – новое седло; | II – седло после ремонта |
Профиль седла выпускного клапана
![]() | |
I – новое седло; | II – седло после ремонта |
Форма фасок седел клапанов показана на рис. Профиль седла впускного клапана и рис. Профиль седла выпускного клапана.
На рабочих фасках седел (зона контакта с клапанами) не должно быть точечных раковин, коррозии и повреждений. Небольшие повреждения можно устранить шлифованием седел. При этом снимайте как можно меньше металла. Шлифовать можно как вручную, так и с помощью шлифовальной машинки.
Шлифование
1. Установите головку на подставку А.60353, вставьте в направляющую втулку клапана стержень А.94059 и очистите фаски седел от нагара зенкерами А.94031 и А.94092 для седел выпускных клапанов и зенкерами А.94003 и А.94101 для седел впускных клапанов. Зенкера надеваются на шпиндель А.94058 и центрируются направляющим стержнем А.94059.
ВНИМАНИЕ: Стержни А.94059 существуют двух различных диаметров: А.94059/1 – для направляющих втулок впускных клапанов и А.94059/2 для направляющих втулок выпускных клапанов.
2. Наденьте на направляющий стержень А.94059 пружину А.94069/5, установите на шпиндель А.94069 конический круг А.94078 для седел выпускных клапанов или круг А.94100 для седел впускных клапанов, закрепите шпиндель в шлифовальной машинке и прошлифуйте седло клапана.
3. В момент соприкосновения круга с седлом машинка должна быть выключена, иначе возникнет вибрация и фаска будет неправильной.
4. Рекомендуется чаще производить правку круга алмазом.
5. Для седел выпускных клапанов ширину рабочей фаски доведите до величин, указанных на рис. Профиль седла выпускного клапана, зенкером А.94031 (угол 20°) и зенкером А.94092, которым устраняется наклеп на внутреннем диаметре. Зенкеры надеваются на шпиндель А.94058 и, также как и при шлифовании, центрируются стержнем А.94059.
6. У седел впускных клапанов ширину рабочей фаски доведите до величин, указанных на рис. Профиль седла впускного клапана, сначала обработав внутреннюю фаску зенкером А.94003 до получения размера диаметром 33 мм, а затем фаску 20° зенкером А.94101 до получения рабочей фаски шириной 1,9–2,0 мм.
Клапаны
1. Удалите нагар с клапанов. Проверьте, не деформирован ли стержень и нет ли трещин на тарелке; при повреждениях замените клапан.
2. Проверьте, не слишком ли изношена и не повреждена ли рабочая фаска. При шлифовании рабочей фаски клапана на шлифовальном станке выдерживайте угол фаски, равный 45°30’±5’, и следите, чтобы толщина цилиндрической части тарелки клапана после шлифования была не меньше 0,5 мм, а также чтобы у выпускного клапана не оказался снятым слой сплава, наплавленный на фаску.
Направляющие втулки клапанов
1. Проверьте зазор между направляющими втулками и стержнем клапана, измерив диаметр клапана и отверстия направляющей втулки. Монтажный зазор для новых втулок: 0,022–0,055 мм – для впускных клапанов и 0,029–0,062 мм – для выпускных клапанов; максимально допустимый предельный зазор (при износе) 0,15 мм.
2. Если увеличенный зазор между направляющей втулкой и клапаном не может быть устранен заменой клапана, замените втулки клапанов, пользуясь оправкой А.60153/R (1 – оправка А.60153/R).
3. Для замены двух направляющих втулок впускного и выпускного клапанов цилиндров № 1 и № 4 отверните две шпильки крепления корпуса подшипников распределительного вала, так как они мешают установке оправки.
4. Запрессовывайте направляющие втулки с надетым стопорным кольцом до упора кольца в плоскость головки цилиндров.
5. После запрессовки разверните отверстия в направляющих втулках развертками А.90310/1 (для втулок впускных клапанов) и А.90310/2 (для втулок выпускных клапанов). Затем прошлифуйте седло клапана и доведите ширину рабочей фаски до нужных размеров, как указано выше.
Маслоотражательные колпачки направляющих втулок
У маслоотражательных колпачков не допускаются отслоение резины от арматуры, трещины и чрезмерный износ рабочей кромки.
При ремонте двигателя маслоотражательные колпачки рекомендуется всегда заменять новыми.
Заменять поврежденные маслоотражательные колпачки рекомендуется на снятой головке цилиндров, чтобы не погнуть стержни клапанов. Для напрессовки колпачков пользуйтесь оправкой 41.7853.4016.
Рычаги клапанов
1. Проверьте состояние рабочих поверхностей рычага, сопрягающихся со стержнем клапана, с кулачком распределительного вала и со сферическим концом регулировочного болта. Если на этих поверхностях появились задиры или риски, замените рычаг новым.
2. Если обнаружена деформация или другие повреждения на втулке регулировочного болта или на самом болте, замените детали.
Пружины
Основные данные для проверки наружной пружины клапана
Основные данные для проверки внутренней пружины клапана
Схема проверки пружины рычага
А – размер в свободном состоянии; В – размер под нагрузкой
1. Убедитесь, нет ли на пружинах трещин и не снизилась ли упругость пружин, для чего проверьте деформацию пружин под нагрузкой (рис. Основные данные для проверки наружной пружины клапана , рис. Основные данные для проверки внутренней пружины клапана , рис. Схема проверки пружины рычага ).
2. Для пружин рычагов (см. рис. Схема проверки пружины рычага ) размер А (пружина в свободном состоянии) должен быть 35 мм, а размер В под нагрузкой 51–73,5 Н (5,2–7,5 кгс) – 43 мм.
Прокладка головки цилиндров
Поверхности прокладки не должны иметь повреждений. Они должны быть ровными, без вмятин, трещин, вздутий и изломов. Отслоение обкладочного материала от арматуры не допускается.
На окантовке отверстий не должно быть трещин, прогаров и отслоений.
Проверка герметичности головки цилиндров
Проверка герметичности головки цилиндров на приспособлении А.60334
1, 2, 4 – заглушки; 3 – плита приспособления; 5 – фланец со штуцером подвода воды
1. Для гидравлического испытания на герметичность рубашки охлаждения головки цилиндров:
установите на головке детали, входящие в комплект приспособления А.60334;
нагнетайте насосом воду внутрь головки под давлением 0,5 МПа (5 кгс/см 2 ).
2. В течение 2 минут не должно наблюдаться утечки воды из головки. При обнаружении трещин головку цилиндров необходимо заменить.
3. Можно проверять герметичность головки цилиндров сжатым воздухом, для чего:
установите на головке цилиндров детали, входящие в комплект приспособления А.60334;
опустите головку цилиндров в ванну с водой, нагретой до 60–80° С, и дайте головке цилиндров прогреться в течение 5 мин;
подайте внутрь головки цилиндров сжатый воздух под давлением 0,15–0,2 МПа (1,5–2 кгс/см 2 ).
4. В течение 1–1,5 мин не должно наблюдаться травления воздуха из головки.
vaz2101spb.ru
ВАЗ 2101 | Головка цилиндров и клапанный механизм
3.11.1 Головка цилиндров и клапанный механизм
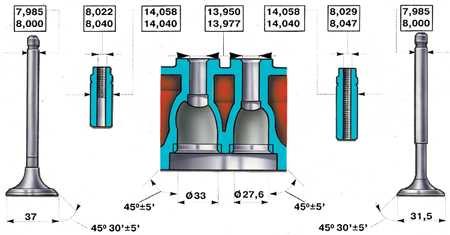
3.11.2 Особенности устройства
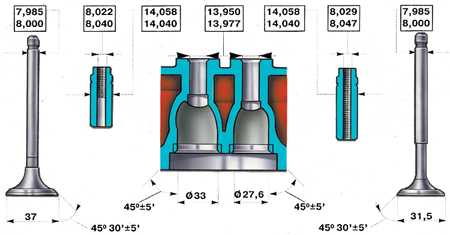
3.11.3 Снятие и установка на автомобиле
Головку цилиндров снимают с двигателя на автомобиле, если для устранения неисправности не нужно снимать сам двигатель или если необходимо только удалить нагар с поверхности камеры сгорания и клапанов. Снятие ПОРЯДОК ВЫПОЛНЕНИЯ 1. Слейте охлаждающую жидкость из радиатора и блока цилиндров и снимите воздушны...
3.11.4 Разборка и сборка
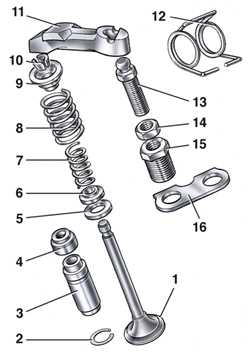
3.11.5 Очистка головки цилиндров
ПОРЯДОК ВЫПОЛНЕНИЯ 1. Установите головку на подставку А.60353. 2. Удалите нагар из камер сгорания и с поверхности выпускных каналов металлической щеткой, приводимой во вращение электрической дрелью. Очистите и осмотрите впускные каналы и каналы подвода масла к ры...
3.11.6 Проверка и шлифование седел клапанов
Профиль седла впускного клапана I – новое седло; II – седло после ремонта Профиль седла выпускного клапана I – новое седло; II – седло после ремонта Форма фасок седел клапанов показана на рис. Профиль седла впускного клапана и рис. Профиль седла вып...3.11.7 Клапаны
ПОРЯДОК ВЫПОЛНЕНИЯ 1. Удалите нагар с клапанов. Проверьте, не деформирован ли стержень и нет ли трещин на тарелке; при повреждениях замените клапан. 2. Проверьте, не слишком ли изношена и не повреждена ли рабочая фаска. При шлифовании рабочей фаски клапана на шли...
3.11.8 Направляющие втулки клапанов
ПОРЯДОК ВЫПОЛНЕНИЯ 1. Проверьте зазор между направляющими втулками и стержнем клапана, измерив диаметр клапана и отверстия направляющей втулки. Монтажный зазор для новых втулок: 0,022–0,055 мм – для впускных клапанов и 0,029–0,062 мм – для выпускных клапанов; максимально допустимый ...3.11.9 Маслоотражательные колпачки направляющих втулок
У маслоотражательных колпачков не допускаются отслоение резины от арматуры, трещины и чрезмерный износ рабочей кромки. При ремонте двигателя маслоотражательные колпачки рекомендуется всегда заменять новыми. Заменять поврежденные маслоотражательные колпачки рекомендуется на снятой головке цилиндров, чтобы не погнуть стержни клапанов. Для напрессовки колпачков пользуйтесь ...
3.11.10 Рычаги клапанов
ПОРЯДОК ВЫПОЛНЕНИЯ 1. Проверьте состояние рабочих поверхностей рычага, сопрягающихся со стержнем клапана, с кулачком распределительного вала и со сферическим концом регулировочного болта. Если на этих поверхностях появились задиры или риски, замените рычаг новым. ...
3.11.11 Пружины
Основные данные для проверки наружной пружины клапана Основные данные для проверки внутренней пружины клапана Схема проверки пружины рычага А – размер в свободном состоянии; В – размер под нагрузкой ПОРЯДОК ВЫПОЛНЕНИЯ ...3.11.12 Прокладка головки цилиндров
Поверхности прокладки не должны иметь повреждений. Они должны быть ровными, без вмятин, трещин, вздутий и изломов. Отслоение обкладочного материала от арматуры не допускается. На окантовке отверстий не должно быть трещин, прогаров и отслоений. ...
3.11.13 Проверка герметичности головки цилиндров
Проверка герметичности головки цилиндров на приспособлении А.60334 1, 2, 4 – заглушки; 3 – плита приспособления; 5 – фланец со штуцером подвода воды ПОРЯДОК ВЫПОЛНЕНИЯ 1. Для гидравлического испытания на герметичность рубашки охлаждения головки цили...automn.ru
ВАЗ 2101 | Дефектовка | Жигули
1. После разборки очистите все детали от грязи, нагара, масла и пр. |
2. Проверьте плоскостность поверхности головки блока, прилегающей к блоку цилиндров. Для этого поставьте металлическую линейку ребром на поверхность головки сначала посредине вдоль оси головки, а затем по диагоналям и измерьте щупом зазор между плоскостью головки и линейкой, как показано на рисунке (см. рис. Проверка плоскостности головки блока цилиндров). Предельно допустимый зазор для бензиновых двигателей составляет 0,05 мм, для дизельных – 0,1 мм. |
3. Если измеренный зазор превышает предельно допустимый, нужно заменить головку блока. У бензиновых двигателей 1,4 л, 55 и 74 кВт допускается шлифовка поверхности, но при этом высота а головки не должна быть меньше 108,25 мм (см. рис. Измерение высоты головки блока цилиндров двигателя объемом 1,4 л). Если в результате шлифовки высота головки окажется меньше, ее нужно заменить. |
Предупреждение
После шлифовки головки блока необходимо прошлифовать седла клапанов на ту же величину, на какую прошлифована головка, чтобы клапаны сели глубже, в противном случае они ударятся о поршни. |
4. У двигателей 1,0 л, 37 кВт и 1,4 л, 50 кВт проверьте, прочно ли сидит на месте заглушка 7 (см. рис. Детали головки блока цилиндров двигателей 1,0 л, 37 кВт и 1,4 л, 50 кВт), если нет – замените ее. Для этого выбейте старую заглушку. Нанесите герметик Loctite 270 по периметру новой заглушки и запрессуйте ее заподлицо в головку блока. |
5. Осмотрите головку: если в камерах сгорания есть трещины или следы прогара, головку нужно заменить. У дизельных двигателей допускаются небольшие трещины между седлами клапанов, если их ширина не превышает 0,5 мм. Замените клапаны с глубокими рисками и царапинами на рабочей фаске, с трещинами, деформацией стержня, короблением тарелки, следами прогара. Неглубокие риски и царапины на рабочей фаске можно вывести притиркой клапанов. |
6. В специализированной мастерской рабочие фаски клапанов с повреждениями, которые невозможно вывести притиркой, можно прошлифовать на специальном станке. При шлифовании надо выдержать размеры, указанные в табл. Размеры клапанов и приведенные на рисунке (см. рис. Размеры клапана). |
7. Проверьте состояние пружин клапанов: искривленные, поломанные или с трещинами замените. |
8. Осмотрите гидротолкатели клапанов, если на их рабочих поверхностях есть задиры, сколы, глубокие царапины, следы ступенчатого или неравномерного износа, замените толкатели. |
9. Осмотрите распределительные валы, если на их шейках и кулачках есть следы износа, задиры, сколы, глубокие риски и др., валы нужно заменить. |
10. Проверьте состояние седел клапанов. На рабочих фасках седел не должно быть следов износа, раковин, коррозии и пр. Незначительные повреждения (мелкие риски, царапины и т.п.) можно вывести притиркой клапанов. |
11. В специализированной мастерской рабочие фаски седел с повреждениями, которые невозможно вывести притиркой клапанов, можно прошлифовать или профрезеровать. На рис. Седло клапана и в табл. Размеры седел клапанов указаны размеры седел двигателей 1,0 л, 37 кВт и 1,4 л, 50 кВт, которые нужно выдержать при обработке. Предварительно нужно рассчитать максимально допустимый размер обработки седел. Для указанных двигателей этот размер определяется следующим образом: – вставьте клапан в головку и прижмите к седлу. Вставлять нужно тот клапан, который будут устанавливать в это седло; – измерьте размер а (см. рис. Измерение выступания клапана над опорной поверхностью пружины в головке блока двигателя) от торца клапана до опорной поверхности пружины клапана на головке блока; – вычислите максимальный допустимый размер обработки седел по формуле: b = a max - a, где b – предельно допустимый размер обработки седел, мм; a max – предельно допустимое выступание клапана (см. табл. Предельно допустимое выступание клапанов) над опорной поверхностью пружины на головке блока, мм; a – измеренный размер от торца клапана до опорной поверхности пружины на головке, мм. Например, для впускного клапана двигателя рабочим объемом 1,0 л измеренное расстояние а равно 42,7 мм, тогда b = 43,1 - 42,7 = 0,4 мм, т.е. максимальная глубина обработки седла – 0,4 мм. |
12. Если в результате расчета b будет равно 0, нужно повторить измерение с новым клапаном; если и в этом случае получится ноль, нужно заменить головку. |
13. У дизельных двигателей 1,4 л, 74 кВт расстояние а (см. рис. Измерение расстояния между торцом клапана и верхней плоскостью головки блока дизельного двигателя 1,9 л, 74 кВт) от торца клапана до верхней плоскости головки блока определяется следующим образом: – вставьте клапан в головку блока и прижмите к седлу. Вставлять нужно тот клапан, который будут устанавливать в это седло; – измерьте размер а; – вычислите максимальный размер обработки седел по формуле: b = a - a min, где b – максимальный размер обработки седел, мм; a – измеренный размер, мм; a min – предельно допустимый размер от торца клапана до верхней плоскости головки блока. |
14. Предельно допустимый размер равен для впускного клапана 43,4 мм, для выпускного – 43,2 мм. |
15. Например, для впускного клапана измереное расстояние а равно 44,1 мм, тогда b = 44,1 - 43,4 = 0,7 мм, т.е. максимальная глубина обработки седла равна 0,7 мм. |
16. Если в результате расчета b равно нулю, повторите измерение с новым клапаном; если и в этом случае получится ноль, нужно заменить головку блока. |
17. Проверьте зазоры между направляющими втулками и клапанами следующим образом: – вставьте клапан в направляющую втулку так, чтобы торец его стержня оказался заподлицо с торцом втулки. Вставлять нужно тот клапан, который будет установлен в эту втулку; – закрепите индикатор так, чтобы его ножка упиралась в тарелку клапана, как показано на рис. Измерение зазора между клапаном и направляющей втулкой. Прижмите клапан в сторону индикатора до упора и установите в этом положении индикатор на ноль. Затем переместите клапан в противоположную сторону до упора и определите по индикатору величину перемещения клапана. Предельно допустимая величина перемещения клапана для бензиновых двигателей составляет 0,5 мм для впускного клапана и 0,6 мм – для выпускного; для дизельных двигателей – 1,3 мм для впускных и выпускных клапанов. Если измеренная величина превышает указанные размеры, нужно повторить измерение с новым клапаном; если снова превышает, замените головку блока. |
18. Проверьте осевой зазор распределительного вала. Для этого у бензиновых двигателей 1,4 л, 55 и 74 кВт: – разместите распределительные валы 27 (см. рис. Детали головки блока цилиндров двигателей 1,4 л, 55 и 74 кВт) в корпусе 5 подшипников и установите задние крышки 7 и 11, затянув болты 8 их крепления моментом 10 Н·м; – закрепите индикатор так, чтобы его ножка упиралась в торец распределительного вала, как показано на рис. Измерение осевого зазора распределительного вала. Передвиньте распределительный вал в сторону индикатора до упора и в этом положении установите индикатор на ноль. Затем передвиньте распределительный вал в противоположную сторону до упора – индикатор покажет величину осевого зазора. |
19. Таким же образом измерьте осевой зазор другого распределительного вала. Осевой зазор у дизельных двигателей измеряется аналогично, но их распределительный вал устанавливается в головку блока (при снятых гидротолкателях клапанов) и закрепляется крышками первого, третьего и пятого подшипников. Осевой зазор для всех двигателей не должен превышать 0,15 мм. |
automn.ru
ВАЗ 2101 | Чистовая обработка посадочной фаски седла / клапана
3.1.3.7. Чистовая обработка посадочной фаски седла / клапана
ОБЩИЕ СВЕДЕНИЯ |
Седла клапанов со следами износа или влияния процесса сгорания могут до обрабатываться, пока выдерживается максимально допустимый размер дообработки. Если этот размер превышен, то гидравлический компенсатор зазора в приводе клапанов перестает выполнять свои функции. В этом случае головку цилиндров следует заменить. Седла клапанов всегда до обрабатываются так, чтобы обеспечить безупречный вид рабочей поверхности. Седла клапанов могут ремонтироваться с помощью обычных инструментов мастерской. Для чистовой обработки требуются развертки. Так как обращение с этими инструментами требует определенного навыка, работу следует выполнять в мастерской.
ПредупреждениеВыпускные седла снабжены дополнительно сужением. При до обработке обязательно обращайте внимание на то, чтобы не повредить радиус сужения.
Определение максимально допустимого размера дообработкиПОРЯДОК ВЫПОЛНЕНИЯ | ||||||
|
ДВИГАТЕЛЬ |
ВПУСКНОЙ КЛАПАН |
ВЫПУСКНОЙ КЛАПАН |
2,8 л (30 клапанов) |
32,2 мм 1) |
33,0 мм |
2,6/ 2,8 л (12 клапанов) |
33,8 мм |
34,1 мм |
1) Средний впускной клапан: 33,2 мм
Угол и ширина посадочной фаски седла клапана
ДВИГАТЕЛЬ |
ВПУСКНОЙ КЛАПАН |
ВЫПУСКНОЙ КЛАПАН |
а = |
39,2 мм (/) |
32,4 мм (/) |
с = |
2,0 мм |
2,4 мм |
b – максимально допустимый размер дообработки (вычисляется)
Z – нижняя контактная поверхность головки цилиндров
300 – верхний корректировочный угол
450 – угол фаски седла клапана
6-цилиндровый бензиновый двигатель: а = макс. 3,5 мм; b = мин. 0,5 мм; а = 450.
automn.ru
Основные размеры клапанов и направляющих втулок Ваз 2107, Ваз 2105, Ваз 2104
ВАЗ
/2104, 2105, 2107
/ремонт
/двигатель
/головка цилиндров
/Размеры головки цилиндров
Снятие и установка клапана лада 2105, порядок действий при ремонте головки своими руками на автомобиле лада 2107, замена сальников ваз 2104, ваз 2105, ваз 2107. Размеры головки цилиндров Устройство головки цилиндров Ваз 2107, Ваз 2105, Ваз 2104, ремонт ремонт двигателя головка цилиндров, устройство и осмотрОсновные размеры головки
Головка цилиндров двигателя Ваз 2107, Ваз 2105, Ваз 2104
Размеры головки цилиндровОсновные размеры клапанов и направляющих втулок Ваз 2107, Ваз 2105, Ваз 2104 |
![]() Снятие и установка головки цилиндровУстановка и снятие головки цилиндров Ваз 2107, Ваз 2105, Ваз 2104 |
![]() Разборка и сборка клапанного механизмаРазборка и сборка клапанного механизма Ваз 2107, Ваз 2105, Ваз 2104 |
Очистка головки цилиндровОчистка головки цилиндров Ваз 2107, Ваз 2105, Ваз 2104 |
![]() Седла клапановПроверка и шлифование седел клапанов Ваз 2107, Ваз 2105, Ваз 2104 |
КлапаныПроверка клапанов Ваз 2107, Ваз 2105, Ваз 2104 |
![]() Направляющие втулки клапановВыпрессовка и запрессовка втулок клапанов Ваз 2107, Ваз 2105, Ваз 2104 |
Маслоотражательные колпачки втулокМаслоотражательные колпачки направляющих втулок Ваз 2107, Ваз 2105, Ваз 2104 |
Рычаги клапановРычаги клапанов Ваз 2107, Ваз 2105, Ваз 2104 |
Пружины клапановПружины клапанов Ваз 2107, Ваз 2105, Ваз 2104 |
Прокладка головки цилиндровПрокладка головки цилиндров Ваз 2107, Ваз 2105, Ваз 2104 |
![]() Герметичность головки цилиндровПроверка герметичности головки цилиндров Ваз 2107, Ваз 2105, Ваз 2104 |
Системы двигателя Ваз 2104, Ваз 2105, Ваз 2107
Обслуживание двигателя лада 2104. Инструкции по ремонту двигателя и систем: питания, охлаждения и смазки лада 2105. Осмотр и ремонт коленвала и распределительного вала, поршневой группы лада 2107. Инструкции по разборке и сборке головки и блока цилиндров.
сборка и разборка двигателя своими руками
блок цилиндров, дефектовка
шатунно-поршневая группа, обслуживание и ремонт
коленчатый вал и маховик, замена и ремонт
головка цилиндров, устройство и осмотр
распределительный вал, установка и настройка
система охлаждения, устройство, фото
система смазки, фото инструкции
система питания, замена и обслуживание
vazclub.com
ВАЗ 2101 | Ремонт головки блока цилиндров
Все детали головки блока цилиндров следует проверить на износ. Следует тщательно очистить привалочную поверхность головки блока цилиндров (иногда остаются прикипевшие фрагменты прокладки). Контроль состояния головки блока цилиндров проводится согласно приведенным ниже указаниям.
Клапанные пружины
Для надлежащей проверки состоянии клапанных пружин необходим специальный тестер пружин. Если его нет в вашем распоряжении, то можно провести простое сравнение старой и новой клапанных пружин. С этой целью взять старую и новую клапанные пружины и зажать их в тиски. Медленно сжимая губки тисков, наблюдать за степенью сжатия обеих пружин. Если они сжимаются одинаково, то это свидетельствует о хорошем состоянии старой пружины. Но если у работавшей пружины большая степень сжатия (выглядит короче новой), то это явный признак усталостного износа — такую пружину следует заменить. Пружины клапанов заменяют полным комплектом.
Подготовленные к установке пружины выставляют на ровной и гладкой поверхности (на стекле) таким образом, чтобы плотно сомкнутые витки находились снизу. Сверху на пружины кладется металлический уголок и проверяется зазор между верхним витком пружины и плоскостью уголка. Этот зазор не должен превышать 2,0 мм. В противном случае пружины подлежат замене.
Направляющие втулки клапанов
Направляющие втулки клапанов, выполненные из чугуна, имеют разные диаметры для впускных и выпускных клапанов. Направляющие втулки выпускных клапанов имеют больший внутренний диаметр и короче, благодаря чему их легко рассортировать. Протягивая через втулки смоченную в бензине ветошь, проведите чистку втулок. Стержни клапанов лучше всего чистить вращающейся металлической щеткой, закрепленной в электродрель.
Контроль износа направляющих втулок проводится с помощью калиброванной оправки. Если выбраковочный калибр оправки свободно входит в направляющую втулку, то такую втулку следует заменить новой. Для демонтажа втулок следует пользоваться специальной оправкой с уступом. Если есть возможность использования направляющих втулок 1-го стандартного размера, то для их монтажа используют специальную оправку, с помощью которой направляющую втулку запрессовывают в посадочное гнездо до тех пор, пока стопорное кольцо не войдет в паз на головке блока цилиндров. При установке направляющих втулок ремонтных размерных групп посадочные гнезда необходимо предварительно обработать ручными протяжными развертками. Так как направляющие втулки перед запрессовкой должны охлаждаться сухим льдом, рекомендуем передать головку блока цилиндров на СТО для установки новых направляющих втулок.
Перед заменой направляющих втулок клапанов сначала проверяют общее состояние головки блока цилиндров. После запрессовки втулки растачивают до требуемых размеров: 8,00–8,015 мм для впускных клапанов и 9,00–9,015 для выпускных клапанов. Направляющие втулки выпускных клапанов имеют большую длину.
При замене направляющих втулок необходимо заменить и клапаны, а клапанные седла — прошлифовать.
Примечание Шлифование клапанных седел проводится только после замены направляющих втулок клапанов. Если вдруг выяснится, что седла больше невозможно растачивать, то направляющие втулки менять не следует. |
Клапанные седла
Рис. 37. Основные размеры седел клапанов: D — наружный диаметр седла клапана; D1 — внутренний диаметр седла клапана; D2 — посадочное гнездо под клапанное седло в головке блока цилиндров; Н — высота клапанного седла; Т — расстояние между плоскостью головки блока цилиндров и верхней кромкой клапанного седла; Н=6,97—7,00 мм — для всех клапанов; Т=2,37—2,25 мм — для впускных клапанов; Т=2,44—2,25 мм — для выпускных клапанов |
Головку блока цилиндров нагреть на водяной бане до 90° С, а клапанное седло остудить на сухом льду, после чего его можно будет запрессовать специальной оправкой в посадочное гнездо. Данную операцию рекомендуется проводить на СТО.
Рис. 38. Определение размера А |
Рис. 39. Притирка клапанов к седлам |
Карандашом нанесите несколько черточек на получившемся матовом пояске с интервалом 1 мм по его периметру. После этого опустить клапан в седло и провернуть его на 90° вокруг стержня, слегка прижимая клапан к седлу.
Выньте клапан из седла и проверьте, чтобы исчезли метки карандаша. Если ширина уплотнительных поясов клапанных седел находится в предписанных пределах, то головку блока цилиндров можно устанавливать на двигатель. В противном случае необходимо продолжать обработку и притирку седел либо заменить головку блока цилиндров.
Клапаны
Вследствие использования гидравлических компенсаторов зазора в клапанах концы клапанных стержней впускных и выпускных клапанов подвергаются специальной обработке для того, чтобы выдерживать повышенные нагрузки. Незначительные повреждения на головках клапанов можно устранить путем их притирки к седлам, как было описано выше. Более серьезные повреждения уплотнительных поверхностей можно исправить на клапанном шлифовальном станке. На отшлифованных клапанах толщина кромок их тарелок не должна быть менее 0,5– 0,7 мм для впускных клапанов и 0,5—0,6 мм — для выпускных.
Рис. 40. Основные размеры клапанов: D — диаметр тарелки (головки) клапана; D1 — диаметр стержня клапана; L — длина клапана; 1 — толкатель; 2 — конические сухари; 3 — тарелка клапанной пружины; 4 — клапанная пружина; 5 — нижняя опорная тарелка клапанной пружины; 6 — маслоотражательный колпачок; 7 — клапан |
При оформлении заказа на клапаны необходимо всегда указывать их назначение (впускные либо выпускные), а также то, что эти клапаны предназначены для дизельного двигателя.
В некоторых случаях можно заменить лишь выпускные клапаны, если у них, например, прогорели кромки.
Головка блока цилиндров
Тщательно почистить привалочные поверхности головки блока цилиндров и блока цилиндров, а затем проверить головку блока цилиндров на отсутствие деформации. С этой целью на привалочную поверхность головки блока цилиндров поместить линейку и с помощью щупа замерить зазор под линейкой в продольном, поперечном и диагональном направлениях. Если в процессе замера зазор между линейкой и поверхностью головки блока цилиндров в продольном направлении превысит 0,10 мм, то эту головку блока цилиндров следует направить на специализированную СТО. При установке линейки в поперечном направлении головки блока цилиндров под линейкой не должно быть никакого просвета. Головки блока цилиндров можно шлифовать до тех пор, пока соответствующая корректировка высоты клапанов позволит это делать (размер А на рис. 38).Точно так же необходимо проверять высоту выступающей части форкамер для впрыска дизельного топлива (601-й двигатель). Кромка форкамер должна выступать на 7,6–8,1 мм.
На СТО предписанный размер выступающей части форкамер может быть выставлен с помощью набора уплотнительных прокладок различной толщины, устанавливаемых под форкамеры. Эта работа должна обязательно выполняться на СТО, так как для этого необходим специальный инструмент для выпрессовки и запрессовки форкамер.
Распределительный вал
Рис. 41. Проверка деформации распределительного вала |
Замена маслоотражательных колпачков (головка блока цилиндров установлена на двигателе)
Рис. 42. Форма маслоотражательных колпачков, надеваемых на стержни клапанов: слева — для выпускных; справа — для впускных клапанов |
Для установки колпачков обычно используется специальный инструмент. Если его нет под рукой, то можно воспользоваться тонкой трубкой, но очень осторожно, чтобы не повредить уплотнительные манжеты и стяжные пружинки колпачков. При установке маслоотражательных колпачков на стержни клапанов, у последних должны быть сняты сухари и клапанные пружины. Для исключения падения клапана в цилиндр необходимо, чтобы поршень этого цилиндра находился в ВМТ. На четырехцилиндровых двигателях эта операция существенно облегчается благодаря тому, что всякий раз два поршня находятся в ВМТ. На пятицилиндровых двигателях выполнять эту работу немного сложнее, так как каждый раз необходимо проворачивать коленчатый вал двигателя на определенный угол, устанавливая поршень очередного цилиндра в ВМТ. Замену маслоотражательных колпачков необходимо выполнять следующим образом (рекомендуем поручить выполнить эту работу опытному специалисту).
Прокрутить двигатель до установки поршня первого цилиндра в ВМТ.
Демонтировать распределительный вал (подразд. 2.12.6).
Удалить сухари клапанов первого цилиндра, как описано в подразд. 2.4.2. На четырехцилиндровом двигателе можно одновременно удалить сухари и снять клапанные пружины с клапанов четвертого цилиндра.
Аккуратно, чтобы не повредить при этом стержни клапанов и отверстия толкателей, сдернуть щипцами старые маслоотражательные колпачки.
Новые маслоотражательные колпачки смазать маслом и аккуратно протолкнуть вниз по стержням клапанов. Не забывайте надевать на стержни впускных клапанов защитные втулки. Плотно насадить маслоотражательные колпачки на направляющие втулки клапанов.
Установить клапанные пружины цветной маркировкой вниз и установить сухари клапана, следя за тем, чтобы сухари хорошо сели в пазы и конические углубления верхних опорных тарелок клапанных пружин.
Слегка приподнять звездочку привода распределительного вала для того, чтобы цепь не вышла из зацепления, и провернуть коленчатый вал четырехцилиндрового двигателя на пол-оборота. После этого можно аналогичным образом поменять маслоотражательные колпачки на клапанах второго и третьего цилиндров. При работе на пятицилиндровом двигателе коленчатый вал необходимо поворачивать до тех пор, пока поршень следующего цилиндра не достигнет ВМТ. Чередование последующих цилиндров, поршень которых проходит ВМТ: 2–4–5–3. Как уже отмечалось выше, проведение этой работы требует особой тщательности.
Примечание Приспособление для сжатия клапанных пружин следует зажимать очень медленно, так как сухари некоторых клапанов зависают в пазах. Избегайте ситуаций, когда вследствие быстрого зажатия приспособления клапан упирается своей тарелкой в поршень. Приспособление должно воздействовать только на клапанную пружину, сжимая и перемещая ее вниз. |
automn.ru